Lean Process Improvement Specialist Resume Examples for 2024 Success
---
**Sample 1**
- **Position number:** 1
- **Person:** 1
- **Position title:** Lean Manufacturing Engineer
- **Position slug:** lean-manufacturing-engineer
- **Name:** John
- **Surname:** Smith
- **Birthdate:** January 15, 1985
- **List of 5 companies:** Toyota, GE Aviation, Ford, Boeing, Honeywell
- **Key competencies:** Lean Six Sigma, Process Mapping, Value Stream Mapping, Kaizen Events, Root Cause Analysis
---
**Sample 2**
- **Position number:** 2
- **Person:** 2
- **Position title:** Continuous Improvement Coordinator
- **Position slug:** continuous-improvement-coordinator
- **Name:** Emily
- **Surname:** Johnson
- **Birthdate:** March 22, 1990
- **List of 5 companies:** Procter & Gamble, PepsiCo, Johnson & Johnson, Kraft Heinz, Coca Cola
- **Key competencies:** Project Management, Lean Tool Implementation, Team Leadership, Performance Metrics Analysis, Training Facilitation
---
**Sample 3**
- **Position number:** 3
- **Person:** 3
- **Position title:** Process Improvement Analyst
- **Position slug:** process-improvement-analyst
- **Name:** Michael
- **Surname:** Williams
- **Birthdate:** July 8, 1983
- **List of 5 companies:** IBM, Amazon, Intel, Siemens, Verizon
- **Key competencies:** Data Analysis, Operations Optimization, Efficiency Strategies, Workflow Design, Stakeholder Engagement
---
**Sample 4**
- **Position number:** 4
- **Person:** 4
- **Position title:** Six Sigma Quality Consultant
- **Position slug:** six-sigma-quality-consultant
- **Name:** Sarah
- **Surname:** Brown
- **Birthdate:** February 18, 1992
- **List of 5 companies:** Boeing, Siemens, DHL, UPS, Abbott Laboratories
- **Key competencies:** Quality Assurance, Statistical Process Control, Training & Mentoring, Problem Solving, Business Process Reengineering
---
**Sample 5**
- **Position number:** 5
- **Person:** 5
- **Position title:** Business Process Engineer
- **Position slug:** business-process-engineer
- **Name:** David
- **Surname:** Taylor
- **Birthdate:** June 5, 1988
- **List of 5 companies:** Deloitte, Accenture, Capgemini, McKinsey & Company, PwC
- **Key competencies:** Systems Thinking, Business Process Mapping, Change Management, Cost-Benefit Analysis, Cross-functional Collaboration
---
**Sample 6**
- **Position number:** 6
- **Person:** 6
- **Position title:** Operational Excellence Manager
- **Position slug:** operational-excellence-manager
- **Name:** Jessica
- **Surname:** Miller
- **Birthdate:** September 12, 1980
- **List of 5 companies:** Oracle, Nestle, Hewlett Packard, 3M, L'Oreal
- **Key competencies:** Change Leadership, Lean Methodologies, Performance Improvement, Strategic Planning, Employee Engagement
---
These samples outline different individuals aiming for distinct sub-positions related to lean process improvement, showcasing their competencies and experience.
Lean Process Improvement Specialist: 6 Resume Examples for Success
We are seeking a dynamic Lean Process Improvement Specialist with a proven track record of leading successful initiatives that streamline operations and enhance productivity. The ideal candidate has demonstrated accomplishments in reducing waste and increasing efficiency across diverse teams, fostering a collaborative environment that encourages innovation and continuous improvement. With exceptional technical expertise in Lean methodologies, they will conduct training sessions to empower staff at all levels, ensuring sustainable change. Their ability to analyze complex processes and implement effective solutions has resulted in significant cost savings and improved service delivery, making a measurable impact on organizational performance.
