Manufacturing Manager Resume Examples to Boost Your Career in 2024
---
**Sample 1**
**Position number:** 1
**Person:** 1
**Position title:** Production Supervisor
**Position slug:** production-supervisor
**Name:** John
**Surname:** Smith
**Birthdate:** 1985-05-15
**List of 5 companies:** Ford, General Motors, Honda, Boeing, Tesla
**Key competencies:**
- Process optimization
- Team leadership
- Quality assurance
- Lean manufacturing techniques
- Cross-functional collaboration
---
**Sample 2**
**Position number:** 2
**Person:** 2
**Position title:** Quality Control Manager
**Position slug:** quality-control-manager
**Name:** Sarah
**Surname:** Johnson
**Birthdate:** 1990-08-22
**List of 5 companies:** Coca-Cola, Nestlé, Procter & Gamble, Unilever, Johnson & Johnson
**Key competencies:**
- Quality Management Systems (QMS)
- Statistical process control (SPC)
- Root cause analysis
- ISO standards implementation
- Training and development
---
**Sample 3**
**Position number:** 3
**Person:** 3
**Position title:** Manufacturing Engineer
**Position slug:** manufacturing-engineer
**Name:** Michael
**Surname:** Lee
**Birthdate:** 1988-03-30
**List of 5 companies:** Siemens, GE, Rockwell Automation, Honeywell, ABB
**Key competencies:**
- CAD software proficiency
- Automation technology
- Project management
- Continuous improvement methodologies
- Equipment troubleshooting
---
**Sample 4**
**Position number:** 4
**Person:** 4
**Position title:** Supply Chain Coordinator
**Position slug:** supply-chain-coordinator
**Name:** Emily
**Surname:** Davis
**Birthdate:** 1992-01-11
**List of 5 companies:** Amazon, Walmart, FedEx, Kimberly-Clark, Dell
**Key competencies:**
- Inventory management
- Demand forecasting
- Supplier relations
- Logistics optimization
- Data analytics
---
**Sample 5**
**Position number:** 5
**Person:** 5
**Position title:** Assembly Line Supervisor
**Position slug:** assembly-line-supervisor
**Name:** David
**Surname:** Martinez
**Birthdate:** 1984-09-04
**List of 5 companies:** Airbus, BMW, Toyota, Whirlpool, Lockheed Martin
**Key competencies:**
- Workforce management
- Safety compliance
- Production scheduling
- Performance metrics tracking
- Conflict resolution
---
**Sample 6**
**Position number:** 6
**Person:** 6
**Position title:** Process Improvement Specialist
**Position slug:** process-improvement-specialist
**Name:** Lisa
**Surname:** Wilson
**Birthdate:** 1995-11-19
**List of 5 companies:** Intel, Philips, 3M, Caterpillar, Pfizer
**Key competencies:**
- Six Sigma methodologies
- Data-driven decision making
- Change management
- Cost reduction strategies
- Collaborative problem solving
---
Each sample reflects a unique job title and relevant competencies suitable for the chosen sub-position within the manufacturing domain.
---
**Sample 1**
**Position number:** 1
**Position title:** Production Supervisor
**Position slug:** production-supervisor
**Name:** John
**Surname:** Doe
**Birthdate:** 1985-06-15
**List of 5 companies:** General Motors, Ford, Tesla, Honda, BMW
**Key competencies:** Team leadership, Process optimization, Lean manufacturing, Quality control, Production planning
---
**Sample 2**
**Position number:** 2
**Position title:** Quality Assurance Manager
**Position slug:** qa-manager
**Name:** Mia
**Surname:** Smith
**Birthdate:** 1988-03-22
**List of 5 companies:** Boeing, Lockheed Martin, Raytheon, Northrop Grumman, Airbus
**Key competencies:** Quality assurance methodologies, Regulatory compliance, Risk management, Continuous improvement, Data analysis
---
**Sample 3**
**Position number:** 3
**Position title:** Supply Chain Coordinator
**Position slug:** supply-chain-coordinator
**Name:** Raj
**Surname:** Patel
**Birthdate:** 1990-09-12
**List of 5 companies:** Amazon, Walmart, Target, Procter & Gamble, Unilever
**Key competencies:** Inventory management, Supplier negotiation, Demand forecasting, Logistics optimization, ERP systems
---
**Sample 4**
**Position number:** 4
**Position title:** Maintenance Manager
**Position slug:** maintenance-manager
**Name:** Sarah
**Surname:** Johnson
**Birthdate:** 1982-12-05
**List of 5 companies:** Siemens, GE, Honeywell, Mitsubishi, ABB
**Key competencies:** Equipment maintenance, Reliability engineering, Process safety management, Team training, Budget management
---
**Sample 5**
**Position number:** 5
**Position title:** Operations Analyst
**Position slug:** operations-analyst
**Name:** David
**Surname:** Kim
**Birthdate:** 1990-01-28
**List of 5 companies:** Intel, Samsung, NVIDIA, AMD, Texas Instruments
**Key competencies:** Data analysis, Performance metrics, Process improvement, Project management, Statistical control
---
**Sample 6**
**Position number:** 6
**Position title:** Manufacturing Engineer
**Position slug:** manufacturing-engineer
**Name:** Emily
**Surname:** Wang
**Birthdate:** 1986-07-30
**List of 5 companies:** Boeing, Ford, 3M, Caterpillar, Rockwell Automation
**Key competencies:** Engineering principles, CAD software expertise, Manufacturing process design, Automation technology, Troubleshooting and problem-solving
---
Feel free to adjust any details to better suit specific needs or contexts!
