Lean Methodology: 19 Essential Skills to Boost Your Resume Success
Certainly! Here are six different sample cover letters for subpositions related to the position of "lean-methodology," complete with the requested details.
---
### Sample 1
**Position number:** 1
**Position title:** Lean Process Improvement Specialist
**Position slug:** lean-process-improvement-specialist
**Name:** John
**Surname:** Doe
**Birthdate:** January 15, 1988
**List of 5 companies:** Apple, Dell, Google, Amazon, Microsoft
**Key competencies:** Lean Six Sigma, Process Mapping, Root Cause Analysis, Project Management, Team Facilitation
**Cover Letter:**
[Your Address]
[City, State, ZIP Code]
[Email Address]
[Phone Number]
[Date]
[Recipient's Name]
[Company's Name]
[Company's Address]
[City, State, ZIP Code]
Dear [Recipient's Name],
I am writing to express my interest in the Lean Process Improvement Specialist position as advertised. With a comprehensive background in Lean Six Sigma methodologies and a passion for optimizing operations, I believe I would be an ideal fit for your team.
Over the past six years, I have successfully implemented Lean processes in companies such as Dell and Amazon, resulting in significant reductions in waste and improvements in efficiency. My expertise in process mapping and root cause analysis has led to several successful projects that not only enhanced productivity but also fostered a culture of continuous improvement.
I look forward to the opportunity to discuss how my skills can contribute to [Company's Name]’s journey towards operational excellence.
Thank you for considering my application.
Sincerely,
John Doe
---
### Sample 2
**Position number:** 2
**Position title:** Lean Manufacturing Coordinator
**Position slug:** lean-manufacturing-coordinator
**Name:** Emily
**Surname:** Smith
**Birthdate:** March 22, 1990
**List of 5 companies:** Toyota, Tesla, Boeing, Honda, GE
**Key competencies:** Lean Manufacturing, Kaizen, Value Stream Mapping, Team Leadership, Continuous Improvement
**Cover Letter:**
[Your Address]
[City, State, ZIP Code]
[Email Address]
[Phone Number]
[Date]
[Recipient's Name]
[Company's Name]
[Company's Address]
[City, State, ZIP Code]
Dear [Recipient's Name],
I am eager to apply for the Lean Manufacturing Coordinator position at [Company's Name]. With over seven years of experience in lean manufacturing environments, I have honed my skills in Kaizen and value stream mapping, which I believe would greatly benefit your operations.
During my tenure at Toyota, I led a team that identified inefficiencies and implemented solutions that reduced production lead times by 30%. My ability to foster collaboration among cross-functional teams has been critical in driving continuous improvement initiatives.
I am excited about the opportunity to bring my expertise in lean practices to [Company's Name] and help propel your manufacturing processes to new heights.
Thank you for your consideration.
Best regards,
Emily Smith
---
### Sample 3
**Position number:** 3
**Position title:** Lean Operations Analyst
**Position slug:** lean-operations-analyst
**Name:** Michael
**Surname:** Johnson
**Birthdate:** July 8, 1985
**List of 5 companies:** Intel, IBM, Facebook, Oracle, SAP
**Key competencies:** Data Analysis, Lean Strategy Development, Performance Metrics, Process Optimization, Team Collaboration
**Cover Letter:**
[Your Address]
[City, State, ZIP Code]
[Email Address]
[Phone Number]
[Date]
[Recipient's Name]
[Company's Name]
[Company's Address]
[City, State, ZIP Code]
Dear [Recipient's Name],
I am excited to submit my application for the Lean Operations Analyst position at [Company's Name]. With a strong background in data analysis and lean strategy development, I am confident in my ability to drive efficiency improvements for your organization.
In my previous role at Intel, I developed performance metrics that guided operational improvements in collaboration with engineering teams. My analytical skills, paired with a deep understanding of lean methodologies, have enabled me to support initiatives that save costs and enhance performance.
I would love the chance to discuss my fit for this role and how I can support [Company's Name]'s goals.
