Lean Management: 19 Essential Skills to Boost Your Resume and Career
Here are six different sample cover letters for subpositions related to "lean-management," each with unique details such as the position title, individual information, and tailored competencies.
### Sample 1
**Position number:** 1
**Position title:** Lean Manufacturing Specialist
**Position slug:** lean-manufacturing-specialist
**Name:** John
**Surname:** Smith
**Birthdate:** January 15, 1985
**List of 5 companies:** Toyota, Boeing, GE
**Key competencies:** Lean Six Sigma, Process Optimization, Team Leadership, Analytical Problem Solving, Continuous Improvement
---
**Cover Letter:**
[Today’s Date]
[Your Address]
[City, State, Zip]
[Your Email]
[Your Phone Number]
[Hiring Manager's Name]
Toyota Motor Corporation
[Company Address]
[City, State, Zip]
Dear [Hiring Manager's Name],
I am writing to express my interest in the Lean Manufacturing Specialist position at Toyota. With over 10 years of experience in lean management methodologies, I have successfully driven process improvement initiatives at previous organizations such as Boeing and GE. My expertise in Lean Six Sigma has enabled me to reduce waste and enhance productivity, thus delivering tangible results that align with Toyota's commitment to quality and efficiency.
At my last position, I led a cross-functional team in implementing 5S practices, which resulted in a 20% decrease in cycle times and improved the team’s engagement levels. I am passionate about fostering a culture of continuous improvement, and I look forward to the opportunity to bring my expertise to Toyota.
Thank you for considering my application. I look forward to discussing how I can contribute to your team.
Sincerely,
John Smith
---
### Sample 2
**Position number:** 2
**Position title:** Lean Process Consultant
**Position slug:** lean-process-consultant
**Name:** Emily
**Surname:** Johnson
**Birthdate:** March 22, 1990
**List of 5 companies:** Dell, IBM, Ford
**Key competencies:** Value Stream Mapping, Change Management, Training and Mentoring, Root Cause Analysis, Statistical Analysis
---
**Cover Letter:**
[Today’s Date]
[Your Address]
[City, State, Zip]
[Your Email]
[Your Phone Number]
[Hiring Manager's Name]
Dell Technologies
[Company Address]
[City, State, Zip]
Dear [Hiring Manager's Name],
I am excited to apply for the Lean Process Consultant position at Dell Technologies. With a Master’s Degree in Industrial Engineering and experience in lean methodologies at IBM and Ford, I have honed my skills in Value Stream Mapping and change management to facilitate significant improvements in operational efficiency.
In my previous role, I directed a team that revamped a production line, resulting in a 30% reduction in lead time while improving quality metrics. My analytical approach and dedication to training and mentoring teams have equipped many organizations with sustainable lean practices. I am eager to contribute my expertise to Dell’s commitment to operational excellence.
I appreciate your time and consideration and look forward to the opportunity to discuss my background further.
Best regards,
Emily Johnson
---
### Sample 3
**Position number:** 3
**Position title:** Lean Operations Manager
**Position slug:** lean-operations-manager
**Name:** Robert
**Surname:** Brown
**Birthdate:** June 5, 1980
**List of 5 companies:** Amazon, Intel, Lockheed Martin
**Key competencies:** Supply Chain Management, Kaizen Facilitation, Project Management, Data Analysis, Employee Engagement
---
**Cover Letter:**
[Today’s Date]
[Your Address]
[City, State, Zip]
[Your Email]
[Your Phone Number]
[Hiring Manager's Name]
Amazon
[Company Address]
[City, State, Zip]
Dear [Hiring Manager's Name],
I am writing to express my interest in the Lean Operations Manager position at Amazon. I have over 15 years of experience in leading lean initiatives within fast-paced environments such as Intel and Lockheed Martin. My proficiency in supply chain management and kaizen facilitation has equipped me with the tools to drive substantial operational efficiencies.
In my last role, I spearheaded a project that optimized supply chain processes, leading to a 25% reduction in costs and improving delivery timelines. I am deeply committed to fostering an environment that encourages employee engagement and collaboration, which I believe is critical to successful lean transformations.
