Lean Manufacturing Resume Examples: 16 Effective Templates to Guide You
---
### Sample 1
**Position number:** 1
**Person:** 1
**Position title:** Lean Manufacturing Engineer
**Position slug:** lean-manufacturing-engineer
**Name:** James
**Surname:** Smith
**Birthdate:** 1985-04-15
**List of 5 companies:** Toyota, General Motors, Boeing, Lockheed Martin, Honeywell
**Key competencies:** Lean Six Sigma, Process Optimization, Value Stream Mapping, Kaizen Implementation, Root Cause Analysis
---
### Sample 2
**Position number:** 2
**Person:** 2
**Position title:** Continuous Improvement Manager
**Position slug:** continuous-improvement-manager
**Name:** Sarah
**Surname:** Johnson
**Birthdate:** 1978-09-23
**List of 5 companies:** Ford, Siemens, ABB, Procter & Gamble, 3M
**Key competencies:** Change Management, Performance Metrics, Employee Training, Workflow Analysis, Statistical Process Control
---
### Sample 3
**Position number:** 3
**Person:** 3
**Position title:** Process Improvement Specialist
**Position slug:** process-improvement-specialist
**Name:** Rakesh
**Surname:** Patel
**Birthdate:** 1990-01-10
**List of 5 companies:** Intel, Merck, Coca-Cola, Nestlé, Philips
**Key competencies:** Lean Tools Application, Lean Audits, Cross-Functional Collaboration, Data Analysis, Risk Management
---
### Sample 4
**Position number:** 4
**Person:** 4
**Position title:** Lean Production Supervisor
**Position slug:** lean-production-supervisor
**Name:** Maria
**Surname:** Gonzalez
**Birthdate:** 1982-06-30
**List of 5 companies:** Amazon, Unilever, Caterpillar, Prologis, Lockheed Martin
**Key competencies:** Team Leadership, Just-in-Time Manufacturing, Inventory Management, Process Mapping, Performance Improvement
---
### Sample 5
**Position number:** 5
**Person:** 5
**Position title:** Value Stream Manager
**Position slug:** value-stream-manager
**Name:** Robert
**Surname:** Brown
**Birthdate:** 1987-11-05
**List of 5 companies:** GE Aviation, PepsiCo, Dell Technologies, Johnson & Johnson, BMW
**Key competencies:** Value Stream Design, Cost Reduction Strategies, Project Management, Analytical Problem Solving, Supplier Collaboration
---
### Sample 6
**Position number:** 6
**Person:** 6
**Position title:** Lean Quality Assurance Analyst
**Position slug:** lean-quality-assurance-analyst
**Name:** Lisa
**Surname:** Wang
**Birthdate:** 1992-08-18
**List of 5 companies:** Xerox, Samsung, Tesla, Fujitsu, Honeywell
**Key competencies:** Quality Control Systems, ISO Compliance, Audit Management, Quality Improvement Tools, Lean Methodology Training
---
These resume samples encompass various aspects of lean manufacturing and show diverse paths professionals can take within the field.
We are seeking a dynamic Lean Manufacturing Leader with a proven track record of driving operational excellence and enhancing production efficiency. With a history of implementing successful lean initiatives, this position demands a results-oriented professional who has led cross-functional teams to achieve significant waste reduction and cost savings. The ideal candidate will possess a deep technical expertise in lean principles and methodologies, and have experience in conducting impactful training programs that empower employees at all levels. By fostering a culture of continuous improvement, this leader will collaborate closely with stakeholders to optimize processes, ensuring sustainable growth and increased productivity.
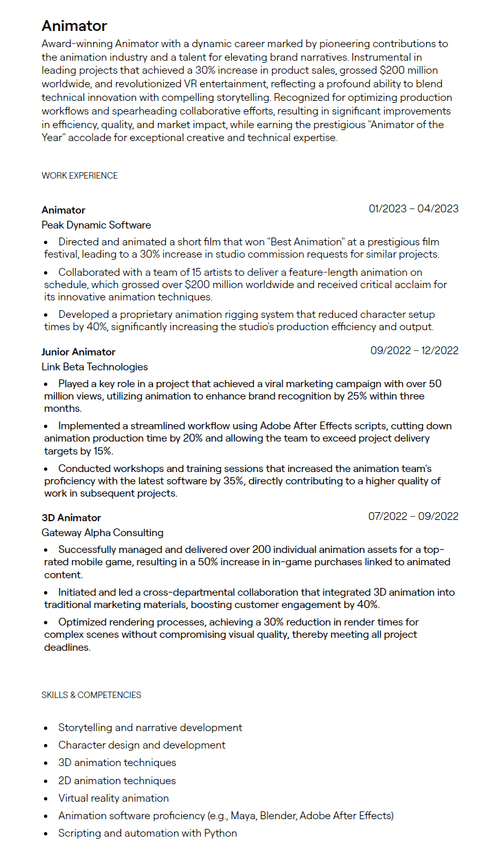
Lean manufacturing is a systematic approach aimed at minimizing waste while maximizing productivity, playing a crucial role in enhancing operational efficiency across industries. Professionals in this field need talents in problem-solving, critical thinking, and strong communication skills to foster collaboration and drive continuous improvement. Familiarity with lean tools such as Six Sigma, Kaizen, and Value Stream Mapping is essential. To secure a job in lean manufacturing, candidates should pursue relevant certifications, gain hands-on experience through internships, and showcase their ability to implement lean principles in real-world scenarios during the application process. Networking within manufacturing communities can also enhance job prospects.
Common Responsibilities Listed on Lean Manufacturing Position Titles Resumes:
Here are 10 common responsibilities often listed on lean manufacturing resumes:
Process Improvement: Identifying inefficiencies in production processes and implementing lean methodologies to enhance workflow and reduce waste.
Value Stream Mapping: Creating and analyzing value stream maps to visualize processes, eliminate non-value-adding activities, and improve overall efficiency.
5S Implementation: Applying the 5S (Sort, Set in order, Shine, Standardize, Sustain) methodology to maintain an organized and efficient workspace.
Kaizen Facilitation: Leading Kaizen events to drive continuous improvement initiatives involving cross-functional teams to foster a culture of ongoing enhancement.
Standard Operating Procedures (SOPs): Developing, documenting, and enforcing standard operating procedures to ensure consistency and quality in manufacturing processes.
Data Analysis: Utilizing statistical tools to analyze production metrics, track performance, and make data-driven decisions for process optimization.
Training and Mentoring: Conducting training sessions for staff on lean principles and practices to promote understanding and adoption throughout the organization.
