Servicing Equipment: 19 Essential Skills for Your Resume Success in Maintenance
Here are six different sample cover letters for positions related to "servicing equipment," each showcasing a different approach and style.
---
### Sample 1
**Position number:** 1
**Position title:** Equipment Technician
**Position slug:** equipment-technician
**Name:** John
**Surname:** Smith
**Birthdate:** 1985-04-12
**List of 5 companies:** Apple, Dell, Samsung, Microsoft, HP
**Key competencies:** Troubleshooting, Technical Support, Preventative Maintenance, Customer Service, Safety Standards
---
[Your Address]
[City, State, Zip Code]
[Email Address]
[Phone Number]
[Date]
[Recipient Name]
[Company Name]
[Company Address]
[City, State, Zip Code]
Dear [Recipient Name],
I am writing to express my interest in the Equipment Technician position at [Company Name], as advertised on your website. With over eight years of experience in equipment servicing for leading technology companies like Apple and Dell, I possess a strong background in troubleshooting and preventative maintenance.
I have a proven track record of enhancing technical support initiatives, and my commitment to safety standards has consistently led to improved operational efficiency. At [Previous Company], I implemented a new preventative maintenance schedule that reduced equipment downtime by 20%.
I look forward to bringing my technical expertise and dedication to high-quality service to [Company Name].
Sincerely,
John Smith
---
### Sample 2
**Position number:** 2
**Position title:** Field Service Engineer
**Position slug:** field-service-engineer
**Name:** Lisa
**Surname:** Johnson
**Birthdate:** 1990-07-22
**List of 5 companies:** Google, HP, Fujitsu, IBM, Lenovo
**Key competencies:** Proven Problem Solver, Customer Relations, Equipment Diagnostics, Project Management, Technical Documentation
---
[Your Address]
[City, State, Zip Code]
[Email Address]
[Phone Number]
[Date]
[Recipient Name]
[Company Name]
[Company Address]
[City, State, Zip Code]
Dear [Recipient Name],
I am excited to apply for the Field Service Engineer position at [Company Name]. With a Bachelor’s degree in Engineering and five years in the field, I have honed my skills in equipment diagnostics and customer relations while working for esteemed organizations such as Google and HP.
At [Previous Company], I spearheaded a project that streamlined service response times by 30%. My technical background, combined with my passion for helping clients, shapes my commitment to delivering exceptional service. I am eager to contribute my expertise at [Company Name] and support your mission of excellence in service.
Thank you for considering my application. I look forward to discussing how I can add value to your team.
Best regards,
Lisa Johnson
---
### Sample 3
**Position number:** 3
**Position title:** Service Technician
**Position slug:** service-technician
**Name:** Michael
**Surname:** Brown
**Birthdate:** 1988-02-01
**List of 5 companies:** Samsung, Dell, Toshiba, Panasonic, Xenith
**Key competencies:** Mechanical Skills, Attention to Detail, Customer Interaction, Installation & Repair, Equipment Testing
---
[Your Address]
[City, State, Zip Code]
[Email Address]
[Phone Number]
[Date]
[Recipient Name]
[Company Name]
[Company Address]
[City, State, Zip Code]
Dear [Recipient Name],
I am applying for the Service Technician position at [Company Name]. With over seven years of hands-on experience at industry leaders like Samsung and Toshiba, I am well-prepared to handle the challenges of servicing equipment.
My strong mechanical skills, paired with an eye for detail, have allowed me to successfully install and repair a wide range of equipment. I take pride in my ability to build strong customer relationships through effective communication and understanding their needs.
I am enthusiastic about the opportunity to contribute to your team and help maintain [Company Name]'s reputation for outstanding service.
Warmest regards,
Michael Brown
---
### Sample 4
**Position number:** 4
**Position title:** Equipment Maintenance Specialist
**Position slug:** maintenance-specialist
**Name:** Sarah
**Surname:** Davis
**Birthdate:** 1995-10-10
**List of 5 companies:** Intel, Cisco, Philips, LG, Sony
**Key competencies:** Equipment Monitoring, Analytical Thinking, Team Collaboration, Compliance Regulation, Inventory Management
---
[Your Address]
[City, State, Zip Code]
[Email Address]
[Phone Number]
[Date]
[Recipient Name]
[Company Name]
[Company Address]
[City, State, Zip Code]
Dear [Recipient Name],
I am excited to submit my application for the Equipment Maintenance Specialist position at [Company Name]. I hold a degree in Mechanical Engineering and have spent the last three years working at Intel and Cisco, where I developed critical skills in equipment monitoring and compliance regulations.