Thank you for considering my application. I look forward to contributing to Amazon's mission of operational excellence.
Sincerely,
Robert Brown
---
### Sample 4
**Position number:** 4
**Position title:** Continuous Improvement Coordinator
**Position slug:** continuous-improvement-coordinator
**Name:** Sarah
**Surname:** Green
**Birthdate:** October 10, 1988
**List of 5 companies:** Google, Microsoft, Procter & Gamble
**Key competencies:** Problem-Solving, Lean Tools Implementation, Cross-Functional Collaboration, Training Program Development, Performance Metrics
---
**Cover Letter:**
[Today’s Date]
[Your Address]
[City, State, Zip]
[Your Email]
[Your Phone Number]
[Hiring Manager's Name]
Google
[Company Address]
[City, State, Zip]
Dear [Hiring Manager's Name],
I am thrilled to apply for the Continuous Improvement Coordinator position at Google. With extensive experience implementing lean tools and methodologies at Microsoft and Procter & Gamble, I have developed a strong skill set in performance metrics and problem-solving strategies which can bring value to your team.
In my last position, I successfully designed and conducted training programs that equipped employees with lean principles, resulting in a measurable increase in productivity across departments. My ability to collaborate with cross-functional teams has been essential to driving continuous improvement initiatives.
I am excited about the possibility of discussing how I can contribute to the innovative culture at Google. Thank you for considering my application.
Warm regards,
Sarah Green
---
### Sample 5
**Position number:** 5
**Position title:** Lean Quality Analyst
**Position slug:** lean-quality-analyst
**Name:** Michael
**Surname:** White
**Birthdate:** February 28, 1992
**List of 5 companies:** Mercedes-Benz, HP, Nestlé
**Key competencies:** Quality Assurance, Lean Methodologies, Data-Driven Decision Making, Process Documentation, Compliance Management
---
**Cover Letter:**
[Today’s Date]
[Your Address]
[City, State, Zip]
[Your Email]
[Your Phone Number]
[Hiring Manager's Name]
Mercedes-Benz
[Company Address]
[City, State, Zip]
Dear [Hiring Manager's Name],
I am eager to apply for the Lean Quality Analyst role at Mercedes-Benz. With a background in quality assurance and lean methodologies gained through my experiences at HP and Nestlé, I am well-prepared to contribute to your team.
My extensive experience in data-driven decision-making has enabled me to lead initiatives that enhance product quality while minimizing waste. I have successfully documented processes and ensured compliance with industry standards, ensuring that quality remains a top priority in every project.
I look forward to the opportunity to discuss how my approach to lean quality analysis aligns with Mercedes-Benz's values. Thank you for considering my application.
Sincerely,
Michael White
---
### Sample 6
**Position number:** 6
**Position title:** Lean Strategy Analyst
**Position slug:** lean-strategy-analyst
**Name:** Jessica
**Surname:** Black
**Birthdate:** July 12, 1986
**List of 5 companies:** IBM, Siemens, Unilever
**Key competencies:** Strategic Planning, Market Analysis, KPI Development, Lean Strategy Formulation, Business Process Reengineering
---
**Cover Letter:**
[Today’s Date]
[Your Address]
[City, State, Zip]
[Your Email]
[Your Phone Number]
[Hiring Manager's Name]
IBM
[Company Address]
[City, State, Zip]
Dear [Hiring Manager's Name],
I am excited to submit my application for the Lean Strategy Analyst position at IBM. With expertise in strategic planning and lean methodology developed through experiences at Siemens and Unilever, I am confident in my ability to contribute to your team's objectives.
Throughout my career, I have successfully formulated and implemented lean strategies, backed by thorough market analysis and KPI development to ensure operational effectiveness. My strength in business process reengineering has led to increased profitability and improved customer satisfaction metrics.
I am eager to discuss how my experience and passion for lean strategies can add value to IBM. Thank you for considering my application.
Warm regards,
Jessica Black
---
Feel free to customize the letters further as needed!