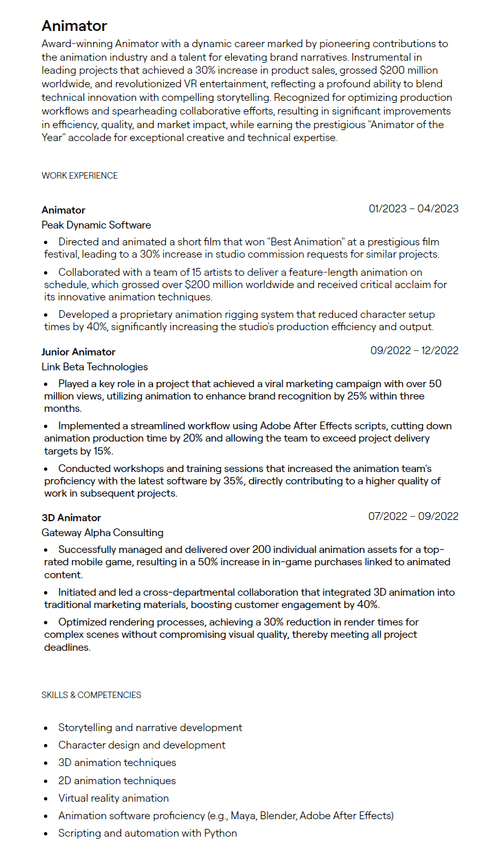
Certainly! Here are 10 common responsibilities often listed on resumes for Lean Process Improvement Specialists:
Conducting Process Assessments: Evaluating existing business processes to identify inefficiencies and areas for improvement using Lean methodologies.
Facilitating Kaizen Events: Organizing and leading continuous improvement workshops aimed at identifying and implementing process enhancements.
Developing Process Maps: Creating detailed process flow diagrams to visualize workflows and highlight bottlenecks or redundancies.
Training Employees: Delivering training sessions and workshops on Lean principles and tools to promote a culture of continuous improvement across the organization.
Implementing Improvement Strategies: Designing and deploying Lean initiatives that reduce waste, enhance quality, and increase overall operational effectiveness.
Monitoring Key Performance Indicators (KPIs): Establishing and tracking metrics to measure the impact of process improvements and ensure alignment with organizational goals.
Collaborating with Cross-Functional Teams: Working closely with various departments to gather data, share insights, and implement process improvement strategies.
Conducting Root Cause Analyses: Analyzing issues and defects in processes to identify root causes and develop targeted corrective actions.
Creating Standard Operating Procedures (SOPs): Developing and documenting best practices to ensure consistency and effectiveness in operations.
Reporting and Presenting Findings: Compiling data and insights into reports and presentations for stakeholders to communicate progress and outcomes of improvement initiatives.
These points reflect the key duties and skills that Lean Process Improvement Specialists typically engage in within various organizations.
Results-driven Lean Manufacturing Engineer, John Smith, boasts extensive expertise in Lean Six Sigma methodologies and process improvement within prominent organizations such as Toyota and Boeing. With a proven track record in implementing process mapping, value stream mapping, and facilitating Kaizen events, he excels at identifying inefficiencies and driving innovative solutions. His strong analytical skills enable effective root cause analysis, ensuring sustainable improvements and enhanced operational efficiency. Committed to fostering a culture of continuous improvement, John is adept at collaborating cross-functionally to elevate organizational performance and deliver significant cost savings.
WORK EXPERIENCE
SKILLS & COMPETENCIES
COURSES / CERTIFICATIONS
EDUCATION
WORK EXPERIENCE
SKILLS & COMPETENCIES
COURSES / CERTIFICATIONS
EDUCATION
Bachelor of Science in Industrial Engineering
University of Michigan, Ann Arbor, MI
Graduated: May 2012Master of Business Administration (MBA)
Harvard Business School, Cambridge, MA
Graduated: May 2016
Michael Williams is an accomplished Process Improvement Analyst with a proven track record in data analysis and operations optimization across leading technology companies such as IBM and Amazon. Born on July 8, 1983, he specializes in developing efficiency strategies and workflow designs that enhance productivity and stakeholder engagement. His analytical skills and strategic approach empower organizations to streamline processes and achieve operational excellence. Michael’s dedication to continuous improvement positions him as a vital asset for any organization seeking to elevate their performance and drive sustainable growth.
WORK EXPERIENCE
- Led a cross-functional team that identified and eliminated bottlenecks resulting in a 30% increase in operational efficiency.
- Implemented data-driven strategies that optimized workflows, reducing processing time by 25%.
- Developed and presented comprehensive performance reports to senior management, facilitating informed decision-making.
- Conducted training sessions on Lean methodologies, enhancing team capabilities and improving project outcomes.
- Collaborated with stakeholders to redesign service processes, significantly enhancing customer satisfaction ratings.
- Utilized advanced data analytics to assess operational performance, identifying key areas for improvement that led to a 35% cost reduction.
- Spearheaded the implementation of continuous improvement initiatives, driving a culture of efficiency across multiple departments.
- Designed and executed training programs for new tools and processes, resulting in a 20% increase in employee productivity.
- Facilitated workshops with teams to promote engagement in problem-solving and process innovation.
- Recognized for outstanding contributions to team projects with an annual excellence award for driving profitability.
