Six Sigma Skills for Your Resume: Boost Your Career in Quality Management
Sure! Below are six sample cover letters for different six-sigma-related positions, complete with specified details.
---
### Sample 1
**Position number:** 1
**Position title:** Six Sigma Black Belt Consultant
**Position slug:** six-sigma-black-belt-consultant
**Name:** John
**Surname:** Smith
**Birthdate:** 1985-04-15
**List of 5 companies:** Apple, Dell, Google, Microsoft, IBM
**Key competencies:** Lean management, quality improvement, process optimization, project management, data analysis
---
[Your Address]
[City, State, Zip]
[Email]
[Phone Number]
[Date]
[Recipient's Name]
[Title]
[Company Name]
[Company Address]
[City, State, Zip]
Dear [Recipient's Name],
I am writing to express my interest in the Six Sigma Black Belt Consultant position at [Company Name], as advertised on [Job Board/Company Website]. With over 10 years of experience in quality and process improvement across various industries, including technology and manufacturing, I am excited about the opportunity to contribute to your team.
During my career, I have successfully led projects that resulted in substantial cost reduction and efficiency improvements by implementing Six Sigma methodologies. My recent project with Apple involved significant process optimization, yielding a 30% increase in productivity while reducing defects by 25%. My ability to analyze data and lead cross-functional teams equips me to effectively drive success in this role.
I look forward to the chance to discuss how my skills and experiences align with the goals of [Company Name]. Thank you for considering my application.
Sincerely,
John Smith
---
### Sample 2
**Position number:** 2
**Position title:** Six Sigma Process Improvement Specialist
**Position slug:** six-sigma-process-improvement-specialist
**Name:** Linda
**Surname:** Johnson
**Birthdate:** 1990-06-22
**List of 5 companies:** Google, Amazon, Tesla, Intel, Procter & Gamble
**Key competencies:** Statistical analysis, root cause analysis, lean methodologies, project management, team leadership
---
[Your Address]
[City, State, Zip]
[Email]
[Phone Number]
[Date]
[Recipient's Name]
[Title]
[Company Name]
[Company Address]
[City, State, Zip]
Dear [Recipient's Name],
I am excited to apply for the Six Sigma Process Improvement Specialist position at [Company Name]. With a Master’s degree in Industrial Engineering and a proven track record of tackling complex process improvement challenges, I believe I can deliver significant value to your organization.
At Google, I led a project team that utilized Six Sigma tools and methodologies to decrease production cycle times by 15% while improving overall quality metrics. My statistical analysis skills and experience in root cause analysis enable me to effectively identify and implement solutions to operational problems.
I would be delighted to further discuss how my background and skills can benefit [Company Name]. Thank you for your consideration.
Warm regards,
Linda Johnson
---
### Sample 3
**Position number:** 3
**Position title:** Six Sigma Quality Manager
**Position slug:** six-sigma-quality-manager
**Name:** David
**Surname:** Brown
**Birthdate:** 1988-03-10
**List of 5 companies:** Dell, Siemens, Caterpillar, Honeywell, Johnson & Johnson
**Key competencies:** Quality assurance, team management, process mapping, problem-solving, training and mentoring
---
[Your Address]
[City, State, Zip]
[Email]
[Phone Number]
[Date]
[Recipient's Name]
[Title]
[Company Name]
[Company Address]
[City, State, Zip]
Dear [Recipient's Name],
I am eager to apply for the Six Sigma Quality Manager position at [Company Name]. My background in quality assurance and process improvement, combined with a passion for mentoring emerging talent, aligns seamlessly with the requirements of this role.
In my previous position at Dell, I oversaw multiple teams in the execution of quality improvement initiatives, which resulted in a 20% reduction in product defects. My experience creating process maps and training staff in Six Sigma principles helped foster a culture of continuous improvement within our organization.
I am looking forward to the opportunity to contribute to [Company Name] and help elevate its quality standards. Thank you for your time and consideration.
