Industrial Worker Resume: 6 Examples to Enhance Your Job Search
### Sample 1
- **Position number:** 1
- **Person:** 1
- **Position title:** Assembly Line Worker
- **Position slug:** assembly-line-worker
- **Name:** John
- **Surname:** Doe
- **Birthdate:** 1988-05-14
- **List of 5 companies:** General Motors, Ford Motor Company, Toyota, Honda, BMW
- **Key competencies:** Assembly line efficiency, attention to detail, basic machinery operation, teamwork, quality control
---
### Sample 2
- **Position number:** 2
- **Person:** 2
- **Position title:** Forklift Operator
- **Position slug:** forklift-operator
- **Name:** Sarah
- **Surname:** Smith
- **Birthdate:** 1990-02-20
- **List of 5 companies:** Amazon, Walmart, Home Depot, FedEx, UPS
- **Key competencies:** Forklift certification, warehouse management, safety compliance, loading/unloading goods, teamwork
---
### Sample 3
- **Position number:** 3
- **Person:** 3
- **Position title:** Quality Control Inspector
- **Position slug:** quality-control-inspector
- **Name:** Michael
- **Surname:** Johnson
- **Birthdate:** 1985-11-05
- **List of 5 companies:** Pfizer, Johnson & Johnson, Merck, Nestlé, Coca-Cola
- **Key competencies:** Attention to detail, analytical skills, familiarity with inspection instruments, problem-solving, regulatory knowledge
---
### Sample 4
- **Position number:** 4
- **Person:** 4
- **Position title:** Warehouse Worker
- **Position slug:** warehouse-worker
- **Name:** Emily
- **Surname:** Brown
- **Birthdate:** 1992-09-30
- **List of 5 companies:** Target, Costco, IKEA, Lowe's, BJ's Wholesale
- **Key competencies:** Inventory management, heavy lifting, order fulfillment, safety practices, teamwork
---
### Sample 5
- **Position number:** 5
- **Person:** 5
- **Position title:** Machine Operator
- **Position slug:** machine-operator
- **Name:** William
- **Surname:** Williams
- **Birthdate:** 1983-07-25
- **List of 5 companies:** Boeing, Raytheon, Lockheed Martin, Honeywell, Caterpillar
- **Key competencies:** CNC machining, mechanical aptitude, machine maintenance, production scheduling, quality assurance
---
### Sample 6
- **Position number:** 6
- **Person:** 6
- **Position title:** Production Supervisor
- **Position slug:** production-supervisor
- **Name:** Jessica
- **Surname:** Wilson
- **Birthdate:** 1980-03-15
- **List of 5 companies:** PepsiCo, Kraft Heinz, Unilever, Mars, Nestlé
- **Key competencies:** Leadership, process optimization, workflow management, team motivation, safety protocols
---
These sample resumes provide a brief outline for each individual, showing their potential sub-positions within the field of industrial work.
---
### Sample 1
**Position number:** 1
**Position title:** Machine Operator
**Position slug:** machine-operator
**Name:** John
**Surname:** Doe
**Birthdate:** 1985-05-12
**List of 5 companies:** Toyota, General Motors, Ford, Caterpillar, Honeywell
**Key competencies:**
- Proficient in operating industrial machinery
- Strong attention to detail
- Time management skills
- Basic troubleshooting and mechanical repair
- Safety compliance and regulations adherence
---
### Sample 2
**Position number:** 2
**Position title:** Assembly Line Worker
**Position slug:** assembly-line-worker
**Name:** Emily
**Surname:** Johnson
**Birthdate:** 1990-08-25
**List of 5 companies:** Procter & Gamble, Johnson & Johnson, PepsiCo, Nestlé, Siemens
**Key competencies:**
- Quick learner with the ability to follow instructions
- Experience in high-paced assembly environments
- Quality control and inspection skills
- Team collaboration and communication
- Strong manual dexterity
---
### Sample 3
**Position number:** 3
**Position title:** Production Technician
**Position slug:** production-technician
**Name:** Michael
**Surname:** Smith
**Birthdate:** 1978-11-30
**List of 5 companies:** General Electric, Honeywell, Bosch, 3M, Rockwell Automation
**Key competencies:**
- Technical awareness of production processes
- Equipment calibration and maintenance
- Problem-solving skills for production-related issues
- Inventory management and logistics
- Understanding of lean manufacturing principles
---
### Sample 4
**Position number:** 4
**Position title:** Quality Assurance Inspector
**Position slug:** quality-assurance-inspector
**Name:** Sarah
**Surname:** Williams
**Birthdate:** 1987-06-17
**List of 5 companies:** Samsung, Intel, Lockheed Martin, Coca-Cola, Pfizer
**Key competencies:**
- Knowledge of quality control methods and standards
- Strong analytical skills for data analysis
- Excellent observational skills
- Ability to manage multiple tasks effectively
- Commitment to continuous improvement practices
---
### Sample 5
**Position number:** 5
**Position title:** Warehouse Associate
**Position slug:** warehouse-associate
**Name:** David
**Surname:** Brown
**Birthdate:** 1992-02-01
**List of 5 companies:** Amazon, UPS, FedEx, Walmart, Target
**Key competencies:**
- Forklift operation and materials handling experience
- Knowledge of inventory management systems
- Physical stamina and ability to lift heavy materials
- Teamwork and communication skills
- Attention to safety protocols
---
### Sample 6
**Position number:** 6
**Position title:** Forklift Operator
**Position slug:** forklift-operator
**Name:** Laura
**Surname:** Taylor
**Birthdate:** 1983-09-20
**List of 5 companies:** Home Depot, Costco, DHL, Panasonic, PepsiCo
**Key competencies:**
- Certified forklift operation
- Understanding of warehouse safety protocols
- Skilled in loading and unloading freight
- Quick reflexes and hand-eye coordination
- Strong organizational skills and time management
---
These sample resumes focus on various subpositions within the industrial worker field, showcasing different competencies and experiences that accommodate the specific needs of each role.
Industrial Worker Resume Examples: 6 Winning Templates and Tips
We are seeking a skilled industrial worker with a proven track record of leadership in fast-paced environments. The ideal candidate has successfully led teams to enhance productivity, resulting in a 20% increase in output and a 15% reduction in downtime. With strong collaborative skills, they foster a culture of safety and innovation, driving projects that align with organizational goals. Leveraging their technical expertise, they have designed and conducted training programs that elevate team competencies and efficiency. Join us to make a significant impact in our operations by mentoring colleagues and ensuring high standards of quality and performance.
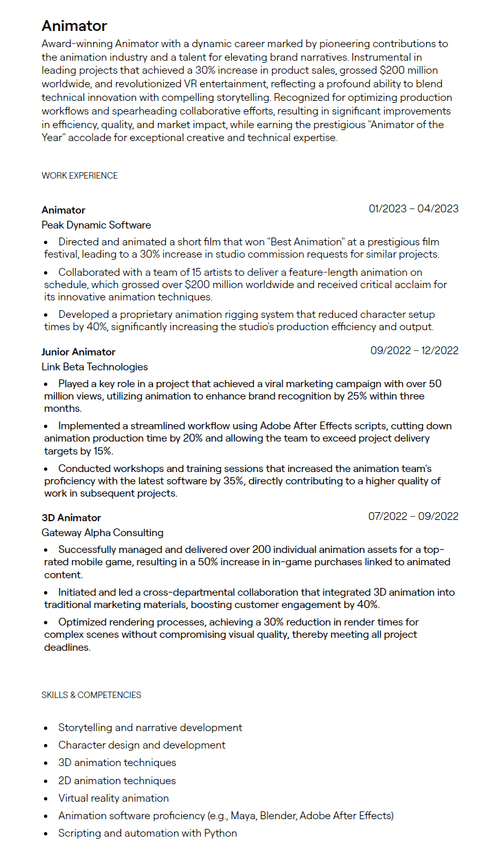
Industrial workers play a pivotal role in maintaining and enhancing production processes across various manufacturing sectors. Their expertise in operating machinery, adhering to safety protocols, and executing quality control measures is essential for ensuring efficient and safe operations. To excel in this position, candidates should possess technical skills, problem-solving abilities, and a strong attention to detail. Additionally, physical stamina and teamwork are crucial for success in often demanding environments. Securing a job in this field typically requires relevant training or certifications, a solid understanding of industry standards, and an eagerness to learn and adapt to new technologies.
Common Responsibilities Listed on Industrial Worker Resumes:
Sure! Here are 10 common responsibilities often listed on industrial worker resumes:
Operating Machinery: Safely operating and maintaining heavy machinery and equipment, such as forklifts, conveyors, and assembly line tools.
Quality Control: Inspecting products for quality assurance, ensuring they meet company and industry standards.
Safety Compliance: Adhering to safety protocols and regulations to maintain a safe work environment, including wearing appropriate personal protective equipment (PPE).
Assembly Line Work: Participating in assembly line production, following instructions to build products efficiently and correctly.
Material Handling: Managing the storage, movement, and organization of raw materials and finished products within the facility.
Preventive Maintenance: Performing routine maintenance checks on tools and equipment to prevent breakdowns and ensure optimal performance.
Record Keeping: Maintaining accurate logs and records of production outputs, equipment maintenance, and inventory levels.
Team Collaboration: Working closely with team members and supervisors to meet production goals and improve processes.
Troubleshooting Issues: Identifying and resolving production issues quickly and effectively to minimize downtime.
Training New Employees: Assisting in the onboarding and training of new workers on equipment operation, safety standards, and company policies.
These responsibilities reflect the diverse skills and duties of industrial workers across various industries.
When crafting a resume for a machine operator, it's crucial to highlight proficiency in operating industrial machinery, along with strong attention to detail and time management skills. Emphasizing basic troubleshooting and mechanical repair capabilities will demonstrate technical aptitude. Additionally, showcasing adherence to safety compliance and regulations is essential, as it reflects a commitment to maintaining a safe work environment. Listing experience with reputable companies within the industry can enhance credibility. Overall, focus on relevant competencies and achievements that align with the responsibilities of the machine operator role.