- Developing comprehensive efficiency frameworks that streamline operations and reduce waste across global supply chains.
- Leading strategic initiatives that enhance product delivery timelines and inventory accuracy, improving fulfillment metrics by 40%.
- Utilizing performance metrics to analyze and refine operational processes, fostering continuous growth and improvement.
- Engaging with global stakeholders to ensure alignment on process improvement objectives and maintaining high standards of quality.
- Recognized as a key contributor to achieving the company's sustainability goals through innovative process reengineering.
SKILLS & COMPETENCIES
Sure! Here are 10 skills for Michael Williams, the Process Improvement Analyst:
- Data Analysis
- Operations Optimization
- Efficiency Strategies
- Workflow Design
- Stakeholder Engagement
- Process Documentation
- Problem-Solving Techniques
- Change Management
- Performance Metrics Development
- Cross-Functional Collaboration
COURSES / CERTIFICATIONS
Here’s a list of 5 certifications and completed courses for Michael Williams, the Process Improvement Analyst:
Lean Six Sigma Green Belt Certification
- Date: March 2021
Certified ScrumMaster (CSM)
- Date: June 2019
Data Analysis and Visualization with Excel
- Date: January 2020
Project Management Professional (PMP)
- Date: August 2022
Business Process Management (BPM) Certification
- Date: November 2020
EDUCATION
Bachelor of Science in Industrial Engineering
University: University of Michigan
Graduation Date: May 2005Master of Business Administration (MBA)
University: Harvard University
Graduation Date: May 2010
When crafting a resume for the Six Sigma Quality Consultant role, it’s crucial to emphasize expertise in quality assurance and statistical process control, showcasing experience with Six Sigma methodologies. Highlight measurable achievements in process improvements, including successful training and mentoring efforts. Detail problem-solving abilities and instances of business process reengineering that led to enhanced efficiency. Mention collaborations with cross-functional teams and engagement in real-world projects within respected companies. Also, underscore any relevant certifications and the ability to effectively communicate complex concepts, which will demonstrate both technical proficiency and interpersonal skills essential for consultant roles.
[email protected] • (555) 123-4567 • https://www.linkedin.com/in/sarahbrown • https://twitter.com/sarahbrown
WORK EXPERIENCE
SKILLS & COMPETENCIES
Skills for Sarah Brown - Six Sigma Quality Consultant:
- Six Sigma Methodology
- Quality Assurance Techniques
- Statistical Process Control (SPC)
- Root Cause Analysis
- Training and Mentoring
- Business Process Reengineering
- Problem Solving Skills
- Data Interpretation and Analysis
- Continuous Improvement Practices
- Cross-functional Team Collaboration
COURSES / CERTIFICATIONS
Here is a list of 5 certifications and completed courses for Sarah Brown, the Six Sigma Quality Consultant:
Certified Six Sigma Green Belt (CSSGB)
- Date: March 2015
Lean Six Sigma Black Belt Certification
- Date: October 2016
Statistical Process Control Training
- Date: January 2018
Root Cause Analysis and Problem Solving Techniques
- Date: July 2019
Business Process Reengineering Course
- Date: November 2020
EDUCATION
Master of Science in Quality Assurance
University of Southern California, 2015Bachelor of Science in Industrial Engineering
Georgia Institute of Technology, 2010
[email protected] • (555) 123-4567 • https://www.linkedin.com/in/davidtaylor • https://twitter.com/david_taylor
David Taylor is a results-driven Business Process Engineer with extensive experience in top-tier consulting firms such as Deloitte and Accenture. He excels in systems thinking and business process mapping, leveraging a keen analytical mindset for effective change management and cost-benefit analysis. With a proven track record in cross-functional collaboration, David is adept at optimizing workflows to enhance operational efficiency. His strategic approach ensures the alignment of process improvements with organizational goals, making him a valuable asset for any organization seeking to streamline operations and drive performance enhancements.
WORK EXPERIENCE
SKILLS & COMPETENCIES
Here are 10 skills for David Taylor, the Business Process Engineer:
- Business Process Mapping
- Systems Thinking
- Change Management
- Cost-Benefit Analysis
- Cross-functional Collaboration
- Stakeholder Communication
- Performance Metrics Development
- Risk Assessment and Mitigation
- Process Automation
- Continuous Improvement Methodologies
COURSES / CERTIFICATIONS
EDUCATION
When crafting a resume for an Operational Excellence Manager, it's crucial to emphasize leadership in change management and strategic planning. Highlight experience in implementing lean methodologies that drive performance improvement and enhance operational efficiency. Focus on competencies in employee engagement and communication, demonstrating the ability to foster a culture of continuous improvement. Showcase past achievements, including quantifiable results from projects that led to significant cost savings or process optimization. Include relevant certifications, such as Lean Six Sigma, and illustrate cross-functional collaboration skills to convey versatility in working with diverse teams across an organization.