Best regards,
David Brown
---
### Sample 4
**Position number:** 4
**Position title:** Six Sigma Lean Specialist
**Position slug:** six-sigma-lean-specialist
**Name:** Sarah
**Surname:** Williams
**Birthdate:** 1992-08-18
**List of 5 companies:** IBM, Ford, Coca-Cola, General Electric, Nestlé
**Key competencies:** Lean Six Sigma, process evaluation, change management, collaboration, KPI analysis
---
[Your Address]
[City, State, Zip]
[Email]
[Email]
[Phone Number]
[Date]
[Recipient's Name]
[Title]
[Company Name]
[Company Address]
[City, State, Zip]
Dear [Recipient's Name],
I am writing to express my interest in the Six Sigma Lean Specialist role at [Company Name]. With a strong background in Lean Six Sigma methodologies and a knack for process evaluation, I am excited about the prospect of improving systems and workflows at your esteemed organization.
In my role at IBM, I led several initiatives aimed at streamlining operations, which successfully achieved a 40% reduction in waste and boosted overall efficiency. My collaborative approach with cross-functional teams has been instrumental in fostering buy-in for change management processes.
I would love to discuss how my experience and passion for continuous improvement align with the objectives of [Company Name]. Thank you for your consideration.
Sincerely,
Sarah Williams
---
### Sample 5
**Position number:** 5
**Position title:** Six Sigma Data Analyst
**Position slug:** six-sigma-data-analyst
**Name:** Michael
**Surname:** Martinez
**Birthdate:** 1995-12-02
**List of 5 companies:** Amazon, Facebook, Samsung, Pfizer, Lockheed Martin
**Key competencies:** Data visualization, statistical modeling, trend analysis, reporting, process optimization
---
[Your Address]
[City, State, Zip]
[Email]
[Phone Number]
[Date]
[Recipient's Name]
[Title]
[Company Name]
[Company Address]
[City, State, Zip]
Dear [Recipient's Name],
I am excited to submit my application for the Six Sigma Data Analyst position at [Company Name]. With extensive experience in data visualization and statistical modeling, I am well-prepared to use my analytical skills to support your Six Sigma initiatives.
While working at Facebook, I was part of a team that leveraged data analysis to identify key trends and areas for improvement, resulting in a reduction of processing bottlenecks by 30%. I am adept at using various data analysis tools to inform project decisions and drive quality enhancements.
I would welcome the opportunity to discuss how my analytical expertise can contribute to the success of [Company Name]. Thank you for your time and consideration.
Best regards,
Michael Martinez
---
### Sample 6
**Position number:** 6
**Position title:** Six Sigma Project Manager
**Position slug:** six-sigma-project-manager
**Name:** Jessica
**Surname:** Taylor
**Birthdate:** 1987-11-25
**List of 5 companies:** HP, Motorola, Boeing, Walgreens, Starbucks
**Key competencies:** Project leadership, stakeholder management, process redesign, risk assessment, strategic planning
---
[Your Address]
[City, State, Zip]
[Email]
[Phone Number]
[Date]
[Recipient's Name]
[Title]
[Company Name]
[Company Address]
[City, State, Zip]
Dear [Recipient's Name],
I am reaching out to apply for the Six Sigma Project Manager position at [Company Name]. With a solid background in project leadership and dedicated experience in process redesign, I am passionate about driving quality and operational excellence in organizations.
In my previous role at HP, I managed a project that integrated Six Sigma principles, successfully reducing project costs by 15% while ensuring delivery on time. I have extensive experience in engaging stakeholders at all levels, which has allowed me to effectively manage expectations and gain consensus on project objectives.
I am looking forward to the possibility of contributing my expertise to [Company Name] and helping to refine its operational processes further. Thank you for considering my application.
Warm regards,
Jessica Taylor
---
Feel free to adjust any of the details as necessary!
