Factory Manager Resume Examples: 6 Templates to Boost Your Career
---
**Sample**
- **Position number:** 1
- **Person:** 1
- **Position title:** Production Supervisor
- **Position slug:** production-supervisor
- **Name:** John
- **Surname:** Smith
- **Birthdate:** March 14, 1985
- **List of 5 companies:** GE, Siemens, Honeywell, Ford, Lockheed Martin
- **Key competencies:** Team leadership, process optimization, quality control, lean manufacturing, safety compliance
---
**Sample**
- **Position number:** 2
- **Person:** 2
- **Position title:** Quality Assurance Manager
- **Position slug:** quality-assurance-manager
- **Name:** Sarah
- **Surname:** Johnson
- **Birthdate:** June 22, 1990
- **List of 5 companies:** Toyota, Bosch, Procter & Gamble, Nestlé, Unilever
- **Key competencies:** Quality management systems, root cause analysis, regulatory compliance, training and development, statistical process control
---
**Sample**
- **Position number:** 3
- **Person:** 3
- **Position title:** Maintenance Manager
- **Position slug:** maintenance-manager
- **Name:** Michael
- **Surname:** Brown
- **Birthdate:** January 5, 1980
- **List of 5 companies:** Boeing, Caterpillar, DuPont, 3M, General Motors
- **Key competencies:** Preventive maintenance, troubleshooting, team management, budget management, continuous improvement
---
**Sample**
- **Position number:** 4
- **Person:** 4
- **Position title:** Supply Chain Coordinator
- **Position slug:** supply-chain-coordinator
- **Name:** Emily
- **Surname:** Davis
- **Birthdate:** November 16, 1992
- **List of 5 companies:** Amazon, Walmart, Nestlé, Samsung, Dell
- **Key competencies:** Inventory management, logistics optimization, vendor negotiation, data analysis, process improvement
---
**Sample**
- **Position number:** 5
- **Person:** 5
- **Position title:** Safety Coordinator
- **Position slug:** safety-coordinator
- **Name:** David
- **Surname:** Wilson
- **Birthdate:** April 8, 1983
- **List of 5 companies:** ExxonMobil, Pfizer, Schlumberger, Nestlé, ArcelorMittal
- **Key competencies:** Safety training, incident investigation, regulatory compliance, risk assessment, emergency response planning
---
**Sample**
- **Position number:** 6
- **Person:** 6
- **Position title:** Operations Analyst
- **Position slug:** operations-analyst
- **Name:** Jessica
- **Surname:** Lee
- **Birthdate:** July 30, 1991
- **List of 5 companies:** Intel, PepsiCo, Bayer, Hyundai, Lockheed Martin
- **Key competencies:** Data analysis, project management, operational efficiency, cost reduction strategies, cross-departmental collaboration
---
Feel free to tweak any sections or details that you would like to alter based on your needs.
### Sample 1
**Position number:** 1
**Position title:** Production Supervisor
**Position slug:** production-supervisor
**Name:** James
**Surname:** Thompson
**Birthdate:** 1985-03-15
**List of 5 companies:** Ford, General Motors, Boeing, Tesla, Caterpillar
**Key competencies:** Team leadership, Process optimization, Safety compliance, Inventory management, Quality assurance.
---
### Sample 2
**Position number:** 2
**Position title:** Quality Control Manager
**Position slug:** quality-control-manager
**Name:** Emily
**Surname:** Robinson
**Birthdate:** 1990-07-22
**List of 5 companies:** Procter & Gamble, Nestlé, Johnson & Johnson, Coca-Cola, Unilever
**Key competencies:** Quality management systems, Statistical process control, Auditing, Root cause analysis, Regulatory compliance.
---
### Sample 3
**Position number:** 3
**Position title:** Maintenance Supervisor
**Position slug:** maintenance-supervisor
**Name:** Michael
**Surname:** Garcia
**Birthdate:** 1983-11-02
**List of 5 companies:** PepsiCo, GE Appliances, Honeywell, Siemens, Samsung
**Key competencies:** Preventive maintenance, Mechanical troubleshooting, Budget management, Staff training, Equipment reliability.
---
### Sample 4
**Position number:** 4
**Position title:** Supply Chain Coordinator
**Position slug:** supply-chain-coordinator
**Name:** Sarah
**Surname:** Patel
**Birthdate:** 1995-01-18
**List of 5 companies:** Amazon, Walmart, Nike, Adidas, Target
**Key competencies:** Supply chain logistics, Vendor management, Data analysis, Demand forecasting, ERP systems.
---
### Sample 5
**Position number:** 5
**Position title:** Safety Officer
**Position slug:** safety-officer
**Name:** David
**Surname:** Lee
**Birthdate:** 1988-09-10
**List of 5 companies:** ExxonMobil, Chevron, Schlumberger, DuPont, BASF
**Key competencies:** Safety regulations compliance, Risk assessment, Incident investigation, Training development, Emergency response planning.
---
### Sample 6
**Position number:** 6
**Position title:** Logistics Manager
**Position slug:** logistics-manager
**Name:** Rachel
**Surname:** Smith
**Birthdate:** 1992-05-30
**List of 5 companies:** FedEx, DHL, UPS, Maersk, XPO Logistics
**Key competencies:** Warehouse management, Transportation optimization, Cost reduction strategies, Team collaboration, Supply chain integration.
---
These samples cover different aspects of factory management and demonstrate diverse competencies associated with various subpositions.
Factory Manager Resume Examples: Stand Out with These 6 Templates
We are seeking a dynamic Factory Manager with a proven track record in enhancing operational efficiency and driving production excellence. The ideal candidate will have successfully implemented lean manufacturing principles, resulting in a 20% reduction in waste and a 15% increase in output. This leader thrives in collaborative environments, fostering strong teamwork and cross-departmental communication to ensure seamless operations. With technical expertise in modern manufacturing technologies and a commitment to staff development, the Factory Manager will conduct training programs that elevate workforce skills, ultimately enhancing productivity and maintaining high-quality standards across all production lines.
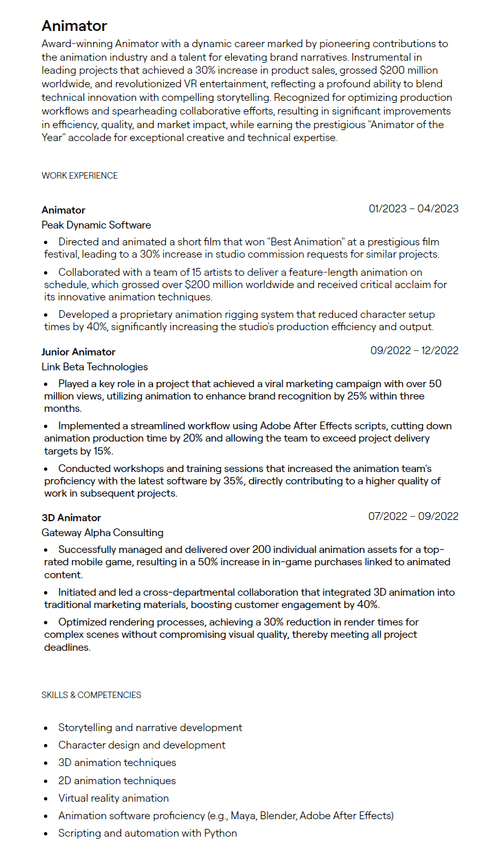
A factory manager plays a crucial role in ensuring seamless production operations, overseeing inventory management, quality control, and workforce efficiency. This position demands strong leadership skills, problem-solving abilities, and a deep understanding of manufacturing processes. Effective communication and team-building skills are essential, as the manager must collaborate with various departments to meet production goals. To secure a job in this field, candidates typically need relevant experience in manufacturing, a degree in industrial engineering or management, and a commitment to continuous improvement and safety standards. Networking, internships, and industry certifications can also enhance job prospects.
Common Responsibilities Listed on Factory Manager Resumes:
Here are 10 common responsibilities often listed on factory manager resumes:
Overseeing Production Operations: Manage day-to-day manufacturing processes to ensure products are produced efficiently and meet quality standards.
Staff Management: Recruit, train, and supervise factory personnel; conduct performance evaluations and foster a positive work environment.
Quality Control: Implement and maintain quality assurance protocols to ensure product compliance with industry standards and regulations.
Inventory Management: Monitor inventory levels, oversee procurement and ensure optimal stock levels to prevent production delays.
Budget Management: Develop and manage factory budgets, monitor expenses, and identify cost-saving opportunities to enhance profitability.
Health and Safety Compliance: Ensure adherence to safety regulations and practices, conducting safety training and inspections to minimize workplace accidents.
Process Improvement: Identify areas for process optimization and implement lean manufacturing techniques to enhance productivity and efficiency.
Equipment Maintenance: Schedule and oversee regular maintenance of machinery and equipment to minimize downtime and enhance operational efficiency.
Reporting and Analysis: Prepare operational reports and analyze data to inform management decisions and improve production processes.
Cross-Departmental Collaboration: Work closely with supply chain, engineering, and quality assurance teams to ensure alignment of manufacturing goals and objectives.
In crafting a resume for the production supervisor position, it's crucial to highlight experience in team leadership, emphasizing the ability to inspire and manage a workforce effectively. Showcase expertise in process optimization and quality control, demonstrating a commitment to improving production efficiency and maintaining high standards. Mention familiarity with lean manufacturing techniques and safety compliance to underscore the capacity to foster a safe and efficient working environment. Additionally, list relevant experiences from reputable companies to establish credibility and highlight accomplishments that illustrate measurable results in previous roles.
[email protected] • +1-555-0123 • https://www.linkedin.com/in/johnsmith • https://twitter.com/johnsmith
Driven and results-oriented Production Supervisor with extensive experience in leading teams and optimizing manufacturing processes. Proven track record at industry leaders such as GE, Siemens, and Honeywell, specializing in quality control, lean manufacturing, and safety compliance. Adept at fostering a culture of continuous improvement and ensuring adherence to safety standards. Possesses strong analytical skills to enhance production efficiency while maintaining quality. Committed to developing team capabilities and driving operational excellence, aiming to contribute effectively to a factory management role that values innovation and teamwork.