[email protected] • (555) 123-4567 • https://www.linkedin.com/in/jessica-miller-lean-excellence/ • https://twitter.com/JessicaMillerLE
WORK EXPERIENCE
- Led cross-functional initiatives that increased operational efficiency by 30% and reduced costs by $1.2 million annually.
- Implemented Lean methodologies across multiple departments, achieving a 25% reduction in cycle time and improving customer satisfaction ratings.
- Facilitated team workshops that fostered a culture of continuous improvement, resulting in a 40% increase in employee engagement scores.
- Developed and executed strategic plans that drove performance improvements and streamlined processes, contributing to a 15% increase in revenue year-over-year.
- Mentored and trained over 100 employees in Lean principles and operational excellence, empowering teams to identify and execute improvement projects independently.
- Conducted value stream mapping sessions that identified key areas for process enhancement, improving lead times by 20%.
- Managed multiple Lean projects simultaneously, providing oversight and strategic guidance that led to measurable results in efficiency and quality.
- Collaborated with supplier partners to implement quality improvement initiatives, reducing defects by 18% and enhancing supplier performance.
- Created and standardized operational procedures that improved workflow consistency and compliance, leading to a 10% decrease in operational errors.
- Drove Kaizen events that successfully engaged employees at all levels, fostering a shared vision for process excellence and innovation.
- Established a quality improvement program centered around data-driven decision making, achieving a 22% reduction in product returns.
- Conducted root cause analysis for quality control issues, implementing corrective measures that led to a 15% increase in manufacturing yield.
- Collaborated with R&D and production teams to integrate quality metrics into the product development lifecycle, enhancing product reliability.
- Presented quarterly results to senior management, effectively communicating project achievements through data visualization and storytelling.
- Developed training materials and conducted workshops on quality assurance practices, improving team capabilities and knowledge of quality standards.
- Delivered consultancy to various clients, helping them implement process improvements that resulted in cost savings of up to $600,000 annually.
- Utilized Six Sigma tools for process analysis, achieving significant improvement in client satisfaction metrics and service delivery timelines.
- Conducted comprehensive process assessments and designed tailored improvement plans that aligned with clients' strategic goals.
- Facilitated client workshops to foster collaboration and innovation, leading to the generation of over 50 improvement ideas that were executed towards operational excellence.
- Awarded 'Consultant of the Year' for exemplary service and delivering outstanding results across client projects.
SKILLS & COMPETENCIES
Here are 10 skills for Jessica Miller, the Operational Excellence Manager:
- Change Leadership
- Lean Methodologies
- Performance Improvement
- Strategic Planning
- Employee Engagement
- Project Management
- Process Optimization
- Data-Driven Decision Making
- Cross-Functional Team Collaboration
- Risk Management
COURSES / CERTIFICATIONS
EDUCATION
Generate Your Resume Summary with AI
Accelerate your resume crafting with the AI Resume Builder. Create personalized resume summaries in seconds.
Lean Process Improvement Specialist Resume Headline Examples:
Strong Resume Headline Examples
Weak Resume Headline Examples
Crafting an Outstanding Lean Process Improvement Specialist Resume Summary:
Crafting an exceptional resume summary is crucial for any Lean Process Improvement Specialist, as it is the first impression potential employers will have of you. This brief yet impactful section should encapsulate your professional experience, technical skills, and storytelling abilities. A well-crafted summary not only highlights your unique talents and collaborative skills but also your keen attention to detail, all tailored to the specific role you are pursuing. Here are key points to include in your summary to ensure it stands out:
Years of Experience: Clearly state how many years you have worked in process improvement, specifying any relevant certifications (e.g., Six Sigma, Lean Management) to assert your qualifications.
Specialized Industries: Mention any particular industries you have contributed to (e.g., manufacturing, healthcare, or IT), showcasing your versatility and understanding of sector-specific needs.
Technical Expertise: Highlight proficiency with relevant software tools, such as Lean Six Sigma tools, data analysis software (e.g., Minitab), or project management applications (e.g., Microsoft Project).
Collaboration and Communication Skills: Emphasize your ability to work within cross-functional teams, lead workshops, and communicate complex ideas clearly, demonstrating how you foster collaboration to achieve process improvements.
Attention to Detail: Illustrate your meticulous nature, providing examples of how your analytical mindset has led to identifying inefficiencies and implementing successful solutions.