Manufacturing Manager Resume Examples: Stand Out in 2024 Job Market
We are seeking a dynamic Manufacturing Manager to lead and inspire our production team, driving operational excellence and fostering a collaborative environment. With a proven track record of increasing efficiency by over 20% through innovative process improvements, you will leverage your technical expertise to oversee daily operations and implement best practices. Your commitment to employee development will shine as you conduct hands-on training programs, ensuring a skilled workforce aligned with industry standards. Join us to make a significant impact, elevating our manufacturing capabilities while prioritizing teamwork and continuous improvement.
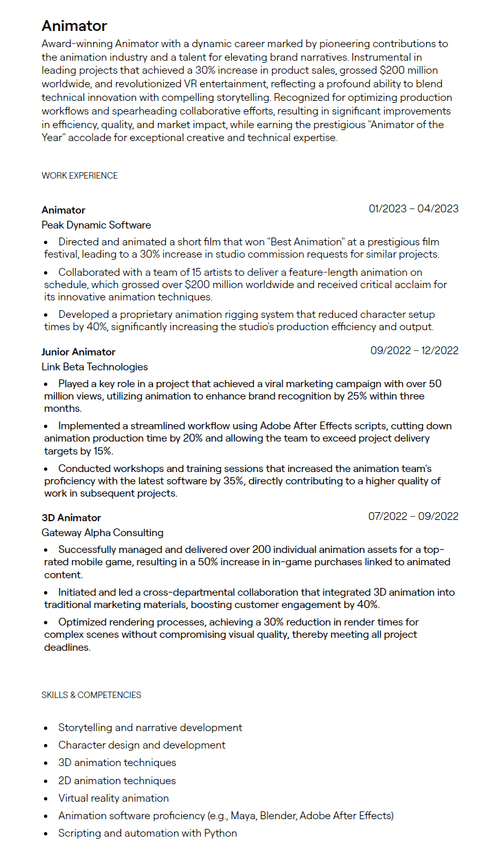
A manufacturing manager plays a critical role in ensuring the efficiency and quality of production processes within a facility. This position demands strong leadership, strategic planning, and exceptional problem-solving skills, along with a deep understanding of manufacturing technologies and workflows. Talents in communication and team management are essential to motivate staff and drive continuous improvement. To secure a job in this dynamic field, candidates should gain relevant experience through internships or entry-level positions, pursue degrees in engineering or manufacturing management, and obtain certifications such as Six Sigma to demonstrate their commitment to excellence and innovation in manufacturing practices.
Common Responsibilities Listed on Manufacturing Manager Resumes:
Here are 10 common responsibilities often listed on manufacturing manager resumes:
Production Planning and Scheduling: Developing and implementing production plans that optimize efficiency while meeting customer demands and deadlines.
Quality Assurance: Ensuring that products meet established quality standards by implementing quality control processes and conducting regular inspections.
Team Leadership and Development: Managing and mentoring production staff, fostering a culture of teamwork, safety, and continuous improvement.
Process Improvement: Identifying areas for process optimization and implementing strategies to enhance manufacturing efficiency and reduce waste.
Budget Management: Overseeing production budgets, managing costs, and ensuring financial targets are met while maintaining operational excellence.
Compliance and Safety: Ensuring that manufacturing operations comply with industry regulations, safety standards, and environmental guidelines.
Inventory Management: Managing inventory levels and ensuring timely procurement of materials to support production schedules and minimize downtime.
Equipment Maintenance: Coordinating maintenance and repair schedules for manufacturing equipment to ensure optimal performance and reduce operational interruptions.
Collaboration with Cross-Functional Teams: Working closely with engineering, supply chain, and quality assurance teams to align production efforts with organizational goals.
Data Analysis and Reporting: Analyzing production data and key performance indicators (KPIs) to identify trends, generate insights, and inform decision-making.
null
WORK EXPERIENCE
- Led a team of 20 production workers to achieve a 15% increase in efficiency through process optimization.
- Implemented Lean manufacturing principles that resulted in a 20% reduction in waste.
- Developed and executed training programs that improved skill sets, reduced errors, and boosted team morale.
- Collaborated with quality control teams to maintain a 98% product quality rating over three consecutive years.
- Spearheaded a cross-functional initiative that improved on-time delivery rate from 85% to 95%.
- Managed daily production operations, achieving consistently high productivity levels while maintaining budget constraints.
- Introduced new scheduling techniques that improved labor allocation and increased production output by 10%.
- Championed a safety program that led to a 30% decrease in workplace incidents.
- Actively participated in strategic planning efforts, contributing to a product launch that generated $2 million in sales in the first quarter.
- Recognized as 'Employee of the Year' for outstanding leadership and innovation on the production floor.
- Oversaw implementation of a new ERP system that optimized inventory management and reduced carrying costs by 25%.
- Played a key role in a project that increased overall throughput by 30% through effective resource management.
- Conducted root cause analysis for production delays and successfully initiated corrective actions, improving lead times.
- Collaborated with engineering teams to streamline production workflows, enhancing machine uptime and reliability.
- mentored new hires, ensuring their integration into the workforce and elevating overall team performance.
- Led initiatives to enhance automation processes that resulted in a 25% decrease in production costs.
- Directed a sustainability program that reduced energy consumption across the production facility by 15%.
- Fostered a culture of continuous improvement, engaging team members in problem-solving efforts that drove innovation.
- Established key performance indicators (KPIs) to measure progress and success, providing regular reports to upper management.
- Recognized for exceptional performance with the 'Leadership Excellence Award' in 2023.