[email protected] • 555-0123 • https://www.linkedin.com/in/johndoe • https://twitter.com/johndoe1985
John Doe is an experienced Machine Operator with a solid background in operating industrial machinery across leading companies such as Toyota and Ford. Born on May 12, 1985, he possesses key competencies including strong attention to detail, effective time management skills, and basic troubleshooting and mechanical repair abilities. Committed to adhering to safety compliance and regulations, John demonstrates a proactive approach to his work. His extensive experience equips him to excel in fast-paced manufacturing environments, making him a valuable asset in ensuring operational efficiency and quality in production.
WORK EXPERIENCE
- Operated advanced machinery to manufacture automotive parts, consistently meeting production targets.
- Implemented safety protocols that reduced workplace accidents by 30%.
- Collaborated with quality assurance teams to identify areas of improvement, enhancing output quality by 15%.
- Conducted routine maintenance on machines, minimizing downtime and ensuring operational efficiency.
- Trained new employees on machinery operation and safety standards, contributing to a more informed workforce.
- Led a team of operators to streamline the machining process, resulting in a 20% increase in productivity.
- Conducted detailed inspections of completed products, ensuring compliance with strict quality standards.
- Developed and documented best practices for machine operation, improving overall efficiency.
- Collaborated with engineers to troubleshoot equipment issues, reducing repair time by 40%.
- Participated in regular safety audits and training sessions, fostering a culture of safety within the department.
- Utilized advanced computer systems to monitor machine performance data, identifying trends and areas for improvement.
- Achieved 98% on-time production delivery through effective time management and prioritization.
- Operated CNC machinery, contributing to the successful production of precision components.
- Worked closely with maintenance teams to schedule preventive maintenance, enhancing machine longevity.
- Championed the integration of new machinery that increased production capabilities by 25%.
- Implemented lean manufacturing principles to optimize workflows, resulting in a significant reduction in waste.
- Conducted training for junior operators on equipment and safety measures, ensuring consistent operational quality.
- Collaborated with cross-functional teams to launch new production lines, contributing to an expanded product offering.
- Utilized data analysis software to track machine performance metrics, leading to actionable insights for improvement.
- Recognized as 'Employee of the Month' for exceptional contributions to safety and process optimization.
SKILLS & COMPETENCIES
- Proficient in operating and monitoring industrial machinery
- Strong attention to detail and precision in tasks
- Effective time management and prioritization of workloads
- Basic troubleshooting skills and mechanical repair knowledge
- Adherence to safety compliance and regulations
- Ability to work independently and as part of a team
- Strong problem-solving skills in operational contexts
- Understanding of machinery maintenance practices
- Willingness to learn and adapt to new technologies
- Effective communication skills in a manufacturing environment
COURSES / CERTIFICATIONS
Here are five certifications or complete courses for John Doe, the Machine Operator:
Certified Forklift Operator
Date Completed: March 2019OSHA 10-Hour General Industry Safety Training
Date Completed: July 2021Basic Machine Maintenance Certification
Date Completed: November 2020Lean Manufacturing Fundamentals
Date Completed: January 2022Advanced Troubleshooting Techniques for Industrial Equipment
Date Completed: February 2023
EDUCATION
Education for John Doe (Machine Operator)
Associate Degree in Industrial Technology
- Institution: Community College of Technology
- Dates: 2003 - 2005
High School Diploma
- Institution: Springfield High School
- Dates: 1999 - 2003
When crafting a resume for the assembly line worker position, it's crucial to highlight adaptability and the ability to thrive in high-paced environments. Emphasize quick learning capabilities, adherence to instructions, and experience in quality control and inspection. Showcase teamwork and communication skills, as collaboration is vital on assembly lines. Additionally, strong manual dexterity should be underscored, along with any relevant experiences in similar roles or industries. Referring to prior companies where similar work was performed can enhance credibility, illustrating familiarity with the industry and commitment to maintaining high production standards.
[email protected] • (555) 123-4567 • https://www.linkedin.com/in/emilyjohnson • https://twitter.com/emilyjohnson
Dynamic and detail-oriented Assembly Line Worker with extensive experience in fast-paced manufacturing environments. Proven ability to quickly learn and implement instructions, ensuring efficient production processes. Skilled in quality control and inspection, with strong manual dexterity and teamwork capabilities. Demonstrates excellent communication skills and a collaborative spirit, contributing to high-performing teams. Committed to maintaining safety standards while achieving production goals. Previously employed by industry leaders like Procter & Gamble and Johnson & Johnson, showcasing adaptability and reliability in various assembly settings. Ready to leverage skills to enhance operational efficiency and product quality in future roles.
WORK EXPERIENCE
- Successfully contributed to a 20% increase in production efficiency by implementing a new assembly process.
- Trained and mentored new employees on machinery operation and safety protocols, improving team performance.
- Conducted regular quality assurance tests, reducing defects by 15%, which enhanced product reliability.
- Collaborated with team members to optimize workflow and minimize downtime during peak production periods.
- Participated in cross-departmental meetings to provide input on process improvements and product enhancements.
- Played a key role in maintaining high standards of quality control, resulting in a 30% reduction in product returns.
- Assisted in the implementation of lean manufacturing principles, contributing to a more streamlined production process.
- Utilized strong manual dexterity to effectively operate complex assembly machinery, ensuring timely production.
- Developed and maintained positive relationships with team members, fostering a collaborative work environment.
- Recognized as 'Employee of the Month' multiple times for outstanding performance and commitment to deadlines.
- Increased assembly speed by 15% through innovative techniques and consistent communication with supervisors.
- Performed routine maintenance on assembly equipment, which decreased downtime and improved productivity.
- Engaged in continuous training sessions to stay updated on the latest production techniques and quality standards.
- Contributed to team discussions focused on safety improvements, leading to an accident reduction of 20%.
- Collaborated in a special project that introduced automation, ultimately decreasing labor costs.
- Assisted in the launch of a new product line, which achieved sales goals within the first quarter of launch.
- Maintained high safety compliance, receiving commendation from management for adherence to regulations.
- Streamlined packaging processes by suggesting improvements that reduced material waste by 10%.
- Facilitated communication between assembly teams to enhance collaborative efforts on projects.
- Provided feedback on product prototypes during assembly, aiding in the refinement process before mass production.
SKILLS & COMPETENCIES
Here are 10 skills for Emily Johnson, the Assembly Line Worker:
- Quick learner and ability to adapt to new tasks
- Proficient in following detailed instructions and procedures
- Experience in working in fast-paced assembly environments
- Strong manual dexterity for handling small parts
- Quality control and inspection techniques
- Team collaboration skills to work effectively with co-workers
- Excellent communication skills for clear information exchange
- Time management skills to meet production deadlines
- Ability to use basic hand tools and equipment
- Understanding of safety procedures and practices in a manufacturing setting
COURSES / CERTIFICATIONS
Here are five certifications or completed courses for Emily Johnson, the Assembly Line Worker:
Lean Manufacturing Certification
Institution: American Society for Quality (ASQ)
Date: March 2021Forklift Safety Training and Certification
Institution: OSHA Training Institute
Date: July 2022Basic Quality Control Techniques Course
Institution: National Institute of Standards and Technology (NIST)
Date: October 2020Teamwork and Communication Skills Workshop
Institution: Local Workforce Development Board
Date: January 2023OSHA 10-Hour General Industry Safety Training
Institution: OSHA
Date: April 2022
EDUCATION
High School Diploma
Springfield High School, Springfield, IL
Graduated: May 2008Associate Degree in Manufacturing Technology
Community College of Springfield, Springfield, IL
Completed: May 2010
When crafting a resume for the Production Technician position, it's crucial to highlight technical expertise in production processes, which demonstrates the ability to understand and optimize operations. Emphasize skills in equipment calibration, maintenance, and troubleshooting to showcase reliability in maintaining production efficiency. Additionally, include experience in inventory management and knowledge of lean manufacturing principles to illustrate a commitment to efficient practices. Highlight problem-solving abilities and adaptability in fast-paced environments, along with a strong work ethic and teamwork skills, to align with the demands of the role and the expectations of potential employers.
[email protected] • (555) 123-4567 • https://www.linkedin.com/in/michael-smith • https://twitter.com/michael_smith
Dedicated Production Technician with over 15 years of experience in the industrial sector, specializing in equipment calibration and maintenance. Proven track record at leading companies like General Electric and Honeywell, demonstrating technical awareness of production processes and effective problem-solving skills for various production-related issues. Skilled in inventory management, logistics, and applying lean manufacturing principles to enhance operational efficiency. Committed to continuous improvement and fostering a collaborative work environment, ensuring high standards of quality and productivity in every project undertaken. Seeking to leverage expertise to contribute to a dynamic production team.
WORK EXPERIENCE
- Calibrated and maintained production equipment to ensure optimal performance, reducing downtime by 20%.
- Led a team in implementing lean manufacturing principles, resulting in a 15% increase in production efficiency.
- Streamlined inventory management processes that enhanced logistics and reduced waste.
- Collaborated with design engineers to troubleshoot production issues, leading to improved product quality.
- Trained new hires on operational procedures and safety protocols, enhancing team productivity.
- Utilized technical awareness to optimize production processes resulting in a 30% decrease in cycle time.
- Initiated and led a project for equipment refurbishment that enhanced operational reliability.
- Conducted regular equipment audits and provided solutions to improve efficiency, reducing overhead costs by 10%.
- Worked cross-functionally with quality assurance to implement corrective actions on production defects.
- Mentored junior technicians, helping them achieve technical proficiency in equipment operation and troubleshooting.
- Spearheaded the implementation of a new production tracking system that improved material usage tracking.
- Played a key role in a team that reduced waste by 25% through process improvement initiatives.
- Managed safety compliance audits ensuring the facility passed all regulations without violations.
- Acted as the liaison between production and maintenance teams to ensure minimal disruption during maintenance activities.
- Achieved recognition for excellence in safety handling leading to a notable decrease in incidents.
- Directed team activities to enhance process efficiency, achieving a 40% increase in output within six months.
- Implemented advanced troubleshooting techniques that reduced machine downtime by 15%.
- Conducted training seminars on equipment operation and safety protocols for new employees.
- Developed a comprehensive maintenance schedule that improved equipment lifespan and reliability.