Six Sigma Skills for Your Resume: Boost Your Quality Management Career
Why This Six Sigma Skill is Important
Mastering the skill of data analysis is crucial in the Six Sigma methodology as it empowers organizations to identify inefficiencies and improve processes systematically. By diving deep into statistical tools and techniques, professionals are equipped to interpret complex data sets and uncover patterns that might not be immediately visible. This analytical approach facilitates informed decision-making, enabling teams to pinpoint the root causes of problems and deploy effective solutions. As a result, organizations can reduce defects, enhance quality, and drive profitability.
Furthermore, strong data analysis skills foster a culture of continuous improvement within an organization. When employees are adept at using data to guide their strategies, it encourages accountability and positions everyone as stakeholders in the company's quality initiatives. This collective effort not only enhances operational effectiveness but also boosts customer satisfaction, as businesses become more responsive to their clients’ needs. In essence, mastering data analysis is pivotal for achieving long-term success and sustainability in any organization embracing Six Sigma principles.
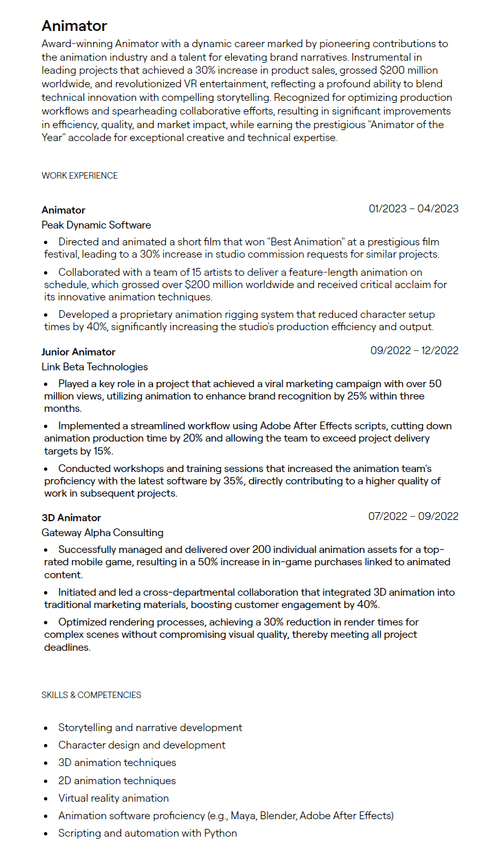
Six Sigma professionals play a crucial role in driving process improvement and enhancing operational efficiency across organizations. This skill demands a blend of analytical thinking, problem-solving abilities, and strong communication skills, as practitioners must identify inefficiencies, analyze data, and collaborate with teams to implement solutions. To secure a job in this field, acquiring relevant certifications, such as Six Sigma Green Belt or Black Belt, is essential, alongside gaining experience through internships or project involvement that highlights your ability to effect positive change. Continuous learning and networking within industry forums can also propel your career in Six Sigma.
Six Sigma Green Belt Certification: What is Actually Required for Success?
Sure! Here are ten bullet points outlining what is actually required for success in Six Sigma skills, along with brief descriptions for each:
Strong Analytical Skills
- Success in Six Sigma requires the ability to analyze complex data sets. Professionals must be adept at identifying trends, patterns, and root causes of problems to enhance processes effectively.
Statistical Knowledge
- A foundational understanding of statistics is crucial. This includes knowledge of concepts like standard deviation, hypothesis testing, and control charts, which serve as the backbone for data-driven decision-making in Six Sigma.
Process Mapping and Flowcharting
- The ability to visualize processes through mapping techniques is essential. This allows Six Sigma practitioners to understand current workflows, identify inefficiencies, and implement targeted improvements.
Project Management Skills
- Six Sigma is inherently project-based, requiring good project management skills. This includes planning, organizing, and executing projects effectively while managing timelines, resources, and team dynamics.
Cross-Functional Team Collaboration
- Six Sigma often involves working with diverse teams across various departments. Effective communication and collaboration skills are necessary to ensure stakeholder buy-in and harness different perspectives toward a common goal.
Problem-Solving Mindset
- A proactive approach to problem-solving is vital. Six Sigma professionals should be prepared to tackle challenges head-on, using structured methodologies to devise innovative solutions.