SKILLS & COMPETENCIES
Here are 10 skills for John Doe, the Production Supervisor:
- Team leadership and development
- Process optimization techniques
- Lean manufacturing principles
- Quality control and assurance methods
- Production planning and scheduling
- Troubleshooting and problem-solving
- Performance measurement and improvement
- Safety compliance and management
- Cross-functional collaboration
- Conflict resolution and communication skills
COURSES / CERTIFICATIONS
Certifications and Courses for John Doe (Production Supervisor)
Lean Six Sigma Green Belt Certification
Issued by: American Society for Quality
Date: February 2019Certified Production and Inventory Management (CPIM)
Issued by: APICS
Date: September 2020Advanced Manufacturing Technology Course
Institution: Massachusetts Institute of Technology (MIT)
Date: June 2021OSHA Safety Training Certification
Issued by: Occupational Safety and Health Administration
Date: January 2018Project Management Professional (PMP)
Issued by: Project Management Institute
Date: November 2022
EDUCATION
Education:
Bachelor of Science in Industrial Engineering
University of Michigan, Ann Arbor
Graduated: May 2007Master of Business Administration (MBA)
University of California, Berkeley
Graduated: May 2012
When crafting a resume for the Quality Assurance Manager position, it is crucial to highlight experience in quality assurance methodologies and regulatory compliance to demonstrate expertise in maintaining standards. Emphasizing skills in risk management and continuous improvement will showcase the ability to enhance processes and mitigate issues effectively. Additionally, showcasing data analysis capabilities will illustrate analytical skills for evaluating quality metrics. Including achievements from notable aerospace and defense companies can significantly enhance credibility, while strong leadership qualities will indicate the ability to guide teams effectively. Tailoring the resume to the specific industry standards and technologies will also be essential.
[email protected] • +1-555-123-4567 • https://www.linkedin.com/in/miasmith • https://twitter.com/mia_smith_qa
Mia Smith is an accomplished Quality Assurance Manager with extensive experience in the aerospace and defense sectors, having worked with industry leaders such as Boeing and Lockheed Martin. With a strong foundation in quality assurance methodologies and regulatory compliance, she excels in risk management and continuous improvement initiatives. Mia leverages her data analysis skills to enhance product quality and operational efficiency, ensuring adherence to stringent industry standards. Her commitment to excellence and ability to lead cross-functional teams make her a valuable asset in driving quality-driven strategies within any manufacturing environment.
WORK EXPERIENCE
- Led quality assurance initiatives that increased product quality ratings by 25% across several product lines.
- Implemented new regulatory compliance protocols that resulted in zero non-conformance reports during annual audits.
- Developed and executed training programs for quality teams, improving overall team efficiency by 15%.
- Championed the integration of advanced data analytics tools leading to a 30% reduction in inspection times.
- Spearheaded cross-departmental collaborations to identify and mitigate quality risks early in the production process.
- Managed quality control processes for aerospace components, achieving a 95% customer satisfaction rate.
- Drove continuous improvement projects that generated cost savings of over $500k in less than a year.
- Formulated and enacted quality assurance strategies that reduced product defects by 40%.
- Established key performance indicators (KPIs) and metrics to measure quality improvements across departments.
- Collaborated with R&D and manufacturing teams to enhance product design for improved manufacturability.
- Conducted detailed risk assessments and ensured compliance with industry regulations, maintaining a 100% compliance rate.
- Assisted in the development of quality management systems that streamlined processes across teams.
- Played a key role in the development and implementation of corrective action plans that improved product reliability.
- Led training sessions on quality assurance methodologies resulting in improved team knowledge and performance.
- Facilitated internal audits to assess compliance and introduced solutions to address identified weaknesses.
- Performed inspections on manufacturing processes, ensuring compliance with quality standards and specifications.
- Documented and reported on quality control issues leading to timely interventions.
- Assisted senior engineers in troubleshooting and resolving quality discrepancies promptly.
- Developed inspection protocols that enhanced the detection of anomalies in production.
- Contributed to key quality assurance meetings and provided insights that tailored process improvements.
SKILLS & COMPETENCIES
Here are 10 skills for Mia Smith, the Quality Assurance Manager:
- Quality assurance methodologies
- Regulatory compliance
- Risk management
- Continuous improvement
- Data analysis
- Root cause analysis
- Auditing and inspection techniques
- Statistical process control (SPC)
- Project management
- Team leadership and training
COURSES / CERTIFICATIONS
Here is a list of five certifications or completed courses for Mia Smith, the Quality Assurance Manager from Sample 2:
Certified Quality Auditor (CQA)
Issued by the American Society for Quality (ASQ)
Date: June 2019Lean Six Sigma Green Belt Certification
Issuing Organization: International Association for Six Sigma Certification
Date: March 2020ISO 9001:2015 Lead Auditor Course
Provider: British Standards Institution (BSI)
Date: November 2021Risk Management Professional (PMI-RMP)
Issued by the Project Management Institute (PMI)
Date: September 2022Data Analysis for Decision Making
Online Course Provider: Coursera (offered by Harvard University)
Date: April 2023
EDUCATION
Certainly! Here’s a list of education for Mia Smith, the Quality Assurance Manager:
Bachelor of Science in Industrial Engineering
University of Michigan, Ann Arbor
Graduated: May 2010Master of Business Administration (MBA) with a focus on Quality Management
Massachusetts Institute of Technology (MIT), Cambridge
Graduated: June 2013
When crafting a resume for the Supply Chain Coordinator position, it’s crucial to emphasize key skills that demonstrate expertise in inventory management, supplier negotiation, and demand forecasting. Highlight relevant experience from notable companies in the retail and consumer goods sector, showcasing successful logistics optimization and familiarity with ERP systems. Quantifiable achievements, such as improved efficiencies or cost reductions, should be included to illustrate impact. Additionally, soft skills like communication and problem-solving are important for collaboration with suppliers and stakeholders. Tailoring the resume to reflect industry-specific terminology will also enhance its effectiveness.