Cross-Functional Collaboration: Working closely with engineering, quality assurance, and production teams to align processes and improve overall manufacturing efficiency.
Problem Solving: Employing root cause analysis techniques (such as 8D or Fishbone diagrams) to diagnose and resolve production issues promptly.
Performance Monitoring: Setting key performance indicators (KPIs) and conducting regular assessments to evaluate the effectiveness of lean initiatives and drive accountability.
When crafting a resume for a Lean Manufacturing Engineer, it's essential to emphasize relevant engineering experience and technical skills in Lean Six Sigma and process improvement methodologies. Highlight successful projects demonstrating value stream mapping and root cause analysis. Include experience in recognized companies, showcasing industry expertise. Additionally, focus on project management capabilities, emphasizing leadership in driving efficiency and quality improvements. Certifications related to Lean principles should be listed prominently. Tailoring the resume to reflect quantifiable achievements will further strengthen the application, aligning it with the specific needs of potential employers in lean manufacturing environments.
WORK EXPERIENCE
SKILLS & COMPETENCIES
COURSES / CERTIFICATIONS
Here are five certifications or completed courses for John Smith, the Lean Manufacturing Engineer:
Lean Six Sigma Green Belt Certification
- Date: March 2018
Certified Lean Manufacturing Engineer (CLME)
- Date: November 2019
Value Stream Mapping Workshop
- Date: June 2020
Root Cause Analysis Training
- Date: February 2021
Project Management Professional (PMP) Certification
- Date: September 2021
EDUCATION
- Bachelor of Science in Mechanical Engineering, University of Michigan, 2007
- Master of Science in Industrial Engineering, Georgia Institute of Technology, 2010
When crafting a resume for the Continuous Improvement Specialist position, it's crucial to highlight experience with Kaizen and other Lean tools such as 5S and Kanban. Emphasizing problem-solving skills, data analysis capabilities, and familiarity with performance metrics will demonstrate the candidate's ability to drive efficiency and effectiveness. Including industry-relevant experience from recognized companies can enhance credibility. Additionally, showcasing specific projects or accomplishments that resulted in measurable improvements will provide concrete evidence of the candidate's impact in previous roles. Clear, concise formatting and targeted keywords related to continuous improvement are also essential for catching the attention of hiring managers.
[email protected] • +1-234-567-8901 • https://www.linkedin.com/in/lindajohnson • https://twitter.com/lindajohnson
Dynamic Continuous Improvement Specialist with over 5 years of experience driving operational excellence in high-tech environments. Proficient in Kaizen, Lean Tools (5S, Kanban), and data analysis, I have a proven track record of enhancing performance metrics and fostering a culture of continuous improvement at renowned organizations such as 3M and Intel. With strong problem-solving skills and a passion for optimizing processes, I excel at collaborating cross-functionally to implement innovative solutions that result in increased efficiency and reduced operational costs. Committed to delivering exceptional results and empowering teams to achieve their full potential.
WORK EXPERIENCE
- Spearheaded a Kaizen initiative that improved production efficiency by 25% in the first 6 months.
- Developed and implemented a performance metrics system that enhanced data-driven decision-making across operations.
- Led cross-functional teams in the adoption of Lean Tools such as 5S and Kanban, achieving a 30% reduction in waste.
- Facilitated workshops that resulted in a 40% increase in employee engagement and buy-in for continuous improvement processes.
- Recognized with the 'Excellence in Innovation' award for contributions to process improvement and operational efficiency.
- Conducted root cause analysis on quality defects, leading to a 15% reduction in returns and complaints within the first year.
- Piloted Lean Six Sigma projects that decreased costs by $500,000 through optimized resource allocation.
- Utilized data analysis to identify performance bottlenecks, resulting in a 20% increase in overall equipment effectiveness (OEE).
- Implemented training programs on Lean tools across departments, enhancing team performance and understanding of continuous improvement methodologies.
- Collaborated with the supply chain team to improve inventory turnover by 18% through enhanced demand forecasting techniques.
- Advised multiple clients in the aerospace sector on strategies to implement Lean manufacturing practices, resulting in a 30% decrease in production lead times.
- Developed customized training materials and conducted sessions that equipped teams with Lean tools and methodologies.
- Monitored progress and facilitated consistent performance reviews to ensure continual alignment with Lean principles.
- Created value stream maps for various processes, successfully identifying waste and areas for improvement that led to increased overall throughput.
- Receieved 'Consultant of the Year' award for outstanding results achieved with client engagements.
- Led initiatives that improved service delivery times by 35% through process mapping and waste reduction strategies.
- Collaborated with IT to automate reporting systems, cutting down the processing time for performance reports by up to 50%.
- Facilitated team workshops that educated employees on Lean principles, resulting in a culture shift towards continuous improvement.
- Analyzed performance data, providing actionable insights that drove continuous enhancements in product quality.
- Contributed to a cross-departmental project that achieved a significant cost reduction of $1 million per year through optimized inventory management.
SKILLS & COMPETENCIES
COURSES / CERTIFICATIONS
EDUCATION
WORK EXPERIENCE
SKILLS & COMPETENCIES
Sure! Here is a list of 10 skills for David Brown, the Production Planner from Sample Resume 3:
- Resource Allocation
- Demand Forecasting
- Inventory Management
- Scheduling
- Lean Manufacturing Principles
- Production Workflow Optimization
- Capacity Planning
- Cost Analysis
- Team Collaboration
- Data Analysis and Reporting
COURSES / CERTIFICATIONS
EDUCATION
[email protected] • +1-234-567-8901 • https://www.linkedin.com/in/sarahwilson • https://twitter.com/sarahwilsonQA
Dedicated Quality Assurance Analyst with a strong background in enhancing product quality and operational efficiency. With experience in esteemed organizations like Johnson & Johnson and Medtronic, I excel in implementing Six Sigma methodologies and adhering to ISO standards. My key competencies include quality control, process auditing, and statistical process control (SPC), allowing me to identify root causes of issues and drive continuous improvement. A detail-oriented professional, I am committed to fostering a culture of quality and excellence, ensuring that products meet the highest standards while optimizing overall operational performance.