Warm regards,
Michael Johnson
---
### Sample 4
**Position number:** 4
**Position title:** Lean Quality Assurance Consultant
**Position slug:** lean-quality-assurance-consultant
**Name:** Sarah
**Surname:** Brown
**Birthdate:** September 10, 1992
**List of 5 companies:** Pfizer, Johnson & Johnson, Merck, GSK, Novartis
**Key competencies:** Quality Management, Lean Methodologies, Compliance Auditing, Risk Assessment, Training and Development
**Cover Letter:**
[Your Address]
[City, State, ZIP Code]
[Email Address]
[Phone Number]
[Date]
[Recipient's Name]
[Company's Name]
[Company's Address]
[City, State, ZIP Code]
Dear [Recipient's Name],
I am writing to express my interest in the Lean Quality Assurance Consultant position at [Company's Name]. With a strong foundation in quality management systems and lean methodologies, I am dedicated to ensuring product excellence while enhancing operational efficiency.
During my time at Johnson & Johnson, I led various compliance audits and implemented lean practices that improved our quality metrics and minimized waste by 25%. I am passionate about training teams in best practices and fostering a mindset of continuous improvement.
I would appreciate the opportunity to discuss how my background aligns with the needs of your team and contributes to [Company's Name]’s success.
Thank you for your time and consideration.
Sincerely,
Sarah Brown
---
### Sample 5
**Position number:** 5
**Position title:** Lean Six Sigma Black Belt
**Position slug:** lean-six-sigma-black-belt
**Name:** David
**Surname:** Wilson
**Birthdate:** November 5, 1980
**List of 5 companies:** Honeywell, Lockheed Martin, Siemens, ABB, Caterpillar
**Key competencies:** Six Sigma, Project Management, Statistical Analysis, Change Management, Mentoring
**Cover Letter:**
[Your Address]
[City, State, ZIP Code]
[Email Address]
[Phone Number]
[Date]
[Recipient's Name]
[Company's Name]
[Company's Address]
[City, State, ZIP Code]
Dear [Recipient's Name],
I am thrilled to apply for the Lean Six Sigma Black Belt position at [Company's Name]. With over nine years of experience in leading lean and Six Sigma projects, I have a proven track record of delivering measurable improvements in quality and efficiency.
In my previous role at Honeywell, I successfully led multiple cross-departmental projects that resulted in significant cost savings and operational enhancements. My expertise in statistical analysis and change management has allowed me to drive positive cultural shifts while mentoring junior staff in lean practices.
I look forward to the possibility of contributing to [Company's Name] and becoming a part of your commitment to excellence.
Best regards,
David Wilson
---
### Sample 6
**Position number:** 6
**Position title:** Lean Supply Chain Manager
**Position slug:** lean-supply-chain-manager
**Name:** Laura
**Surname:** Martinez
**Birthdate:** February 18, 1986
**List of 5 companies:** Walmart, Procter & Gamble, Nestlé, Unilever, Coca-Cola
**Key competencies:** Supply Chain Optimization, Vendor Management, Inventory Control, Process Improvement, Data-Driven Decision Making
**Cover Letter:**
[Your Address]
[City, State, ZIP Code]
[Email Address]
[Phone Number]
[Date]
[Recipient's Name]
[Company's Name]
[Company's Address]
[City, State, ZIP Code]
Dear [Recipient's Name],
I am writing to apply for the Lean Supply Chain Manager position at [Company's Name]. My extensive experience in supply chain optimization, coupled with my passion for continuous improvement, positions me well to support your organization in achieving its efficiency goals.
At Walmart, I played a crucial role in the implementation of lean supply chain practices that led to a 20% reduction in inventory costs over a two-year period. My ability to analyze data effectively and collaborate with vendors has been key to enhancing our supply chain operations.
I would welcome the chance to discuss how I can contribute to [Company's Name]'s supply chain excellence.
Thank you for considering my application.
Sincerely,
Laura Martinez
---
Feel free to modify any of the details as necessary!
Lean Methodology: 19 Essential Skills to Boost Your Resume in Business
Why This Lean-Methodology Skill is Important
Understanding and implementing the principles of lean methodology is vital for organizations seeking to optimize their processes and enhance overall efficiency. This skill equips individuals with the ability to identify waste, streamline operations, and improve productivity. By adopting a lean mindset, teams can focus on delivering value to customers while minimizing unnecessary expenditure and resources. The ability to create a culture of continuous improvement fosters innovation and responsiveness, which are critical in today’s fast-paced business environment.