Focus on Customer Requirements
- Understanding customer needs is central to Six Sigma methodology. Practitioners must effectively translate customer feedback into actionable improvement initiatives to enhance overall satisfaction.
Continuous Learning and Adaptability
- The Six Sigma environment is dynamic, requiring professionals to stay updated with the latest tools and techniques. A commitment to continuous learning and flexibility in adapting to changes are key to long-term success.
Change Management Expertise
- Implementing Six Sigma initiatives often requires significant changes in processes and culture. Understanding change management principles helps in effectively guiding teams through transitions and overcoming resistance.
Certification and Training
- While not mandatory, gaining formal Six Sigma certification (such as Green Belt or Black Belt) ensures a comprehensive understanding of the methodology. Certification can enhance credibility and career prospects in the field.
These points outline the multifaceted skill set necessary for success in Six Sigma, combining technical knowledge, soft skills, and practical experience.
Sample Mastering Six Sigma: Unlocking Excellence in Process Improvement skills resume section:
When crafting a resume highlighting Six Sigma skills, it's crucial to emphasize relevant certifications, such as Six Sigma Black Belt or Green Belt, alongside your experience in process improvement projects. Clearly articulate specific methodologies and tools used, such as DMAIC or statistical analysis software. Quantify achievements with measurable outcomes, like percentage reductions in defects or improvements in efficiency. Additionally, showcase key competencies such as teamwork, leadership, and data-driven decision-making. Tailor your resume to match the job description, demonstrating how your expertise aligns with the organization's goals and needs in process optimization and quality management.
• • •
We are seeking a Six Sigma Specialist to drive process improvement initiatives within our organization. The ideal candidate will possess advanced knowledge of Six Sigma methodologies and tools, including DMAIC (Define, Measure, Analyze, Improve, Control). Responsibilities include analyzing operational data, identifying inefficiencies, and implementing data-driven solutions to enhance quality and reduce costs. Strong leadership skills are essential to facilitate cross-functional teams and promote a culture of continuous improvement. Candidates should have relevant certifications (e.g., Green Belt or Black Belt) and experience in project management. Excellent communication and analytical skills are a must for effective stakeholder engagement.
WORK EXPERIENCE
- Led a cross-functional team to implement Six Sigma strategies that improved production efficiency by 25%, resulting in a $1.5 million increase in annual revenue.
- Developed and executed a comprehensive training program on Six Sigma methodologies, resulting in a 40% reduction in process defects across departments.
- Utilized advanced statistical tools to analyze process data, identify root causes of inefficiencies, and propose actionable improvement strategies.
- Created compelling presentations and reports to communicate project outcomes and strategic recommendations to senior leadership, enhancing stakeholder engagement.
- Implemented Six Sigma tools that reduced product return rates by 30%, contributing significantly to corporate sales growth.
- Conducted root cause analysis on quality failures and collaborated with engineering teams to deploy corrective measures, achieving a 15% reduction in manufacturing errors.
- Facilitated workshops to train team members on Six Sigma principles and quality improvement processes, fostering a culture of continuous improvement.
- Recognized for Excellence in Quality Management by the executive team for outstanding commitment to minimizing defects and enhancing product reliability.
- Drove process mapping and analysis for key operational flows, leading to a streamlining initiative that improved overall operational efficiency by 20%.
- Developed KPIs to monitor ongoing process improvements and implemented corrective actions that led to a 10% reduction in operational costs.
- Collaborated with suppliers to initiate Six Sigma-based quality improvement projects, achieving significant reductions in material waste and costs.
- Presented project outcomes and strategic initiatives to C-suite executives, receiving commendation for clarity and impact in storytelling.
- Analyzed customer feedback and sales data to identify opportunities for process optimization, which led to the launch of a new product line generating $3 million in additional revenue.
- Conducted market analysis and performance assessments that facilitated the implementation of Six Sigma methodologies, leading to improved customer satisfaction scores.