- Coordinated with department heads to streamline operations and minimize bottlenecks in production.
SKILLS & COMPETENCIES
Skills for Michael Smith (Production Technician)
- Technical awareness of production processes
- Equipment calibration and maintenance
- Problem-solving skills for production-related issues
- Inventory management and logistics
- Understanding of lean manufacturing principles
- Proficient in using production software and machinery
- Strong analytical skills for process improvement
- Excellent communication and team collaboration
- Ability to adhere to safety regulations and practices
- Flexibility to adapt to changing production demands
COURSES / CERTIFICATIONS
Here’s a list of 5 certifications or completed courses for Michael Smith, the Production Technician from Sample 3:
Certified Production Technician (CPT)
- Date: June 2019
Lean Manufacturing Principles
- Date: March 2020
Six Sigma Green Belt Certification
- Date: November 2021
Forklift Operation and Safety Course
- Date: January 2022
Industrial Equipment Maintenance Workshop
- Date: July 2022
EDUCATION
Education for Michael Smith (Position number: 3, Production Technician)
Associate Degree in Industrial Technology
Community College of Tech, Graduated: May 2000Certification in Lean Manufacturing Principles
Lean Institute, Completed: August 2015
When crafting a resume for the Quality Assurance Inspector position, it is crucial to highlight expertise in quality control methods and industry standards. Emphasize analytical and observational skills, showcasing the ability to analyze data effectively and identify discrepancies. Include experience managing multiple tasks and a commitment to continuous improvement practices, which demonstrates dedication to enhancing quality and efficiency. Additionally, mentioning familiarity with specific industries or notable companies can enhance credibility. Tailoring the resume to reflect relevant skills and experiences will better position the candidate for success in this specialized role.
[email protected] • (555) 123-4567 • https://www.linkedin.com/in/sarahwilliams • https://twitter.com/sarahwilliamsQA
**Summary:**
Dedicated Quality Assurance Inspector with extensive experience in major corporations such as Samsung and Intel. Proficient in quality control methods and standards, with strong analytical abilities for precise data analysis. Exceptional observational skills ensure thorough inspections and adherence to industry regulations. Highly organized, capable of managing multiple tasks effectively, while committed to continuous improvement practices. Proven track record in enhancing product quality and operational efficiency, making a significant impact in fast-paced environments. A reliable team player focused on delivering excellence and maintaining high standards in every project undertaken.
WORK EXPERIENCE
- Led quality assurance initiatives that reduced defect rates by 25% over three years.
- Implemented new quality control processes, resulting in a 15% increase in overall production efficiency.
- Conducted regular audits and inspections to ensure compliance with ISO 9001 certification, successfully passing all evaluations.
- Collaborated with cross-functional teams to design and develop training programs on quality standards.
- Utilized statistical analysis to identify trends in production quality, leading to targeted improvements.
- Received the 'Employee of the Month' award multiple times for exceptional performance and contribution to quality enhancement.
- Developed and implemented inspection criteria that improved product reliability and customer satisfaction ratings.
- Created detailed reports that informed management decisions on production practices and quality enhancements.
- Trained and mentored a team of junior inspectors, fostering a culture of quality and accountability.
- Piloted a new non-destructive testing technique that decreased inspection time by 20% without compromising quality.
- Established a feedback loop with production teams to address quality issues and develop preventative measures.
- Recognized as a key contributor to achieving a significant decrease in returns and complaints from end-users.
- Engaged in root cause analysis for production issues, leading to effective corrective actions that reduced rework costs by 30%.
- Performed statistical sampling and analysis to maintain high product quality and compliance with industry standards.
- Drove continuous improvement initiatives that cultivated a proactive approach to quality assurance among team members.
- Coordinated with suppliers to enhance quality of raw materials, leading to improved end-product quality.
- Facilitated quality assurance training sessions for new hires, ensuring a strong foundational understanding of required standards.
- Instrumental in the successful launch of a new product line that met all quality expectations during initial production.
- Conducted detailed inspections of manufactured products, identifying defects and suggesting practical improvements.
- Collaborated with engineering teams to enhance product designs based on quality feedback, leading to a 10% reduction in customer returns.
- Managed documents related to quality management systems, ensuring compliance with regulatory requirements.
- Participated in regular team meetings to discuss quality metrics and brainstorm strategic improvements.
- Utilized problem-solving techniques to resolve quality issues swiftly and effectively in the production process.
- Achieved recognition from upper management for exemplifying best practices in quality assurance procedures.
SKILLS & COMPETENCIES
Here are 10 skills for Sarah Williams, the Quality Assurance Inspector from Sample 4:
- Proficient in quality control methods and standards
- Strong analytical skills for data analysis
- Excellent observational skills
- Ability to manage multiple tasks effectively
- Commitment to continuous improvement practices
- Knowledge of inspection tools and equipment
- Familiarity with regulatory compliance and standards
- Strong communication skills for team collaboration
- Detail-oriented with a focus on accuracy
- Problem-solving skills for identifying and resolving quality issues
COURSES / CERTIFICATIONS
Here is a list of 5 certifications and completed courses for Sarah Williams, the Quality Assurance Inspector from Sample 4:
Certified Quality Auditor (CQA)
Issued by: American Society for Quality (ASQ)
Date: June 2019ISO 9001:2015 Internal Auditor Training
Issued by: International Register of Certificated Auditors (IRCA)
Date: January 2020Six Sigma Green Belt Certification
Issued by: International Association for Six Sigma Certification (IASSC)
Date: March 2021Statistical Process Control (SPC) Training
Issued by: Quality Assurance Institute (QAI)
Date: November 2020Quality Management Fundamentals Course
Issued by: Coursera (offered by the University of Maryland)
Date: April 2022
EDUCATION
- Bachelor of Science in Industrial Engineering, University of Michigan, Graduated May 2009
- Associate Degree in Quality Control Technology, Community College of Atlanta, Graduated May 2007
When crafting a resume for a warehouse associate position, it's crucial to highlight relevant experience and skills, including proficiency in forklift operation and materials handling. Emphasizing knowledge of inventory management systems and adherence to safety protocols is essential. Additionally, showcasing physical stamina and the ability to lift heavy items is important. Strong teamwork and communication skills should also be underscored, as collaboration is vital in a warehouse environment. Tailoring the resume to reflect experience with reputable companies can enhance credibility and attract potential employers' attention.
[email protected] • +1-555-123-4567 • https://www.linkedin.com/in/david-brown • https://twitter.com/david_brown
David Brown is an experienced Warehouse Associate with a strong background in materials handling and inventory management, having worked with leading companies like Amazon and UPS. He possesses essential skills in forklift operation, ensuring adherence to safety protocols while effectively managing warehouse tasks. Known for his physical stamina and ability to lift heavy objects, David demonstrates excellent teamwork and communication abilities, making him a valuable asset in high-paced environments. His attention to detail and commitment to efficient operations contribute to a productive workplace, aligning well with the demands of any industrial setting.
WORK EXPERIENCE
- Managed the logistics of inbound and outbound shipments, increasing efficiency by 20%.
- Implemented a new inventory tracking system that reduced errors by 15%.
- Collaborated with team members to streamline workflows, enhancing overall productivity.
- Trained new employees on safety protocols and operational procedures, ensuring compliance with company standards.
- Conducted regular safety audits, contributing to a 30% reduction in workplace accidents.
- Operated forklifts to safely transport materials within the warehouse, improving delivery times by 25%.
- Achieved certification in forklift operation and maintained a 100% safety record during tenure.
- Assisted with the reorganization of warehouse layout, which optimized space utilization and improved workflow.
- Monitored and maintained equipment, ensuring all machinery was in excellent working condition.
- Created comprehensive reports on inventory levels and product movement, enhancing inventory management.
- Operated and monitored machinery for the production of goods, maintaining high standards of quality and efficiency.
- Developed and implemented preventive maintenance schedules that reduced downtime by 20%.
- Collaborated with quality assurance teams to identify and resolve production issues swiftly.
- Participated in continuous improvement initiatives, leading to cost reductions and increases in product throughput.
- Coached team members on equipment operation and best practices, enhancing overall team performance.
- Performed rigorous inspections of products to ensure compliance with quality standards, decreasing defects by 40%.
- Utilized analytical skills to analyze data and drive improvements in product quality and manufacturing processes.
- Developed training materials for new hires, enhancing their understanding of quality control methods.
- Conducted routine audits and documented findings, ensuring transparency and accountability in the QA process.
- Led a project team that developed new quality assurance protocols, resulting in significant improvements in product consistency.
SKILLS & COMPETENCIES
Here are 10 skills for David Brown, the Warehouse Associate from Sample 5:
- Forklift operation and certification
- Proficient in materials handling techniques
- Knowledge of inventory management systems
- Strong physical stamina and ability to lift heavy materials
- Familiarity with safety protocols and OSHA regulations
- Teamwork and effective communication skills
- Time management and organizational abilities
- Experience in order picking and packing processes
- Basic computer skills for inventory tracking
- Attention to detail and accuracy in stock management
COURSES / CERTIFICATIONS
Here are five certifications or completed courses for David Brown, the Warehouse Associate:
Forklift Operator Certification
Completed: March 2020Hazardous Materials Handling Course
Completed: June 2021OSHA 10-Hour General Industry Safety and Health
Completed: October 2021Inventory Management Systems Training
Completed: January 2022Team Building and Communication Skills Workshop
Completed: May 2023
EDUCATION
Education for David Brown (Warehouse Associate)
High School Diploma
Springfield High School, Springfield, IL
Graduated: June 2010Certified Forklift Operator Training
Forklift Certification Institute, Chicago, IL
Completed: March 2018
When crafting a resume for a forklift operator position, it’s crucial to highlight relevant certifications, particularly for forklift operation. Emphasizing a strong understanding of warehouse safety protocols is essential, demonstrating the ability to adhere to safety regulations. Include specific skills such as loading and unloading freight, as well as quick reflexes and excellent hand-eye coordination. Additionally, showcasing organizational abilities and effective time management will illustrate reliability in fast-paced environments. Previous experience in notable warehouses or companies can further enhance credibility and attract attention from potential employers in the industrial sector.