By integrating these elements into your summary, you will present a compelling introduction that effectively captures your expertise and aligns with the position you are targeting. Tailoring your summary is key to attracting the attention of hiring managers and setting the stage for a successful application.
Lean Process Improvement Specialist Resume Summary Examples:
Strong Resume Summary Examples
Lead/Super Experienced level
Here are five strong bullet points for a resume summary tailored for a lead/super experienced Lean Process Improvement Specialist:
Proven Track Record of Transformation: Over 15 years of experience driving operational excellence and process optimization in diverse industries, resulting in an average of 30% reduction in cycle times and significant cost savings.
Expert in Lean Methodologies: Certified Lean Six Sigma Master Black Belt, adept at deploying Lean principles and tools such as Kaizen, Value Stream Mapping, and 5S to enhance productivity and foster a culture of continuous improvement.
Strategic Leadership: Demonstrated ability to lead cross-functional teams in the execution of large-scale process improvement initiatives, achieving organizational goals through effective stakeholder engagement and change management strategies.
Data-Driven Decision Maker: Proficient in utilizing data analytics and performance metrics to identify inefficiencies, streamline processes, and implement sustainable improvements that enhance operational performance and customer satisfaction.
Transformational Change Agent: Recognized for spearheading successful Lean transformations and skillfully mentoring teams on Lean practices, cultivating a mindset of innovation that empowers employees and drives collaborative solutions.
Senior level
Sure! Here are five bullet points for a strong resume summary tailored for a Senior Lean Process Improvement Specialist:
Proven track record of enhancing operational efficiency by leveraging Lean Six Sigma methodologies, resulting in a 30% reduction in cycle times and significant cost savings for multiple projects across various industries.
Extensive experience in leading cross-functional teams to implement process improvements that streamline workflows, reduce waste, and drive a culture of continuous improvement within the organization.
Expert in data analysis and root cause identification, utilizing advanced problem-solving techniques to diagnose process inefficiencies and develop targeted solutions that align with strategic business objectives.
Strong communication and leadership skills, adept at facilitating training sessions and workshops to empower staff at all levels in Lean principles, fostering an environment of collaboration and innovation.
Exceptional project management capabilities, successfully overseeing multiple process improvement initiatives from conception through execution, ensuring alignment with organizational goals and adherence to timelines and budgets.
Mid-Level level
Here are five strong resume summary examples for a lean process improvement specialist at a mid-level experience level:
Results-Driven Lean Practitioner: Certified Lean Six Sigma Green Belt with over 5 years of experience in optimizing operational processes and enhancing efficiency across diverse industries. Proven track record of implementing strategic improvements that reduce waste and increase productivity.
Strategic Process Improvement Analyst: Mid-level professional with 6 years of expertise in identifying process bottlenecks and streamlining workflows, leading to a 20% reduction in operational costs. Adept at utilizing data-driven approaches to drive continuous improvement initiatives and foster a culture of excellence.
Cross-Functional Collaboration Expert: Experienced lean process improvement specialist skilled in collaborating with cross-functional teams to deliver coordinated solutions and achieve organizational goals. Effective in training staff on lean methodologies to cultivate a sustainable improvement mindset.
Operational Efficiency Champion: Accomplished process improvement specialist with a focus on utilizing Lean and Six Sigma methodologies to achieve measurable improvements. Successfully facilitated Kaizen events that resulted in enhanced quality control measures and increased customer satisfaction scores.
Data-Driven Improvement Advocate: Mid-level lean process improvement specialist with a strong analytical background, dedicated to leveraging data analytics to drive informed decision-making. Recognized for developing comprehensive training programs that empower teams to adopt lean principles and achieve outstanding results.
Junior level
Sure! Here are five bullet point examples of strong resume summaries for a junior-level Lean Process Improvement Specialist:
Results-Oriented Problem Solver: Passionate about optimizing processes and enhancing efficiency, with hands-on experience in applying Lean principles to reduce waste and streamline operations in diverse environments.
Analytical Thinker: Proficient in conducting process mapping and data analysis, capable of identifying areas for improvement and supporting teams in the implementation of Lean methodologies to achieve measurable results.
Collaborative Team Player: Strong communicator who thrives in team settings, committed to fostering a culture of continuous improvement and engaging stakeholders to drive successful Lean initiatives.
Eager Learner: Actively pursuing knowledge in Lean Six Sigma practices, with practical experience in supporting projects that improve quality and reduce cycle times, contributing to overall operational excellence.