Lean Management: 19 Essential Skills to Boost Your Resume and Career
Why This Lean-Management Skill is Important
One of the cornerstone skills in lean management is the ability to identify and eliminate waste. This skill is crucial because inefficiencies can significantly hinder operational performance and profitability. By systematically recognizing areas of surplus—be it in time, materials, or processes—organizations can streamline operations and focus resources on value-adding activities. This not only enhances productivity but also fosters a culture of continuous improvement, empowering employees to contribute creatively to operational excellence.
Moreover, mastering waste elimination aids in aligning business operations with customer needs. By understanding and reducing non-value-added activities, companies can ensure that their products and services meet consumer expectations more efficiently. This alignment ultimately leads to improved customer satisfaction and loyalty. As organizations increasingly navigate complex market landscapes, the ability to effectively manage resources and drive efficiency is not just beneficial, but essential for sustainable growth and competitive advantage.
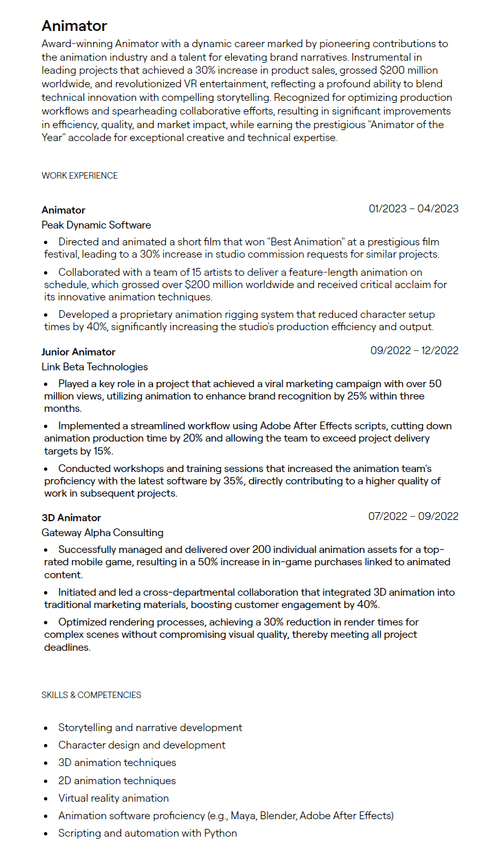
Lean management is a vital skill that focuses on maximizing value while minimizing waste, crucial for enhancing operational efficiency in various industries. Professionals in this field must possess talents in problem-solving, critical thinking, and strong communication to effectively implement lean principles and foster a culture of continuous improvement. To secure a job in lean management, candidates should pursue relevant certifications such as Lean Six Sigma, gain practical experience through internships or projects, and develop a deep understanding of value stream mapping and process optimization. Building a robust professional network in the industry can also significantly enhance job prospects.
Lean Process Optimization: What is Actually Required for Success?
Sure! Here are 10 key points about what is actually required for success in lean management skills:
Strong Leadership Commitment
Lean management requires the unwavering support of leadership to drive cultural change and sustain improvement efforts. Leaders must be active participants in promoting lean principles and practices, modeling behaviors that encourage continuous improvement.Employee Engagement and Empowerment
Success in lean management hinges on involving all employees in the process of identifying inefficiencies and suggesting improvements. Empowering team members fosters ownership and accountability, making them more likely to contribute to the lean initiative.Clear Vision and Goals
Establishing a clear vision for lean initiatives helps align the efforts of all team members toward common objectives. Defining specific, measurable goals provides direction and motivation, ensuring that everyone understands what success looks like.Ongoing Training and Development
Regular training on lean principles, tools, and methodologies is crucial for ensuring that all employees have the necessary skills and knowledge. Training helps cultivate a culture of continuous learning, enabling teams to adapt and improve over time.Effective Communication
Transparent and open communication throughout the organization is vital for lean management success. Consistent dialogue fosters collaboration, helps to share successes, and encourages feedback, making it easier to address challenges as they arise.Customer Focus
A true understanding of customer needs and expectations is essential in lean management. By prioritizing customer value, organizations can eliminate waste more effectively and ensure that improvements directly contribute to meeting or exceeding customer demands.Data-Driven Decision Making
Utilizing data and metrics to guide decisions is a key component of lean management. By analyzing performance data, organizations can identify areas for improvement, measure progress, and make informed decisions that enhance efficiency.Flow and Process Mapping
Understanding and visualizing workflows through process mapping allows teams to identify bottlenecks and waste. This clarity helps in designing more efficient and effective processes, leading to streamlined operations and better resource allocation.Standardization of Best Practices
Establishing standardized processes ensures that successful lean initiatives are documented and replicated across the organization. Standardization not only promotes consistency but also provides a baseline for continuous improvement efforts.Sustaining Continuous Improvement
Lean management is not a one-time effort but a continuous journey. Fostering a culture where teams are encouraged to regularly seek out improvements and challenge the status quo is essential for long-term success and adaptability in a changing environment.