[email protected] • +1-555-0123 • https://www.linkedin.com/in/laurataylor • https://twitter.com/laurataylor
**Summary for Laura Taylor - Forklift Operator**
Dedicated and certified forklift operator with extensive experience in loading and unloading freight within dynamic warehouse environments. Proven ability to adhere to safety protocols and ensure efficient materials handling. Possesses strong organizational skills, quick reflexes, and excellent hand-eye coordination, enabling effective operation of forklifts and other warehouse equipment. A reliable team player committed to maintaining a safe and organized workspace, with exceptional time management capabilities that enhance productivity. Previous experience with leading companies, including Home Depot and Costco, underlines a solid work ethic and proficiency in logistics operations.
WORK EXPERIENCE
- Successfully operated forklifts in a fast-paced warehouse environment, ensuring timely loading and unloading of freight.
- Maintained a 100% safety record while adhering to all warehouse safety protocols.
- Streamlined loading processes, resulting in a 20% reduction in wait times during peak hours.
- Trained new employees on forklift operation and safety regulations, enhancing team efficiency and skill level.
- Contributed to inventory management through precise movements and accurate recording of material locations.
- Awarded 'Employee of the Month' for outstanding performance and commitment to safety standards.
- Assisted in the optimization of warehouse floor layout, improving operational efficiency by 15%.
- Participated in routine safety inspections, ensuring compliance with OSHA regulations and reducing workplace accidents.
- Utilized inventory management software to keep track of incoming and outgoing shipments, enhancing accuracy.
- Collaborated with team members to implement best practices on material handling, leading to successful project completions.
- Efficiently managed the flow of goods to ensure smooth operations in a busy warehouse setting.
- Monitored stock levels and reported discrepancies to management, helping maintain accurate inventory records.
- Assisted in the creation of training materials for new warehouse associates, facilitating smoother onboarding processes.
- Supported cross-departmental initiatives to enhance communication and teamwork, resulting in an overall increase in productivity.
- Handled customer returns and exchanges with a focus on maintaining high levels of service satisfaction.
- Operated forklifts safely and efficiently, contributing to seamless supply chain operations.
- Executed detailed loading and unloading procedures that minimized damage to goods.
- Collaborated with inventory control teams to track materials and ensure timely dispatch.
- Implemented safety measures that contributed to a significant drop in operational incidents.
- Worked with management to refine processes, improving overall logistics operations.
SKILLS & COMPETENCIES
Here are 10 skills for Laura Taylor, the Forklift Operator from Sample 6:
- Certified forklift operation
- Proficient in loading and unloading materials
- Familiarity with warehouse safety protocols
- Strong hand-eye coordination
- Excellent reflexes for operating machinery
- Effective time management skills
- Strong organizational abilities
- Basic maintenance and troubleshooting skills for forklift equipment
- Ability to follow safety guidelines and company policies
- Team collaboration and communication skills
COURSES / CERTIFICATIONS
Here are five certifications and courses that Laura Taylor, the Forklift Operator, might pursue:
OSHA Forklift Operator Certification
Date completed: March 2021Warehouse Safety and Hazard Communication Training
Date completed: January 2022Certified Logistics Associate (CLA)
Date completed: June 2022Defensive Driving Course for Forklift Operators
Date completed: November 2021Time Management for Warehouse Personnel
Date completed: April 2023
EDUCATION
- Associate Degree in Logistics and Supply Chain Management, Community College of City, 2002-2004
- Forklift Operator Certification, National Safety Council, 2021
Crafting an effective resume as an industrial worker requires a strategic approach that not only highlights your experience but also showcases your skills in a way that aligns with industry expectations. Begin by emphasizing technical proficiency with industry-standard tools and machinery pertinent to the specific job you’re applying for. For example, if you have experience with CNC machines, welding, or quality control systems, make sure these details are prominently featured in your skills section. Use industry-specific keywords that match the job description to help your resume pass automated applicant tracking systems. Additionally, don't overlook the importance of demonstrating both hard and soft skills. While technical abilities are crucial, soft skills like teamwork, communication, and problem-solving are equally important and can set you apart from other candidates. Consider including specific examples or anecdotes that illustrate how you've effectively utilized these skills in previous roles, making your resume more compelling.
Tailoring your resume to the specific industrial worker job role is essential for capturing the attention of hiring managers. Begin by reviewing the job description carefully and identifying the key qualifications and skills that employers are seeking. Then, customize your resume to reflect how your particular experiences and skills align with these requirements. This may include reorganizing your work history to prioritize relevant positions or incorporating specific achievements that demonstrate your ability to meet the challenges of the role. Be succinct yet impactful; use bullet points to make your qualifications easy to read while ensuring each point includes quantifiable outcomes when possible, such as meeting production targets or improving efficiency. Given the competitive nature of the job market for industrial workers, your resume must stand out. By strategically showcasing your skills, technical proficiency, and understanding of the role, you will create a resume that not only highlights your qualifications but also positions you as a top candidate for the job.
Essential Sections for an Industrial Worker Resume
Contact Information
- Full name
- Phone number
- Email address
- LinkedIn profile (if applicable)
- Address (optional)
Objective or Summary Statement
- Brief overview of skills and career goals
- Tailored to the specific job application
Work Experience
- Job titles
- Company names and locations
- Dates of employment
- Key responsibilities and achievements
Education
- Degree(s) obtained
- Schools attended
- Graduation dates
Skills
- Relevant technical skills (e.g., machinery operation, safety protocols)
- Soft skills (e.g., teamwork, problem-solving)
Certifications and Licenses
- Relevant industry certifications (e.g., OSHA, forklift operator)
- Expiration dates (if applicable)
References
- Available upon request (or include names and contact information)
Additional Sections to Stand Out
Professional Affiliations
- Membership in relevant organizations or unions
Technical Proficiencies
- Familiarity with specific tools, machinery, or software
Achievements and Awards
- Recognition for exemplary work or safety records
Volunteer Experience
- Relevant volunteer work that showcases skills or commitment to the industry
Projects
- Notable projects or initiatives you played a role in, detailing your contributions
Languages
- Additional languages spoken, with proficiency levels
Training and Workshops
- Relevant training sessions or professional development courses attended
Generate Your Resume Summary with AI
Accelerate your resume crafting with the AI Resume Builder. Create personalized resume summaries in seconds.
Crafting an impactful resume headline is crucial for industrial workers aiming to make a strong first impression on hiring managers. The headline serves as a snapshot of your skills and specialization, enticing potential employers to explore your application further. To create a compelling headline, start by identifying your distinctive qualities and core competencies that are relevant to the industry.
Consider the specific roles you are targeting; specificity will resonate more with hiring managers. For example, instead of a vague title like "Experienced Industrial Worker," opt for "Certified Forklift Operator and Safety Compliance Specialist with 5+ Years in Manufacturing." This headline clearly communicates your specialization, relevant certifications, and the experience you bring to the table.
Your headline should also reflect key achievements or skill sets that set you apart. Think about the aspects of your work that have garnered praise or led to measurable improvements. Incorporating such details can enhance your visibility in a competitive market. For instance: "Lean Manufacturing Expert Driving 15% Productivity Increases through Continuous Improvement Initiatives."
Additionally, make sure your headline aligns with the job description. Use keywords that are commonly found in job listings to increase the chances of passing automated applicant tracking systems. Tailoring your headline to the specific role not only captures attention but also demonstrates your interest in the position.
Remember, the headline is the first element hiring managers see, and it sets the tone for your entire resume. By effectively communicating your specialization, distinctive skills, and career successes, you can significantly increase your chances of standing out among a crowded field of candidates. Keep it concise, impactful, and relevant, ensuring it reflects who you are as a professional.
Assembly Line Technician Resume Headline Examples:
Strong Resume Headline Examples
Strong Resume Headline Examples for Industrial Workers:
- "Dedicated Industrial Worker with 5+ Years of Experience in Manufacturing and Assembly Line Operations"
- "Skilled Forklift Operator Specializing in Safety Compliance and Efficiency Optimization"
- "Experienced Warehouse Technician with Expertise in Inventory Management and Quality Control"
Why These Are Strong Headlines:
Clarity and Specificity: Each headline clearly states the individual's area of expertise and relevant experience, making it immediately apparent to employers what qualifications they bring to the table. This specificity helps the resume stand out in a sea of generic headlines.
Quantifiable Experience: The inclusion of quantifiable years of experience (e.g., "5+ Years") demonstrates credibility and showcases a commitment to the field. This not only helps convey the candidate’s reliability but also signals their ability to handle responsibility in industrial roles.
Relevant Skills and Focus: By highlighting specific skills and focuses (like “Safety Compliance,” “Efficiency Optimization,” or “Quality Control”), these headlines appeal directly to the needs of potential employers. This strategic approach shows a clear understanding of the industry's priorities and the ability to contribute to operational goals.
Weak Resume Headline Examples
Weak Resume Headline Examples for Industrial Worker:
- "Hardworking Individual Seeking Job"
- "Unemployed Worker Looking for Opportunities"
- "Factory Worker Open to New Positions"
Why These are Weak Headlines:
Lack of Specificity: The phrase "Hardworking Individual" is vague and doesn't convey any specific skills or strengths relevant to the industrial sector. Employers often look for concrete qualifications or experiences that differentiate candidates.
Negative Connotation: The term "Unemployed Worker" carries a negative implication and may suggest a lack of recent experience or commitment. Instead, headlines should focus on what the candidate can offer rather than their current situation.
Generic and Uninspiring: "Factory Worker Open to New Positions" is generic and lacks enthusiasm or a proactive stance. It doesn't highlight any unique value the candidate could bring to an employer, making it easy to overlook in a competitive job market. A stronger headline would emphasize specific skills, certifications, or achievements relevant to the position.
A well-crafted resume summary is an essential tool for industrial workers seeking to make a strong first impression on potential employers. This snapshot of your professional experience and qualifications serves as an introduction, allowing you to convey your technical proficiency, storytelling abilities, and collaboration skills effectively. An exceptional summary captures not only your expertise but also your attention to detail, which is critical in the industrial sector. By tailoring your resume summary to align with the specific role you're targeting, you can create a compelling introduction that engages hiring managers and highlights your fit for the position.