I have a proven track record of collaborating within teams to maximize productivity while complying with safety standards. I also excel in inventory management, ensuring efficient use of resources.
I am eager to bring my technical skills and a passion for excellence to [Company Name] and contribute to your repair service team's success.
Thank you for your consideration.
Best,
Sarah Davis
---
### Sample 5
**Position number:** 5
**Position title:** Equipment Servicing Coordinator
**Position slug:** servicing-coordinator
**Name:** David
**Surname:** Wilson
**Birthdate:** 1982-05-15
**List of 5 companies:** IBM, Xerox, Panasonic, Hitachi, Epson
**Key competencies:** Organizational Skills, Communication, Scheduling, Troubleshooting, Team Leadership
---
[Your Address]
[City, State, Zip Code]
[Email Address]
[Phone Number]
[Date]
[Recipient Name]
[Company Name]
[Company Address]
[City, State, Zip Code]
Dear [Recipient Name],
I am writing to express my interest in the Equipment Servicing Coordinator position at [Company Name]. With extensive experience in service coordination for companies like IBM and Xerox, combined with my background in troubleshooting, I am excited about the opportunity to contribute to your team.
My organizational skills have been honed through years of scheduling and managing service teams, ensuring that all equipment is serviced promptly and efficiently. My proactive communication approach ensures that all stakeholders are informed throughout the servicing process.
I am excited about the possibility of working at [Company Name] and am eager to bring my skills in leadership and coordination to your esteemed organization.
Sincerely,
David Wilson
---
### Sample 6
**Position number:** 6
**Position title:** Technical Support Specialist
**Position slug:** technical-support-specialist
**Name:** Emily
**Surname:** Thomas
**Birthdate:** 1993-11-20
**List of 5 companies:** Dell, Google, Xerox, LG, Apple
**Key competencies:** Technical Expertise, Issue Resolution, Training, Customer Engagement, Documentation
---
[Your Address]
[City, State, Zip Code]
[Email Address]
[Phone Number]
[Date]
[Recipient Name]
[Company Name]
[Company Address]
[City, State, Zip Code]
Dear [Recipient Name],
I am thrilled to apply for the Technical Support Specialist position at [Company Name]. My educational background in Information Technology and my experience at industry-leading companies like Dell and Google make me a strong candidate for this role.
I have a deep understanding of servicing equipment and excel at resolving technical issues to ensure customer satisfaction. My experience training users and creating technical documentation has helped enhance service quality and efficiency in my previous roles.
I am looking forward to the possibility of joining [Company Name]'s dedicated team of professionals and am eager to contribute my expertise to further improve your technical support initiatives.
Thank you for your time and consideration.
Warm regards,
Emily Thomas
---
Feel free to customize any specific fields such as [Recipient Name], [Previous Company], and [Company Name] to align with your applications!
Servicing Equipment: 19 Essential Skills for Your Resume Success in Repair
Why This Servicing-Equipment Skill is Important
Mastering servicing-equipment skills is crucial in today’s fast-paced technological environment. These skills ensure that service technicians can effectively diagnose, maintain, and repair a wide array of mechanical and electronic systems. With the increasing complexity of machinery and devices across industries, having robust servicing skills minimizes downtime and enhances operational efficiency. Technicians proficient in servicing equipment are invaluable, as they play a pivotal role in extending the lifecycle of equipment and reducing overall maintenance costs.
Moreover, possessing strong servicing-equipment skills fosters a culture of safety and reliability. Proper maintenance and timely servicing help prevent catastrophic failures that could lead to costly accidents, legal issues, or production halts. This competence not only safeguards employee welfare but also boosts the company's reputation for quality and dependability. In an era where technology evolves rapidly, ongoing training and skill enhancement in servicing equipment is indispensable for both individual career growth and organizational success.