Moreover, this skill promotes cross-functional collaboration, empowering employees at all levels to contribute to problem-solving efforts. As organizations strive for excellence, skilled practitioners of lean methodology can facilitate workshops and training sessions that engage teams in identifying bottlenecks and implementing solutions. Ultimately, mastering lean principles not only drives operational success but also enhances customer satisfaction and loyalty, positioning organizations for sustainable long-term growth.
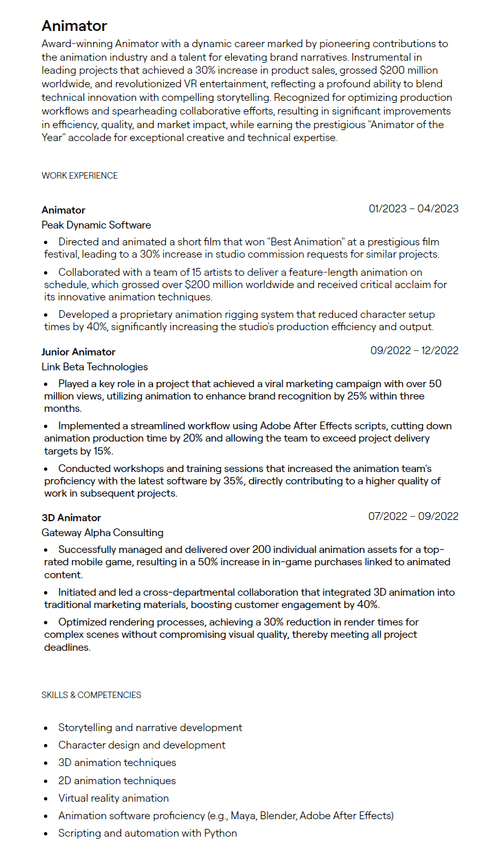
Lean methodology is crucial for enhancing efficiency and reducing waste in organizations, making it a highly sought-after skill in various industries. Professionals in this field must possess analytical thinking, problem-solving abilities, and strong communication skills to effectively identify inefficiencies and implement solutions. A solid understanding of process mapping, data analysis, and continuous improvement techniques is essential. To secure a job in this domain, candidates should pursue certifications such as Lean Six Sigma, gain practical experience through internships or projects, and demonstrate their expertise through a well-crafted portfolio highlighting successful process improvements.
Lean Six Sigma: What is Actually Required for Success?
Here are 10 bullet points outlining what is actually required for success in lean methodology skills, along with brief descriptions for each point:
Understanding Lean Principles
Familiarity with the core principles of lean, such as value, waste elimination, continuous improvement, and respect for people, is vital. This foundational knowledge guides decision-making and process improvements.Data-Driven Decision Making
Success in lean methodology requires the ability to collect and analyze data effectively. Utilizing data analytics allows teams to pinpoint inefficiencies and make informed decisions on process improvements.Commitment to Continuous Improvement
Embracing a culture of continuous improvement (Kaizen) is essential for long-term success. This mindset encourages ongoing small changes that cumulatively lead to significant enhancements in processes and outcomes.Effective Communication Skills
Clear communication fosters collaboration and ensures that all team members understand objectives and processes. Effective sharing of ideas and feedback is crucial for driving change and achieving lean goals.Cross-Functional Collaboration
Lean methodology thrives on the collaboration of diverse teams across the organization. Involving various departments enables a holistic approach to problem-solving and ensures that all viewpoints are considered.Skill in Value Stream Mapping
Mastering value stream mapping allows practitioners to visualize processes, identify waste, and identify areas for improvement. This tool is essential for understanding the flow of materials and information in a system.Proficiency in Problem-Solving Techniques
Tools such as the 5 Whys, Fishbone diagrams, and A3 problem-solving provide structured approaches to identifying root causes of issues. This proficiency is essential to effectively address and resolve operational challenges.Strong Leadership and Engagement
Successful lean implementation relies on leadership that inspires and engages team members. Leaders must advocate for lean practices and support a culture that values contributions from all levels of the organization.Training and Development
Offering ongoing training ensures that all team members are equipped with the necessary lean skills and knowledge. This investment in development fosters a competent workforce capable of driving continuous improvements.Measurement and Feedback Mechanisms
Establishing clear metrics to assess progress is critical for lean success. Implementing feedback loops allows teams to adjust strategies in real-time, ensuring that improvements are measurable and aligned with broader business objectives.