WORK EXPERIENCE
null
SKILLS & COMPETENCIES
- Quality Control
- Six Sigma Methodologies
- ISO Standards Compliance
- Process Auditing
- Statistical Process Control (SPC)
- Root Cause Analysis
- Risk Management
- Document Control
- Quality Improvement Initiatives
- Data Analysis and Reporting
COURSES / CERTIFICATIONS
Here’s a list of 5 certifications and courses for Sarah Wilson, the Quality Assurance Analyst from Sample Resume 4:
Certified Six Sigma Green Belt
Issued by: American Society for Quality (ASQ)
Date: March 2021ISO 9001:2015 Lead Auditor Training
Provider: International Register of Certificated Auditors (IRCA)
Date: November 2020Statistical Process Control (SPC) Training
Provider: Quality America
Date: June 2019Root Cause Analysis (RCA) Certification
Provider: Lean Methods Group
Date: September 2018Quality Management Systems (QMS) Overview Course
Provider: Coursera (offered by Rochester Institute of Technology)
Date: January 2017
EDUCATION
Here is a list of education for Sarah Wilson, the Quality Assurance Analyst from Sample Resume 4:
- Bachelor of Science in Chemical Engineering, University of Illinois at Urbana-Champaign, Graduated: May 2014
- Master of Science in Quality Assurance, California State University, Graduated: May 2016
When crafting a resume for an Operations Manager role in lean manufacturing, it's crucial to emphasize leadership skills, experience in implementing lean principles, and a strong understanding of supply chain management. Highlight key accomplishments related to cost reduction and performance improvements, showcasing the ability to drive efficiency and enhance operations. Include specific projects demonstrating successful team management and effective communication. Additionally, mention familiarity with relevant technologies and methodologies. Tailoring the resume to reflect the requirements of the position while aligning with industry standards will significantly enhance the candidate's appeal to potential employers.
[email protected] • +1-555-123-4567 • https://www.linkedin.com/in/jason-miller-operations • https://twitter.com/jasonmillerops
Results-driven Operations Manager with over 15 years of experience in leading lean initiatives within the manufacturing and food industries. Proven track record in implementing cost reduction strategies and improving operational efficiency at companies like Coca-Cola and Kraft Foods. Strong leadership skills with a focus on team development and supply chain management. Adept at leveraging lean operations principles to enhance performance and drive continuous improvement. Recognized for ability to foster a culture of excellence and collaboration, delivering superior results in dynamic environments. Passionate about optimizing processes and achieving organizational goals through innovative solutions.
WORK EXPERIENCE
- Led a cross-functional team to achieve a 20% reduction in operating costs through lean manufacturing principles.
- Implemented continuous improvement initiatives that increased production efficiency by 30%.
- Developed and executed a cost reduction strategy that resulted in annual savings of $2 million.
- Fostered a culture of safety and efficiency, leading to a 50% decrease in workplace incidents.
- Actively participated in product development initiatives that drove a 15% increase in sales in key markets.
- Managed supply chain operations, leading to a 40% improvement in delivery times.
- Developed performance metrics that enhanced productivity tracking across multiple departments.
- Facilitated workshops that trained over 50 employees on lean methodologies, improving team engagement.
- Collaborated with sales and marketing teams to align operational capabilities with market demands.
- Spearheaded a waste reduction project that cut raw material costs by 25%.
- Designed and implemented effective lean processes that streamlined production workflows and reduced lead times by up to 50%.
- Customized training programs that significantly improved employee knowledge on lean practices.
- Led troubleshooting teams to identify and mitigate production issues, resulting in a 98% customer satisfaction rating.
- Established supplier partnerships that enhanced quality standards and reduced material shortages.
- Drove a culture of continuous improvement, leading to several process innovations recognized company-wide.
- Implemented a comprehensive performance improvement strategy that increased overall equipment effectiveness (OEE) by 22%.
- Championed initiatives that integrated green practices into production, yielding reduced environmental footprints.
- Launched a team-based approach to problem-solving that fostered employee ownership of operational success.
- Conducted regular audits and data analysis to measure process effectiveness and identify areas for improvement.
- Initiated cross-training programs that enhanced workforce flexibility and reduced labor costs.
SKILLS & COMPETENCIES
Here is a list of 10 skills for Jason Miller, the Operations Manager from Sample Resume 5:
- Lean Operations Implementation
- Team Leadership and Development
- Supply Chain Optimization
- Cost Reduction Strategies
- Performance Improvement Metrics
- Strategic Planning and Execution
- Cross-Functional Collaboration
- Process Improvement Initiatives
- Data-Driven Decision Making
- Operational Excellence and Best Practices
COURSES / CERTIFICATIONS
Here are five certifications or completed courses for Jason Miller, the Operations Manager:
Certified Lean Operations Professional
Institution: Lean Certification Board
Date: June 2019Project Management Professional (PMP)
Institution: Project Management Institute (PMI)
Date: March 2020Six Sigma Black Belt Certification
Institution: ASQ (American Society for Quality)
Date: January 2021Supply Chain Management Certification
Institution: APICS (Association for Supply Chain Management)
Date: August 2022Leadership in Energy and Environmental Design (LEED) Green Associate
Institution: U.S. Green Building Council
Date: November 2021
EDUCATION
Sure! Here are the education details for Jason Miller (Sample Resume 5):
Bachelor of Science in Industrial Engineering
University of Michigan, Ann Arbor, MI
Graduated: May 2005Master of Business Administration (MBA)
Purdue University, West Lafayette, IN
Graduated: May 2010
When crafting a resume for a Lean Trainer/Facilitator, it's crucial to emphasize experience in training and development, showcasing the ability to design and deliver effective workshops. Highlight expertise in lean methodologies and continuous improvement culture, demonstrating a track record of fostering organizational growth. Include any relevant certifications, such as Lean Six Sigma, along with metrics that illustrate successful training outcomes. Additionally, stress interpersonal and communication skills, as the role requires engaging diverse teams and promoting collaboration. Listing experience with reputable companies in the manufacturing sector can also enhance credibility.
[email protected] • +1-555-0123 • https://www.linkedin.com/in/emilydavis • https://twitter.com/emily_davis
Dedicated Lean Trainer and Facilitator with over 20 years of experience in promoting continuous improvement and lean methodologies across diverse industries. Expertise in training development, workshop facilitation, and fostering a culture of organizational excellence. Proven track record of driving performance improvements at renowned companies like Dell Technologies, Toyota Motor Manufacturing, and PepsiCo. Passionate about empowering teams through engaging workshops and practical training, ensuring the effective implementation of lean principles. Committed to cultivating a continuous improvement mindset that enhances operational efficiency and boosts employee engagement.
WORK EXPERIENCE
- Developed and delivered over 50 training sessions focused on lean methodologies, resulting in a 30% improvement in team productivity.
- Facilitated workshops that led to a 25% reduction in waste across multiple departments, significantly enhancing operational efficiency.
- Implemented a continuous improvement culture that empowered team members to identify and resolve process inefficiencies independently.
- Collaborated with leadership to design and launch an organization-wide lean transformation initiative, leading to a 20% increase in global revenue.