- Created data visualizations and reports that effectively communicated insights and guided decision-making at the management level.
- Received the Analyst of the Year award for outstanding performance and contributions to the company’s strategic goals.
SKILLS & COMPETENCIES
Certainly! Here’s a list of 10 skills related to a job position focused on Six Sigma:
- Statistical Analysis: Proficiency in statistical methods to analyze data and identify trends.
- Process Mapping: Ability to create detailed process maps to visualize workflows and identify areas for improvement.
- Root Cause Analysis: Skill in identifying underlying causes of defects or inefficiencies using techniques such as the 5 Whys or Fishbone diagrams.
- Project Management: Capability to plan, execute, and oversee projects effectively within timelines and budgets.
- Lean Methodologies: Knowledge of Lean principles to eliminate waste and optimize processes.
- Data Collection and Management: Expertise in gathering, organizing, and managing data for quality improvement projects.
- Change Management: Ability to lead and manage organizational change initiatives in a way that ensures buy-in from stakeholders.
- Team Leadership: Experience in leading cross-functional teams towards achieving quality improvement goals.
- Communication Skills: Strong verbal and written communication skills for reporting findings and collaborating with team members.
- Software Proficiency: Familiarity with Six Sigma tools and software (e.g., Minitab, Excel) for data analysis and process improvement.
These skills are essential for effectively implementing Six Sigma methodologies and driving quality improvement initiatives.
COURSES / CERTIFICATIONS
Here’s a list of five certifications or complete courses related to Six Sigma skills, along with their associated dates:
Certified Six Sigma Green Belt (CSSGB)
- Offered by: ASQ (American Society for Quality)
- Duration: Self-paced (approximately 3-4 months)
- Next Start Date: January 2024
Six Sigma Black Belt Certification
- Offered by: IASSC (International Association for Six Sigma Certification)
- Duration: Self-paced (approximately 4-6 months)
- Next Start Date: February 2024
Lean Six Sigma Yellow Belt Training
- Offered by: Coursera (through various universities, e.g., University System of Georgia)
- Duration: 4 weeks (approx. 3-5 hours per week)
- Next Start Date: January 15, 2024
Six Sigma Master Black Belt Certification
- Offered by: ASQ (American Society for Quality)
- Duration: Self-paced (approximately 5-6 months)
- Next Start Date: March 2024
Six Sigma Process Improvement (Online Course)
- Offered by: Udemy
- Duration: 10 hours (on-demand, self-paced)
- Available: Ongoing, enroll anytime
Make sure to confirm the dates and availability as they may change or have different cohorts.
EDUCATION
Here is a list of educational qualifications related to Six Sigma skills:
Bachelor’s Degree in Industrial Engineering
- Institution: [University Name]
- Dates: September 2015 - June 2019
Master’s Degree in Quality Assurance or Operations Management
- Institution: [University Name]
- Dates: September 2019 - June 2021
Six Sigma Green Belt Certification
- Institution: [Certification Body Name]
- Dates: January 2021
Six Sigma Black Belt Certification
- Institution: [Certification Body Name]
- Dates: March 2023
(Note: Replace "[University Name]" and "[Certification Body Name]" with specific institutions as needed.)
Certainly! Here are 19 important hard skills that professionals involved in Six Sigma should possess, with descriptions for each:
Statistical Analysis
- Proficiency in statistical concepts is crucial, as it allows professionals to analyze data effectively and identify trends. This skill helps in understanding variation and the capabilities of processes.
Process Mapping
- The ability to create process maps helps visualize workflows, making it simpler to identify inefficiencies. Process mapping is essential for understanding the current state and pinpointing areas for improvement.
Root Cause Analysis
- Root cause analysis (RCA) is a structured method for identifying the underlying causes of problems. This skill is fundamental in ensuring that solutions address the source of issues rather than just their symptoms.
Control Charts
- Knowledge of control charts enables professionals to monitor process stability over time. This skill is important for distinguishing between common and special cause variations.