WORK EXPERIENCE
- Led a team of 20+ employees, achieving a 15% increase in production efficiency through the implementation of lean manufacturing principles.
- Developed and executed quality control processes that reduced product defects by 30% over two years.
- Facilitated training sessions on safety compliance, resulting in a 50% decrease in workplace incidents and injuries.
- Collaborated with cross-functional teams to optimize production workflows, contributing to a 20% reduction in lead times.
- Spearheaded a process optimization project that increased output by 25%, directly boosting product sales.
- Managed daily operations of a manufacturing facility, achieving record production levels via process improvements.
- Implemented quality assurance programs that ensured compliance with industry standards, resulting in an ISO 9001 certification.
- Initiated a risk assessment strategy which identified potential safety hazards, improving overall safety scores.
- Mentored junior supervisors, enhancing their leadership skills and improving team performance on projects.
- Played a crucial role in a project that introduced a new product line, leading to an additional $2 million in annual revenue.
- Led a high-performing operations team to surpass production targets by 10% consistently over three years.
- Established process improvement initiatives that streamlined production operations, yielding a 30% cost reduction.
- Drove a safety improvement initiative that resulted in achieving the 'Safety Excellence Award' within the first year.
- Utilized data analytics to make informed decisions on operational planning, leading to enhanced productivity rates.
- Recognized for developing and executing a cross-departmental collaboration project that increased operational efficiency.
SKILLS & COMPETENCIES
Here’s a list of 10 skills for John Smith, the Production Supervisor:
- Team leadership
- Process optimization
- Quality control
- Lean manufacturing techniques
- Safety compliance and regulations
- Production planning and scheduling
- Resource allocation and management
- Performance metrics analysis
- Problem-solving and troubleshooting
- Communication and interpersonal skills
COURSES / CERTIFICATIONS
Sure! Here are five certifications and completed courses for John Smith, the Production Supervisor:
Certified Lean Six Sigma Green Belt (CLSSGB)
Completed: March 2017ISO 9001:2015 Quality Management Systems Auditor
Completed: July 2018OSHA Safety and Health Certification
Completed: September 2019Project Management Professional (PMP)
Completed: January 2020Advanced Manufacturing Technology Course
Completed: April 2021
EDUCATION
- Bachelor of Science in Industrial Engineering, University of Michigan, 2003-2007
- Master of Business Administration (MBA), Northwestern University - Kellogg School of Management, 2008-2010
When crafting a resume for the Quality Assurance Manager position, it's crucial to emphasize expertise in quality management systems and regulatory compliance. Highlight experience with root cause analysis and statistical process control, demonstrating ability to improve product quality and adhere to industry standards. Mention accomplishments in training and development to show leadership and team-building skills. Including relevant experience with renowned companies can also enhance credibility. Finally, showcase strong analytical skills and a commitment to continuous improvement to illustrate readiness for challenges in the role, making the applicant stand out in a competitive field.
[email protected] • +1-234-567-8901 • https://www.linkedin.com/in/sarah-johnson • https://twitter.com/sarah_johnson
**Summary for Sarah Johnson**
Dynamic Quality Assurance Manager with over a decade of experience in leading quality management systems across top-tier companies like Toyota and Procter & Gamble. Expertise in root cause analysis and regulatory compliance, complemented by a strong background in training and development. Proven track record in utilizing statistical process control to enhance product quality and drive continuous improvement. Adept at fostering a culture of quality and safety, ensuring organizational standards are not only met but exceeded. Passionate about cultivating high-performing teams and implementing strategic initiatives to optimize quality performance and operational excellence.
WORK EXPERIENCE
- Successfully implemented a new quality management system that improved product quality ratings by 25%.
- Led a cross-functional team in conducting root cause analysis on production failures, resulting in a 30% reduction in defects.
- Developed and delivered training programs for staff on quality assurance best practices, enhancing team competency and awareness.
- Streamlined quality control processes, which decreased inspection times by 15% while maintaining compliance with regulatory standards.
- Collaborated with product development teams to introduce quality checkpoints earlier in the production process, enhancing overall product quality.
- Led quality audits across multiple manufacturing sites, ensuring compliance with ISO 9001 standards.
- Identified and addressed areas for improvement that reduced waste by 20% in the production line.
- Worked closely with engineers to develop statistical process controls that optimized production processes.
- Introduced metrics for continuous feedback on quality assurance processes, increasing accountability within teams.
- Spearheaded the use of new quality assurance tools, which resulted in a 40% improvement in reporting efficiency.
- Conducted thorough inspections and tests on product lines, reducing the return rate by 15%.
- Collaborated with production teams on quality improvement initiatives that linked factory outputs with consumer feedback.
- Assisted in the preparation of regulatory compliance documents, ensuring a 100% pass rate during external audits.
- Enhanced reporting systems that facilitated improved communication between production and quality teams.
- Participated in a company-wide initiative on lean manufacturing techniques that led to a significant cost reduction.
- Developed inspection procedures and checklists for product quality evaluations.
- Assisted senior QA managers in conducting audits that ensured compliance with established quality standards.
- Compiled data for periodic reviews, analyzing patterns to suggest areas for process enhancements.
- Worked alongside the training team to help roll out new QA guidelines to factory staff.
- Gained hands-on experience in statistical analysis through the use of different quality analysis tools.
SKILLS & COMPETENCIES
Here are 10 skills for Sarah Johnson, the Quality Assurance Manager from the context:
- Quality management systems implementation
- Root cause analysis techniques
- Regulatory compliance expertise
- Training and development facilitation
- Statistical process control (SPC) methods
- Auditing and inspection proficiency
- Risk management strategies
- Continuous improvement methodologies (e.g., Six Sigma)
- Documentation and reporting skills
- Communication and interpersonal skills
COURSES / CERTIFICATIONS
Here’s a list of 5 certifications or completed courses for Sarah Johnson (Person 2):
Certified Quality Auditor (CQA)
- Date: May 2018
Six Sigma Green Belt Certification
- Date: September 2019
ISO 9001:2015 Lead Auditor Training
- Date: January 2020
Root Cause Analysis Training
- Date: March 2021
Statistical Process Control (SPC) Workshop
- Date: August 2022
EDUCATION
- Bachelor of Science in Industrial Engineering, University of Michigan, 2008 - 2012
- Master of Business Administration (MBA), Harvard Business School, 2015 - 2017
When crafting a resume for the Maintenance Manager position, it’s crucial to emphasize relevant experience in preventive maintenance and troubleshooting. Highlight leadership abilities and team management skills, showcasing successful collaboration in previous roles. Include any experience with budget management, particularly in optimizing efficiency or cutting costs. Continuous improvement initiatives should be featured to demonstrate a proactive approach. Additionally, listing competencies in adhering to safety and quality standards is essential. Mention specific industries worked in to establish familiarity with diverse environments. Tailor the resume to showcase achievements and measurable results to attract potential employers effectively.
[email protected] • +1-555-0123 • https://www.linkedin.com/in/michael-brown-123456789 • https://twitter.com/michaelbrown93
**Michael Brown** is an accomplished Maintenance Manager with over 15 years of experience in leading maintenance operations for top-tier companies such as Boeing and Caterpillar. He excels in preventive maintenance, troubleshooting, and team management, ensuring optimal equipment performance and minimal downtime. With a strong focus on budget management and continuous improvement, Michael effectively drives operational efficiency while fostering a culture of safety and reliability. His robust skill set positions him as a key asset in enhancing factory performance and achieving organizational goals.
WORK EXPERIENCE
- Led a team of 15 in maintaining production machinery, increasing operational uptime by 30%.
- Implemented a predictive maintenance program that reduced equipment failure costs by 25%.
- Coordinated a project that streamlined maintenance processes, resulting in a 20% decrease in turnaround time.
- Conducted training sessions on equipment safety, boosting compliance rates by 40%.
- Achieved a 15% reduction in energy consumption through targeted equipment upgrades.
- Managed the maintenance budget, achieving a 10% year-over-year savings.
- Created a comprehensive inventory system for spare parts that improved parts availability by 35%.
- Directed safety improvement initiatives that resulted in zero accident reports for two consecutive years.
- Conducted root cause analysis on recurring equipment issues, leading to effective long-term solutions.
- Enhanced cross-functional collaboration with production teams to ensure alignment of maintenance activities.
- Spearheaded the implementation of IoT-driven maintenance systems that increased efficiency by 25%.
- Developed and executed training programs for maintenance staff, elevating team skill levels and performance.
- Negotiated contracts with vendors that resulted in a 15% cost reduction in maintenance supplies.
- Authored technical documentation for maintenance processes, facilitating knowledge transfer across teams.
- Innovated preventive maintenance scheduling that optimized equipment uptime and minimized outages.
- Performed regular inspections and maintenance on manufacturing machinery, contributing to a 10% increase in production output.
- Assisted in the development of maintenance strategies that significantly improved equipment reliability.
- Utilized troubleshooting skills to diagnose machine faults and implement corrective actions swiftly.
- Maintained detailed records of maintenance activities, supporting compliance and audit requirements.
- Collaborated with engineering teams to design modifications that enhanced machine performance.