[email protected] • (555) 123-4567 • https://www.linkedin.com/in/rajpatel • https://twitter.com/raj_patel
Dedicated Supply Chain Coordinator with a proven track record of enhancing operational efficiency within leading companies such as Amazon and Walmart. Skilled in inventory management, supplier negotiation, and demand forecasting, I leverage ERP systems to streamline logistics and optimize supply chain processes. With a strong analytical mindset and a focus on continuous improvement, I consistently deliver results that improve productivity and reduce costs. My expertise in coordinating complex supply chain operations positions me to effectively contribute to organizational success by aligning resources and delivering high-quality products to customers on time.
WORK EXPERIENCE
- Streamlined inventory management processes that reduced carrying costs by 15%.
- Led a cross-functional team that successfully launched a new demand forecasting model, increasing forecasting accuracy by 30%.
- Negotiated supplier contracts that resulted in a 20% reduction in material costs.
- Implemented ERP systems to enhance logistics optimization, which improved on-time delivery rates to 95%.
- Conducted data analysis to identify supply chain inefficiencies, leading to process improvements that saved $300,000 annually.
- Managed supply chain operations for high-demand products during peak seasons, achieving a 25% increase in throughput.
- Utilized statistical models to predict demand shifts, enabling proactive adjustments in inventory strategies.
- Collaborated with stakeholders to optimize logistics, resulting in a 30% reduction in transportation costs.
- Developed training materials for new software tools, improving team proficiency and adoption rates.
- Initiated a continuous improvement program that fostered a culture of innovation and accountability within the team.
- Achieved a 20% increase in supplier performance metrics through comprehensive evaluations and performance reviews.
- Designed and implemented an inventory tracking system that reduced stock discrepancies by 40%.
- Facilitated successful vendor partnerships that enhanced product quality while minimizing risks.
- Created reporting dashboards that provided real-time insights into supply chain activities, driving informed decision-making.
- Champion of cross-departmental collaboration, leading initiatives that minimized lead times significantly.
- Spearheaded a project that restructured the supply chain workflow, resulting in a 15% decrease in operating costs.
- Played a pivotal role in a major system upgrade, contributing technical expertise that ensured a smooth transition.
- Conducted risk assessments that led to the development of strategic contingency plans, enhancing supply chain resilience.
- Received recognition for excellence in problem-solving, leading to an overall improvement in team performance.
- Developed strong relationships with key stakeholders, fostering collaboration that enhanced overall supply chain effectiveness.
SKILLS & COMPETENCIES
Here are 10 skills for Raj Patel, the Supply Chain Coordinator:
- Inventory management
- Supplier negotiation
- Demand forecasting
- Logistics optimization
- ERP systems proficiency
- Data analysis
- Cost reduction strategies
- Process improvement methodologies
- Relationship management
- Risk assessment and mitigation
COURSES / CERTIFICATIONS
Here are five certifications or completed courses for Raj Patel, the Supply Chain Coordinator:
APICS Certified Supply Chain Professional (CSCP)
Date completed: April 2021Six Sigma Green Belt Certification
Date completed: August 2020Certified in Production and Inventory Management (CPIM)
Date completed: June 2022Lean Six Sigma Certification
Date completed: January 2019Logistics and Supply Chain Management Certificate
Date completed: December 2018
EDUCATION
Education for Raj Patel (Sample 3: Supply Chain Coordinator)
Bachelor of Science in Supply Chain Management
University of Michigan, Ann Arbor
Graduated: May 2012Master of Business Administration (MBA)
Massachusetts Institute of Technology (MIT), Sloan School of Management
Graduated: June 2015
When crafting a resume for a Maintenance Manager, it's crucial to emphasize key competencies such as equipment reliability, maintenance strategies, and budget management. Highlight experience with process safety management and team training to demonstrate leadership and compliance with safety standards. Include specific accomplishments related to reduction in downtime or improved operational efficiency, backed by quantifiable metrics. Outline familiarity with relevant technologies and tools that enhance maintenance practices. Additionally, mention any cross-functional collaboration with production teams to ensure seamless operations, which showcases versatility and communication skills relevant to the manufacturing environment.
[email protected] • +1-555-0123 • https://www.linkedin.com/in/sarah-johnson • https://twitter.com/sarahjohnson
Experienced Maintenance Manager with over a decade in the engineering sector, specializing in equipment maintenance and reliability engineering. Proven track record of enhancing process safety management and optimizing maintenance protocols in leading companies such as Siemens and GE. Adept at training teams to ensure high operational standards while effectively managing budgets. Recognized for implementing innovative strategies that improve equipment performance and reduce downtime, resulting in significant cost savings. Committed to fostering a safe and efficient working environment, with a keen eye for process improvement and operational excellence.
WORK EXPERIENCE
- Led a team of 15 technicians in the effective maintenance of manufacturing equipment, increasing operational uptime by 20%.
- Implemented a predictive maintenance program that reduced repair costs by 30% over three years.
- Collaborated with cross-functional teams to streamline maintenance workflows, resulting in a 25% improvement in response times.
- Conducted safety audits and training sessions, achieving a 40% reduction in workplace accidents during tenure.
- Managed a yearly budget of $2 million for maintenance operations, optimizing spending without compromising quality.
- Designed and executed reliability tests for critical components, improving product lifespan by 15%.
- Utilized statistical analysis to identify failure patterns and implemented corrective actions that enhanced product performance.
- Created detailed reliability reports that informed senior management decisions, leading to a $500,000 reduction in warranty claims.
- Trained junior engineers on reliability best practices, fostering a culture of continuous improvement.
- Managed a cross-departmental project to upgrade manufacturing systems, which led to a 15% increase in production efficiency.