Sample Mastering Lean Methodology: Streamlining Processes for Optimal Efficiency skills resume section:
null
• • •
WORK EXPERIENCE
SKILLS & COMPETENCIES
Certainly! Here are 10 skills related to the main lean-methodology skill for a job position:
Value Stream Mapping: Ability to analyze and visualize the flow of materials and information for process improvement.
Kaizen Facilitation: Experience in leading continuous improvement workshops to foster a culture of incremental change.
Root Cause Analysis: Proficient in identifying underlying issues that lead to inefficiencies or defects.
5S Methodology: Knowledge of organizational techniques to maintain a clean and efficient workspace (Sort, Set in Order, Shine, Standardize, Sustain).
Waste Identification: Skill in recognizing and eliminating waste (Muda) in processes to enhance efficiency.
Process Standardization: Experience in creating and implementing standardized work procedures to ensure consistency and quality.
Data Analysis and Metrics Tracking: Ability to analyze performance metrics and data to drive improvements in lean initiatives.
Cross-Functional Collaboration: Strong interpersonal skills to work effectively with diverse teams and departments.
Change Management: Competence in guiding teams through organizational changes related to lean practices.
Training and Mentoring: Ability to educate and support others on lean principles and practices to build a culture of continuous improvement.
COURSES / CERTIFICATIONS
Here’s a list of five certifications and courses related to lean methodology, along with their dates:
Lean Six Sigma Green Belt Certification
Offered by: ASQ (American Society for Quality)
Duration: 3-5 months
Completion Date: Ongoing (Multiple cohorts each year)Lean Leadership Certification
Offered by: The Lean Enterprise Institute
Duration: 1 week
Completion Date: Scheduled workshops throughout the yearCertified Lean Practitioner
Offered by: International Lean Six Sigma Institute
Duration: 6 weeks
Completion Date: On-demand, with flexible start datesLean Manufacturing Certification
Offered by: Purdue University (Online)
Duration: 3 months
Completion Date: Available year-roundIntroduction to Lean Six Sigma
Offered by: Coursera (by the University of Michigan)
Duration: 4 weeks
Completion Date: Available for enrollment at any time
These credentials can help validate your expertise in lean methodologies and enhance your qualifications for related job positions.
EDUCATION
Here’s a list of educational qualifications relevant to positions that emphasize lean methodology skills:
Bachelor of Science in Industrial Engineering
University of XYZ, 2010 - 2014Master of Business Administration (MBA) with a focus on Operations Management
University of ABC, 2015 - 2017
These qualifications are instrumental for roles that require expertise in lean methodologies, process improvement, and operational efficiency.