SKILLS & COMPETENCIES
Here are 10 skills for Michael Brown, the Maintenance Manager:
- Preventive maintenance
- Troubleshooting and problem-solving
- Team management and leadership
- Budget management and cost control
- Continuous improvement methodologies
- Equipment reliability analysis
- Training and development of maintenance staff
- Safety standards compliance
- Root cause analysis
- Project management and planning
COURSES / CERTIFICATIONS
Here are five certifications or completed courses for Michael Brown, the Maintenance Manager:
Certified Maintenance & Reliability Technician (CMRT)
- Date: June 2018
Root Cause Analysis (RCA) Training
- Date: September 2019
Lean Six Sigma Green Belt Certification
- Date: March 2020
Preventive Maintenance Management Course
- Date: November 2021
OSHA Safety Training Certification
- Date: February 2022
EDUCATION
Bachelor of Science in Mechanical Engineering
University of Michigan, Ann Arbor
Graduated: May 2002Master of Business Administration (MBA)
University of Chicago, Booth School of Business
Graduated: June 2010
When crafting a resume for the Supply Chain Coordinator position, it's crucial to emphasize key competencies such as inventory management, logistics optimization, and vendor negotiation, showcasing measurable achievements in these areas. Highlight experience with data analysis and process improvement to demonstrate an ability to enhance operational efficiency. Additionally, detail specific contributions to previous companies, particularly in optimizing supply chains or enhancing logistics processes. It's also important to include relevant technological proficiency and any certifications related to supply chain management. Lastly, an engaging summary that reflects problem-solving skills and teamwork will enhance the overall impact.
[email protected] • +1-555-123-4567 • https://www.linkedin.com/in/emily-davis-123456 • https://twitter.com/emilydavis
**Summary:**
Emily Davis is a dynamic Supply Chain Coordinator with a proven track record in managing inventory and optimizing logistics for top-tier companies such as Amazon and Nestlé. Born on November 16, 1992, she possesses exceptional skills in vendor negotiation and data analysis, driving process improvement initiatives that enhance operational efficiency. With a passion for supply chain excellence and a keen eye for detail, Emily effectively collaborates across departments to streamline operations and reduce costs, positioning herself as a valuable asset in any manufacturing environment. Her commitment to continuous improvement makes her an ideal candidate for factory management roles.
WORK EXPERIENCE
- Led a project that optimized inventory management processes, resulting in a 20% reduction in excess stock.
- Collaborated with cross-functional teams to streamline logistics, achieving a 15% decrease in transportation costs.
- Implemented a vendor performance evaluation system, which improved supplier delivery times by 25%.
- Conducted data analysis to identify trends and make informed decisions, leading to increased operational efficiency.
- Facilitated training workshops on process improvement techniques, enhancing team capabilities and performance.
- Managed supplier relationships, negotiating contracts that saved the company over $500,000 annually.
- Developed and executed inventory forecasting models that improved stock availability and reduced stockouts.
- Spearheaded implementation of a new supply chain software, enhancing visibility and communication across departments.
- Analyzed shipping and logistics data to propose enhancements leading to faster turnaround times.
- Contributed to the establishment of KPIs for supply chain performance tracking, resulting in improved accountability.
- Conducted comprehensive analyses of logistics operations, leading to process re-engineering that improved service levels.
- Collaborated with transportation partners to optimize routing, resulting in a 30% cost reduction on freight.
- Produced actionable reports for management, highlighting areas for operational improvements and cost savings.
- Facilitated cross-training sessions for team members, boosting knowledge sharing and collaboration.
- Played a pivotal role in a project that reduced lead times by 18% through improved scheduling.
- Managed order processing and fulfillment operations, achieving a 98% accuracy rate in order delivery.
- Designed and implemented a new order tracking system that enhanced customer service and satisfaction.
- Coordinated inventory audits that ensured compliance with regulatory standards and reduced discrepancies.
- Assisted in the development of safe working practices to enhance team safety and efficiency.
- Mentored junior staff, fostering a culture of continuous learning and development within the team.
SKILLS & COMPETENCIES
- Inventory management
- Logistics optimization
- Vendor negotiation
- Data analysis
- Process improvement
- Supply chain forecasting
- Demand planning
- Cross-functional collaboration
- Cost reduction strategies
- Customer relationship management
COURSES / CERTIFICATIONS
Here is a list of 5 certifications and completed courses for Emily Davis, the Supply Chain Coordinator:
Certified Supply Chain Professional (CSCP)
- Issuing Organization: APICS
- Date Completed: March 2021
Lean Six Sigma Green Belt Certification
- Issuing Organization: International Association for Six Sigma Certification
- Date Completed: July 2020
Inventory Management Certification
- Issuing Organization: Institute for Supply Management (ISM)
- Date Completed: November 2019
Logistics and Transportation Management Course
- Issuing Organization: Coursera (University of Georgia)
- Date Completed: January 2022
Data Analysis for Supply Chain Management Course
- Issuing Organization: LinkedIn Learning
- Date Completed: September 2022
EDUCATION
- Bachelor of Science in Supply Chain Management, University of California, Los Angeles (UCLA) - Graduated June 2014
- Master of Business Administration (MBA), Harvard Business School - Graduated May 2019
When crafting a resume for a safety coordinator role, it is crucial to emphasize expertise in safety training, incident investigation, and regulatory compliance. Highlight any relevant certifications and experience in risk assessment and emergency response planning, as these demonstrate the candidate's capability to ensure workplace safety. Additionally, experience with safety protocols at prominent companies can enhance credibility. Focus on measurable achievements in reducing incidents or improving safety standards, showcasing the ability to create a culture of safety within the organization. Strong communication skills and teamwork are also essential, as collaboration is key in implementing safety initiatives effectively.
[email protected] • +1-555-0123 • https://www.linkedin.com/in/davidwilson • https://twitter.com/davidwilson
David Wilson is a dedicated Safety Coordinator with extensive experience in enhancing workplace safety across diverse industries, including ExxonMobil and Pfizer. Born on April 8, 1983, he possesses strong competencies in safety training, incident investigation, and regulatory compliance. His expertise in risk assessment and emergency response planning supports the development of safe operational environments, ensuring adherence to safety standards and practices. With a proven record of implementing effective safety programs, David is committed to promoting a culture of safety and continuous improvement in any organization he serves.
WORK EXPERIENCE
- Implemented comprehensive safety training programs that decreased workplace incidents by 30%.
- Conducted thorough incident investigations leading to a 25% reduction in repeat incidents through preventive measures.
- Collaborated with management to develop and enforce new safety protocols that improved regulatory compliance ratings by 40%.
- Led emergency response planning initiatives, ensuring readiness for critical incidents across all facility operations.
- Spearheaded a risk assessment project that identified and mitigated key hazards, resulting in improved health and safety scores.
- Oversaw safety compliance audits across multiple facilities, achieving a 95% compliance rate with national safety standards.
- Developed and launched a digital safety reporting system that enhanced data collection and incident tracking efficiency by 50%.
- Coordinated with external regulatory agencies to maintain operational certification and ensure ongoing adherence to evolving safety regulations.
- Trained cross-functional teams on safety best practices, cultivating a culture of safety that resulted in zero major incidents during tenure.
- Awarded 'Safety Excellence Award' for outstanding contributions to workplace safety improvement initiatives.
- Led a project to redesign safety processes, utilizing lean methodologies that improved overall operational efficiency by 20%.
- Implemented a robust emergency response plan that effectively minimized risks associated with hazardous material handling.
- Facilitated monthly safety workshops that enhanced employee training participation by 60%, raising safety awareness company-wide.
- Collaborated with engineering teams to ensure design safety features were integrated into new product developments.
- Generated quarterly safety reports that provided data-driven insights to the executive team, enabling informed decision-making.
SKILLS & COMPETENCIES
Here are 10 skills for David Wilson, the Safety Coordinator:
- Hazard identification and risk assessment
- Incident investigation and reporting
- Safety training and program development
- Regulatory compliance and standards implementation
- Emergency response planning and drills
- Safety audits and inspections
- Occupational health and safety management systems
- Risk mitigation and control strategies
- Communication and teamwork in safety practices
- Safety data analysis and reporting
COURSES / CERTIFICATIONS
Here’s a list of 5 certifications and courses for David Wilson, the Safety Coordinator:
OSHA Certified Safety and Health Official (CSHO)
- Date: May 2020
Certified Occupational Safety Specialist (COSS)
- Date: November 2019
Emergency Response and Crisis Management Certification
- Date: March 2021
Safety Management Training Course
- Date: July 2022
Risk Assessment and Safety Control Techniques Course
- Date: January 2023
EDUCATION
Bachelor of Science in Occupational Safety and Health
University of Southern Maine, 2001 - 2005Certified Safety Professional (CSP)
Board of Certified Safety Professionals, 2008
When crafting a resume for an Operations Analyst, it is crucial to emphasize analytical skills and experience in data analysis, as well as the ability to enhance operational efficiency. Highlight project management capabilities and examples of successful cost reduction strategies. Illustrate cross-departmental collaboration through specific achievements that demonstrate teamwork and communication skills. Additionally, mention past experience with notable companies to add credibility and showcase industry knowledge. Prioritize results-oriented language, providing quantifiable outcomes of previous projects to illustrate impact and effectiveness in driving improvements within operations. Tailor the resume to align with the specific requirements of potential employers.
[email protected] • +1-555-0123 • https://www.linkedin.com/in/jessicalee91 • https://twitter.com/jessicalee91
**Summary for Jessica Lee**
Dynamic Operations Analyst with expertise in data analysis and project management. Proven track record in enhancing operational efficiency and implementing cost reduction strategies across diverse industries, including technology and consumer goods. Skilled in fostering cross-departmental collaboration to drive organizational success. With experience at leading companies such as Intel and PepsiCo, Jessica combines analytical acumen with strategic insight to streamline processes and improve productivity. A results-driven professional, she is committed to leveraging her skills to contribute to continuous improvement and operational excellence in any manufacturing setting.
WORK EXPERIENCE
- Implemented data-driven strategies that increased operational efficiency by 30%, reducing costs across multiple departments.
- Collaborated with cross-functional teams to streamline process workflows, resulting in a 25% reduction in project completion time.
- Conducted in-depth market analysis that informed strategic planning and contributed to a 15% increase in product sales.
- Developed and maintained performance metrics dashboards that enhanced visibility into operational process improvements.
- Received the 'Outstanding Analyst Award' for exceptional contributions to operational efficiency and team collaboration.