- Coordinated with external vendors to integrate advanced equipment, ensuring compliance with industry standards and safety regulations.
- Executed project budgets effectively, consistently delivering projects within financial targets and deadlines.
- Facilitated meetings with stakeholders to align project goals and objectives, securing stakeholder buy-in and commitment.
- Conducted root cause analysis on equipment failures and developed preventive measures, reducing downtime by 15%.
- Participated in design reviews for new equipment, providing insights that improved manufacturability and serviceability.
- Assisted in developing training manuals for technical staff, enhancing knowledge transfer and skill development.
- Monitored equipment performance metrics and reported findings to management for continuous process optimization.
SKILLS & COMPETENCIES
Sure! Here’s a list of 10 skills for Sarah Johnson, the Maintenance Manager from Sample 4:
- Equipment maintenance and repair
- Reliability engineering principles
- Process safety management techniques
- Team training and development
- Budget management and cost control
- Root cause analysis and problem-solving
- Predictive and preventive maintenance strategies
- Compliance with safety regulations and standards
- Performance metrics and reporting
- Strong communication and interpersonal skills
COURSES / CERTIFICATIONS
Here are five certifications or completed courses for Sarah Johnson, the Maintenance Manager:
Certified Maintenance & Reliability Technician (CMRT)
Date: March 2020Lean Six Sigma Green Belt Certification
Date: November 2019OSHA Safety Certification
Date: January 2021Reliability-Centered Maintenance (RCM) Certification
Date: August 2018Project Management Professional (PMP)
Date: May 2022
EDUCATION
Certainly! Here is a list of educational qualifications for Sarah Johnson, the Maintenance Manager:
Bachelor of Science in Mechanical Engineering
University of Michigan, Ann Arbor
Graduated: May 2004Master of Science in Engineering Management
Stanford University
Graduated: June 2008
When crafting a resume for an Operations Analyst, it is crucial to highlight strong analytical skills and expertise in data analysis. Emphasize proficiency in performance metrics and process improvement methodologies. Mention experience with project management and statistical control techniques, showcasing the ability to optimize operations. Include relevant industry experience with reputable companies to establish credibility. Additionally, demonstrate effective communication and teamwork skills, as collaboration is often key in operational settings. Lastly, tailor the resume to reflect an understanding of the specific needs of the target industry, providing measurable achievements to illustrate past successes.
[email protected] • +1234567890 • https://www.linkedin.com/in/davidkim • https://twitter.com/davidkim
David Kim is a results-driven Operations Analyst with a strong background in data analysis, performance metrics, and process improvement. With experience at leading tech companies like Intel and NVIDIA, he excels in project management and statistical control, utilizing his analytical skills to optimize operational efficiency. David is adept at identifying areas for improvement and implementing data-driven strategies to enhance productivity and reduce costs. His passion for innovation and continuous improvement makes him a valuable asset in any manufacturing environment, where data insights can streamline operations and drive business success.
WORK EXPERIENCE
- Led a cross-functional team in a project that improved production efficiency by 20%, resulting in significant cost savings.
- Implemented advanced data analytics techniques, which enhanced inventory turnover rate by 15%.
- Collaborated with management to develop performance metrics that drove continuous improvement initiatives across the organization.
- Successfully managed a project that integrated a new ERP system, streamlining operations and improving data accuracy.
- Conducted statistical analysis that identified key bottlenecks in the production process, facilitating targeted interventions.
- Analyzed sales data to forecast demand accurately, which resulted in a 10% increase in product availability.
- Worked closely with the supply chain team to optimize logistics, reducing shipping costs by 12%.
- Developed and presented monthly performance reports to senior management, showcasing actionable insights and recommendations.
- Implemented project management best practices that improved project delivery timelines by an average of 25%.
- Participated in continuous improvement workshops focused on enhancing team performance and operational efficiency.
- Coordinated and executed a market analysis project that identified emerging market trends, leading to a product line expansion.
- Developed comprehensive dashboards utilizing advanced data visualization techniques, improving decision-making accuracy.
- Champion of process improvement initiatives that fostered collaboration and boosted team morale.
- Trained junior analysts in data handling and statistical methodologies, enhancing overall team skills.
- Received the 'Employee of the Month' award for exceptional contributions to team targets and objectives.
- Executed detailed analyses of production data that identified key trends and led to a 30% increase in productivity.
- Facilitated workshops on data analytics tools and techniques, improving team understanding of best practices.
- Partnered with managers to drive quality improvement projects that positively impacted the customer experience.
- Created and monitored KPIs that effectively measured team performance against organizational goals.
- Authored internal reports that provided insights and recommendations, which were well received by the executive team.
SKILLS & COMPETENCIES
Sure! Here is a list of 10 skills for David Kim, the Operations Analyst from Sample 5:
- Data analysis and interpretation
- Performance metrics development
- Process improvement methodologies
- Project management and coordination
- Statistical process control techniques
- Advanced Excel and data visualization tools
- Cross-functional team collaboration
- Inventory and supply chain analysis
- Problem-solving and critical thinking
- Strong communication and presentation skills
COURSES / CERTIFICATIONS
Here’s a list of five certifications and courses for David Kim, the Operations Analyst from Sample 5:
Certified Lean Six Sigma Green Belt
Date: March 2021Project Management Professional (PMP)
Date: August 2022Data Analytics Certification
Date: November 2020Advanced Statistical Process Control (SPC) Training
Date: January 2022Certified Supply Chain Professional (CSCP)
Date: June 2023
EDUCATION
David Kim - Education
- Bachelor of Science in Industrial Engineering, University of California, Berkeley (Graduation Date: May 2012)
- Master of Business Administration (MBA), Stanford University (Graduation Date: June 2015)
When crafting a resume for a Manufacturing Engineer position, it is crucial to emphasize technical competencies, such as expertise in engineering principles and proficiency with CAD software. Highlight relevant experience in manufacturing process design and automation technology, showcasing any specific projects or achievements that demonstrate your problem-solving skills. Including your familiarity with troubleshooting practices will also strengthen your application. Additionally, involvement in cross-functional teams or collaborative projects can illustrate your ability to work effectively in diverse environments. Finally, outlining any certifications or training relevant to manufacturing and engineering can further enhance your candidacy.