- Recognized as 'Trainer of the Year' for exceptional commitment to fostering lean practices within the organization.
- Advised clients in the automotive industry on lean process improvements that increased overall production efficiency by 35%.
- Conducted root cause analysis to identify bottlenecks, implementing corrective actions that eliminated defects by 40%.
- Coached cross-functional teams on value stream mapping techniques, leading to enhanced understanding of workflow efficiencies.
- Developed customized training programs for client organizations, resulting in sustainable lean practices.
- Designed and executed operation training modules that improved employee engagement by 50%.
- Utilized storytelling techniques to simplify complex lean concepts, making them accessible to diverse teams.
- Championed process improvement projects that directly contributed to a 15% cost reduction in operational expenses.
- Facilitated lean workshops that encouraged team collaboration and innovation.
- Led a successful kaizen event that increased production throughput by 20% within a six-month period.
- Managed cross-functional teams to implement 5S methodology, creating a more organized and efficient workspace.
- Analyzed performance metrics to identify areas for improvement, contributing to a 30% reduction in cycle times.
- Presented actionable insights to senior management, aiding strategic decision-making related to lean initiatives.
SKILLS & COMPETENCIES
COURSES / CERTIFICATIONS
Here are five certifications or completed courses for Emily Davis, the Lean Trainer/Facilitator:
Lean Six Sigma Green Belt Certification
Issued by: American Society for Quality (ASQ)
Date: June 2018Certified Lean Practitioner
Issued by: Lean Enterprise Institute
Date: March 2019Kaizen Workshop Facilitation Training
Issued by: International Kaizen Institute
Date: November 2020Change Management Certification
Issued by: Prosci
Date: September 2021Training and Development Professional Course
Issued by: Association for Talent Development (ATD)
Date: January 2022
EDUCATION
Generate Your Resume Summary with AI
Accelerate your resume crafting with the AI Resume Builder. Create personalized resume summaries in seconds.
Resume Headline Examples:
Strong Resume Headline Examples
Weak Resume Headline Examples
Weak Resume Headline Examples for Lean Manufacturing:
- "Hardworking Individual with Some Lean Manufacturing Experience"
- "Entry-Level Employee Looking for Lean Manufacturing Opportunities"
- "Dedicated Team Player in the Manufacturing Sector"
Why These are Weak Headlines:
Lack of Specificity:
- The phrases "some experience" and "entry-level" are vague and do not communicate the candidate’s actual skills or achievements. This type of language fails to capture attention and does not highlight the unique value the individual brings to a potential employer.
Absence of Key Terms:
- The headlines do not incorporate essential industry-specific keywords (e.g., "Lean Six Sigma," "Process Improvement," "Kaizen"). Including these terms would demonstrate familiarity with lean manufacturing concepts and practices, helping the resume resonate better with hiring managers or applicant tracking systems (ATS).
Generic Language:
- Terms like "hardworking" or "dedicated team player" are overly generic and could apply to any candidate across various industries; they do not differentiate the candidate in the competitive field of lean manufacturing. A strong headline should convey the candidate's specialty or specific accomplishments related to lean principles, making them more memorable and impactful.
Resume Summary Examples:
Strong Resume Summary Examples
Lead/Super Experienced level
Senior level
Mid-Level level
Junior level
Entry-Level level
Weak Resume Summary Examples
Resume Objective Examples for :
Strong Resume Objective Examples
Lead/Super Experienced level
Senior level
Mid-Level level
Sure! Here are five strong resume objective examples for a mid-level professional specializing in lean manufacturing:
Results-Driven Lean Specialist: Seeking a mid-level position in lean manufacturing where I can leverage my 5+ years of experience in streamlining operations and reducing waste to enhance production efficiency and contribute to continuous improvement initiatives.
Process Improvement Advocate: Dedicated manufacturing professional with a proven track record of implementing lean principles in diverse environments, aiming to utilize my expertise in Kaizen and Six Sigma to drive operational excellence and foster a culture of innovation within your organization.
Lean Manufacturing Engineer: Aspiring to join a forward-thinking company as a Lean Manufacturing Engineer, where my skills in data analysis and cross-functional collaboration can directly contribute to achieving quality objectives and improving process workflows.
Supply Chain Efficiency Expert: Motivated mid-level specialist seeking to apply my hands-on experience in lean methodologies to optimize supply chain operations, reduce lead times, and increase profitability while ensuring high standards of customer satisfaction.
Continuous Improvement Leader: Looking to contribute my strong background in lean manufacturing and team leadership to an organization committed to operational excellence, focusing on driving sustainable improvements and fostering a culture of continuous learning and development.
Junior level
Here are five strong resume objective examples tailored for a junior-level position in lean manufacturing:
Detail-oriented graduate with a background in industrial engineering, seeking a junior lean manufacturing position to apply my knowledge of process optimization and waste reduction methodologies to improve operational efficiency.
Enthusiastic manufacturing technician with hands-on experience in applying lean principles, eager to contribute to a dynamic team by enhancing production processes and implementing cost-saving initiatives.
Passionate about continuous improvement, I aim to leverage my academic foundation in lean manufacturing concepts and team collaboration skills to assist in streamlining workflows and increasing productivity.
Results-driven individual with internship experience in lean projects, looking to secure a junior role where I can utilize my analytical skills and commitment to quality to support an organization in achieving its operational goals.
Recent engineering graduate with knowledge of Six Sigma and Kaizen methodologies, seeking to join a forward-thinking team to assist in driving lean transformations and delivering measurable improvements in production efficiency.
Entry-Level level
Sure! Here are five strong resume objective examples tailored for entry-level positions in lean manufacturing:
Objective: Motivated and detail-oriented recent graduate with a degree in Industrial Engineering seeking an entry-level position in lean manufacturing. Eager to apply knowledge of continuous improvement methodologies to enhance production efficiency and reduce waste.
Objective: Results-driven individual with foundational knowledge in lean principles and a passion for optimizing processes. Looking to contribute to a dynamic team focused on implementing lean strategies to improve operational excellence in a manufacturing environment.
Objective: Enthusiastic and analytical entry-level professional dedicated to advancing lean manufacturing initiatives. Aiming to leverage strong problem-solving skills and collaborative mindset to drive efficiencies and support quality improvements.
Objective: Detail-focused recent graduate with academic training in lean manufacturing techniques and hands-on internship experience. Excited to bring fresh perspectives and eagerness to learn to an entry-level role, helping to foster a culture of continuous improvement within the organization.