Sample Mastering Lean Management: Streamlining Processes for Enhanced Efficiency skills resume section:
When crafting a resume highlighting lean management skills, it is crucial to showcase relevant experience with specific methodologies, such as Lean Six Sigma or Kaizen. Emphasize quantifiable achievements, like percentage reductions in waste or improvements in operational efficiency, to demonstrate your impact. Include key competencies such as process optimization, data analysis, and employee training to highlight your multifaceted expertise. Tailor the resume to the job description, aligning your skills with the organization's goals. Additionally, showcase your ability to lead cross-functional teams and foster a culture of continuous improvement, illustrating your commitment to enhancing productivity and quality.
• • •
We are seeking a skilled Lean Management Specialist to drive continuous improvement across our operations. The ideal candidate will possess expertise in Lean principles, value stream mapping, and waste reduction techniques. Responsibilities include analyzing processes, implementing effective solutions, and fostering a culture of efficiency within teams. Strong communication and leadership skills are essential to engage stakeholders and facilitate training sessions. The successful candidate will have a proven track record of achieving operational excellence and enhancing productivity. If you are passionate about creating streamlined, cost-effective processes and driving transformative change, we invite you to apply and join our team.
WORK EXPERIENCE
- Led a cross-functional team to streamline operations, achieving a 30% reduction in waste and a 25% increase in overall productivity.
- Implemented a Lean Six Sigma framework that resulted in a 40% decrease in project cycle time, significantly boosting revenue.
- Facilitated workshops and training sessions for over 100 employees on lean principles and problem-solving techniques.
- Developed a comprehensive reporting system for measuring performance and continuous improvement, adopted across multiple departments.
- Recognized with the 'Lean Excellence Award' for outstanding contributions to project success and operational efficiency.
- Conducted value stream mapping sessions that identified key areas for improvement, leading to a 20% increase in product sales.
- Collaborated with stakeholders to design and implement process improvements, enhancing customer satisfaction ratings by 15%.
- Utilized data analysis and statistical tools to diagnose issues and drive strategic decisions, contributing to a 10% boost in global revenue.
- Wrote narrative reports to present findings and improvement strategies, effectively communicating technical concepts to non-technical audiences.
- Trained and mentored junior staff on Lean methodologies, fostering a culture of continuous improvement within the organization.
- Oversaw daily operations and implemented lean strategies that resulted in a 35% reduction in operational costs.
- Drove cross-departmental collaboration that enhanced process efficiencies, leading to a significant uplift in production capability.
- Managed a team of 50 staff, fostering an environment of accountability and continuous improvement that improved employee engagement by 20%.
- Established KPIs to monitor performance and conducted root cause analysis to resolve recurring issues effectively.
- Recognized as 'Manager of the Year' for exceptional leadership and contribution to operational excellence.
- Analyzed supply chain processes and identified inefficiencies, leading to a 15% improvement in lead times.
- Developed and implemented inventory management systems that optimized stock levels and reduced holding costs by 10%.
- Collaborated with suppliers to enhance communication and operational flow, improving service levels and reducing stockouts.
- Presented analytical reports and insights to senior management, supporting data-driven decision-making.