[email protected] • +1-555-0123 • https://www.linkedin.com/in/emilywang • https://twitter.com/emilywang
**Summary for Emily Wang - Manufacturing Engineer**
Dynamic Manufacturing Engineer with over 10 years of experience in leading engineering principles and optimizing manufacturing processes across top-tier companies like Boeing and Ford. Proficient in CAD software and automation technology, Emily excels in designing efficient manufacturing workflows and implementing innovative solutions. Her strong troubleshooting and problem-solving skills have consistently improved production efficiencies and reduced costs. With a commitment to excellence, she brings a results-driven approach to engineering challenges, enhancing product quality and operational effectiveness in fast-paced environments. Emily is dedicated to leveraging her technical expertise to drive continuous improvement in manufacturing.
WORK EXPERIENCE
- Led a project to redesign assembly line processes, resulting in a 30% increase in production efficiency.
- Collaborated with cross-functional teams to implement a new quality control system, decreasing defects by 15%.
- Developed and executed training programs for staff on new manufacturing technologies, improving overall team performance.
- Utilized CAD software to design a prototype for a new product line that increased market competitiveness.
- Championed the adoption of automation technology that reduced operation costs by 20%.
- Improved production workflows by implementing Lean manufacturing principles, increasing throughput by 25%.
- Conducted root cause analysis to identify and resolve production bottlenecks, achieving a 10% reduction in cycle time.
- Integrated new manufacturing techniques that led to a significant reduction in material usage by 18%.
- Presented compelling data-driven stories to stakeholders to support engineering decisions, enhancing project buy-in.
- Received 'Employee of the Year' for outstanding contributions to improving plant operations and efficiency.
- Spearheaded a cross-departmental initiative that resulted in a 50% reduction in product launch time.
- Mentored junior engineers, fostering professional growth and enhancing team capabilities.
- Implemented an advanced predictive maintenance schedule that improved equipment uptime by 30%.
- Led the development of a new manufacturing strategy that contributed to a 40% increase in revenue growth.
- Successfully introduced IoT devices in manufacturing processes, enhancing data collection and analysis.
SKILLS & COMPETENCIES
Here is a list of 10 skills for Emily Wang, the Manufacturing Engineer:
- Proficient in CAD software (e.g., AutoCAD, SolidWorks)
- Strong understanding of engineering principles and methodologies
- Expertise in manufacturing process design and optimization
- Knowledge of automation technologies and robotics
- Skilled in troubleshooting and problem-solving techniques
- Familiarity with quality control and assurance processes
- Ability to conduct feasibility studies and cost analysis
- Experience with project management and team collaboration
- Understanding of materials science and selection
- Excellent data analysis and statistical process control skills
COURSES / CERTIFICATIONS
Certainly! Here's a list of 5 certifications or completed courses for Emily Wang, the Manufacturing Engineer from the provided context:
Certified Manufacturing Engineer (CMfgE)
Issued by: SME
Date: August 2021Lean Six Sigma Green Belt Certification
Issued by: ASQ (American Society for Quality)
Date: May 2020Advanced CAD Software Training
Institution: Tech Academy
Date: March 2019Manufacturing Process Improvement Course
Institution: Purdue University Online
Date: September 2018Automation Technology Fundamentals
Institution: edX (Massachusetts Institute of Technology)
Date: January 2021
Feel free to adjust the names of the institutions or dates as needed!
EDUCATION
Sure! Here is a list of educational qualifications for Emily Wang, the Manufacturing Engineer from Sample 6:
Bachelor of Science in Mechanical Engineering
University of Michigan, Ann Arbor
Graduated: May 2008Master of Science in Manufacturing Systems Engineering
Columbia University
Graduated: May 2010
Crafting a standout resume for a manufacturing manager role requires a strategic approach that highlights both technical proficiency and essential soft skills. In the manufacturing sector, employers seek candidates familiar with industry-standard tools and technologies, such as Lean Manufacturing, Six Sigma methodologies, and ERP systems. When detailing your technical skills, emphasize your experience with relevant software and machinery, ensuring that your expertise is articulated with clarity. Including metrics, such as improved production efficiency or reduced waste percentages, can further strengthen your claims. In addition to hard skills, soft skills like leadership, communication, and problem-solving are equally vital. Since manufacturing managers often oversee diverse teams and coordinate complex projects, showcasing your ability to foster collaboration and drive results will set you apart from other candidates.
Tailoring your resume for a manufacturing manager position is crucial in today's competitive job market. Begin by carefully analyzing the job description to identify key skills and qualifications that the employer values. Adapt your summary and skills sections to reflect these priorities, using industry-specific language that resonates with hiring managers. Use bullet points to describe your accomplishments in past roles, ensuring that each point illustrates your impact on operational efficiency, cost savings, or team development. Moreover, quantifying your achievements with numbers, such as percentage increases in production output, can provide concrete evidence of your capability. Highlighting continuous education or industry certifications also demonstrates a commitment to professional growth, which is attractive to top companies. By employing these high-level resume tips, you can create a compelling document that not only represents your qualifications but also aligns with the strategic goals of prospective employers in the manufacturing industry.