Objective: Aspiring lean manufacturing specialist with a solid internship experience in process improvement environments. Seeking an entry-level position to apply my strong analytical skills and commitment to teamwork in driving efficiency and reducing operational costs.
Weak Resume Objective Examples
When crafting an effective work experience section for a resume in lean manufacturing, it’s vital to focus on specificity, relevance, and results. Here’s a concise guide:
Tailor Your Content: Start by aligning your work experience with the job description. Highlight relevant roles that directly pertain to lean manufacturing principles—such as continuous improvement, waste reduction, and process optimization.
Use Action Verbs: Initiate bullet points with strong action verbs such as “implemented,” “analyzed,” “led,” and “streamlined.” This adds dynamism to your statements and emphasizes your active role in initiatives.
Quantify Achievements: Whenever possible, quantify your contributions. Use metrics to demonstrate the impact of your work, such as “Reduced production downtime by 20% through the implementation of a new scheduling system” or “Improved inventory turnover by 15% by applying Just-In-Time (JIT) strategies.”
Describe Methodologies: Specify the lean tools and methodologies you have employed. Mention techniques such as Value Stream Mapping, 5S, Kaizen, and Kanban. This showcases your familiarity with core concepts in lean manufacturing.
Highlight Team Collaboration: Lean manufacturing often involves cross-functional teams. Emphasize your ability to work collaboratively by noting your partnerships with engineering, production, and quality assurance teams to facilitate improvements.
Include Certifications and Training: If applicable, mention any relevant certifications (like Six Sigma or Lean Practitioner) or training sessions that enhanced your skills in lean methodologies.
Show Continuous Learning: Conclude with a commitment to continuous improvement, underscoring any professional development efforts, such as workshops or courses related to lean practices.
By clearly articulating your experiences and accomplishments, you can create a compelling work experience section that resonates with potential employers in the lean manufacturing sector.
Best Practices for Your Work Experience Section:
Here are 12 best practices for crafting the Work Experience section in a lean manufacturing context:
Use Action-Oriented Language: Start each bullet point with strong action verbs (e.g., "Implemented," "Streamlined," "Facilitated") to convey your contributions clearly.
Focus on Lean Principles: Highlight your experience with lean methodologies (e.g., 5S, Kaizen, Value Stream Mapping) to demonstrate your familiarity with the philosophy.
Quantify Achievements: Whenever possible, use specific metrics (e.g., reduced waste by 20%, improved efficiency by 15%) to illustrate the impact of your work.
Emphasize Problem-Solving: Describe situations where you identified problems and implemented lean solutions, showcasing your analytical skills and initiative.
Highlight Team Collaboration: Mention your experience working on cross-functional teams or leading initiatives, as collaboration is key in lean environments.
Showcase Continuous Improvement: Detail your role in continuous improvement projects, including any specific tools or frameworks you utilized.
Discuss Training and Mentoring: If applicable, include experiences where you trained or mentored colleagues on lean practices, illustrating your leadership and expertise.
Relate to Customer Focus: Demonstrate how your lean efforts improved customer satisfaction or product quality, aligning with the goal of delivering value.
Document Process Changes: Include examples of how you documented process changes or standard operating procedures (SOPs) to sustain improvements.
Utilize Industry Terminology: Use relevant industry vocabulary to show your knowledge and familiarity with lean practices and concepts.
Link Experience to Business Goals: Make connections between your work in lean manufacturing and broader business objectives, such as cost reduction and efficiency gains.
Keep it Relevant and Concise: Tailor your work experience to the specific position you’re applying for, focusing on the most relevant roles and achievements within lean manufacturing contexts.
By following these best practices, you can create a Work Experience section that effectively showcases your qualifications in lean manufacturing.
Strong Resume Work Experiences Examples
Work Experience Examples:
Lean Manufacturing Specialist at XYZ Manufacturing Co.
Successfully implemented lean methodologies resulting in a 30% reduction in waste and a 25% improvement in production efficiency within the first year. Led cross-functional teams in Kaizen events, promoting a culture of continuous improvement.Production Supervisor at ABC Fabricators
Managed a team of 25 employees while introducing 5S principles, which improved workplace organization and increased production capacity by 15%. Enhanced team performance through targeted training on lean techniques and real-time problem-solving.Process Improvement Analyst at DEF Automotive
Conducted thorough value stream mapping sessions that identified bottlenecks in the production line, leading to a 40% decrease in cycle time. Collaborated with multiple departments to streamline processes and achieve project goals ahead of schedule.
Why this is Strong Work Experience:
Quantifiable Achievements: Each bullet point contains measurable outcomes (e.g., percentage reductions in waste or cycle time), demonstrating impact and results that hiring managers find compelling.
Leadership and Collaboration: The examples highlight not only individual contributions but also the ability to lead teams and work collaboratively across departments, essential traits in lean manufacturing environments focused on continuous improvement.
Innovative Implementation of Lean Principles: Reference to specific lean methodologies (like Kaizen, 5S, and value stream mapping) showcases technical knowledge and expertise, indicating the candidate's strong grasp of lean concepts and their application in real-world scenarios.
Lead/Super Experienced level
Certainly! Here are five strong bullet points for a resume showcasing lean manufacturing work experience at a lead or senior level:
Implemented Lean Six Sigma methodologies across operations, resulting in a 30% reduction in waste and a 25% increase in production efficiency, which contributed to a significant boost in profitability.
Led cross-functional teams in Kaizen workshops, driving continuous improvement initiatives that enhanced workflow processes and improved cycle times by 20%, fostering a culture of accountability and innovation.
Developed and executed a comprehensive training program for over 100 employees on lean principles and tools, enhancing overall team competency and engagement, leading to a 40% decrease in defects.
Orchestrated the redesign of production layout using 5S principles, optimizing space utilization and reducing material handling time by 15%, which improved productivity and safety within the manufacturing environment.
Spearheaded the introduction of value stream mapping to identify bottlenecks and streamline operations, resulting in a 35% improvement in lead times and a strengthened supply chain resilience.
Senior level
Here are five strong resume work experience examples for a senior-level position in lean manufacturing:
Continuous Improvement Manager, XYZ Manufacturing Co.