- Contributed to cross-functional projects that improved overall supply chain network performance.
SKILLS & COMPETENCIES
Here’s a list of 10 skills related to lean management:
- Process Mapping: Ability to visualize and analyze workflows to identify waste and inefficiencies.
- Value Stream Mapping: Expertise in assessing and optimizing the flow of materials and information to enhance value delivery.
- Problem Solving: Strong analytical skills to identify root causes of issues and implement effective solutions.
- Continuous Improvement: Commitment to fostering a culture of ongoing enhancements through methodologies like Kaizen.
- Data Analysis: Proficiency in interpreting data to make informed decisions and measure performance metrics.
- Team Collaboration: Capability to work effectively in cross-functional teams, promoting communication and engagement.
- Project Management: Skill in planning, executing, and monitoring projects to ensure lean principles are implemented effectively.
- Change Management: Experience in guiding teams and organizations through transitions towards lean practices.
- Training and Mentoring: Ability to educate and empower team members in lean methodologies and practices.
- Customer Focus: Understanding of customer needs to ensure that lean initiatives align with enhancing customer satisfaction and value.
COURSES / CERTIFICATIONS
Here are five certifications or courses related to lean management that can enhance skills for positions in this field:
Lean Six Sigma Green Belt Certification
- Provider: American Society for Quality (ASQ)
- Dates: Ongoing enrollment; courses typically run January to December annually.
Lean Management Training
- Provider: Massachusetts Institute of Technology (MIT) - Professional Education
- Dates: Scheduled sessions, typically offered in May and November each year.
Certified Lean Practitioner Course
- Provider: Association for Manufacturing Excellence (AME)
- Dates: Next session scheduled for March 2024.
Lean Bronze Certification
- Provider: Society of Manufacturing Engineers (SME)
- Dates: Continuing certification through workshops and exams throughout the year.
Kaizen Training: Continuous Improvement Strategies
- Provider: Udemy
- Dates: Available year-round; self-paced learning.
Make sure to check the specific websites or institutions for the most current dates and availability, as they can change.
EDUCATION
Here are some education and higher education qualifications related to lean management skills:
Bachelor’s Degree in Industrial Engineering
- Institution: [University Name]
- Dates: September 2015 - June 2019
Master’s Degree in Lean Manufacturing
- Institution: [University Name]
- Dates: September 2019 - May 2021
Lean Six Sigma Green Belt Certification
- Institution: [Certification Organization]
- Dates: January 2022
Bachelor’s Degree in Business Administration with a focus on Operations Management
- Institution: [University Name]
- Dates: September 2016 - June 2020
Feel free to replace "[University Name]" and "[Certification Organization]" with specific institutions or organizations relevant to your context.
Here are 19 important hard skills related to lean management that professionals should possess:
Value Stream Mapping
- Value stream mapping is a visual tool used to analyze the flow of materials and information required to bring a product or service to the consumer. This skill enables professionals to identify bottlenecks and areas for improvement in the process, thus ensuring efficient use of resources and quicker delivery times.
Process Improvement Techniques
- Professionals should be proficient in various process improvement methodologies, such as DMAIC (Define, Measure, Analyze, Improve, Control) and PDCA (Plan, Do, Check, Act). These techniques help in systematically addressing inefficiencies and enhancing operational effectiveness.
Root Cause Analysis
- Root cause analysis involves identifying the fundamental causes of problems to prevent recurrence. Skills in tools like the Fishbone Diagram or 5 Whys enable professionals to dig deeper into issues instead of merely addressing superficial symptoms.
Kaizen Principles
- Kaizen, or continuous improvement, is central to lean management. Understanding and applying Kaizen principles allows professionals to foster a culture of incremental improvements, empowering employees to contribute to process enhancement regularly.
Lean Six Sigma Certification
- Certification in Lean Six Sigma combines lean manufacturing principles with Six Sigma methodologies. This credential signifies expertise in reducing waste while maintaining high quality, making it a critical asset for professionals in quality management.