Adaptable and Detail-Oriented: Adept at managing multiple tasks simultaneously while maintaining a focus on quality and efficiency, leveraging critical thinking skills to implement solutions that enhance productivity.
Entry-Level level
Entry-Level Lean Process Improvement Specialist Summary
Motivated Recent Graduate: Highly driven recent graduate with a degree in Industrial Engineering, passionate about applying lean principles to enhance operational efficiency and eliminate waste in various processes.
Solid Understanding of Lean Methodologies: Knowledgeable in lean tools such as 5S, Value Stream Mapping, and Kaizen, gained through hands-on projects and academic coursework focused on process optimization.
Analytical Thinker: Strong analytical and critical thinking skills, capable of assessing workflows and identifying areas for improvement to increase productivity and quality in organizational processes.
Team Player with Communication Skills: Excellent interpersonal and communication abilities, eager to collaborate with multidisciplinary teams to promote a culture of continuous improvement and drive change effectively.
Results-Oriented Attitude: Committed to achieving measurable outcomes, with a proven track record of successfully contributing to process improvement initiatives during internships and volunteer activities.
Experienced Lean Process Improvement Specialist Summary
Seasoned Lean Expert: Accomplished Lean Process Improvement Specialist with over 5 years of experience in implementing lean manufacturing principles, driving operational excellence, and achieving significant cost savings for mid- to large-sized organizations.
Proven Track Record of Success: Expertise in leading cross-functional teams in successful lean transformations, resulting in a 20% reduction in cycle times and a 30% decrease in operational costs across multiple projects.
Data-Driven Decision Maker: Strong ability to utilize data analysis and statistical methods to identify inefficiencies and implement sustainable solutions, improving overall process performance and customer satisfaction.
Certified Lean Six Sigma Practitioner: Certified Lean Six Sigma Green Belt, adept at using DMAIC methodology to instill a culture of continuous improvement and empower teams to contribute to process excellence.
Strategic Change Leader: Experienced in change management and training, effectively guiding staff through process changes and fostering a proactive mindset towards ongoing improvement initiatives.
Weak Resume Summary Examples
Weak Resume Summary Examples for Lean Process Improvement Specialist
"Experienced specialist in process improvement looking for a new job. I have knowledge of various methodologies."
"I am a Lean Process Improvement Specialist with some skills in analyzing processes. I want to help companies improve."
"Detail-oriented individual interested in applying Lean principles in a challenging environment."
Why These Are Weak Headlines
Lack of Specificity: These summaries do not provide specific details or measurable achievements that demonstrate the candidate's expertise. Without quantifiable outcomes or concrete examples of past successes, hiring managers may overlook the candidate's potential contributions.
Generic Language: Phrases like "looking for a new job," "have knowledge of," or "want to help" are vague and non-committal. They fail to showcase the unique value that the individual can bring to an organization, making them blend in with other applicants rather than stand out.
Insufficient Focus on Skills and Impact: The summaries do not effectively highlight key skills or the impact of the candidate's work. They should emphasize specific methodologies used (e.g., Six Sigma, Kaizen) and the results achieved (e.g., cost reduction percentages, time savings) to convey the candidate's capability and effectiveness in driving process improvements.
Resume Objective Examples for Lean Process Improvement Specialist:
Strong Resume Objective Examples
Results-oriented Lean Process Improvement Specialist with over 5 years of experience in analyzing workflows and implementing efficiency-enhancing strategies, aiming to leverage expertise at [Company Name] to streamline operations and reduce waste.
Dedicated Lean Process Improvement Specialist skilled in Six Sigma methodologies, seeking to contribute a proven track record of successful project management and team collaboration to enhance productivity and drive continuous improvement at [Company Name].
Detail-focused Lean Process Improvement Specialist passionate about fostering a culture of excellence and sustainability, looking to utilize proven analytical skills to support [Company Name] in achieving operational goals and enhancing customer satisfaction.
Why this is a strong objective:
These objectives are strong because they clearly define the candidate’s role, relevant experience, and specific skills that relate directly to the job they are applying for. Each objective highlights their commitment to continuous improvement and operational efficiency, making them an attractive candidate for employers looking for expertise in lean methodologies. The inclusion of quantifiable experiences or methodologies, along with a mention of the targeted company, demonstrates a tailored approach and genuine interest in contributing to that organization’s success.
Lead/Super Experienced level
Senior level
Mid-Level level
Junior level
Entry-Level level
Weak Resume Objective Examples
How to Impress with Your Lean Process Improvement Specialist Work Experience
When writing an effective work experience section for a Lean Process Improvement Specialist, it’s essential to focus on clarity, relevance, and quantifiable achievements. Here are some key guidelines:
Use a Clear Format: Start with your job title, company name, location, and dates of employment. Follow with bullet points to describe your responsibilities and achievements. This format enhances readability.