- Led initiatives focusing on cost reduction strategies, successfully achieving a 20% annual savings in departmental budgets.
- Facilitated training sessions on effective project management techniques, improving team productivity by 18%.
- Pioneered the development of a new data analysis tool that improved error detection rates by over 35%.
- Collaborated with senior management to align operational goals with corporate strategy, enhancing overall performance metrics.
- Recognized for exemplary work with a 'Team Player Award' for exceptional communication and collaboration skills.
- Analyzed operational data to identify performance trends, which informed process enhancements leading to a 15% increase in production output.
- Coordinated with various departments to execute company-wide initiatives aimed at improving operational workflows.
- Successfully managed multiple projects simultaneously, ensuring adherence to tight deadlines and budget constraints.
- Conducted comprehensive risk assessments that minimized operational downtime by enhancing contingency planning protocols.
- Honored with the 'Innovator Award' for pioneering cost-cutting initiatives that improved profit margins.
- Implemented lean principles that decreased waste and improved efficiency in manufacturing processes, yielding a 22% cost reduction.
- Presented key findings from operational analyses to stakeholders, facilitating informed decision-making and strategic initiatives.
- Managed vendor relationships to ensure operational supplies were delivered timely, which enhanced production pace.
- Contributed to a cross-departmental task force aimed at improving overall company operational strategies, leading to improved employee satisfaction scores.
- Received recognition as a 'Top Performer' due to consistent achievement of project goals and objectives.
SKILLS & COMPETENCIES
Here is a list of 10 skills for Jessica Lee, the Operations Analyst:
- Data analysis
- Project management
- Operational efficiency
- Cost reduction strategies
- Cross-departmental collaboration
- Process improvement
- Statistical analysis
- Problem-solving
- Time management
- Communication skills
COURSES / CERTIFICATIONS
Here is a list of 5 certifications and completed courses for Jessica Lee, the Operations Analyst:
Lean Six Sigma Green Belt Certification
Institution: American Society for Quality
Date Completed: March 2022Project Management Professional (PMP) Certification
Institution: Project Management Institute
Date Completed: June 2021Advanced Data Analysis Techniques
Institution: Coursera (offered by University of Pennsylvania)
Date Completed: November 2023Operational Excellence Training
Institution: Institute of Operational Excellence
Date Completed: January 2023Cost Reduction Strategies Workshop
Institution: MIT Professional Education
Date Completed: September 2022
EDUCATION
- Bachelor of Science in Industrial Engineering, University of California, Los Angeles (UCLA), Graduated: June 2013
- Master of Business Administration (MBA), Massachusetts Institute of Technology (MIT), Graduated: May 2016
Crafting a compelling resume for a factory manager position requires a strategic approach that showcases both technical proficiency and interpersonal skills. Highlighting experience with industry-standard tools, such as manufacturing management systems and quality control applications, is essential. A strong resume should include specific metrics, such as improved production efficiency or reduced costs, to quantify your achievements and demonstrate how your expertise aligns with the company’s goals. Additionally, be sure to showcase your knowledge of production processes, regulatory compliance, and inventory management. By integrating relevant keywords and phrases from the job description, you can create a tailored resume that resonates with hiring managers and applicant tracking systems, illustrating your capability to meet the specific demands of the role.
Beyond technical skills, demonstrating hard and soft skills is crucial in presenting yourself as a well-rounded candidate. Highlighting your leadership abilities, problem-solving expertise, and communication skills can differentiate you from other candidates. Consider including anecdotes that illustrate how you effectively managed teams, resolved conflicts, or implemented successful training programs. Personalize your resume by aligning your experience with the company’s values and operational philosophy, drawing clear connections between your past achievements and the job's requirements. In today’s competitive job market, creating a standout resume that effectively combines these elements will help you catch the eye of top employers seeking a factory manager who can drive productivity and foster a positive work environment.
Essential Sections for a Factory Manager Resume
- Contact Information (name, phone number, email, LinkedIn profile)
- Professional Summary (brief overview of career and skills)
- Work Experience (detailed descriptions of previous roles)
- Education (degree, major, and institution)
- Skills (key competencies relevant to factory management)
- Certifications (relevant industry certifications and training)
- Achievements (notable accomplishments in previous roles)
- Professional Affiliations (membership in industry organizations)
Additional Sections to Gain an Edge
- Projects (highlight significant projects managed or contributed to)
- Technical Skills (specific software or machinery expertise)
- Leadership Experience (examples of leadership roles or initiatives)
- Language Proficiencies (benefit in diverse workplace environments)
- Performance Metrics (quantifiable success indicators from past roles)
- Volunteer Experience (community service or non-profit contributions)
- References (notable professionals willing to vouch for your work)
- Awards and Honors (recognition received in your career)
Generate Your Resume Summary with AI
Accelerate your resume crafting with the AI Resume Builder. Create personalized resume summaries in seconds.
Crafting an impactful resume headline for a factory manager is crucial, as it serves as a powerful snapshot of your skills and expertise, setting the tone for the entire application. This brief yet compelling statement should be tailored to resonate with hiring managers and effectively communicate your specialization in factory management.
Your headline is essential as it’s the first impression hiring managers will have of you, making it imperative to capture their attention immediately. Aim to distill your professional identity into a concise phrase that reflects your distinctive qualities, skills, and career achievements. For example, consider using phrases like “Results-Driven Factory Manager | Expert in Lean Manufacturing & Process Optimization” to highlight your unique competencies.
When crafting your headline, focus on incorporating specific elements that define your professional brand. Mention your years of experience, key industries, certifications, or any specific methodologies you excel in, such as Six Sigma or total quality management. This not only showcases your qualifications but also aligns your profile with the company’s needs and expectations.
Additionally, remember to keep your headline relevant to the specific factory management roles you’re targeting. By aligning your wording with the job description, you further increase the likelihood of engaging hiring managers who are seeking a candidate with your precise skills and background.
In a competitive field where many candidates vie for the same position, your resume headline should distinctly reflect what sets you apart. Aim to convey your value proposition, emphasizing the results and improvements you’ve driven in previous positions. An impactful headline ultimately serves as a gateway to your resume, enticing potential employers to delve deeper into your qualifications and achievements. By investing time in this essential first step, you can significantly enhance your chances of making a memorable impression.
Factory Manager Resume Headline Examples:
Strong Resume Headline Examples
Strong Resume Headline Examples for Factory Manager
Results-Driven Factory Manager with 10 Years of Experience in Lean Manufacturing and Operational Excellence
Dynamic Manufacturing Leader Specializing in Process Optimization and Team Development to Drive Performance
Proven Factory Manager Skilled in Cost Reduction, Inventory Management, and Quality Assurance Strategies
Why These Are Strong Headlines
Emphasis on Experience and Achievements:
- Each headline highlights years of experience and specific skills that are critical in manufacturing, such as lean manufacturing, operational excellence, and process optimization. This immediately positions the candidate as a qualified and capable professional, drawing attention from hiring managers.
Focus on Value and Results:
- The terms "results-driven", "dynamic", and "proven" signal to potential employers that the candidate is not just experienced, but also delivers measurable outcomes. This strengthens the candidate’s value proposition by indicating a focus on efficiency, performance improvement, and tangible contributions to the organization.
Industry-Specific Keywords:
- Using terminology like "lean manufacturing", "cost reduction", and "quality assurance" makes these headlines relevant to the manufacturing industry. This helps the resume stand out in Applicant Tracking Systems (ATS) and captures the interest of hiring managers looking for individuals with specific expertise in areas that can impact the factory's bottom line.
Weak Resume Headline Examples
Weak Resume Headline Examples for Factory Manager
- "Factory Manager Seeking New Opportunity"
- "Experienced Manager in Manufacturing"
- "Factory Management Professional"
Why These are Weak Headlines
Lack of Specificity: Each headline fails to specify an area of expertise, industry, or particular skills. For instance, "Factory Manager Seeking New Opportunity" does not indicate what kind of factory (e.g., food production, automotive, electronics) or any unique qualifications that set the candidate apart.
Generic Terminology: Headlines like "Experienced Manager in Manufacturing" and "Factory Management Professional" use vague terms that don't convey the candidate's unique value or experiences. They do not highlight specific achievements, leadership skills, or industry expertise, making them blend in with many other resumes.
Limited Impact: These headlines do not evoke interest or inspire confidence in the reader. A strong resume headline should showcase the candidate's strengths and intriguing qualities directly related to the desired job role, ultimately drawing the hiring manager's attention and encouraging them to read further.
Crafting an exceptional resume summary is essential for factory managers aiming to stand out in a competitive job market. The summary acts as a snapshot of your professional journey, encapsulating your experience, technical expertise, and compelling storytelling abilities. A well-crafted summary highlights your unique talents, collaboration skills, and attention to detail. This brief section not only sets the tone for your resume but also serves as a powerful tool to connect with prospective employers. Tailoring your summary to align with the specific role you're targeting can make a significant difference. Here are key points to include in your factory manager resume summary:
Years of Experience: Clearly state your years of experience in factory management or related roles, emphasizing any leadership positions you've held.
Specialized Industries: Mention any specific industries you have worked in, such as automotive, electronics, or food production, to demonstrate your niche expertise.
Technical Proficiency: Highlight expertise with relevant software and technologies, such as ERP systems, production scheduling software, or quality management tools, showcasing your ability to optimize operations.
Collaboration Skills: Describe your ability to work cross-functionally, communicating effectively with teams across departments, to illustrate your capability in fostering a collaborative work environment.
Attention to Detail: Emphasize your commitment to maintaining high standards in production processes, quality control, and safety regulations, reflecting your meticulous approach to management.
By including these elements in your summary, you create a compelling introduction that captures the attention of potential employers and showcases what makes you an exceptional candidate for a factory manager role.