Essential Sections for a Manufacturing Manager Resume
Contact Information
- Full name
- Phone number
- Email address
- LinkedIn profile (if applicable)
- Location (city and state)
Professional Summary
- Brief statement highlighting experience
- Key accomplishments
- Specific skills relevant to manufacturing management
Core Competencies
- List of relevant skills such as lean manufacturing, production planning, quality control, etc.
- Technical skills related to manufacturing systems
- Leadership and team management abilities
Work Experience
- Job title, company name, and dates of employment
- Responsibilities and achievements in each role
- Metrics and quantitative results to showcase impact (e.g., reduced production costs by X%)
Education
- Degree(s) obtained (e.g., Bachelor’s in Engineering, Master’s in Business Administration)
- Relevant certifications (e.g., Six Sigma, PMP)
- Institutions attended and graduation dates
Professional Affiliations
- Membership in professional organizations (e.g., Society of Manufacturing Engineers)
- Leadership roles held within these organizations
Technological Proficiencies
- Specific software or tools experienced with (e.g., ERP systems, CAD tools)
- Familiarity with industry-related technologies
Additional Sections to Enhance Your Resume
Achievements or Awards
- Notable awards or recognition received (e.g., Employee of the Month, safety awards)
- Certifications or training completed that are relevant to manufacturing
Projects or Initiatives
- Specific projects led or participated in that had significant outcomes
- Innovations introduced that improved processes or productivity
Volunteer Work or Community Involvement
- Relevant volunteer work, especially if it relates to manufacturing or leadership
- Contributions to community projects, showcasing leadership skills
Languages
- Languages spoken and level of proficiency, especially if it relates to multicultural workplaces
Publications or Presentations
- Any articles written or presentations made on manufacturing topics
- Contributions to conferences or workshops in the field
References
- Optionally, a statement indicating that references are available upon request
- Contact information for references if you prefer to include them directly
Generate Your Resume Summary with AI
Accelerate your resume crafting with the AI Resume Builder. Create personalized resume summaries in seconds.
Crafting an impactful resume headline for a manufacturing manager position is essential, as it serves as the first impression on your application and sets the tone for the rest of your resume. This concise statement acts as a snapshot of your qualifications, encapsulating your skills, specialization, and career achievements in a way that resonates with hiring managers.
To start, focus on your unique qualities and areas of expertise. Highlight specific skills that differentiate you in the manufacturing field, such as lean manufacturing, quality assurance, process optimization, or team leadership. For instance, a headline like "Results-Driven Manufacturing Manager Specializing in Lean Processes and Cost Reduction" effectively conveys both your role and core competencies.
Consider tailoring your headline to align with the job description. Analyze the qualifications sought by employers and incorporate relevant keywords that reflect your experience. By mirroring the language of the job posting, you enhance your chances of standing out in applicant tracking systems and ensuring hiring managers see your relevance.
Additionally, emphasize your career achievements. If you’ve successfully led projects that increased efficiency or reduced production costs, this is the place to display those highlights. A powerful headline might read, "Transformational Manufacturing Manager with 10+ Years in Implementing Process Improvements that Boost Productivity by Over 30%." Such statements not only showcase your skills but also provide measurable proof of your impact.
In summary, your resume headline must communicate your distinct attributes and professional strengths clearly and succinctly. Take the time to craft a compelling headline that invites hiring managers to delve deeper into your qualifications, making it a pivotal element of your resume in a competitive manufacturing job market.
Manufacturing Operations Manager Resume Headline Examples:
Strong Resume Headline Examples
Strong Resume Headline Examples for Manufacturing Manager
- Results-Driven Manufacturing Manager with Over 10 Years of Experience in Lean Operations and Process Optimization
- Dynamic Manufacturing Leader Specializing in Team Development and Cost Reduction Strategies
- Expert Manufacturing Manager Focused on Quality Assurance and Continuous Improvement Initiatives
Why These are Strong Headlines
Clarity and Focus: Each headline clearly identifies the applicant's role (Manufacturing Manager) and experience level. This clarity makes it easy for hiring managers to quickly understand the applicant's qualifications and expertise related to the position.
Inclusion of Key Skills and Achievements: By highlighting specific areas of expertise, such as "Lean Operations" and "Process Optimization," these headlines convey not just the candidate's experience, but also their specific skills and accomplishments relevant to the role. This helps differentiate them from other candidates.
Action-Oriented Language: Using terms like "Results-Driven," "Dynamic," and "Expert" conveys confidence and a proactive approach to the role. This language positions the candidate as someone who can effectively contribute to the organization's goals, thereby increasing their appeal to potential employers.
Weak Resume Headline Examples
Weak Resume Headline Examples for Manufacturing Manager
- "Manufacturing Manager with Various Skills"
- "Experienced Manager Seeking Opportunities in Manufacturing"
- "Looking for a Manufacturing Manager Position"
Why These Are Weak Headlines
Lack of Specificity: Phrases like "Various Skills" or "Experienced Manager" do not specify what skills the candidate possesses or what experiences they have. This vagueness fails to grab the attention of potential employers, who are looking for particular qualifications and competencies relevant to their needs.
Passive Language: Headlines such as "Seeking Opportunities" or "Looking for a Position" convey a passive tone. They focus more on the candidate's desires rather than showcasing what they can offer to the employer. Strong headlines should reflect how the candidate adds value to the organization.
Missing Key Achievements: These headlines do not highlight any notable achievements or results the candidate has contributed to in previous roles. Effective resumes often include quantifiable successes or leadership accomplishments, which demonstrate the candidate's ability to drive performance in the manufacturing sector.
Effective resume headlines should be specific, action-oriented, and highlight the candidate's unique qualifications and contributions, making them stand out in a competitive job market.