Tailor Content to the Role: Highlight experience that directly relates to Lean methodologies, such as Value Stream Mapping, Kaizen, 5S, and DMAIC. If you’ve led or participated in continuous improvement projects, detail those experiences.
Quantify Achievements: Use numbers to demonstrate your impact. For instance, rather than simply stating you improved a process, specify how you reduced waste by a certain percentage, saved the company a specific amount of time or money, or increased throughput in a measurable way.
Focus on Specific Projects: Describe specific projects where you employed Lean principles. Discuss your role, the challenge you addressed, the actions you took, and the outcomes that ensued. This helps employers visualize your contributions and problem-solving skills.
Use Action-Oriented Language: Start each bullet with strong action verbs like "analyzed," "designed," "facilitated," or "implemented." This creates a dynamic picture of your capabilities.
Highlight Collaboration and Leadership: Lean often involves working in teams. Mention experiences where you guided cross-functional teams or engaged with stakeholders to drive improvements, showcasing your teamwork and leadership skills.
Customize for Each Application: Tailor your work experience section based on the job description, emphasizing the most relevant experiences and skills.
By strategically highlighting relevant experiences and results, your work experience section can effectively illustrate your qualifications as a Lean Process Improvement Specialist.
Best Practices for Your Work Experience Section:
Strong Resume Work Experiences Examples
Lead/Super Experienced level
Senior level
Here are five strong resume bullet points for a Senior Lean Process Improvement Specialist:
Led cross-functional teams in the implementation of Lean methodologies, resulting in a 25% reduction in operational costs and a 30% increase in throughput across multiple production lines within one fiscal year.
Conducted comprehensive process mapping and value stream analysis that identified key waste areas, facilitating targeted process redesign initiatives that improved cycle time by 40%.
Spearheaded a continuous improvement training program for over 200 employees, fostering a culture of lean thinking and enhancing workforce engagement, which contributed to a sustained increase in the Net Promoter Score (NPS) by 15 points.
Championed the use of Kaizen events and root cause analysis to address persistent quality issues, achieving a 50% decrease in defect rates and minimizing rework costs across key product lines.
Collaborated with senior leadership to align Lean strategies with corporate objectives, driving strategic initiatives that improved overall organizational efficiency and led to a project savings forecast of $5 million annually.
Mid-Level level
Here are five examples of strong resume work experience bullet points for a mid-level Lean Process Improvement Specialist:
Implemented Lean Six Sigma methodologies to streamline operations in the manufacturing department, resulting in a 20% reduction in cycle time and a 15% decrease in production costs over a one-year period.
Facilitated cross-functional workshops to identify inefficiencies and waste in processes, leading to the successful launch of three key improvement initiatives that enhanced overall productivity by 30%.
Conducted root cause analysis on recurring quality issues, developing and executing corrective action plans that reduced defect rates by 25% while improving customer satisfaction scores by 10%.
Utilized value stream mapping techniques to visualize workflows and identify bottlenecks, enabling the team to implement targeted process changes that improved lead times by 40%.
Mentored and trained staff on Lean principles and tools, fostering a culture of continuous improvement and empowering teams to independently identify and solve process-related challenges.
Junior level
Entry-Level level
Weak Resume Work Experiences Examples
Top Skills & Keywords for Lean Process Improvement Specialist Resumes:
Top Hard & Soft Skills for Lean Process Improvement Specialist:
Hard Skills
Soft Skills
Elevate Your Application: Crafting an Exceptional Lean Process Improvement Specialist Cover Letter
Lean Process Improvement Specialist Cover Letter Example: Based on Resume
Resume FAQs for Lean Process Improvement Specialist:
How long should I make my Lean Process Improvement Specialist resume?
When crafting a resume for a Lean Process Improvement Specialist position, aim for a length of one page, or two pages if you have extensive experience. The key is to be concise while effectively showcasing your skills and accomplishments.
For most professionals, particularly those with 5-10 years of experience, a one-page resume is ideal. Focus on relevant skills such as Lean methodologies, Six Sigma certifications, and project management expertise. Use bullet points to highlight accomplishments using quantifiable metrics to demonstrate your impact, like cost savings or efficiency improvements.
If you possess significant experience, specialized certifications, or a diverse work history, a two-page resume might be appropriate. However, ensure that every piece of information adds value and stays relevant to the role.