Factory Manager Resume Summary Examples:
Strong Resume Summary Examples
Resume Summary Examples for a Factory Manager:
Result-Oriented Manufacturing Leader
Accomplished Factory Manager with over 10 years of experience in optimizing production processes and leading diverse teams to exceed performance targets. Proven ability to implement lean manufacturing techniques, resulting in a 30% reduction in operational costs and enhanced product quality.Innovative Operations Specialist
Dynamic Factory Manager with a strong background in supply chain optimization and workforce management. Skilled in deploying cutting-edge technologies to streamline manufacturing operations, driving a 25% increase in productivity while maintaining strict adherence to safety regulations and quality standards.Dedicated Team Builder
Experienced Factory Manager with a passion for fostering a culture of excellence and collaboration within manufacturing environments. Adept at mentoring staff and leading cross-functional teams, achieving a remarkable 40% improvement in employee engagement and retention metrics.
Why These Summaries Are Strong:
Specificity and Measurable Achievements: Each summary highlights specific achievements and quantifiable results, such as percentage improvements and cost reductions. This concrete data shows potential employers the candidate’s direct impact on previous operations.
Relevant Skills and Expertise: The summaries emphasize relevant skills such as lean manufacturing, supply chain optimization, and workforce management. This showcases the candidate’s technical know-how and aligns their expertise with the needs of a factory manager role.
Leadership and Team Building: By mentioning team management and collaboration, these summaries convey the candidate’s leadership qualities. Strong leadership is crucial in managing factory teams, and these summaries illustrate the candidate’s ability to foster positive work environments, which is often a critical factor for hiring managers.
Lead/Super Experienced level
Here are five strong resume summary examples for a Lead/Super Experienced Factory Manager:
Results-driven factory manager with over 15 years of comprehensive experience in optimizing production processes, reducing costs, and enhancing product quality in high-volume manufacturing environments. Proven track record of implementing lean manufacturing practices that increased operational efficiency by 30%.
Dynamic leader with extensive expertise in overseeing multi-million-dollar manufacturing operations and leading diverse teams of 100+ employees. Skilled in developing strategic initiatives that drive productivity and foster a culture of safety and excellence within the factory.
Accomplished factory manager recognized for exceptional problem-solving skills and ability to streamline operations while maintaining compliance with industry standards. Successfully guided a team through two major facility improvements, resulting in a 25% reduction in downtime and a 15% increase in output.
Strategic thinker with a strong background in supply chain management and just-in-time manufacturing. Expert at analyzing key performance indicators to drive performance improvements, ensuring optimal inventory levels and a seamless flow of materials to the production line.
Dedicated professional with a solid foundation in workforce development and training initiatives, enhancing employee skills and engagement. Committed to fostering an inclusive environment, resulting in improved team morale and reduced turnover rates in a fast-paced factory setting.
Senior level
Sure! Here are five examples of a strong resume summary for a senior-level factory manager:
Results-driven factory manager with over 15 years of experience in optimizing production processes and advocating for efficiency, leading to a 25% reduction in operational costs while maintaining product quality standards.
Dynamic senior factory manager with a proven track record of leading cross-functional teams to achieve production targets and implement lean manufacturing principles, driving a year-over-year productivity increase of 30%.
Strategic operations leader with expertise in large-scale manufacturing environments, specializing in supply chain optimization and workforce development, resulting in improved operational KPIs and enhanced employee engagement.
Seasoned factory manager certified in Six Sigma and Lean practices, dedicated to fostering a culture of continuous improvement and safety, demonstrated by a 40% reduction in workplace accidents over three years.
Accomplished manufacturing professional with robust problem-solving skills and a deep understanding of automation technologies, successfully implementing processes that boosted production capacity by 50% and enhanced overall effectiveness.
Mid-Level level
Here are five examples of strong resume summaries for a mid-level factory manager:
Results-Driven Leader: Dynamic factory manager with over 7 years of experience in optimizing production processes, reducing operational costs by 15%, and ensuring compliance with safety regulations to enhance workplace efficiency.
Process Optimization Expert: Proficient in Lean Manufacturing and Six Sigma methodologies, successfully led projects that increased productivity by 20% while maintaining quality standards, resulting in improved customer satisfaction and reduced waste.
Cross-Functional Team Builder: Exceptionally skilled in managing and mentoring diverse teams, fostering a collaborative environment that enhances communication and drives performance improvements throughout the production process.
Strategic Planner: Experienced in developing and executing operational strategies that align with corporate goals, effectively managing budgets and resources to streamline production and support scaling operations in a fast-paced environment.
Safety Compliance Advocate: Strong focus on promoting a culture of safety, ensuring compliance with OSHA standards and implementing training programs that have led to a 30% reduction in workplace incidents over the past three years.
Junior level
Certainly! Here are five resume summary examples for a junior-level Factory Manager:
Results-Oriented Leader: Detail-oriented and motivated Junior Factory Manager with over 3 years of experience in overseeing production processes, ensuring operational efficiency, and implementing quality control measures to drive continuous improvement.
Team-Oriented and Efficient: Dynamic Junior Factory Manager with a passion for team leadership and a proven ability to train and motivate staff, enhancing productivity and fostering a positive work environment in manufacturing settings.
Process Improvement Advocate: Junior Factory Manager adept at analyzing workflows and identifying opportunities for optimization, contributing to a 15% increase in output and reduced waste during tenure at previous manufacturing facility.
Safety-Conscious and Compliant: Committed to maintaining high safety standards and compliance with industry regulations, I am a Junior Factory Manager skilled in developing training programs that have successfully reduced workplace incidents by 20%.
Data-Driven Problem Solver: Junior Factory Manager with a strong analytical mindset, experienced in utilizing production metrics and KPIs to diagnose issues, streamline operations, and implement effective solutions that enhance overall factory performance.
Entry-Level level
Entry-Level Factory Manager Resume Summary Examples
Results-Driven Leader: Highly motivated and detail-oriented individual with a strong academic background in industrial management, eager to leverage theoretical knowledge and hands-on experience in manufacturing processes to ensure operational efficiency.
Adaptable Problem-Solver: Equipped with strong analytical skills and a passion for optimizing workflows, demonstrating the ability to quickly learn and implement best practices in a fast-paced factory environment.
Team Collaboration Focus: Proven ability to work effectively within diverse teams, fostering a positive work atmosphere and driving collective success while adhering to safety and production standards.
Basic Project Management Knowledge: Familiar with Lean Manufacturing principles and Six Sigma methodologies, keen on using these frameworks to enhance productivity and reduce waste in factory operations.
Strong Communication Skills: Exceptional interpersonal abilities, enabling effective communication across departments to facilitate seamless collaboration and achieve production goals.
Experienced Level Factory Manager Resume Summary Examples
Strategic Operations Leader: Seasoned Factory Manager with over 7 years of experience in overseeing manufacturing operations, adept at enhancing productivity and implementing cost-effective solutions that align with organizational objectives.
Lean Manufacturing Expert: Demonstrated success in applying Lean and Six Sigma principles to streamline processes, reduce lead times by 30%, and significantly increase overall production efficiency while maintaining high-quality standards.
Team Development Advocate: Skilled at cultivating talent through effective training and mentorship programs, resulting in a motivated workforce and decreased employee turnover rates by 20% in previous roles.
Cross-Functional Collaboration Specialist: Proven track record of partnering with engineering, quality assurance, and supply chain teams to drive continuous improvement initiatives that enhance production workflows and optimize resource allocation.
Data-Driven Decision Maker: Proficient in utilizing data analytics and KPIs to assess production performance, leading to informed strategic decisions that elevated output levels and improved profitability by 15% year-over-year.
Weak Resume Summary Examples
Weak Resume Summary Examples for Factory Manager:
- "Factory Manager with some experience in overseeing plant operations."
- "Experienced in managing a factory but lacking specific achievements."
- "Factory Manager looking for a new opportunity after working in the same position for a while."
Why These Are Weak Headlines:
Lack of Specificity:
- The first example mentions "some experience" but does not quantify it or provide details about the scale of operations managed, the size of teams, or types of products manufactured. It fails to convey a compelling narrative about the candidate's capabilities.
Absence of Achievements:
- The second summary indicates experience but does not highlight any specific achievements or contributions to the factory. Employers are often interested in measurable results, such as improvements in efficiency, cost reductions, or successful project implementations; this summary offers none of that.
Lack of Motivation and Direction:
- The third example reflects a passive approach, simply stating a desire for a new opportunity without expressing enthusiasm for the role or detailing what the candidate brings to the table. It gives the impression that the candidate is more focused on leaving their current position than on how they can contribute to a new employer.
Resume Objective Examples for Factory Manager:
Strong Resume Objective Examples
Results-oriented factory manager with over 10 years of experience in optimizing production processes and enhancing operational efficiency, seeking to drive continuous improvement and increase profitability at [Company Name].
Dedicated and skilled factory manager with a proven track record in team leadership and project management, looking to leverage expertise in lean manufacturing and quality control to contribute to the success of [Company Name].
Motivated factory manager with extensive knowledge in supply chain management and innovative problem-solving techniques, aiming to implement effective strategies that improve overall production flow and employee performance at [Company Name].
Why this is a strong objective:
These resume objectives are effective because they are specific and tailored to the manufacturing industry. They highlight key skills and experience relevant to the role of a factory manager, showcasing the candidate's ability to make a positive impact on the organization. By mentioning measurable outcomes like efficiency enhancement and profitability, the objectives convey the candidate's results-driven mindset. Furthermore, addressing the potential employer by name adds a personalized touch, indicating the candidate's genuine interest in the position and company.
Lead/Super Experienced level
Sure! Here are five strong resume objective examples for a factory manager with extensive experience:
Results-Driven Leader: "Dynamic factory manager with over 10 years of experience in optimizing production processes and driving operational excellence. Proven track record of increasing efficiency by 30% through strategic planning and team development."
Operational Excellence Expert: "Seasoned factory manager with over 15 years of expertise in lean manufacturing and quality control. Committed to implementing innovative solutions to reduce waste and enhance productivity while maintaining the highest safety standards."