Key Points to Include in Your Resume Summary:
Years of Experience: Mention your total years in the industrial field, showcasing your familiarity with industry standards and practices.
Specialized Styles or Industries: Highlight any specialized expertise within particular industrial sectors or techniques, demonstrating your adaptability and proficiency.
Technical Proficiency: List relevant software or tools you've mastered, emphasizing skills such as machinery operation, safety protocols, and inventory management systems that are crucial for the role.
Collaboration and Communication Abilities: Showcase your teamwork experience and ability to communicate effectively with colleagues and supervisors, which are vital in a collaborative environment.
Attention to Detail: Mention specific instances or processes where your attention to detail led to improved efficiency, quality assurance, or safety measures, reinforcing your commitment to excellence.
By following these guidelines and incorporating these elements, you can create a captivating resume summary that not only showcases your qualifications but also tells your unique professional story, setting you apart in a competitive job market.
Assembly Line Technician Resume Summary Examples:
Strong Resume Summary Examples
Resume Summary Examples for an Industrial Worker
Detail-oriented industrial worker with over 5 years of experience in manufacturing and assembly line operations. Proven ability to operate complex machinery while adhering to safety protocols and optimizing production processes to meet tight deadlines. Committed to maintaining high standards of quality and efficiency.
Dedicated industrial technician with extensive experience in process improvement and team collaboration, successfully reducing downtime by 15% in previous roles. Skilled in troubleshooting and maintaining machinery to ensure consistent production levels and safety compliance. Adaptable and proactive in high-pressure environments.
Highly motivated industrial worker with a strong background in logistics and material handling. Adept at using forklifts and other equipment to streamline workflows and improve supply chain management. Known for reliability and a strong work ethic, ensuring projects are completed on time and within budget.
Why These Are Strong Summaries:
Specificity and Experience: Each summary mentions years of experience and specific skills or achievements, giving a clear picture of the candidate's background and expertise.
Accomplishments and Impact: They highlight measurable achievements (e.g., reducing downtime by 15%, maintaining safety compliance, completing projects on time), which demonstrate the candidate's contributions to previous employers.
Keywords for ATS: The use of industry-relevant terminology (like "manufacturing," "safety protocols," "process improvement," and "logistics") can help the resume pass through Applicant Tracking Systems (ATS) and attract the attention of hiring managers.
Professional Traits: Each summary emphasizes traits such as "detail-oriented," "dedicated," "highly motivated," and "reliable," which are desirable attributes for industrial jobs, portraying the candidate as a strong team member.
Lead/Super Experienced level
Here are five bullet points for a strong resume summary for an experienced lead or supervisor level industrial worker:
Proven Leadership: Accomplished industrial supervisor with over 10 years of experience in managing diverse teams in high-paced manufacturing environments, consistently achieving production goals and improving operational efficiency.
Process Optimization: Expertise in streamlining processes and implementing lean manufacturing principles, resulting in a 20% reduction in production costs and significant increases in output quality.
Safety Compliance: Committed to maintaining the highest safety standards, with a track record of reducing workplace accidents by 30% through effective training, rigorous oversight, and continuous improvement initiatives.
Cross-Functional Collaboration: Skilled in fostering collaboration across departments, leading cross-functional teams to address production challenges and drive project success, while promoting a culture of accountability.
Performance Management: Strong background in performance monitoring and employee development, successfully coaching team members to enhance skills, boost morale, and increase retention rates within the workforce.
Senior level
Sure! Here are five examples of strong resume summaries for a senior experienced industrial worker:
Results-Driven Manufacturing Professional: Over 15 years of hands-on experience in large-scale manufacturing environments, specializing in process optimization and efficiency improvements that have led to a 20% reduction in production costs and enhanced product quality.
Expert in Operational Excellence: Proven track record in implementing Lean Six Sigma methodologies to streamline operations, resulting in a significant increase in productivity and a reduction in waste across multiple manufacturing lines.
Skilled Team Leader and Trainer: Accomplished in managing diverse teams of up to 50 employees, fostering a culture of safety and continuous improvement while mentoring junior staff to exceed performance targets.
Versatile Maintenance Specialist: Extensive expertise in machinery troubleshooting and preventative maintenance, contributing to an impressive 98% equipment uptime and minimized downtime across various production facilities.
Adaptive Supply Chain Coordinator: Strong background in coordinating logistics and inventory management with a focus on efficiency, ensuring optimal supply chain performance and a seamless flow of materials to support production goals.
Mid-Level level
Certainly! Here are five strong resume summary examples tailored for a mid-level industrial worker:
Versatile Industrial Technician with over 6 years of hands-on experience in manufacturing and assembly processes, proficient in operating heavy machinery and ensuring adherence to safety regulations to optimize productivity.
Detail-Oriented Process Operator skilled in quality control and continuous improvement methodologies, successfully implementing lean practices that resulted in a 15% reduction in operational downtime and increased overall efficiency.
Dedicated Maintenance Specialist with a proven track record in preventive maintenance and troubleshooting of industrial equipment, contributing to an enhanced lifecycle of machinery and a 20% decrease in repair costs.
Results-Driven Warehouse Associate adept at inventory management and along with supply chain logistics, consistently meeting shipment deadlines while maintaining accuracy and efficiency to support operational goals.
Experienced Quality Assurance Inspector with a strong background in conducting rigorous inspections and ensuring compliance with industry standards, leading to a 30% decrease in product defects and enhancements in customer satisfaction.
Junior level
Here are five strong resume summary examples for a junior-level industrial worker:
Enthusiastic Junior Industrial Worker with hands-on experience in assembly line processes and a solid understanding of safety protocols. Eager to contribute to team efficiency and production quality through a strong work ethic and quick learning abilities.
Detail-oriented Industrial Assistant skilled in operating machinery and performing maintenance checks to ensure optimal performance. Committed to adhering to workplace safety standards while supporting production targets in a fast-paced environment.
Motivated Entry-level Industrial Technician with experience in the manufacturing sector, adept at troubleshooting equipment issues and maintaining quality control. Ready to leverage technical skills and teamwork capabilities to enhance workflow efficiency.
Adaptable Industrial Worker with a foundational knowledge of production processes and inventory management. Proven ability to follow instructions meticulously and support team members to achieve production deadlines.
Dedicated Manufacturing Associate with experience in material handling and quality assurance. Strong communication skills, capability to work in diverse teams, and a passion for maintaining a safe, organized workplace.
Entry-Level level
Entry-Level Industrial Worker Resume Summary
Motivated and Safety-Conscious: Recent high school graduate eager to contribute to a dynamic industrial team. Strong understanding of safety protocols and a commitment to maintaining a clean and efficient workspace.
Hands-On Learner: Quick to adapt and learn new techniques and equipment operation, with a proactive attitude towards teaming and collaboration in a fast-paced environment.
Detail-Oriented and Reliable: Possesses a strong work ethic with attention to detail; consistently punctual and dedicated to producing high-quality work under supervision.
Technical Aptitude: Familiar with basic industrial machinery and tools through coursework and internships, demonstrating a clear intent to develop technical skills for increased productivity.
Strong Communicator: Effective in collaborating with team members and supervisors, ensuring optimal workflow and adherence to project timelines.
Experienced Industrial Worker Resume Summary
Dedicated Industrial Professional: Over 5 years of experience in manufacturing and warehousing environments, known for consistently meeting production targets while ensuring safety standards.
Skilled in Equipment Operation: Proficient in operating various industrial machinery, including forklifts and CNC machines, with comprehensive knowledge of maintenance practices to prolong equipment lifespan.
Team Leadership Experience: Proven track record of mentoring and training new staff, fostering a collaborative team culture that promotes safety and productivity.
Quality Assurance Advocate: Strong background in quality control processes and methodologies, with an emphasis on precision and attention to detail that enhances product reliability and customer satisfaction.
Adaptable and Efficient: Ability to quickly respond to changing production demands and troubleshoot operational challenges, ensuring seamless workflow and minimal downtime.
Weak Resume Summary Examples
Weak Resume Summary Examples for Industrial Worker
"I have some experience in manufacturing and am looking for a job in an industrial setting."
"Hard worker with basic skills in warehouse operations and a desire to learn more."
"Dependable individual interested in industrial work with no specific skills or certifications."
Why These are Weak Headlines
Lack of Specificity: The summaries are vague and do not provide any detailed information about the candidate's qualifications or experiences. They fail to mention specific roles, responsibilities, or accomplishments, which are crucial in catching the eye of employers in industrial settings.
Limited Skill Set: Phrases like "basic skills" and "some experience" suggest an inadequate level of expertise. Employers are looking for candidates who can bring a clear set of skills to the table, and these summaries do not instill confidence in the applicant's capabilities.
No Unique Selling Proposition: Each of these summaries lacks a unique selling proposition that distinguishes the candidate from others. In a competitive job market, it's important to highlight specific strengths or experiences that make one a valuable asset to the company, which these summaries fail to do.
Resume Objective Examples for Assembly Line Technician:
Strong Resume Objective Examples
Dedicated and detail-oriented industrial worker with over 5 years of experience in manufacturing and assembly processes, seeking to leverage expertise in quality control and safety protocols to contribute to a high-performance team. Committed to ensuring efficiency and enhancing productivity in a fast-paced environment.
Motivated and skilled industrial worker with a proven track record of improving operational efficiency and reducing waste. Aiming to apply hands-on experience in machine operation and maintenance to support the goals of a dynamic manufacturing facility.
Safety-conscious industrial worker with a strong background in diverse production roles, eager to bring a strong work ethic and problem-solving abilities to a collaborative team. Focused on adhering to company standards while driving continuous improvement and innovation in all tasks.
Why this is a strong objective:
These objectives are compelling because they are concise and highlight specific experience and skills relevant to the industrial sector. Each objective clearly states the candidate's background, demonstrates an understanding of the job requirements, and reflects a commitment to contributing to the employer's goals. Additionally, the language used conveys professionalism and readiness to tackle challenges, making them impactful in drawing the attention of hiring managers. Overall, these objectives not only outline what the candidate brings to the table but also indicate a strong alignment with the needs of potential employers.