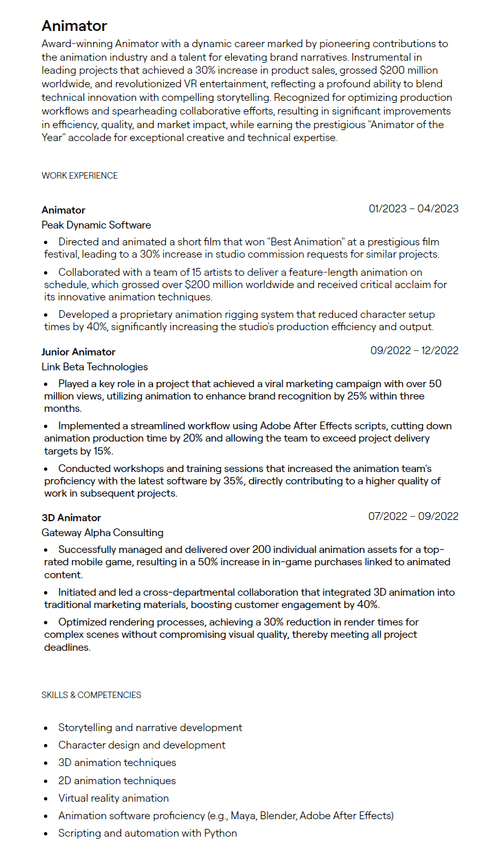
Servicing-equipment skills are vital in ensuring the functionality and safety of machinery across various industries. Professionals in this role must possess a strong technical aptitude, problem-solving ability, and attention to detail, as well as skills in diagnostics, maintenance, and repair. To secure a job in this field, candidates should pursue relevant certifications, gain hands-on experience through internships or apprenticeships, and stay updated with the latest technological advancements. Networking within industry circles and showcasing a strong understanding of equipment operations can further enhance job prospects, making candidates more appealing to potential employers.
Servicing Equipment Mastery: What is Actually Required for Success?
Here are ten essential components required for success in servicing equipment skills:
Technical Knowledge
A deep understanding of the equipment's mechanics, electronics, and systems is crucial. Familiarity with manufacturers' specifications and industry standards enhances troubleshooting abilities.Hands-On Experience
Practical experience through internships, apprenticeships, or on-the-job training allows technicians to apply theoretical knowledge. Real-world exposure helps to develop problem-solving skills in diverse scenarios.Diagnostic Skills
Strong diagnostic skills are necessary for identifying issues quickly and accurately. Being able to use diagnostic tools and methods effectively can save time and reduce costs in the repair process.Attention to Detail
Precision is key when servicing equipment, as small oversights can lead to significant problems. A meticulous approach can ensure all components are functioning correctly and safely.Communication Skills
The ability to clearly communicate with team members and clients is vital. Explaining technical terms in layman's language fosters trust and ensures everyone is on the same page regarding repairs and maintenance.Continuous Learning
Staying updated with the latest technologies and industry developments is essential for ongoing success. Participating in training workshops, certifications, and online courses can enhance knowledge and skillsets.Safety Awareness
Understanding safety protocols and regulations for servicing equipment is critical. Proper safety measures protect technicians and clients, minimizing the risk of accidents and damage.Time Management
Efficiently managing time during service calls or repairs can enhance productivity. Prioritizing tasks based on urgency and importance ensures timely service and customer satisfaction.Problem-Solving Abilities
The ability to think critically and creatively when faced with unexpected issues is invaluable. Developing systematic troubleshooting approaches can help technicians tackle complex problems with confidence.Customer Service Orientation
Providing excellent customer service creates positive experiences for clients and builds lasting relationships. Listening to customer concerns and addressing them professionally can lead to repeat business and referrals.
Sample Mastering Servicing Equipment: Techniques for Optimal Performance skills resume section:
When crafting a resume focused on servicing equipment skills, it’s crucial to emphasize relevant technical competencies, including troubleshooting, equipment diagnostics, and maintenance techniques. Highlight hands-on experience with specific equipment types and industries. Showcase problem-solving abilities, attention to detail, and effective customer interaction skills, as these are vital for success in service roles. Additionally, include any certifications or training that pertain to equipment servicing, and quantify achievements, such as improved response times or reduced downtime. Finally, demonstrate a commitment to safety standards and compliance, which are essential in equipment management and servicing environments.
[email protected] • (555) 123-4567 • https://www.linkedin.com/in/alice-thompson • https://twitter.com/alice_t
We are seeking a dedicated Equipment Servicing Technician to join our team. The ideal candidate will excel in diagnosing, repairing, and maintaining servicing equipment across various settings. Key responsibilities include performing routine preventive maintenance, troubleshooting mechanical issues, and ensuring compliance with safety standards. The role demands strong technical skills, attention to detail, and the ability to work independently or as part of a team. A background in mechanical engineering or a related field is preferred, along with relevant certifications. Join us to contribute your expertise and enhance our equipment's operational efficiency.
WORK EXPERIENCE
- Led a successful project that improved equipment servicing response time by 40%, significantly enhancing customer satisfaction.