Led a cross-functional team in the implementation of lean manufacturing principles, resulting in a 30% reduction in waste and a 25% increase in operational efficiency over two years. Developed and facilitated training programs on lean tools such as Kaizen, 5S, and value stream mapping for over 100 employees.Lean Operations Specialist, ABC Industries
Spearheaded multiple Kaizen events, successfully achieving a 15% increase in throughput and a 20% reduction in cycle time across key production lines. Collaborated with engineering and supply chain teams to redesign workflow processes, enhancing product delivery speed and customer satisfaction.Lean Six Sigma Black Belt, DEF Corporation
Managed and directed complex projects employing lean and Six Sigma methodologies, yielding over $1 million in annual savings through improved process efficiencies. Mentored junior engineers and team members in data analysis techniques and lean practices to foster a culture of continuous improvement.Process Improvement Director, GHI Tech
Oversaw the strategic deployment of lean methodologies across all manufacturing sites, successfully leading a transformation that improved operational performance metrics by 40% within one year. Established a robust performance management system to monitor key indicators and sustain lean practices long-term.Manufacturing Excellence Leader, JKL Enterprises
Championed lean initiatives that integrated automated systems with manual processes, enhancing overall equipment effectiveness (OEE) by 35%. Collaborated with leadership to drive a cultural shift towards lean thinking, resulting in a 50% reduction in lead time and significantly improved employee engagement in process optimization efforts.
Mid-Level level
Certainly! Here are five bullet point examples for a mid-level resume focused on lean manufacturing experience:
Implemented Lean Six Sigma Initiatives: Led cross-functional teams in the adoption of Lean Six Sigma methodologies, reducing production waste by 25% and improving overall efficiency in the assembly line processes.
Value Stream Mapping (VSM) Expert: Conducted value stream mapping sessions to identify bottlenecks and optimize workflows, resulting in a 15% reduction in cycle time and enhanced product delivery to customers.
Kaizen Facilitation: Spearheaded multiple Kaizen events that fostered a culture of continuous improvement, empowering team members to identify and execute process enhancements that saved over $100,000 annually.
Training and Development: Designed and delivered training programs on Lean principles for over 100 employees, effectively increasing team engagement and accelerating the adoption of best practices across the organization.
Root Cause Analysis Implementation: Utilized root cause analysis techniques to troubleshoot production issues, leading to a 30% decrease in downtime and ultimately improving our OEE (Overall Equipment Effectiveness) metrics.
Junior level
Certainly! Here are five strong resume work experience examples for a junior-level candidate in lean manufacturing:
Production Assistant, ABC Manufacturing
Contributed to the implementation of 5S methodology on the production floor, leading to a 15% increase in workspace efficiency. Assisted in monitoring production metrics, helping to identify areas for process improvement.Lean Manufacturing Intern, XYZ Corp
Collaborated with the lean team to conduct value stream mapping sessions and identify waste in production processes. Participated in Kaizen events that resulted in a reduction of cycle time by 10%.Quality Control Analyst, DEF Industries
Supported quality improvement initiatives by collecting and analyzing data on production defects. Helped streamline inspection processes, reducing rework times by 20%.Manufacturing Technician, GHI Ltd.
Assisted in daily production activities while adhering to lean principles to enhance workflow. Contributed to cross-training efforts, allowing for greater flexibility and efficiency among team members.Warehouse Associate, JKL Distribution
Implemented FIFO (First In, First Out) inventory management practices, reducing product spoilage by 30%. Collaborated with the lean team to optimize warehouse layout, improving picking speeds and reducing travel time.
Entry-Level level
Here are five bullet points for strong resume work experience examples focused on lean manufacturing suitable for entry-level positions:
Lean Production Assistant, XYZ Manufacturing
Assisted in implementing lean manufacturing principles that reduced production cycle time by 15%, contributing to a more efficient workflow and minimizing waste.Process Improvement Intern, ABC Corp
Collaborated with the manufacturing team to identify areas for efficiency improvements, leading to the successful execution of a 5S initiative that enhanced workplace organization and safety.Quality Control Associate, DEF Industries
Monitored production processes and utilized root cause analysis to address quality issues, achieving a 10% reduction in defects while supporting continuous improvement initiatives.Manufacturing Technician, GHI Enterprises
Participated in cross-functional teams to apply lean tools, such as value stream mapping, resulting in optimized layouts and a smoother production flow.Production Line Operator, JKL Components
Operated machinery and engaged in daily Kaizen meetings to foster a culture of continuous improvement, leading to a significant increase in team productivity and morale.
Weak Resume Work Experiences Examples
Weak Resume Work Experience Examples for Lean Manufacturing
Manufacturing Associate at ABC Widgets (June 2020 - August 2021)
- Assisted in daily production tasks without a clear understanding of lean principles or methodologies.
- Followed existing processes but didn't suggest any process improvements or efficiencies.
Inventory Clerk at XYZ Industries (January 2019 - May 2020)
- Managed stock levels and assisted in inventory counts with little to no involvement in waste reduction strategies.
- Participated in team meetings but did not actively contribute to discussions on improving operational efficiency.
Quality Control Intern at 123 Manufacturing (Summer 2022)
- Monitored product quality, reported defects, and completed basic quality checks without implementing corrective actions to reduce defects.
- Shadowed team members without gaining hands-on experience in lean tools like 5S or Kaizen.
Why These are Weak Work Experiences
Lack of Proactivity and Initiative:
- The roles describe responsibilities that are largely reactive and do not involve any proactive engagement with lean methodologies. Employers in lean manufacturing look for candidates who not only understand these principles but also actively apply and advocate for them in their daily tasks.
Absence of Results and Impact:
- The experiences fail to highlight any measurable contributions to efficiency, cost savings, or productivity improvements. Lean manufacturing emphasizes the importance of quantifying results, such as a specific percentage reduction in waste or improvement in lead times, to demonstrate tangible impact.
Limited Engagement with Lean Practices:
- The examples indicate minimal exposure to core lean principles such as continuous improvement, value stream mapping, or root cause analysis. Employers prefer candidates who have hands-on experience with these methodologies and can demonstrate their ability to contribute to a lean culture and drive operational excellence.
Top Skills & Keywords for Resumes:
When crafting a resume for lean manufacturing roles, emphasize skills such as Kaizen, Six Sigma, Value Stream Mapping, and 5S methodology. Highlight experience in process improvement, waste reduction, and cross-functional teamwork. Include keywords like Continuous Improvement, Just-In-Time (JIT), Total Productive Maintenance (TPM), and Root Cause Analysis. Proficiency in data analysis tools and project management software can also set you apart. Showcase your ability to train and mentor teams in lean principles, ensuring a focus on measurable results and efficiency. Tailor your resume to include industry-specific terminology that aligns with the job description for best results.