Lead/Super Experienced level
Here are five strong resume objective examples tailored for a lead or highly experienced industrial worker:
Dynamic Industrial Leader with over a decade of hands-on experience in manufacturing and operations management, seeking to leverage expertise in team leadership and process optimization to enhance production efficiency and drive operational excellence.
Results-Oriented Industrial Supervisor with a proven track record in overseeing large-scale projects and improving safety protocols. Aiming to utilize extensive knowledge of industry best practices to foster a culture of continuous improvement within a forward-thinking organization.
Experienced Operations Manager with 15+ years in the industrial sector, committed to implementing innovative solutions that boost productivity and reduce waste. Seeking to contribute advanced analytical skills and leadership abilities to enhance team synergy and project success.
Dedicated Manufacturing Specialist and team leader with in-depth experience in Lean Six Sigma methodologies. Eager to apply a strong background in process improvement and staff development to lead a high-performing workforce in achieving company objectives.
Accomplished Industrial Foreman with a wealth of experience in supervising multi-disciplinary teams and managing complex workflows. Looking to bring exceptional organizational skills and a passion for safety and efficiency to a leading industrial firm focused on growth and quality improvement.
Senior level
Here are five strong resume objective examples for a senior-level industrial worker:
Highly skilled industrial worker with over 10 years of experience in high-volume manufacturing environments, seeking to leverage expertise in process optimization and team leadership to enhance productivity and operational efficiency at [Company Name].
Detail-oriented and safety-focused industrial professional with extensive knowledge in advanced machinery operation, materials handling, and production management, looking to contribute my problem-solving skills and industry insight to drive continuous improvement at [Company Name].
Results-driven industrial worker with a proven track record of exceeding production targets and reducing downtime, aiming to utilize my extensive experience in quality assurance and workforce training to support [Company Name]'s commitment to excellence.
Dynamic senior industrial worker with comprehensive experience in supply chain management and lean manufacturing principles, seeking to apply my strategic planning and strong interpersonal skills to foster a collaborative and productive work environment at [Company Name].
Dedicated industrial professional with a history of implementing innovative solutions that enhance operational workflows, looking to bring my leadership abilities and technical expertise to [Company Name] to advance its growth and efficiency goals.
Mid-Level level
Sure! Here are five strong resume objective examples for a mid-level industrial worker:
Detail-oriented industrial worker with over 5 years of experience in manufacturing processes and quality control, seeking to leverage expertise in a dynamic environment to enhance operational efficiency and team collaboration.
Dedicated manufacturing professional skilled in machinery operation and safety protocols, aiming to contribute to a progressive company by improving production workflows and maintaining high standards of quality.
Results-driven industrial technician with proven success in troubleshooting equipment issues and implementing effective maintenance strategies, looking to utilize hands-on skills in a challenging role to optimize performance and reduce downtime.
Experienced industrial operator with a solid background in assembly line processes and inventory management, eager to bring strong problem-solving abilities and teamwork skills to a reputable manufacturing firm focused on innovation.
Adaptable industrial worker with a comprehensive understanding of lean manufacturing principles and workplace safety regulations, seeking to enhance productivity and team dynamics in a mid-level position within an organization committed to excellence.
Junior level
Here are five strong resume objective examples for a junior-level industrial worker:
Dedicated and safety-conscious industrial worker with 2 years of hands-on experience in manufacturing environments, seeking to contribute to [Company Name] by leveraging technical skills and a proactive approach to maintenance and quality assurance.
Detail-oriented junior industrial worker with foundational experience in assembly line operations, looking to join [Company Name] to enhance production efficiency and uphold rigorous safety standards while further developing skills in machine operation.
Motivated industrial worker with a keen eye for detail and commitment to team collaboration, eager to bring my experience in operating machinery and performing quality checks to [Company Name] to support successful daily operations.
Enthusiastic entry-level industrial worker skilled in adhering to safety regulations and executing tasks efficiently, seeking to apply strong problem-solving skills and a solid work ethic at [Company Name] to help drive productivity and success.
Results-driven junior industrial worker with experience in working with diverse teams and utilizing hand tools, aiming to secure a position at [Company Name] to contribute to innovative production methods while continuing to learn and grow in the field.
Entry-Level level
Here are five strong resume objective examples for an entry-level industrial worker:
Safety-Focused Operator: Seeking an entry-level position in the industrial sector where I can apply my understanding of safety protocols and machine operation, while contributing to a team committed to high-quality production standards.
Dedicated Team Player: Motivated individual looking to join a dynamic industrial team, leveraging my strong work ethic and willingness to learn to support efficient operations and contribute to company goals.
Hands-On Learner: Detail-oriented and mechanically inclined recent graduate eager to secure an entry-level role in the industrial field. I aim to develop my skills while ensuring adherence to safety and quality measures.
Quality Assurance Enthusiast: Ambitious candidate seeking to start my career in the industrial industry, focused on maintaining product standards and efficiency, and eager to contribute to a reputable company while honing my technical skills.
Adaptable and Reliable Worker: Energetic individual aiming to enter the industrial workforce in an entry-level position, with a strong commitment to safety, teamwork, and continuous improvement in production processes.
Weak Resume Objective Examples
Weak Resume Objective Examples for Industrial Worker
"To obtain a position as an industrial worker where I can utilize my skills."
“Seeking an industrial worker role in a manufacturing company to learn and grow.”
"To work as an industrial worker in a reputable company and contribute to the team."
Reasons Why These Objectives are Weak:
Lack of Specificity: The first objective is vague and does not specify what skills the applicant has or how they relate to the job in question. Employers prefer candidates who clearly demonstrate their value and relevant expertise.
Lack of Initiative: The second objective suggests a passive approach to the job. Phrases like "to learn and grow" imply that the applicant is primarily focused on personal gain rather than contributing to the company’s success. This can come across as unambitious.
Generic Statements: The third objective is overly general and does not distinguish the applicant from others. It lacks strong action verbs and fails to convey what unique qualities or experiences the candidate brings to the position. A statement like this could apply to many different applicants and lacks a personal touch.
In summary, weak objectives often fail to convey distinct value, align with employer needs, and demonstrate enthusiasm or commitment, all of which are essential for standing out in a competitive job market.
Writing an effective work experience section for an industrial worker's resume is crucial to showcasing your skills, accomplishments, and suitability for the role. Here are some key guidelines to consider:
Start with Job Titles: Clearly state your job title, followed by the company name, location, and dates of employment. Use a bold font for job titles to make them stand out.
Use Action Verbs: Start each bullet point with strong action verbs (e.g., Operated, Assembled, Inspected, Maintained). This conveys a sense of proactivity and engagement.
Focus on Relevant Experience: Tailor your work experience to highlight roles that are most relevant to the industrial position you are applying for. Include any specific machinery, equipment, or processes that relate to the job description.
Quantify Achievements: Where possible, quantify your accomplishments. For instance, mention how you improved production efficiency by a percentage, reduced downtime, or contributed to safety improvements.
Highlight Skills: Incorporate important skills such as adherence to safety protocols, attention to detail, teamwork, and problem-solving abilities. These skills are crucial in an industrial setting.
Include Certifications: If applicable, mention any certifications relevant to industrial work (e.g., OSHA safety certification, forklift operation, or industry-specific training).
Keep It Concise: Use bullet points for clarity and brevity. Aim for 3-5 bullet points per position, focusing on the most impactful information.
Show Progression: If applicable, highlight any promotions or increased responsibilities over time. This demonstrates growth and reliability in your professional journey.
Proofread: Ensure there are no grammatical errors or typos, as these can undermine your professionalism.
By following these guidelines, you can create a compelling work experience section that effectively highlights your qualifications for an industrial worker role, making a strong impression on potential employers.
Best Practices for Your Work Experience Section:
Here are 12 best practices for the work experience section of a resume tailored for an industrial worker:
Use Clear Job Titles: Ensure your job titles accurately reflect your role and responsibilities. Use industry-standard terminology where possible.
Quantify Achievements: Use numbers to highlight your contributions (e.g., "Increased production efficiency by 20%" or "Reduced waste by 30% through process improvements").
Focus on Relevant Skills: Emphasize skills pertinent to the industrial sector, such as machine operation, safety practices, and quality control.
Highlight Certifications: Include any relevant certifications (e.g., OSHA, Lean Manufacturing, Six Sigma) to demonstrate compliance with industry standards.
Detail Specific Responsibilities: Explain your day-to-day duties to provide context and show your level of expertise in the field.
Showcase Team Contributions: If you've worked in teams, describe your role in collaboration and how it contributed to team success.
Include Technical Proficiencies: Mention specific tools, machinery, or software that you are proficient in (e.g., CAD software, CNC machinery).
Prioritize Relevant Experience: List your work experience in reverse chronological order and prioritize the most relevant positions related to the industrial sector.
Use Action Verbs: Start bullet points with strong action verbs (e.g., Operated, Maintained, Supervised, Optimized) to convey your active role in your work.
Customize for Each Job: Tailor your experience section to match the job description for each position you apply for, highlighting the most relevant experiences.
Include Soft Skills: Mention soft skills that are important for industrial roles, such as problem-solving, teamwork, communication, and adaptability.
Proofread for Accuracy: Review your work experience section to ensure there are no errors in spelling or grammar, as professionalism is key in industrial roles.
By following these best practices, you can create a compelling work experience section that effectively showcases your qualifications as an industrial worker.
Strong Resume Work Experiences Examples
Resume Work Experience Examples for an Industrial Worker
Manufacturing Associate | ABC Manufacturing Co. | June 2021 - Present
Operated and maintained production machinery, ensuring compliance with safety protocols and quality standards. Collaborated with team members to streamline processes, resulting in a 15% increase in overall efficiency.Material Handler | XYZ Logistics | January 2020 - May 2021
Managed the movement of raw materials and finished products within the facility, utilizing forklifts and pallet jacks. Implemented inventory tracking systems that reduced material loss by 20% and improved order fulfillment times.Quality Control Inspector | DEF Industries | March 2019 - December 2019
Conducted thorough inspections of products at various stages of production, identifying defects and ensuring adherence to specifications. Developed quality improvement strategies that led to a 30% reduction in return rates.