- Developed and implemented training programs for staff, which increased team efficiency by 30% in servicing equipment.
- Collaborated with sales teams to create technical sales presentations, boosting product sales in serviced markets by 25%.
- Awarded 'Employee of the Year' for exceptional contributions to project leadership and industry innovation.
- Managed a team of technicians, optimizing workflow and reducing servicing time by 20% through process improvements.
- Implemented a predictive maintenance system that decreased unplanned downtime by 35%, leading to increased client trust and retention.
- Conducted market analysis to identify and exploit new service opportunities, resulting in a revenue increase of 15% over two years.
- Mentored and trained junior staff on advanced servicing techniques, fostering a culture of continuous improvement.
- Provided expert consulting on equipment servicing strategies, contributing to a 30% improvement in client operational efficiency.
- Created comprehensive service manuals that standardized processes and improved compliance across multiple service teams.
- Facilitated workshops and technical training sessions that led to an industry certification for over 50 technicians.
- Achieved recognition for outstanding client feedback, frequently receiving testimonials that highlighted my problem-solving skills.
- Executed equipment diagnostics and repairs in the field, achieving a 98% first-time fix rate.
- Developed strong relationships with clients, enhancing customer loyalty and resulting in an increase in repeat service requests.
- Supported the implementation of new technologies in servicing procedures that reduced downtime and improved service quality.
- Recognized as 'Top Performer of the Month' multiple times due to exceptional service delivery.
SKILLS & COMPETENCIES
Certainly! Here are 10 skills related to the main servicing-equipment skill, which could be applicable for a job position in fields like maintenance, repair, or servicing of equipment:
- Technical Proficiency: Ability to understand and operate various servicing equipment and tools.
- Troubleshooting: Skill in diagnosing equipment malfunctions and determining appropriate repair solutions.
- Preventive Maintenance: Understanding of routine maintenance practices to ensure equipment longevity and performance.
- Safety Compliance: Knowledge of safety protocols and regulations related to servicing equipment and tools.
- Electrical Systems Knowledge: Familiarity with electrical components and systems commonly found in equipment.
- Mechanical Aptitude: Ability to comprehend mechanical systems and apply repair techniques effectively.
- Problem-Solving Skills: Capacity to think critically and develop efficient solutions to equipment-related issues.
- Documentation and Reporting: Competence in maintaining accurate records of service history and performed repairs.
- Time Management: Ability to prioritize tasks and manage time effectively to meet service deadlines.
- Customer Service Orientation: Strong communication skills to interact with clients and provide updates on service status.
These skills collectively enhance the ability to effectively service equipment across various industries.
COURSES / CERTIFICATIONS
Here’s a list of 5 certifications or complete courses related to servicing equipment skills:
Certified Maintenance and Reliability Technician (CMRT)
- Provider: Society for Maintenance & Reliability Professionals (SMRP)
- Date: Ongoing (test available year-round)
Electrical and Mechanical Equipment Maintenance Certification
- Provider: National Institute for Certification in Engineering Technologies (NICET)
- Date: Available throughout the year, with certification exams conducted in various months
Fundamentals of HVAC Systems Course
- Provider: ASHRAE (American Society of Heating, Refrigerating and Air-Conditioning Engineers)
- Date: Available on-demand (Last updated: May 2023)
Industrial Equipment Maintenance Training Program
- Provider: Penn Foster Career School
- Date: Self-paced (Course updated December 2022)
Certification in Repair and Maintenance of Heavy Equipment
- Provider: United Association of Journeymen and Apprentices of the Plumbing and Pipe Fitting Industry (UA)
- Date: Next cohort starts in January 2024
Feel free to check each provider for the most current information regarding enrollment, schedules, and certification availability!
EDUCATION
Sure! Here’s a list of educational qualifications relevant to job positions related to servicing equipment skills:
Associate of Applied Science in Industrial Maintenance Technology
- Institution: Community College of Baltimore County
- Dates: August 2018 - May 2020
Bachelor of Science in Mechanical Engineering Technology
- Institution: University of North Carolina at Charlotte
- Dates: August 2016 - May 2020
Feel free to ask for more specific information or additional qualifications!