Failure Mode and Effects Analysis (FMEA)
- FMEA is a systematic approach for evaluating processes to identify potential failure modes and their impact. Mastering this skill helps prioritize risks and implement mitigations effectively.
Design of Experiments (DOE)
- DOE is a statistical method for planning experiments to maximize the information gained. Professionals skilled in DOE can design experiments that highlight the relationships between factors and responses.
Lean Methodology
- Understanding Lean principles is vital for identifying and eliminating waste in processes. Knowledge of Lean tools contributes to improving efficiency and customer value in project outcomes.
Project Management
- Strong project management skills are essential for planning, executing, and closing Six Sigma projects. Effective project management ensures that projects stay on schedule and within budget, while meeting quality standards.
Capability Analysis
- Capability analysis helps in assessing how well a process meets specifications. This skill enables professionals to evaluate process performance and understand the likelihood of producing defects.
Data Collection Techniques
- Mastery of data collection techniques is essential for gathering accurate and relevant information. This skill ensures that the results of Six Sigma projects are based on reliable data.
SIPOC Diagrams
- Skills in creating Supplier-Input-Process-Output-Customer (SIPOC) diagrams help clarify the high-level processes involved. This visualization aids in understanding the interactions and relationships within a process.
Value Stream Mapping
- Value stream mapping (VSM) is a Lean tool used to visualize the flow of materials and information. Proficiency in VSM allows professionals to identify waste and optimize the flow of processes effectively.
Regression Analysis
- Understanding regression analysis is critical for exploring relationships between variables. This skill aids in predictive analysis and helps in identifying key drivers affecting process performance.
Poka-Yoke (Error Proofing)
- Poka-Yoke techniques focus on designing processes that prevent errors from occurring. Knowledge of this skill is crucial for creating foolproof processes that enhance quality control.
Benchmarking
- Benchmarking involves comparing process performance against best-in-class organizations. This skill helps identify areas for improvement and implement best practices within a company.
Time Series Analysis
- Proficiency in time series analysis helps professionals forecast future trends based on historical data. This skill is valuable in demand planning and capacity management within processes.
Hypothesis Testing
- This statistical method allows professionals to make informed decisions based on sample data. Mastery of hypothesis testing is essential for validating assumptions and improving processes.
Cost-Benefit Analysis
- Skills in cost-benefit analysis enable professionals to evaluate the financial implications of potential improvements. This analysis is crucial for supporting decision-making regarding project selection and resource allocation.
Communication of Findings
- Effectively communicating statistical findings and insights is key to engaging stakeholders. This skill ensures that data-driven recommendations are understood and acted upon by team members and decision-makers.
These hard skills are integral to the practice of Six Sigma and contribute significantly to the success of process improvement initiatives.
Job Position Title: Quality Assurance Manager
Six Sigma Methodology: Proficient in executing and applying Six Sigma principles and tools to improve quality and eliminate defects in processes.
Statistical Analysis: Skilled in the use of statistical methods and tools (like Minitab, SPSS) for data analysis, process control, and monitoring performance metrics.
Root Cause Analysis: Expertise in conducting root cause analysis using techniques such as Fishbone diagrams and 5 Whys to identify and rectify underlying issues.
Process Mapping and Improvement: Ability to create process maps and identify areas for improvement through value stream mapping and workflow analysis.
Project Management: Experience in managing quality improvement projects from initiation to completion, ensuring alignment with organizational goals and timelines.
Regulatory Knowledge: Familiarity with industry standards and regulatory requirements (e.g., ISO 9001, FDA regulations) that impact quality assurance practices.
Training and Development: Capability to design and deliver training programs on quality standards, Six Sigma tools, and methodologies to team members and stakeholders.
Generate Your Cover letter Summary with AI
Accelerate your Cover letter crafting with the AI Cover letter Builder. Create personalized Cover letter summaries in seconds.
Related Resumes:
Generate Your NEXT Resume with AI
Accelerate your Resume crafting with the AI Resume Builder. Create personalized Resume summaries in seconds.