Why This is Strong Work Experience
Quantifiable Achievements: Each example includes specific metrics (e.g., 15% increase in efficiency, 20% reduction in material loss), highlighting the candidate’s direct impact on the organization. This not only demonstrates their effectiveness but also shows potential employers the value they can bring.
Relevant Skills and Responsibilities: The experiences reflect relevant industrial skills, such as machinery operation, inventory management, and quality inspection, which are crucial for industrial positions. This alignment indicates that the candidate is well-prepared for similar roles.
Collaborative and Improvement-Oriented Mindset: The emphasis on collaboration and process improvement illustrates the candidate’s ability to work well in teams and contribute to organizational goals. This trait is essential in industrial environments, where teamwork and efficiency are key to success.
Lead/Super Experienced level
Certainly! Here are five examples of strong resume work experiences for an industrial worker at a lead/super experienced level:
Production Team Leader
Spearheaded a team of 20 operators in a high-volume manufacturing facility, achieving a 15% increase in production efficiency through innovative process improvements and rigorous quality control protocols.Safety Compliance Coordinator
Developed and implemented safety training programs that reduced workplace accidents by 40%, while ensuring compliance with OSHA regulations and fostering a culture of safety among all staff members.Process Optimization Specialist
Led a cross-functional team to identify and eliminate bottlenecks in the production line, resulting in a 25% reduction in cycle time and substantial cost savings for the organization.Inventory Management Supervisor
Managed inventory levels and operational logistics for a 50,000-square-foot warehouse, streamlining supply chain processes and achieving a 98% accuracy rate in order fulfillment.Quality Assurance Manager
Directed quality assurance initiatives by performing comprehensive audits and implementing corrective actions, ultimately increasing product quality ratings and achieving an ISO 9001 certification for the facility.
Senior level
Sure! Here are five examples of strong resume work experience bullet points for an experienced industrial worker:
Managed daily operations in a fast-paced manufacturing environment, leading a team of 15 workers to achieve a 20% increase in productivity while maintaining quality standards and safety protocols.
Implemented lean manufacturing techniques that reduced waste by 30% and improved process efficiency, resulting in a cost savings of $150,000 annually for the organization.
Conducted regular equipment maintenance and troubleshooting, proactively identifying issues that decreased downtime by 25% and ensuring optimal performance of machinery in a high-volume production setting.
Trained and mentored new personnel on safety procedures and operational protocols, fostering a culture of continuous improvement that reduced workplace accidents by 40% over a two-year period.
Collaborated with cross-functional teams to develop and refine production schedules, optimizing resource allocation and enhancing overall workflow efficiency, leading to a 15% improvement in on-time delivery metrics.
Mid-Level level
Manufacturing Technician
Operated and maintained CNC machinery to produce precision components, achieving a 15% increase in production efficiency through meticulous quality control and machine calibration. Collaborated with engineering teams to implement process improvements that reduced downtime by 20%.Assembly Line Supervisor
Led a team of 10 assembly line workers in a high-volume manufacturing environment, ensuring adherence to safety standards and production targets. Streamlined workflows and training programs, resulting in a 30% reduction in onboarding time for new employees.Quality Control Inspector
Conducted rigorous inspections of materials and finished products, utilizing statistical process control techniques to identify and rectify defects, which improved product quality ratings by 25%. Developed and documented inspection processes that enhanced overall compliance with industry regulations.Logistics Coordinator
Managed inventory and shipping processes in a fast-paced warehouse, optimizing stock levels to achieve a 98% order fulfillment rate. Implemented a new inventory tracking system, reducing retrieval times by 40% and minimizing shipment errors.Maintenance Technician
Performed routine maintenance and emergency repairs on industrial equipment, decreasing downtime by 50% through proactive troubleshooting and problem-solving. Led a cross-functional team in a major overhaul project that improved machine reliability and extended equipment lifespan by an average of three years.
Junior level
Sure! Here are five bullet point examples of strong work experiences for a junior-level industrial worker:
Production Line Operative
Assisted in the efficient operation of production machinery, consistently meeting daily output targets while ensuring adherence to safety protocols and quality standards.Warehouse Assistant
Supported inventory management by accurately tracking stock levels and organizing shipments, resulting in a 15% improvement in order fulfillment speed.Quality Control Technician
Conducted routine inspections of finished products to identify defects and maintain quality assurance, contributing to a 10% reduction in return rates.Maintenance Helper
Collaborated with senior technicians in routine equipment maintenance and repairs, learning crucial troubleshooting techniques that enhanced machine uptime by 20%.Construction Laborer
Participated in various construction projects, assisting with material handling and site clean-up, while developing essential skills in teamwork and time management in fast-paced environments.
Entry-Level level
Certainly! Here are five bullet point examples for an entry-level industrial worker's resume, highlighting relevant skills and experiences:
Assembly Line Operations: Assisted in the efficient assembly of products on the production line, adhering to safety protocols and contributing to a 10% increase in output during peak production periods.
Quality Control: Conducted routine quality inspections on finished products, identifying defects and implementing corrective actions, which reduced rework rates by 15%.
Machine Maintenance: Performed basic maintenance and troubleshooting on industrial machinery, ensuring minimal downtime and enhancing overall equipment effectiveness through timely upkeep.
Inventory Management: Assisted in tracking and managing raw materials and supplies, contributing to streamlined operations by maintaining accurate inventory levels and reducing waste.
Team Collaboration: Actively participated in team meetings and training sessions, fostering a collaborative environment that improved workflow and promoted best practices among coworkers.
Weak Resume Work Experiences Examples
Weak Resume Work Experience Examples for Industrial Worker
Position: General Laborer - XYZ Construction Co.
- Assisted with basic tasks such as cleaning work areas and moving supplies.
- Worked on-site for only a few weeks during the summer.
- Received no specialized training or certifications during the time employed.
Position: Warehouse Helper - ABC Logistics
- Contracted for a short-term project, primarily stacking boxes and emptying trash bins.
- Gained no new skills or knowledge relevant to industrial work during the employment period.
- Was not entrusted with any responsibilities beyond basic manual labor.
Position: Farm Hand - Local Farm
- Performed menial tasks like feeding animals and weeding.
- Worked part-time off-season, leading to inconsistencies in work experience.
- No interaction with machinery or use of industry-related tools.
Why These Work Experiences Are Weak
Limited Responsibilities: The roles primarily involved basic or menial tasks with little to no responsibility. This indicates a lack of engagement or capacity to handle more complex industrial duties.
Short Employment Duration: Many of these roles were temporary or short-term contracts. This raises concerns about reliability and commitment, which are critical traits in industrial positions that often require consistency and dedication.
No Skills Development: There was minimal opportunity for skill enhancement or professional growth in these positions. This lack of training and development means the worker cannot demonstrate competencies relevant to the industry's demands, making them less appealing to potential employers.
Lack of Industry-Relevant Experience: None of these positions involved advanced machinery, safety protocols, or industry standards that are essential in many industrial jobs. Without this experience, the worker may find it difficult to meet the requirements of future roles or show how they can add value to potential employers.
Top Skills & Keywords for Assembly Line Technician Resumes:
When crafting a resume for an industrial worker, emphasize relevant skills and keywords that highlight your capabilities. Include technical skills such as machinery operation, basic troubleshooting, and safety procedures. Mention certifications like OSHA training or forklift operation. Highlight soft skills such as teamwork, communication, and problem-solving. Keywords like "assembly line efficiency," "preventive maintenance," "quality control," and "inventory management" are crucial. Focus on experience related to specific industries, such as manufacturing, warehousing, or construction. Additionally, include any specific software familiarity, such as ERP systems. Tailor your resume to align with the job description for maximum impact.
Top Hard & Soft Skills for Assembly Line Technician:
Hard Skills
Sure! Here’s a table with 10 hard skills relevant for industrial workers, complete with descriptions and formatted links:
Hard Skills | Description |
---|---|
Machinery Operation | The ability to operate and manage various types of industrial machinery effectively and safely. |
Welding | The skill of joining metal parts together using different welding techniques, such as MIG, TIG, or arc welding. |
Quality Control | The process of ensuring products meet required specifications and standards through inspections and testing. |
Blueprint Reading | The capability to interpret technical drawings and schematics to understand how to assemble or manufacture products. |
Safety Regulations | Knowledge of workplace safety practices and regulations to ensure a safe working environment for all employees. |
Maintenance and Repair | The skill involved in performing regular maintenance and necessary repairs on machines and equipment. |
Industrial Electronics | Understanding of electronic systems used in industrial applications, including circuits and control systems. |
Material Handling | The ability to manage and move materials using forklifts, hoists, and other equipment safely and efficiently. |
Automation Systems | Knowledge of automated systems and robotics used in manufacturing and production processes. |
Technical Drawing | The skill of creating accurate and detailed drawings that convey how parts and assemblies should be constructed. |
Feel free to modify any details as needed!
Soft Skills
Here's a table with 10 soft skills relevant for industrial workers, including a description for each skill and the requested hyperlink format:
Soft Skills | Description |
---|---|
Communication | The ability to clearly and effectively convey information, both verbally and in writing, to ensure understanding among team members. |
Teamwork | Working collaboratively with others towards a common goal, fostering a supportive and cooperative work environment. |
Adaptability | The capability to adjust to new conditions and challenges, demonstrating flexibility in thought and action. |
Problem Solving | The ability to identify issues, analyze situations, and develop effective solutions to overcome obstacles. |
Time Management | Organizing and prioritizing tasks efficiently to meet deadlines and improve productivity. |
Attention to Detail | Being meticulous and thorough in one's work to ensure accuracy and quality in all tasks undertaken. |
Leadership | The ability to guide, motivate, and support others, fostering a sense of direction and collaboration within a team. |
Critical Thinking | The skill to analyze information logically and make reasoned decisions, enabling effective evaluations of situations and options. |
Flexibility | Willingness to take on a variety of tasks and roles, demonstrating versatility in the face of changing circumstances. |
Conflict Resolution | The ability to handle disagreements constructively, finding amicable solutions that satisfy all parties involved. |
This table summarizes valuable soft skills for industrial workers, essential for fostering a productive and harmonious work environment.