Strategic Visionary: "Highly experienced factory manager with a strong background in overseeing large-scale operations and achieving production targets. Seeking to leverage skills in workforce management and process improvement to drive significant advancements in manufacturing efficiency."
Change Management Specialist: "Accomplished factory manager with 12+ years of experience in managing multi-site operations and implementing change initiatives that enhance productivity and morale. Adept at leading diverse teams to exceed targets while fostering a culture of continuous improvement."
Supply Chain Optimization Leader: "Results-oriented factory manager with a rich history of leading production teams and managing supply chain operations. Passionate about utilizing data-driven strategies to optimize workflow and achieve production goals, while ensuring compliance and quality assurance."
Senior level
Here are five strong resume objective examples for a senior-level factory manager:
Results-Oriented Leader: Dynamic factory manager with over 15 years of experience in optimizing production processes and improving operational efficiencies, seeking to leverage expertise in lean manufacturing and team development to drive growth and quality improvements at [Company Name].
Innovative Production Strategist: Senior factory manager with a proven track record of leading cross-functional teams in high-volume manufacturing environments, aiming to apply strategic planning and advanced problem-solving skills to enhance productivity and reduce costs at [Company Name].
Operational Excellence Advocate: Committed factory manager with extensive experience in implementing continuous improvement initiatives and overseeing compliance with safety regulations, looking to contribute strong analytical and leadership capabilities to [Company Name]'s mission of operational excellence.
Quality-Centric Manager: Accomplished factory manager with a 20-year background in maintaining high-quality standards and achieving ISO certifications, seeking to utilize expertise in quality control and process optimization to ensure superior output and customer satisfaction at [Company Name].
Transformational Leader: Senior factory manager with a successful track record of driving organizational change and fostering a culture of accountability, aspiring to bring innovative leadership and strategic vision to [Company Name] to enhance operational performance and employee engagement.
Mid-Level level
Here are five strong resume objective examples for a mid-level factory manager:
Results-Driven Leadership: Dedicated factory manager with over five years of experience in optimizing production processes and improving operational efficiency, seeking to leverage expertise in team management and quality assurance to drive success at a forward-thinking manufacturing firm.
Operational Excellence: Detail-oriented factory manager with a proven track record of implementing Lean Manufacturing principles, aiming to enhance productivity and reduce waste while fostering a culture of safety and continuous improvement within the production team.
Innovative Problem Solver: Mid-level factory manager with extensive experience in troubleshooting production challenges and developing effective solutions, looking to utilize strong analytical skills and hands-on leadership to contribute to the high-performance standards of a dynamic manufacturing environment.
Team Development Focus: Accomplished factory manager skilled in employee training and engagement, seeking to mentor and inspire teams to reach their full potential while consistently meeting production targets and adhering to quality standards.
Strategic Planning Expertise: Results-oriented factory manager with a solid background in supply chain management and inventory control, committed to streamlining operations and enhancing profitability in a manufacturing setting through strategic planning and process optimization.
Junior level
Sure! Here are five strong resume objective examples tailored for a junior-level factory manager position:
Dedicated and motivated professional with a background in manufacturing processes seeking a junior factory manager position to leverage strong organizational skills and a commitment to improving operational efficiency and team productivity.
Detail-oriented and proactive factory management graduate aiming to secure a junior management role where I can apply my hands-on experience in process optimization and team collaboration to drive production success and safety standards.
Ambitious recent engineering graduate with internship experience in factory operations seeking a junior factory manager position to contribute innovative solutions and effective management techniques that enhance production quality and workflow.
Enthusiastic and results-driven junior professional with a background in logistics and production, eager to take on a factory manager role to support team performance and operational excellence through effective communication and problem-solving.
Goal-oriented individual with foundational experience in manufacturing and quality control, looking to join a dynamic factory team as a junior manager to implement process improvements and foster a culture of safety and efficiency.
Entry-Level level
Here are five strong resume objective examples for an entry-level factory manager position:
Aspiring Factory Manager: Detail-oriented and motivated recent graduate with a degree in Industrial Engineering, eager to leverage strong organizational skills and knowledge of manufacturing processes to contribute to operational efficiency and team success in a dynamic factory environment.
Entry-Level Management Professional: Dedicated and enthusiastic individual seeking an entry-level factory manager position, aiming to apply my strong problem-solving abilities and passion for optimizing production processes to enhance productivity and safety in a manufacturing setting.
Recent Graduate in Manufacturing Management: Energetic and adaptable individual with a background in production management and internship experience, looking to transition into an entry-level factory manager role where I can utilize my technical knowledge and leadership skills to support and improve factory operations.
Innovative Thinker With a Focus on Efficiency: Results-driven professional with a passion for manufacturing and a proven ability to work in team settings, seeking an entry-level factory manager position to implement process improvements and ensure the smooth operation of daily production activities.
Motivated Team Leader: Committed to developing my career in factory management, I am seeking an entry-level position to apply my strong interpersonal skills and foundational knowledge of Lean Manufacturing principles to foster a collaborative and productive work environment.
Weak Resume Objective Examples
Weak Resume Objective Examples for a Factory Manager
- "To secure a position as a Factory Manager where I can use my skills."
- "Looking for a factory management role that offers good pay and benefits."
- "Desire to work as a Factory Manager in an environment that challenges me."
Why These Objectives Are Weak
Lack of Specificity: These objectives are vague and do not specify what skills or experiences the candidate brings to the table. A good resume objective should clearly outline the candidate’s expertise and how it aligns with the needs of the employer.
Focus on Personal Gain: The objectives emphasize the candidate's desire for pay and benefits rather than highlighting how they can contribute to the company's success. This can come off as self-serving rather than a team-oriented mindset, which is crucial in managerial roles.
Absence of Concrete Goals: The statements do not convey any specific goals or visions for the role, such as improving operational efficiency, leading a team, or implementing safety protocols. Effective objectives should reflect the candidate's intentions to impact the organization positively, showing ambition and initiative.
When writing the work experience section for a factory manager position, it's essential to effectively showcase your skills, achievements, and responsibilities in a concise manner. Here are some guidelines:
Use a Clear Format: List your work experiences in reverse chronological order. Include the job title, company name, location, and dates of employment. This ensures that employers can easily see your most recent and relevant experiences.
Tailor Your Content: Customize your work experience for the factory manager role by focusing on relevant tasks that showcase your leadership, operational efficiency, and safety awareness. Highlight experiences related to production management, team leadership, and process improvement.
Be Specific: Use specific metrics and examples to demonstrate your accomplishments. For instance, instead of saying you "increased productivity," say "implemented Lean manufacturing techniques that improved production efficiency by 20% within six months."
Highlight Leadership Skills: Factory managers need strong leadership qualities. Describe your experience in managing teams, resolving conflicts, and fostering a positive work environment. Use phrases like “led a team of X employees” or “coordinated cross-functional teams to achieve targets.”
Focus on Problem-Solving: Factories often face challenges like equipment failure or staffing issues. Include examples where you successfully identified problems and implemented solutions, minimizing downtime and maintaining output.
Safety and Compliance: Highlight your commitment to safety and regulatory compliance. Mention any safety programs you developed or participated in, emphasizing the impact these measures had on workplace safety ratings or accident reduction.
Keep It Concise: Aim for clarity and brevity. Use bullet points for easy readability, and limit each role description to 4-6 bullet points that cover key responsibilities and achievements.
By following these guidelines, your work experience section will effectively communicate your qualifications and readiness for a factory manager role.
Best Practices for Your Work Experience Section:
Certainly! Here are 12 best practices for showcasing your work experience in the resume section for a factory manager position:
Tailor Your Resume: Customize your work experience to align with the specific job description, highlighting relevant skills and achievements that match the factory manager role.
Use Action Verbs: Begin each bullet point with strong action verbs (e.g., led, implemented, streamlined) to convey your contributions and leadership effectively.
Quantify Achievements: Provide specific metrics and data to demonstrate the impact of your efforts (e.g., increased production efficiency by 20%, reduced waste by 15%).
Focus on Results: Emphasize outcomes over duties by illustrating how your actions improved processes, safety, and profitability in the factory setting.
Highlight Leadership Skills: Detail your experience in leading teams, managing conflicts, and fostering a positive work environment, which are crucial for a factory manager role.
Include Relevant Technologies: Mention any systems, machinery, or technologies (e.g., ERP systems, lean manufacturing tools) you've worked with to underscore your technical proficiency.
Detail Compliance and Safety: Showcase your knowledge of industry regulations, safety standards, and your efforts to maintain a safe workplace, as this is vital in manufacturing.
Show Problem-Solving Abilities: Provide examples of how you identified issues and implemented solutions to improve operations or resolve challenges effectively.
Demonstrate Continuous Improvement: Highlight your commitment to ongoing improvement initiatives, such as Six Sigma or Kaizen, that contributed to operational excellence.
Mention Project Management Skills: If applicable, describe your experience managing projects from conception to execution, including budgeting and timeline management.
Incorporate Soft Skills: Include soft skills like communication, teamwork, and negotiation, as they are essential for managing diverse teams and liaising with other departments.
Keep it Concise: Limit each work experience entry to a few bullet points focused on the most relevant contributions, ensuring clarity and conciseness for easier readability.
By following these best practices, you can create a compelling work experience section that effectively showcases your qualifications for a factory manager position.
Strong Resume Work Experiences Examples
Bullet Points for Factory Manager Work Experience:
Optimized Production Processes: Led a team of 50 employees in implementing lean manufacturing principles, resulting in a 20% increase in production efficiency and a 15% reduction in operational costs over a 12-month period.
Quality Assurance Implementation: Developed and implemented a comprehensive quality control system that reduced product defects by 30%, leading to a significant improvement in customer satisfaction ratings and a 10% increase in repeat business.
Team Development and Training: Designed and executed a training program for new hires that accelerated onboarding by 40%, enhancing workforce productivity and decreasing turnover rates by 25% within two years.