Top Hard & Soft Skills for :
Hard Skills
Here's a table with 10 hard skills for lean manufacturing along with their descriptions:
Hard Skills | Description |
---|---|
Value Stream Mapping | A visual tool to analyze and optimize the flow of materials and information in a manufacturing process. |
5S Methodology | A workplace organization method that promotes efficiency and effectiveness through sorting, setting in order, shining, standardizing, and sustaining. |
Kaizen | A continuous improvement approach that seeks to identify and eliminate waste in processes through incremental changes. |
Lean Six Sigma | A combination of lean manufacturing principles and Six Sigma methodology to improve efficiency and reduce defects. |
Six Sigma | A data-driven approach focusing on process improvement and quality management through statistical analysis. |
Just-in-Time | An inventory management strategy that aligns production with demand, reducing waste and inventory costs. |
Poka-Yoke | Error-proofing techniques designed to prevent mistakes in manufacturing processes. |
Root Cause Analysis | A problem-solving method used to identify the underlying causes of defects or issues in a process. |
Supply Chain Management | The management of the flow of goods and services, including all processes that transform raw materials into final products. |
Total Quality Management | An organization-wide approach to continuous improvement of products, services, and processes through a focus on quality. |
This format allows easy navigation to detailed information about each skill.
Soft Skills
Here's a table with 10 soft skills for lean manufacturing along with their descriptions. Each skill is formatted with a link as specified:
Soft Skills | Description |
---|---|
Communication | The ability to convey information clearly and effectively to ensure understanding among team members. |
Collaboration | Working together with others to achieve common goals and foster a supportive work environment. |
Problem Solving | The capability to identify issues, analyze root causes, and develop effective solutions in a timely manner. |
Adaptability | The ability to adjust to changes and new challenges in the manufacturing process with a positive attitude. |
Leadership | Inspiring and guiding teams towards achieving their goals while maintaining a focus on lean principles. |
Critical Thinking | Analyzing situations logically and making informed decisions based on data and factual information. |
Time Management | Prioritizing tasks effectively while managing time to enhance productivity and efficiency in operations. |
Innovation | Encouraging creativity and new ideas to improve processes and products within a lean manufacturing environment. |
Emotional Intelligence | Recognizing and managing one's emotions and the emotions of others to improve team dynamics and communication. |
Attention to Detail | Ensuring accuracy and thoroughness in tasks to maintain quality and eliminate waste in manufacturing processes. |
Feel free to use or modify this table as needed!
Elevate Your Application: Crafting an Exceptional Cover Letter
Cover Letter Example: Based on Resume
Dear [Company Name] Hiring Manager,
I am excited to submit my application for the Lean Manufacturing position at [Company Name]. With over five years of hands-on experience in lean methodologies and a dedicated commitment to operational excellence, I am passionate about driving continuous improvement and efficiency within manufacturing environments.
In my previous role as a Lean Specialist at [Previous Company Name], I successfully led a team in implementing value stream mapping, which resulted in a 20% reduction in cycle time and a 15% increase in production efficiency. My technical expertise includes proficiency with industry-standard software such as Minitab, AutoCAD, and various ERP systems, which I leverage to analyze data effectively and optimize processes. This technical skillset has allowed me to conduct thorough analyses of workflows and implement data-driven solutions that align with the principles of lean manufacturing.
Collaboration has been key to my success; I thrive in team settings and actively engage cross-functional groups to foster innovative solutions. By conducting training sessions and workshops, I have empowered teams to adopt lean principles, enhancing their skill sets and embedding a culture of continuous improvement.
My achievements extend beyond just process enhancements; I have contributed significantly to achieving cost savings of over $200,000 annually through waste reduction and efficiency initiatives. This is a testament to my unwavering dedication to delivering measurable results while aligning with organizational goals.
I am truly excited about the possibility of joining [Company Name] and contributing to your reputation for excellence in lean manufacturing. I am confident that my skills and passion make me a valuable asset to your team. Thank you for considering my application; I look forward to the opportunity to discuss how I can contribute to your success.
Best regards,
[Your Name]
Crafting a cover letter for a lean-manufacturing position requires a targeted approach that showcases your understanding of lean principles, your relevant experience, and your ability to contribute to continuous improvement initiatives. Here’s how to structure your cover letter and what to include:
Structure of the Cover Letter
Header: Include your name, address, phone number, and email. Follow this by the date and the employer's contact information.
Salutation: Address the hiring manager by name if possible; otherwise, use a generic salutation like "Dear Hiring Manager."
Introduction: Start with a compelling opening that states the position you’re applying for and where you found the job listing. Briefly mention your current role or relevant experience and express enthusiasm for the opportunity.
Body Paragraphs:
- Lean Principles Knowledge: Emphasize your expertise in lean manufacturing methodologies, such as 5S, Kaizen, Value Stream Mapping, and Six Sigma. Provide specific examples of how you've successfully implemented these principles in previous roles.
- Quantifiable Achievements: Highlight measurable outcomes from your past experiences, such as increased efficiency, reduced waste, or improved production timelines. Use figures to illustrate the impact of your contributions.
- Problem Solving and Teamwork: Discuss your ability to identify problems and foster a culture of continuous improvement. Mention collaboration with teams to drive initiatives and achieve goals.
Closing Paragraph: Reinforce your enthusiasm for the position and express your desire to contribute to the organization. Mention your eagerness to discuss your qualifications in more detail during an interview.
Sign-off: Use a professional closing such as "Sincerely," followed by your name.
Tips for Crafting Your Cover Letter
- Tailor Your Content: Customize the letter to the specific job description by using keywords and phrases from the posting.
- Keep it Concise: Aim for one page; be clear and direct in your language.
- Professional Tone: Maintain a formal tone, but let your personality shine through to convey your passion for lean manufacturing.
- Proofread: Check for spelling and grammar mistakes to ensure professionalism.
By following these guidelines, you can create an impactful cover letter that presents you as a strong candidate for a lean-manufacturing role.
Resume FAQs for :
How long should I make my resume?
When crafting a resume for lean manufacturing, aim for a concise yet impactful length of one page, especially if you have less than 10 years of experience. Hiring managers typically prefer resumes that are easy to scan, so focusing on the most relevant skills and accomplishments is crucial.
For professionals with extensive experience or those in senior roles, a two-page resume may be acceptable. However, ensure that every line adds value; unnecessary information can dilute your key qualifications. Tailor your content to highlight lean manufacturing principles, methodologies like Six Sigma or Kaizen, and specific achievements that showcase your impact on efficiency, waste reduction, or process improvement.
Use bullet points for clarity instead of long paragraphs, and include measurable results to illustrate your contributions. This format not only enhances readability but also allows you to present your qualifications succinctly.
Additionally, customize your resume for each application to align with the job description, focusing on relevant skills and experiences that demonstrate your fit for the role. Summarily, keep your resume clear and focused, and strive for one page while remaining flexible to extend to two pages if necessary based on your experience.