Certainly! Here are 19 important hard skills related to lean methodology that professionals should possess, each with a brief description:
Value Stream Mapping (VSM)
Professionals skilled in VSM can visualize and analyze the flow of materials and information in a process. This skill identifies areas of waste and opportunities for optimization by mapping the current state and future state of processes.Kaizen (Continuous Improvement)
Proficiency in Kaizen involves implementing small, incremental changes that lead to significant improvements over time. This skill emphasizes a culture of continuous improvement, where every employee is engaged in enhancing processes.5S Methodology
Understanding and applying the 5S principles—Sort, Set in order, Shine, Standardize, and Sustain—helps create and maintain an organized, efficient workplace. This skill promotes efficiency, safety, and quality by eliminating clutter and standardizing work practices.Root Cause Analysis (RCA)
Experts in RCA can identify the fundamental cause of problems rather than merely addressing symptoms. This skill often employs tools like the "5 Whys" and Fishbone diagrams to ensure that underlying issues are resolved effectively.Standard Work
Creating and documenting standard work involves defining the optimal way to perform tasks to ensure consistency and quality. This skill is crucial for training employees and establishing benchmarks for performance.Lean Metrics and KPIs
Understanding how to develop and use lean metrics and key performance indicators (KPIs) allows professionals to measure performance effectively. This skill helps track progress, identify areas for improvement, and ensure alignment with business goals.Just-In-Time (JIT) Production
Mastery of JIT production techniques enables professionals to optimize inventory levels and reduce waste. This skill focuses on producing only what is needed when it is needed, thereby minimizing excess inventory costs.Poka-Yoke (Error Proofing)
Professionals skilled in Poka-Yoke can design processes that prevent errors before they occur. This skill enhances quality control by implementing safeguards that ensure tasks are completed correctly the first time.Lean Six Sigma
Combining the principles of Lean with Six Sigma methodologies allows for reducing waste while enhancing process quality. Professionals skilled in Lean Six Sigma can apply statistical tools and techniques to analyze data and improve processes systematically.Flowcharting and Process Mapping
Proficiency in creating flowcharts and process maps helps professionals visually depict workflows, making it easier to identify bottlenecks and inefficiencies. This skill is essential for process analysis and redesign initiatives.Gemba Walks
Conducting Gemba walks involves going to the place where work is done to observe processes and engage with employees. This hands-on approach helps identify inefficiencies and gain insights directly from those involved in the work.Statistical Process Control (SPC)
Understanding SPC techniques ensures that professionals can monitor and control processes using statistical methods. This skill helps detect variations from the norm and implements corrective actions before defects occur.Change Management
Skilled professionals can effectively manage organizational change by using tactical strategies that minimize resistance. This includes communication, training, and support to ensure that lean initiatives are successfully implemented.Lean Auditing
Mastery of lean auditing techniques allows professionals to assess the effectiveness of lean practices in place. This skill involves evaluating processes, identifying non-compliance, and recommending improvements for sustained success.Problem-Solving Techniques
Proficiency in structured problem-solving approaches allows for systematic identification and resolution of issues. This skill often uses tools like A3 reports, which provide a clear framework for root cause analysis and action planning.Supplier Relationship Management
Strong skills in managing relationships with suppliers support just-in-time inventory and quality control. This includes negotiating contracts, establishing quality standards, and fostering partnerships for continuous improvement.Team Facilitation
Effective facilitation skills empower professionals to lead teams in discussions, brainstorming sessions, and problem-solving workshops. This skill enhances collaboration and promotes a culture of collective improvement.Data Analysis and Visualization
Proficiency in data analysis and visualization tools (such as Excel, Tableau, or Power BI) enables professionals to interpret and present data effectively. This skill is essential for making informed decisions based on lean performance metrics.Cost-Benefit Analysis
Understanding how to conduct cost-benefit analyses supports decision-making related to lean initiatives. This skill helps evaluate the financial impact of proposed changes, ensuring that resources are allocated effectively for maximum return on investment.
These hard skills form the foundation of a professional's ability to successfully implement and sustain lean methodologies, leading to enhanced efficiency, quality, and profitability.
Job Position Title: Lean Process Improvement Specialist
Data Analysis and Interpretation: Proficiency in analyzing data to identify trends, inefficiencies, and areas for improvement within processes.
Value Stream Mapping: Ability to create and interpret value stream maps to visualize workflows and identify waste.
Statistical Process Control (SPC): Knowledge of statistical tools and methodologies to monitor process performance and ensure quality control.
Root Cause Analysis Techniques: Expertise in applying methodologies like 5 Whys, Fishbone Diagram, and Pareto Analysis to find and address the underlying causes of problems.
Project Management Skills: Familiarity with project management principles to plan, execute, and oversee lean projects and initiatives effectively.
Standard Work Documentation: Skills in developing and implementing standard operating procedures (SOPs) to ensure consistency and efficiency in processes.
Kaizen and Continuous Improvement: Experience in facilitating Kaizen events and fostering a culture of continuous improvement within teams and organizations.
Generate Your Cover letter Summary with AI
Accelerate your Cover letter crafting with the AI Cover letter Builder. Create personalized Cover letter summaries in seconds.
Related Resumes:
Generate Your NEXT Resume with AI
Accelerate your Resume crafting with the AI Resume Builder. Create personalized Resume summaries in seconds.