Why These Are Strong Work Experiences:
Quantifiable Results: Each bullet point includes specific metrics that illustrate success, such as percentage increases in efficiency and reductions in costs or defects. This concrete data demonstrates the candidate's ability to drive impactful changes in a factory setting.
Leadership and Team Management: The experiences highlight the candidate's leadership skills, showing that they can effectively manage and develop a large team while fostering a culture of continuous improvement, which is crucial for a factory manager.
Focus on Key Manufacturing Concepts: By focusing on process optimization, quality standards, and employee training, these bullet points align with critical competencies in factory management, making the candidate's experience relevant and compelling to potential employers.
Lead/Super Experienced level
Streamlined Production Operations: Implemented lean manufacturing techniques that reduced waste by 20% and increased overall equipment effectiveness (OEE) to 95%, resulting in a significant boost in productivity and efficiency across all production lines.
Team Leadership & Development: Led a diverse team of 50+ employees, fostering a culture of continuous improvement through regular training sessions and mentorship programs, which improved staff retention rates by 30% and enhanced team performance.
Quality Assurance Implementation: Developed and executed a comprehensive quality management system that achieved a 98% defect-free rate and resulted in a 15% reduction in customer complaints, ensuring compliance with industry standards and regulations.
Cost Reduction Initiatives: Directed cost-reduction strategies that decreased operational expenses by 25% through effective supplier negotiations and the introduction of energy-efficient equipment, while maintaining product quality and delivery timelines.
Cross-Departmental Collaboration: Established strong communication channels between production, engineering, and logistics teams to optimize workflow processes, leading to a 40% decrease in lead times and improved on-time delivery rates to clients.
Senior level
Certainly! Here are five strong resume work experience examples tailored for a Senior Factory Manager:
Operational Excellence: Led a team of over 150 employees in a high-volume manufacturing environment, achieving a 20% increase in production efficiency through the implementation of Lean methodologies and continuous improvement initiatives.
Budget Management: Managed a multi-million dollar annual budget, successfully reducing operational costs by 15% while maintaining product quality and maximizing resource utilization through strategic sourcing and vendor negotiation.
Safety and Compliance: Championed workplace safety initiatives that resulted in a 40% reduction in workplace incidents over three years, ensuring compliance with OSHA regulations and fostering a culture of safety among all staff.
Cross-Functional Leadership: Collaborated with engineering, quality assurance, and supply chain teams to streamline processes, resulting in a 30% decrease in lead times and enhancing product delivery performance across multiple distribution channels.
Talent Development: Developed and implemented a comprehensive training program for new and existing staff, increasing employee engagement and retention rates by 25% and building a skilled workforce adept in advanced manufacturing technologies.
These examples highlight leadership, strategic impact, and a commitment to excellence in factory management.
Mid-Level level
Sure! Here are five bullet point examples of strong work experiences for a mid-level factory manager:
Operational Leadership: Spearheaded daily operations in a 200,000 sq. ft. manufacturing facility, successfully increasing production efficiency by 20% through the implementation of Lean Manufacturing principles.
Team Development: Trained and mentored a team of 50+ employees, fostering a culture of continuous improvement and safety that led to a 15% reduction in workplace incidents over two years.
Budget Management: Managed an annual budget of $5 million, optimizing resource allocation to achieve a 10% reduction in operating costs while maintaining high-quality standards and meeting production targets.
Quality Assurance: Enhanced quality control processes resulting in a 30% decrease in product defects by collaborating with cross-functional teams to establish best practices and compliance with ISO 9001 standards.
Supply Chain Optimization: Collaborated with suppliers and logistics teams to streamline operations, reducing lead times by 25% and ensuring timely delivery of materials, which significantly improved overall production schedules.
Junior level
Sure! Here are five bullet points tailored for a Junior Factory Manager with limited experience:
Assisted in daily operations of a manufacturing facility, overseeing production schedules and workflow to ensure timely output and quality standards were met.
Collaborated with senior management to develop and implement process improvements, resulting in a 15% increase in production efficiency within the first quarter.
Trained and mentored new employees on safety protocols and machine operation, fostering a culture of compliance and teamwork within the production floor.
Conducted regular inventory audits and maintained supply chain records, optimizing material availability and reducing downtime due to shortages.
Utilized data analysis tools to monitor key performance indicators (KPIs) and generate reports, enabling informed decision-making for continuous operational enhancements.
Entry-Level level
Sure! Here are five bullet points of strong resume work experience examples for an entry-level factory manager:
Assisted in Production Oversight: Collaborated with senior management to monitor daily production schedules and ensure adherence to quality standards, contributing to a 15% increase in overall efficiency.
Team Coordination: Coordinated a team of 15 production staff, facilitating communication and collaboration to meet monthly production targets while improving workplace morale and teamwork.
Process Improvement Projects: Participated in a project to streamline the assembly line process, resulting in a 10% reduction in waste and a noticeable enhancement in product delivery times.
Safety Compliance Monitoring: Supported the implementation of safety protocols and training programs, leading to a 20% decrease in workplace accidents and fostering a culture of safety among employees.
Data Analysis and Reporting: Assisted in monitoring production metrics and preparing weekly reports for management to identify trends, enabling informed decision-making and strategic planning to enhance production output.
Weak Resume Work Experiences Examples
Weak Resume Work Experiences for a Factory Manager
Quality Control Assistant at XYZ Manufacturing (Jan 2020 - Dec 2020)
- Assisted in inspecting products for quality assurance based on specified criteria.
- Recorded inspection results in a data spreadsheet.
Machine Operator at ABC Industries (Jan 2019 - Dec 2019)
- Operated machinery and monitored production lines.
- Occasionally reported equipment issues to the supervisor.
Assembly Line Worker at DEF Corp (Jun 2018 - Dec 2018)
- Worked on an assembly line performing manual assembly tasks.
- Maintained a clean workspace and adhered to safety protocols.
Why These Work Experiences are Weak
Lack of Managerial Responsibilities: None of the experiences listed demonstrate actual leadership or management roles. A factory manager is expected to oversee operations, manage staff, and implement strategies for efficiency. These positions are more entry-level and do not showcase the requisite decision-making abilities or managerial skills.
Limited Scope of Duties: The tasks described are very basic and do not highlight the skills necessary for a management role. They focus on operational tasks rather than strategic planning, resource management, or employee supervision. A strong resume should reflect responsibilities that align with overseeing larger operational components and improving production processes.
Insufficient Quantifiable Accomplishments: The provided experiences lack specific achievements, metrics, or examples of impact. Effective resumes include quantifiable results (such as improving production efficiency by a certain percentage or leading a team to reduce costs), which demonstrate the candidate's capability to contribute meaningfully to a factory's operations. Without these indicators, the experiences do not effectively convey the candidate's value to potential employers.
Top Skills & Keywords for Factory Manager Resumes:
When crafting a factory manager resume, emphasize key skills and relevant keywords that showcase your expertise. Highlight leadership abilities, such as team management and conflict resolution. Include technical skills like process optimization, quality control, and inventory management. Experience with Lean manufacturing, Six Sigma, and safety regulations is vital. Don't forget to mention budget management, production planning, and equipment maintenance. Use keywords like "operational efficiency," "cost reduction," "staff training," and "performance metrics" to capture the attention of hiring managers and applicant tracking systems. Tailoring your resume to specific job descriptions enhances your chances of being noticed and securing an interview.
Top Hard & Soft Skills for Factory Manager:
Hard Skills
Here’s a table with 10 hard skills for a factory manager, including descriptions and links formatted as requested:
Hard Skills | Description |
---|---|
Production Planning | The ability to effectively plan and schedule production activities to meet demand and optimize resources. |
Quality Control | Ensuring that products meet required standards and specifications through checks and evaluations. |
Supply Chain Management | Overseeing and optimizing the entire supply process from raw materials to finished products. |
Equipment Maintenance | Knowledge of maintaining and troubleshooting factory equipment to ensure smooth operations. |
Lean Manufacturing | Implementing lean principles to minimize waste and improve efficiency in production processes. |
Budgeting and Cost Control | Managing the financial aspects of production, including cost estimation and budget adherence. |
Team Leadership | Leading and managing teams effectively to achieve production goals and maintain a positive work environment. |
Health and Safety Regulations | Ensuring compliance with workplace safety standards to protect employees and minimize risks. |
Data Analysis | Utilizing data analysis techniques to improve production processes and decision-making. |
Forecasting | Predicting future production needs based on market trends, sales data, and historical performance. |
Feel free to adjust the descriptions or skills as needed!
Soft Skills
Here’s a table with 10 soft skills for a factory manager, including links formatted as requested:
Soft Skills | Description |
---|---|
Leadership | The ability to inspire and guide teams towards common goals while managing diverse groups effectively. |
Communication | The skill to convey information clearly and listen effectively, enabling better collaboration and understanding among team members. |
Problem Solving | The ability to analyze complex issues, identify solutions, and implement effective strategies to resolve challenges in the factory. |
Teamwork | The capacity to work cooperatively with others, fostering a collaborative environment to achieve productivity and efficiency. |
Adaptability | The skill to adjust to changing circumstances and embrace new challenges in a fast-paced factory setting. |
Time Management | The ability to prioritize tasks effectively and manage schedules to meet deadlines while maximizing productivity. |
Conflict Resolution | The skill to mediate disagreements and maintain harmonious relationships within the team, ensuring a positive work environment. |
Decision Making | The ability to make informed choices quickly and efficiently, especially under pressure or in complex situations. |
Empathy | The capacity to understand and share the feelings of others, which helps in building strong workplace relationships and morale. |
Critical Thinking | The ability to evaluate situations and information logically to make informed decisions that benefit the factory operations. |
This table captures essential soft skills that a factory manager should possess along with their descriptions.