What is the best way to format a resume?
When crafting a resume for a lean manufacturing role, clarity and relevance are key. Start with a clean, professional format: use clear headings, consistent font styles, and bullet points for easy readability.
Contact Information: At the top, include your name, phone number, email, and LinkedIn profile.
Professional Summary: Write a succinct summary that highlights your experience in lean manufacturing, your key accomplishments, and your technical skills.
Core Competencies: Include a section with relevant keywords such as Value Stream Mapping, 5S, Kaizen, and Continuous Improvement to align with job descriptions.
Professional Experience: List your work history in reverse chronological order. Focus on quantifiable achievements related to lean practices, such as reductions in waste or improvements in efficiency, using metrics when possible.
Education: Include degrees and relevant certifications (e.g., Six Sigma, Lean Green Belt) that bolster your qualifications in lean manufacturing.
Projects and Achievements: If applicable, add a section for specific projects demonstrating your direct impact on lean initiatives.
Tailoring: Customize your resume for each application, emphasizing skills and experiences that align closely with the specific position.
Overall, your resume should clearly convey your expertise and results-oriented mindset in lean manufacturing.
Which skills are most important to highlight in a resume?
When crafting a resume to showcase lean manufacturing skills, it's essential to highlight those that demonstrate efficiency, quality improvement, and teamwork. Key skills to focus on include:
Value Stream Mapping: Proficient in identifying waste and optimizing processes to enhance productivity.
Kaizen Principles: Experience in continuous improvement techniques, fostering an environment for incremental changes.
5S Methodology: Knowledge of Sort, Set in order, Shine, Standardize, and Sustain to ensure a clean and organized workspace, promoting efficiency.
Root Cause Analysis: Proficient in problem-solving methods, such as the Five Whys or Fishbone Diagram, to identify and resolve issues effectively.
Just-In-Time (JIT) Production: Familiar with JIT principles to reduce inventory costs and improve cash flow.
Cross-Functional Team Collaboration: Experience in working within diverse teams to promote communication and innovative solutions.
Lean Tools and Techniques: Proficient in using tools like Kanban, PDCA (Plan-Do-Check-Act), and Poka-Yoke (mistake-proofing).
Data Analysis: Ability to analyze metrics to drive decisions and improvements.
Emphasizing these skills can position you as a strong candidate capable of enhancing operational efficiency and driving continuous improvement in any manufacturing setting.
How should you write a resume if you have no experience as a ?
Writing a resume without direct experience in lean manufacturing can feel daunting, but you can effectively showcase relevant skills and interests. Begin with a clear objective statement that highlights your enthusiasm for lean principles and your desire to contribute to a manufacturing setting.
Next, leverage your educational background. If you've completed any courses related to operations management, quality control, or supply chain, make sure to list them prominently. Additionally, include any projects or research that demonstrate your understanding of lean concepts.
In the skills section, emphasize transferable skills such as problem-solving, teamwork, communication, and analytical thinking. Highlight any experience in similar fields, even if they aren't directly related to manufacturing, focusing on how those roles required efficiency and process improvements.
Consider including volunteer work or internships that may have involved relevant tasks, such as working in a team-oriented environment or participating in process optimization efforts.
Lastly, if you have certifications in lean methodologies, such as Six Sigma or Kaizen, be sure to list them. Your goal is to present yourself as a motivated candidate eager to learn and apply lean manufacturing principles, showcasing your potential rather than just your experience.
Professional Development Resources Tips for :
null
TOP 20 relevant keywords for ATS (Applicant Tracking System) systems:
Certainly! Here's a table featuring 20 relevant keywords for lean manufacturing, along with their descriptions. These keywords can help optimize your resume for ATS (Applicant Tracking Systems):
Keyword | Description |
---|---|
Lean Manufacturing | A systematic method for waste minimization within a manufacturing system without sacrificing productivity. |
Continuous Improvement | Ongoing efforts to improve products, services, or processes over time. |
Kaizen | A Japanese term meaning "change for better", often used to describe the practice of continuous improvement activities. |
Value Stream Mapping | A visual tool that helps analyze the flow of materials and information required to bring a product to the customer. |
Six Sigma | A set of techniques and tools for process improvement aimed at reducing defects and variability. |
Process Optimization | Streamlining production processes to enhance efficiency and reduce cycle times. |
Waste Reduction | Strategies and practices aimed at eliminating non-value-added activities in the production process. |
5S | A methodology that focuses on workplace organization and standardization (Sort, Set in order, Shine, Standardize, Sustain). |
Just-In-Time (JIT) | An inventory strategy that aligns raw-material orders with production schedules to minimize inventory costs. |
Root Cause Analysis | A problem-solving technique used to identify the underlying causes of issues rather than just focusing on symptoms. |
Standard Work | Documented best practices for performing a job safely and effectively, serving as a baseline for improvements. |
Kanban | A scheduling system for lean and just-in-time production that uses visual signals to control work-in-progress. |
Gemba | A Japanese term meaning "the real place," commonly used in lean practices to denote going into the field to observe. |
Cross-Functional Teams | Groups composed of members from different departments that collaborate to improve processes and solve problems. |
Statistical Process Control | A method of quality control using statistical methods to monitor and control a process. |
Total Quality Management | An organization-wide approach to continuous improvement focusing on customer satisfaction through quality control. |
Cycle Time Reduction | Strategies aimed at decreasing the time taken to complete a process or produce a product. |
Visual Management | Use of visual tools to convey information quickly and increase transparency within processes. |
Supplier Relationship Management | A systematic approach to evaluating suppliers to enhance performance and overall supply chain efficiency. |
Change Management | Techniques and strategies for managing and adapting to changes in the workplace or processes effectively. |
When crafting your resume, try to incorporate these keywords naturally into your work experience, skills, and accomplishments to align with the expectations of hiring managers in the lean manufacturing field.
Sample Interview Preparation Questions:
Sure! Here are five sample interview questions related to lean manufacturing:
Can you explain the key principles of lean manufacturing and how they contribute to operational efficiency?
Describe a specific instance where you implemented a lean tool or methodology. What challenges did you face, and what were the results?
How do you identify and eliminate waste in a production process? Can you provide an example?
What role does teamwork play in a successful lean manufacturing environment, and how do you foster a culture of continuous improvement among team members?
How do you measure the effectiveness of lean initiatives within a manufacturing system? What metrics do you find most useful?
Related Resumes for :
Generate Your NEXT Resume with AI
Accelerate your resume crafting with the AI Resume Builder. Create personalized resume summaries in seconds.