Kanban System
- Mastery of the Kanban system facilitates efficient workflow management by visualizing work processes and limiting work in progress. This skill allows for improved project management, enabling teams to respond dynamically to changing priorities.
Standard Operating Procedures (SOPs) Development
- Developing clear and effective SOPs is vital for maintaining consistent quality and efficiency. Professionals skilled in SOP development can create guidelines that ensure compliance and standardization across the organization.
Data Analysis and Metrics
- Analyzing data and metrics is crucial for informed decision-making in lean management. Professionals must be adept in using statistical tools and software to interpret performance data, identify trends, and measure the effectiveness of improvements.
Change Management
- Lean management often requires significant organizational changes. Proficiency in change management principles ensures that changes are effectively communicated and implemented, minimizing resistance and maximizing employee engagement.
Cost-Benefit Analysis
- Understanding how to conduct cost-benefit analyses enables professionals to evaluate the financial implications of lean initiatives. This skill aids in justifying investments in improvement projects by quantifying expected returns.
Project Management
- Strong project management skills are essential for executing lean initiatives successfully. Professionals skilled in project management practices can plan, execute, and monitor projects efficiently, ensuring they align with organizational goals.
Supply Chain Management
- A thorough understanding of supply chain dynamics helps professionals optimize sourcing, production, and distribution processes. Skills in lean supply chain management can significantly reduce waste and enhance overall efficiency.
Statistical Process Control (SPC)
- SPC is a method of quality control that uses statistical methods to monitor and control processes. Professionals skilled in SPC can quickly identify variations and implement corrective actions, leading to improved product quality.
Performance Measurement Systems
- Developing and implementing effective performance measurement systems allows organizations to track progress and align operational activities with strategic objectives. This skill ensures that teams remain focused on key performance indicators (KPIs).
Training and Development
- Training team members in lean principles is crucial for embedding a lean culture in the organization. Professionals with skills in training and development can effectively share knowledge and empower others to adopt lean practices.
Benchmarking
- Benchmarking involves comparing processes and performance metrics to industry best practices. Professionals adept at benchmarking can identify areas for improvement and establish realistic performance goals based on external standards.
Automated Process Technologies
- Familiarity with automated process technologies, such as robotic process automation (RPA), can enhance efficiency in lean management. Understanding how to implement and optimize these technologies allows professionals to streamline operations further.
Risk Assessment and Management
- Identifying potential risks in processes and developing management strategies is critical in lean management. Professionals skilled in risk assessment can proactively address vulnerabilities, ensuring smoother operations and better resource allocation.
Compliance and Regulatory Knowledge
- Knowledge of compliance and regulatory requirements ensures that lean practices align with industry standards and legal obligations. Professionals with expertise in this area can help organizations achieve operational efficiency without compromising safety or quality standards.
These hard skills are crucial for professionals aiming to implement and sustain lean management philosophies within their organizations effectively, driving continuous improvement and operational excellence.
Job Position Title: Lean Manufacturing Engineer
Process Mapping and Analysis: Proficient in creating and analyzing process maps to identify inefficiencies and opportunities for improvement.
Value Stream Mapping (VSM): Skilled in using VSM techniques to visualize and optimize production flows.
Statistical Process Control (SPC): Knowledge of statistical methods to monitor and control manufacturing processes.
Root Cause Analysis (RCA): Expertise in identifying the root causes of defects or inefficiencies using tools like the 5 Whys and Fishbone diagrams.
Kaizen Event Facilitation: Ability to lead and facilitate continuous improvement workshops and Kaizen events.
Lean Tools and Techniques: Familiarity with various Lean tools such as 5S, Kanban, and Poka-Yoke to enhance operational efficiency.
Project Management: Proficient in managing projects related to Lean initiatives, including planning, execution, and evaluation of outcomes.
Generate Your Cover letter Summary with AI
Accelerate your Cover letter crafting with the AI Cover letter Builder. Create personalized Cover letter summaries in seconds.
Related Resumes:
Generate Your NEXT Resume with AI
Accelerate your Resume crafting with the AI Resume Builder. Create personalized Resume summaries in seconds.