Prioritize clarity and readability—choose a clean layout with consistent formatting. Tailor your resume to the specific job description by incorporating keywords relevant to Lean principles and process improvement.
In summary, keep your resume succinct, focusing on the most relevant experience, skills, and achievements to effectively present yourself as a strong candidate for the Lean Process Improvement Specialist role.
What is the best way to format a Lean Process Improvement Specialist resume?
When crafting a resume for a Lean Process Improvement Specialist position, clarity and conciseness are paramount. Start with a professional header that includes your name, contact information, and LinkedIn profile if applicable.
Follow with a strong summary statement, emphasizing your experience in lean methodologies, problem-solving skills, and your ability to drive process efficiency. Use bullet points for easy readability.
Next, outline your professional experience. List your roles in reverse chronological order, focusing on achievements rather than just duties. Incorporate quantifiable results, such as percentage improvements in efficiency or cost savings, to demonstrate the impact of your work.
Include a dedicated skills section highlighting relevant competencies like Six Sigma, Kaizen, value stream mapping, and data analysis tools.
Education and certifications should follow, showcasing any degrees or qualifications related to lean practices. If you have certifications like Lean Six Sigma Green or Black Belt, include these prominently.
Finally, consider adding a section for professional affiliations or memberships in relevant organizations to showcase your commitment to continuous improvement. Remember to tailor your resume for each application, using industry-specific keywords to pass through Applicant Tracking Systems. A well-structured and focused resume can significantly enhance your chances of landing an interview.
Which Lean Process Improvement Specialist skills are most important to highlight in a resume?
When crafting a resume for a Lean Process Improvement Specialist, it's crucial to highlight specific skills that demonstrate proficiency in lean methodologies and continuous improvement. Key skills to emphasize include:
Lean Methodologies: Proficiency in Lean principles, including Value Stream Mapping, 5S, Kaizen, and Standardized Work, showcases an understanding of waste reduction and efficiency improvement.
Problem-Solving: Strong analytical skills are essential for identifying inefficiencies and developing effective solutions using root cause analysis techniques, such as the 5 Whys and Fishbone Diagram.
Project Management: Experience in overseeing projects from inception to completion, utilizing tools like Gantt charts and Agile methodologies, indicates the ability to manage timelines and resources effectively.
Data Analysis: Proficiency in data collection and analysis using tools like Six Sigma, Minitab, or Excel to track performance metrics and assess process improvements.
Cross-Functional Collaboration: Ability to work effectively with diverse teams, fostering communication and cooperation among various departments to drive initiatives successfully.
Training and Facilitation: Experience in training staff on lean principles and facilitating workshops helps in building a culture of continuous improvement.
Highlighting these skills will make a Lean Process Improvement Specialist stand out to potential employers.
How should you write a resume if you have no experience as a Lean Process Improvement Specialist?
Writing a resume for a lean process improvement specialist role without direct experience can be challenging, but it’s entirely feasible by leveraging related skills and experiences. Start with a strong summary statement highlighting your enthusiasm for process improvement and your understanding of lean principles. Emphasize any coursework, certifications, or training in lean methodologies, such as Lean Six Sigma or Kaizen.
In the skills section, focus on transferable skills relevant to the role, such as analytical thinking, problem-solving, team collaboration, and project management. If you’ve participated in any projects, internships, or volunteer efforts, describe how you contributed to improving efficiency or solving problems.
When detailing your education, include relevant coursework that showcases your analytical skills or understanding of operational systems. For any work experience, frame your responsibilities in terms of process improvement. For example, if you worked in retail, mention how you streamlined inventory management or enhanced customer service processes.
Finally, consider adding a section for relevant projects or achievements, even if they were part of studies, including quantifiable results. Tailor your resume for each job application to align with the specific requirements and language of the job description.
Professional Development Resources Tips for Lean Process Improvement Specialist:
TOP 20 Lean Process Improvement Specialist relevant keywords for ATS (Applicant Tracking System) systems:
Sample Interview Preparation Questions:
Can you describe your experience with Lean methodologies and how you have applied them in previous roles?
How do you prioritize process improvement initiatives within an organization, and what criteria do you use to determine their potential impact?
Can you provide an example of a successful Lean project you led, including the specific tools and techniques you utilized to achieve the results?
How do you measure the success of a process improvement initiative, and what metrics do you consider most important?
How do you handle resistance to change from team members or stakeholders when implementing Lean practices?
Related Resumes for Lean Process Improvement Specialist:
Generate Your NEXT Resume with AI
Accelerate your resume crafting with the AI Resume Builder. Create personalized resume summaries in seconds.