Certainly! Here are 19 important hard skills that professionals in servicing equipment should possess, along with brief descriptions for each:
Technical Proficiency
Professionals should have a strong understanding of technical specifications and measures. This includes familiarity with manuals and schematics to troubleshoot and repair a wide range of equipment effectively.Electrical Systems Knowledge
A solid grasp of electrical systems and wiring is crucial. Technicians need to be able to safely diagnose and repair issues in electrical circuits, ensuring functionality and safety.Mechanical Skills
Understanding mechanical components is essential for service technicians. They should be adept at dismantling and reassembling equipment, performing repairs on machinery, and replacing parts as necessary.Diagnostic Acumen
Quickly identifying problems is a critical skill. Technicians must use diagnostic tools and their analytical skills to pinpoint issues efficiently and accurately.Preventive Maintenance Expertise
Knowledge of preventive maintenance protocols helps extend equipment life. Professionals should be familiar with scheduling regular assessments and performing necessary upkeep to prevent breakdowns.Hydraulics and Pneumatics Knowledge
Familiarity with hydraulic and pneumatic systems is essential for servicing relevant equipment. Technicians should understand fluid dynamics to troubleshoot and repair these systems effectively.Welding Skills
Welding capabilities are frequently necessary for equipment repairs. Technicians should know various welding techniques to strengthen or repair metal structures safely and effectively.Computer Literacy
Proficiency in using diagnostic software and basic computer tools is increasingly important. Technicians must navigate modern equipment that relies on software for operation and troubleshooting.Safety Compliance Understanding
Adherence to safety regulations and industry standards is paramount. Professionals need to be aware of safety protocols to minimize risk to themselves and their colleagues.Precision Measurement Techniques
Mastery in using measurement instruments for precise calibrations is essential. This skill ensures that equipment operates within specified parameters, avoiding malfunctions.Parts Inventory Management
Knowledge of managing parts and inventory effectively keeps service operations running smoothly. This involves tracking parts, ordering replacements, and maintaining adequate stock levels.Troubleshooting Techniques
The ability to systematically approach problems is essential. Technicians should employ logical reasoning and methodical problem-solving strategies to maintain high service standards.Manufacturer Specifications Familiarity
Understanding equipment manufacturer specifications is crucial for accurate service delivery. Technicians should be able to interpret technical documents and apply them during repairs and maintenance.Fluid Mechanics Knowledge
Complete comprehension of fluid mechanics principles helps in servicing various machinery. This knowledge underpins the ability to troubleshoot issues related to systems that use liquids.Soldering and Circuit Repair Skills
Proficiency in soldering techniques allows professionals to repair and create electronic circuits. This skill is vital for dealing with intricate machinery that relies on electronic components.Calibration Proficiency
Skills in calibrating equipment ensure that all machinery performs within required tolerances. Regular calibration can enhance precision and extend equipment longevity.Environmental Regulations Understanding
Familiarity with environmental regulations is important for compliance. This knowledge helps in the disposal of hazardous materials and in adhering to eco-friendly servicing practices.Data Logging and Reporting Techniques
Skills in documenting service activities and outcomes are essential. Professionals should log data accurately, allowing for effective communication and tracking of service history.Communication Skills
Strong communication skills facilitate effective interactions with clients and team members. Technicians must often explain complex issues in simpler terms to ensure understanding and promote collaboration.
These hard skills form the foundation of expertise necessary for professionals involved in servicing and maintaining various equipment, ensuring efficiency and safety in their work.
Certainly! Here are seven bullet points outlining the top hard skills for the job position of Service Technician in the servicing-equipment field:
Technical Proficiency: In-depth knowledge of diagnostic tools and equipment used in maintenance, repair, and servicing of machinery and electronic devices.
Mechanical Skills: Strong understanding of mechanical systems, including hydraulics, pneumatics, and electrical components, enabling effective troubleshooting and repair.
Electrical Knowledge: Ability to read and interpret electrical schematics, and experience with wiring, circuit troubleshooting, and the installation of electrical systems.
Safety Protocols: Familiarity with workplace safety regulations and practices, ensuring compliance while handling hazardous materials and operating heavy machinery.
Preventive Maintenance: Expertise in developing and implementing preventive maintenance schedules to minimize equipment downtime and enhance operational efficiency.
Software Proficiency: Competence in using diagnostic software and service management systems for tracking maintenance records, scheduling repairs, and managing inventory.
Technical Communication: Skills in documenting service reports and communicating technical information clearly to non-technical clients or team members, ensuring understanding of service issues and resolutions.
Generate Your Cover letter Summary with AI
Accelerate your Cover letter crafting with the AI Cover letter Builder. Create personalized Cover letter summaries in seconds.
Related Resumes:
Generate Your NEXT Resume with AI
Accelerate your Resume crafting with the AI Resume Builder. Create personalized Resume summaries in seconds.