Elevate Your Application: Crafting an Exceptional Assembly Line Technician Cover Letter
Assembly Line Technician Cover Letter Example: Based on Resume
Dear [Company Name] Hiring Manager,
I am writing to express my enthusiasm for the Industrial Worker position at [Company Name], as advertised. With a robust background in industrial operations and a passion for driving efficiency, I am excited about the opportunity to contribute my skills and expertise to your esteemed team.
Over the past five years, I have honed my technical knowledge and practical skills while working in various industrial settings. My experience includes operating complex machinery, conducting quality inspections, and implementing safety protocols that have reduced workplace incidents by 30% in my previous role at [Previous Company Name]. I excel in utilizing industry-standard software such as AutoCAD and SAP, which have enabled me to streamline processes, enhance productivity, and minimize downtime.
Collaboration is at the core of my work ethic. I thrive in team environments where communication and cooperation are essential for achieving operational goals. During my tenure at [Another Previous Company Name], I led a project that involved cross-departmental collaboration, resulting in a 25% increase in production efficiency. My commitment to fostering a positive team dynamic and mentoring junior workers has significantly contributed to raising overall morale and output.
I am particularly drawn to [Company Name] due to your commitment to innovation and sustainability in the industrial sector. I am eager to bring my expertise in process optimization and my proactive approach to problem-solving to your team, helping [Company Name] maintain its standards of excellence and industry leadership.
Thank you for considering my application. I look forward to the possibility of discussing how my experience, passion, and measurable achievements align with the goals of your organization.
Best regards,
[Your Name]
[Your Phone Number]
[Your Email Address]
A cover letter for an industrial worker position should effectively convey your skills, experience, and enthusiasm for the role while addressing the specific requirements of the job. Here’s a guide to crafting an impactful cover letter:
Header: Start with your contact information, followed by the date, and then the employer's contact details. If you're emailing your application, this can be omitted.
Salutation: Address the letter to a specific person whenever possible. If you cannot find a name, a general greeting like "Dear Hiring Manager" is acceptable.
Introduction: Begin with a strong opening statement that clearly states the position you are applying for and where you found the job listing. Express genuine interest in the company and the role, mentioning any connection you may have to the organization.
Body Paragraph(s):
- Relevant Experience: Highlight your previous experience in industrial or manufacturing roles. Discuss specific skills such as machine operation, safety protocols, or team collaboration that are directly relevant to the job. Use quantifiable achievements (e.g., "improved production efficiency by 15%") to demonstrate your impact.
- Skills and Qualifications: Address any specific qualifications listed in the job description. Examples include familiarity with particular tools or technologies, certifications (like OSHA), or physical capabilities (such as lifting heavy materials).
- Soft Skills: Emphasize soft skills such as teamwork, problem-solving, and reliability. These are crucial in industrial settings where collaboration is key.
Conclusion: Reiterate your enthusiasm for the position and briefly mention what you can bring to the team. Thank the employer for considering your application.
Closing: Use a professional closing, such as “Sincerely,” followed by your name.
Final Tips:
- Keep the letter to one page, ideally around 250-350 words.
- Tailor each cover letter to the specific job and company.
- Use a professional tone but let your personality shine through.
By following these guidelines, you can create a compelling cover letter that enhances your application for an industrial worker position.
Resume FAQs for Assembly Line Technician:
How long should I make my Assembly Line Technician resume?
When crafting a resume for an industrial worker position, it’s essential to strike the right balance in length and content. Typically, an effective industrial worker resume should be one page, especially if you have fewer than 10 years of experience. This concise format allows you to highlight your skills, relevant experience, and qualifications without overwhelming potential employers.
For those with extensive experience or specialized skills, a two-page resume may be warranted. However, ensure that each section contributes value; irrelevant information can dilute the impact of your qualifications. Tailor your resume to the specific industrial role you're applying for, emphasizing pertinent experience, certifications, and skills such as machinery operation, safety protocols, and teamwork.
Utilize bullet points for clarity and focus on quantifiable achievements, such as productivity improvements or successful project completions. Additionally, use industry-specific terminology to demonstrate familiarity with the field.
Ultimately, remember that hiring managers often spend just seconds scanning resumes, so clear, concise, and relevant information is key. Aim for maximum impact within your chosen length, ensuring your resume effectively showcases your capabilities and makes a strong impression.
What is the best way to format a Assembly Line Technician resume?
When formatting a resume for an industrial worker, it's crucial to emphasize relevant skills, experience, and certifications in a clear and organized manner. Start with a professional header that includes your name, phone number, and email address.
Follow this with a concise objective statement that highlights your career goals and what you bring to the table. Next, create a section titled "Skills" to showcase relevant abilities such as machinery operation, safety protocols, problem-solving, and teamwork. Use bullet points for easy readability.
The work experience section should be the focal point, listing past employment in reverse chronological order. Include job titles, company names, locations, and dates of employment. For each role, provide bullet points detailing your responsibilities and achievements, quantifying results when possible (e.g., “Increased efficiency by 20%”).
If applicable, add an "Education" section that outlines your qualifications, including relevant courses or certifications like OSHA, forklift operation, or specialized technical training.
Finally, consider including any industry-specific certifications or training programs in a separate section. Keep the format clean with consistent fonts and spacing, using headers and bullet points to enhance readability while ensuring the resume fits on one page.
Which Assembly Line Technician skills are most important to highlight in a resume?
When crafting a resume for an industrial-worker position, it’s essential to highlight skills that demonstrate technical proficiency, safety awareness, and the ability to work effectively in a team.
Technical Skills: Showcase your expertise in operating machinery, understanding blueprints, and utilizing tools relevant to specific industries. Proficiency in automation technologies and computer-aided design (CAD) software can also enhance your employability.
Safety Awareness: Highlight your knowledge of safety regulations and best practices, such as OSHA standards. Certification in safety training or first aid can be advantageous.
Problem-Solving Skills: Indicate your ability to troubleshoot equipment issues and implement effective solutions, proving your resourcefulness in a fast-paced environment.
Teamwork and Communication: Emphasize your experience in collaborating with colleagues and communicating effectively, as these are critical in a team-oriented industrial setting.
Attention to Detail: Stress your meticulous approach to tasks, ensuring quality control and adherence to specifications.
Physical Endurance: Mention any relevant experience that demonstrates your capability to perform physically demanding tasks, as this is often a key requirement in industrial roles.
By prioritizing these skills in your resume, you can effectively convey your suitability for a position in the industrial sector.
How should you write a resume if you have no experience as a Assembly Line Technician?
Writing a resume without industrial experience can be challenging, but it’s an opportunity to showcase your transferable skills, education, and any relevant training. Here’s how to approach it:
Contact Information: Start with your name, phone number, email address, and LinkedIn profile (if applicable).
Objective Statement: Write a brief statement highlighting your interest in industrial work and your eagerness to learn. Tailor it to the specific job.
Education: List your educational qualifications. If you’ve taken courses related to manufacturing, engineering, or safety, include them.
Skills Section: Emphasize relevant skills such as problem-solving, teamwork, attention to detail, and technical skills. If you have experience with tools or machinery, highlight that.
Relevant Experience: Include internships, volunteer work, or part-time jobs, especially those requiring teamwork or physical work. Describe your responsibilities and achievements briefly.
Certifications: If you have any certifications related to safety, machinery operation, or other relevant areas, list them.
Tailored Formatting: Use clear headings and bullet points for easy readability. Keep it concise, ideally one page.
Remember, focus on your eagerness to learn and adapt, which is often a key trait valued in entry-level industrial positions.
Professional Development Resources Tips for Assembly Line Technician:
null
TOP 20 Assembly Line Technician relevant keywords for ATS (Applicant Tracking System) systems:
Certainly! Below is a table of 20 relevant keywords that you can use in your resume to help it pass through Applicant Tracking Systems (ATS), along with brief descriptions of each term:
Keywords | Description |
---|---|
Safety Compliance | Knowledge of and adherence to workplace safety regulations and standards. |
Quality Assurance | Experience in maintaining product quality and ensuring compliance with quality standards. |
Equipment Operation | Proficiency in operating industrial machinery and tools. |
Process Improvement | Skills in identifying and implementing efficient processes to enhance productivity. |
Team Collaboration | Experience working effectively within a team to achieve common goals. |
Lean Manufacturing | Familiarity with lean principles to reduce waste and improve efficiency in production. |
Forklift Certified | Certification in operating forklifts and handling material safely. |
Inventory Management | Skills in managing stock levels and using inventory tracking systems. |
Troubleshooting | Ability to identify, diagnose, and solve problems that arise during production. |
Preventive Maintenance | Knowledge of maintenance practices to prevent equipment failure and increase reliability. |
Time Management | Skills in managing time efficiently to meet production deadlines. |
Technical Skills | Proficiency with specific tools, technologies, or software relevant to the industrial field. |
Production Planning | Ability to assist in planning production schedules and ensuring timely delivery of products. |
Regulatory Compliance | Understanding of legal regulations governing industrial operations and ensuring adherence. |
Blueprint Reading | Skill in reading and interpreting technical drawings and blueprints. |
Performance Metrics | Knowledge of tracking and analyzing performance data for continuous improvement. |
Shift Flexibility | Willingness to work varied shifts or overtime as needed for operational demands. |
Work Station Setup | Skills in efficiently setting up workstations to optimize workflow and productivity. |
Data Entry | Proficiency in inputting and managing data related to production processes or inventory. |
Physical Stamina | Ability to perform physically demanding tasks required in industrial environments. |
Using these keywords and phrases throughout your resume can enhance its effectiveness in passing through ATS filters. Make sure to tailor them to your specific experience and the job description you are applying for. Good luck with your job applications!
Sample Interview Preparation Questions:
Can you describe your previous experience in an industrial setting and the types of machinery you have worked with?
How do you prioritize safety in your daily tasks, and can you provide an example of a safety procedure you follow?
What strategies do you use to troubleshoot and resolve equipment malfunctions on the job?
How do you handle working in a team environment, especially under high-pressure situations or tight deadlines?
Can you explain your understanding of quality control processes and how they are applied in an industrial workplace?
Related Resumes for Assembly Line Technician:
Generate Your NEXT Resume with AI
Accelerate your resume crafting with the AI Resume Builder. Create personalized resume summaries in seconds.