Elevate Your Application: Crafting an Exceptional Factory Manager Cover Letter
Factory Manager Cover Letter Example: Based on Resume
Dear [Company Name] Hiring Manager,
I am writing to express my enthusiastic interest in the Factory Manager position at [Company Name]. With over eight years of experience in manufacturing management, I am passionate about fostering productive environments that prioritize quality, efficiency, and safety. I am excited about the opportunity to contribute my expertise to your esteemed organization.
In my previous role at [Previous Company Name], I successfully managed a team of 50 employees, ensuring that production targets were met while maintaining high standards of quality. I implemented process improvements that led to a 20% increase in efficiency and reduced waste by 15%. My proficiency with industry-standard software, including ERP systems such as SAP and production scheduling tools, has enabled me to analyze performance metrics effectively and drive strategic initiatives.
Collaboration is at the heart of my work ethic. I thrive in team-oriented environments and have led cross-functional teams to enhance operational processes, resulting in significant cost savings and streamlined workflows. My commitment to employee development through training and mentorship has fostered a culture of continuous improvement within the factory. I am proud to have cultivated a motivated workforce that consistently exceeds production goals.
One of my key achievements includes spearheading a safety program that resulted in a 40% reduction in workplace incidents over two years. This initiative not only improved employee morale but also enhanced overall productivity. I am keen to bring this dedication to safety and operational excellence to [Company Name].
I am excited about the opportunity to leverage my technical skills and experience to drive growth and efficiency at [Company Name]. Thank you for considering my application. I look forward to the possibility of discussing how my background can align with your organization's goals.
Best regards,
[Your Name]
A cover letter for a factory manager position should effectively convey your qualifications, experience, and enthusiasm for the role. Here are key elements to include and guidance on crafting your letter:
Contact Information: Start with your name, address, phone number, and email at the top of the letter, followed by the date and the employer’s contact information.
Salutation: Address the letter to the hiring manager by name, if possible. If you don’t have a name, a general salutation like “Dear Hiring Manager” is acceptable.
Introduction: Begin with a strong opening statement that mentions the position you’re applying for and how you learned about the opportunity. Include a brief overview of your professional background, focusing on relevant experience in factory management.
Body Paragraphs:
- Relevant Experience: Highlight your previous roles where you've successfully managed factory operations. Emphasize achievements like improved efficiency, reduced costs, and successful team management.
- Skills and Qualifications: Discuss essential skills, such as leadership, problem-solving, quality control, safety regulations, and production planning. Provide specific examples that demonstrate these skills in action.
- Cultural Fit and Motivation: Explain why you want to work for the specific company, showcasing your alignment with its values, and express your passion for the industry. Mention how your vision aligns with the company’s goals.
Conclusion: Summarize your enthusiasm for the role and express your desire to discuss your qualifications further. Indicate your willingness to provide any additional information and thank the reader for their consideration.
Professional Closing: End with a formal closing such as “Sincerely” or “Best regards,” followed by your name.
Tips for Crafting Your Cover Letter:
- Tailor Each Letter: Customize your letter for each application, reflecting specific job requirements and company culture.
- Use Keywords: Incorporate relevant keywords from the job description to showcase your fit.
- Be Concise: Keep your letter to one page and maintain a clear structure.
- Proofread: Ensure there are no grammatical errors or typos.
By following these guidelines, you can create a compelling cover letter that effectively showcases your qualifications for a factory manager role.
Resume FAQs for Factory Manager:
How long should I make my Factory Manager resume?
When crafting a resume for a factory manager position, it's essential to strike a balance between providing sufficient detail and maintaining brevity. Ideally, your resume should be one to two pages long. A one-page resume is best if you have fewer than ten years of experience, as it allows you to present your most relevant skills and accomplishments concisely. For those with more extensive backgrounds, two pages may be appropriate to cover additional roles, responsibilities, and achievements that demonstrate expertise in factory management.
Regardless of the length, focus on clarity and relevance. Use bullet points to highlight key achievements, such as efficiency improvements, cost reductions, or team leadership. Tailor your resume to align with the job description, emphasizing skills like lean manufacturing, quality control, and safety compliance.
Employers often spend only a few seconds reviewing each resume, so make sure your most pertinent information stands out. Include a powerful summary statement at the top, and prioritize showcasing quantifiable results that reflect your impact in previous roles. Ultimately, the goal is to present a compelling narrative that captures your capabilities as a factory manager within an appropriate length that holds the employer's attention.
What is the best way to format a Factory Manager resume?
When crafting a resume for a factory manager position, it's essential to ensure clarity and professionalism. Begin with a clean, easy-to-read format. Use a standard font like Arial or Times New Roman, ideally sized between 10-12 points.
Start with a strong header that includes your name, phone number, email, and LinkedIn profile, if applicable. Follow this with a brief summary or objective statement that highlights your experience and skills relevant to factory management.
Organize your work experience in reverse chronological order, focusing on relevant positions. For each role, include your job title, company name, location, and dates of employment. Use bullet points to describe your responsibilities and achievements, emphasizing metrics and outcomes when possible, such as production efficiency improvements or cost reductions.
Include a skills section that highlights your technical abilities, leadership skills, knowledge of safety standards, and proficiency in relevant software or machinery.
If applicable, add an education section, mentioning degrees or certifications related to manufacturing and management. Finally, consider adding a section for additional certifications or training relevant to the industry. Ensure the resume is no longer than one page, tailoring it for each job application to reflect the specific requirements of the position.
Which Factory Manager skills are most important to highlight in a resume?
When crafting a resume for a factory manager position, it's essential to highlight a combination of technical, managerial, and interpersonal skills that demonstrate your ability to oversee operations effectively.
Leadership: Showcase your ability to lead and motivate teams, ensuring a productive and harmonious workplace. Highlight experiences where you successfully managed diverse teams.
Operational Expertise: Detail your knowledge of manufacturing processes, quality control, and production planning. Include specific technologies or methodologies you are proficient in, such as Lean Manufacturing or Six Sigma.
Problem-Solving: Emphasize your analytical skills in identifying inefficiencies and implementing solutions, showcasing examples of challenges you overcame in past roles.
Budget Management: Mention your experience with budgeting, cost control, and resource allocation to enhance productivity while maintaining quality.
Health and Safety Compliance: Highlight your commitment to workplace safety regulations and initiatives that promote a safe working environment.
Communication Skills: Include your ability to communicate effectively with team members, upper management, and external stakeholders, ensuring clarity and transparency in operations.
By showcasing these skills, you will present yourself as a well-rounded factory manager capable of driving efficiency and fostering a positive work environment.
How should you write a resume if you have no experience as a Factory Manager?
Writing a resume for a factory manager position without direct experience can be a challenge, but it’s important to highlight transferable skills and relevant experiences. Start with a strong summary statement that showcases your passion for manufacturing, leadership abilities, and any related skills you possess, such as problem-solving, teamwork, or efficiency optimization.
Focus on your educational background, especially if you have a degree in industrial engineering, manufacturing management, or a related field. Include any relevant coursework or projects that demonstrate your knowledge of manufacturing processes.
Next, highlight transferable skills from previous roles. Perhaps you've worked in team leadership, inventory management, or quality control in other industries. Use specific examples to illustrate your accomplishments and how they can apply to a factory setting.
Incorporate volunteer work, internships, or workshops related to manufacturing or management, demonstrating your proactive approach to gaining industry knowledge.
Lastly, tailor your resume to the job description, using keywords from the posting to align your skills with the employer’s needs. This focused approach will help showcase your potential despite a lack of direct experience in factory management.
Professional Development Resources Tips for Factory Manager:
TOP 20 Factory Manager relevant keywords for ATS (Applicant Tracking System) systems:
Certainly! Below is a table with 20 relevant keywords for a factory manager role, along with their descriptions. Using these keywords effectively in your resume can help you pass the Applicant Tracking System (ATS) used in recruitment:
Keyword | Description |
---|---|
Operations Management | Overseeing daily factory operations for efficiency and productivity. |
Lean Manufacturing | Implementing processes to reduce waste and improve processes. |
Quality Control | Ensuring products meet specified quality standards and regulations. |
Production Planning | Scheduling production runs and resource allocation effectively. |
Supply Chain Management | Coordinating logistics and supply chain to ensure timely deliveries. |
Team Leadership | Leading and managing a diverse team of factory workers and supervisors. |
Performance Metrics | Using KPIs to measure productivity, efficiency, and overall performance. |
Health & Safety Compliance | Ensuring the workplace adheres to safety regulations and standards. |
Cost Reduction | Identifying opportunities to lower operational costs without sacrificing quality. |
Inventory Management | Managing inventory levels to ensure a smooth production process. |
Machinery Maintenance | Overseeing the maintenance and repair of factory equipment. |
Process Improvement | Analyzing current processes and implementing improvements. |
Training & Development | Facilitating training programs to improve employee skills and productivity. |
Cross-functional Collaboration | Working with other departments to achieve company goals. |
Budget Management | Creating and managing budgets related to factory operations. |
Project Management | Leading special projects that improve factory operations or processes. |
Data Analysis | Using data to make informed decisions and drive improvements. |
Regulatory Compliance | Ensuring adherence to industry regulations and internal policies. |
Customer Focus | Prioritizing customer needs and ensuring products meet expectations. |
Problem-Solving Skills | Addressing and resolving operational issues efficiently. |
Incorporating these keywords into your resume, especially in the context of your specific experience, achievements, and responsibilities, can help enhance your visibility to recruiters and ATS systems.
Sample Interview Preparation Questions:
Can you describe your experience in managing production processes and ensuring efficiency within a factory setting?
How do you prioritize and delegate tasks among team members to meet production deadlines?
What strategies do you implement to maintain a safe working environment for your employees?
How do you handle conflicts or performance issues among staff in a factory?
Can you provide an example of a time when you successfully implemented a new process or technology that improved productivity?
Related Resumes for Factory Manager:
Generate Your NEXT Resume with AI
Accelerate your resume crafting with the AI Resume Builder. Create personalized resume summaries in seconds.