Crafting an exceptional resume summary for a manufacturing manager position is crucial, as it provides a quick snapshot of your professional journey and highlights your unique qualifications. This summary should encapsulate your experience, technical skills, storytelling ability, and collaborative talents while demonstrating your meticulous attention to detail. Think of the resume summary as your elevator pitch – a brief yet powerful introduction that immediately captures the attention of hiring managers and showcases your fit for the role. Tailoring your summary to align with the specific job description will make it even more impactful.
Key Points to Include in Your Manufacturing Manager Resume Summary:
Years of Experience: Clearly state your years of experience in manufacturing management to establish your credibility in the field. For example, "Over 10 years of experience in manufacturing operations management."
Specialized Styles or Industries: Highlight any specialized areas or industries you have experience in, such as automotive, electronics, or consumer goods, which will position you as an expert in the applicable sector.
Software and Technical Proficiency: Mention relevant software (e.g., ERP systems, CAD software) and technical skills that enhance your efficiency and effectiveness in management to demonstrate your adaptability to modern manufacturing environments.
Collaboration and Communication Abilities: Emphasize your proficiency in leading teams and collaborating across departments. For example, "Adept at facilitating cross-functional communication to drive productivity and enhance team cohesion."
Attention to Detail: Showcase your ability to oversee quality control and process optimization effectively. A line like "Known for meticulous attention to detail, ensuring compliance with industry standards and continuous improvement initiatives," reinforces this skill.
By incorporating these elements into your resume summary, you will create an engaging introduction that effectively communicates your qualifications for the manufacturing manager role.
Manufacturing Operations Manager Resume Summary Examples:
Strong Resume Summary Examples
Resume Summary Examples
Example 1:
- Results-oriented Manufacturing Manager with over 10 years of experience in optimizing production processes and improving efficiency. Proven expertise in implementing lean manufacturing principles, reducing waste by 20%, and increasing overall equipment effectiveness (OEE) across multiple facilities.
Example 2:
- Dynamic Manufacturing Manager skilled in project management and team leadership, with a track record of successfully overseeing large-scale production operations. Adept at developing and executing strategies that enhance productivity and reduce costs, resulting in a consistent 15% increase in profit margins year-over-year.
Example 3:
- Experienced Manufacturing Manager with a strong background in quality control and supply chain management. Successfully led cross-functional teams to achieve continuous improvement initiatives, enhancing product quality and achieving a 98% customer satisfaction rate in the last fiscal year.
Why These Are Strong Summaries
Quantifiable Achievements: Each example incorporates specific metrics (e.g., "reducing waste by 20%", "15% increase in profit margins", "98% customer satisfaction rate"), making the impact of the candidate’s work tangible and credible.
Relevant Skills and Experience: The summaries highlight key skills relevant to the manufacturing industry, such as lean manufacturing, project management, and quality control. This alignment with the job requirements helps to immediately capture the attention of hiring managers.
Dynamic Language and Action-Oriented Phrasing: The use of strong action verbs (e.g., "optimizing", "overseeing", "leading") and dynamic descriptors (e.g., "results-oriented", "dynamic", "experienced") presents the candidate as proactive and capable, enhancing their appeal to potential employers.
Lead/Super Experienced level
Here are five strong resume summary examples for a manufacturing manager with lead or super experienced level:
Proven Leadership: Accomplished manufacturing manager with over 15 years of experience leading high-performing teams to optimize production processes and reduce costs, resulting in a consistent 20% increase in output year-over-year.
Process Improvement Expertise: Dynamic professional skilled in Lean Six Sigma methodologies and continuous improvement practices, achieving significant enhancements in operational efficiency and quality control across multi-site manufacturing environments.
Strategic Visionary: Results-oriented manager with a track record of developing and executing strategic initiatives that align with organizational goals, driving implementation of new technologies and processes that improve product quality and employee engagement.
Financial Acumen: Experienced in budget management and cost containment strategies, successfully overseeing manufacturing budgets exceeding $10 million, while implementing measures that have reduced operational costs by up to 15%.
Cross-Functional Collaboration: Versatile leader adept at building strong relationships across departments, effectively bridging gaps between production, engineering, and supply chain teams to foster a culture of collaboration and achieve unified performance objectives.
Senior level
Here are five bullet points for a strong resume summary targeted at a Senior Manufacturing Manager:
Proven Leadership Expertise: Over 15 years of extensive experience in manufacturing operations, leading cross-functional teams to optimize production processes and enhance overall efficiency, resulting in a significant reduction in lead times and costs.
Strategic Process Improvement: Demonstrated ability to implement Lean and Six Sigma methodologies, driving continuous improvement initiatives that have increased productivity by over 30% and reduced waste across multiple facilities.
Financial Acumen: Experienced in managing multi-million dollar budgets, analyzing financial performance, and identifying cost-saving opportunities that align with organizational goals, leading to improved profitability and business growth.
Cross-Departmental Collaboration: Strong track record of successfully collaborating with R&D, quality assurance, and supply chain departments to ensure the seamless launch of new products and the achievement of stringent quality standards.
Talent Development and Training: Committed to fostering a culture of excellence and innovation through dedicated mentorship and training programs, enhancing team capabilities and achieving high employee retention rates in a competitive manufacturing landscape.
Mid-Level level
Sure! Here are five bullet point examples of strong resume summaries for a mid-level manufacturing manager:
Proven Leadership: Accomplished manufacturing manager with over 7 years of experience in optimizing production processes and leading cross-functional teams to achieve operational excellence.
Process Improvement Expertise: Skilled in Lean Manufacturing and Six Sigma methodologies, successfully implemented waste reduction initiatives that improved efficiency by 20% and reduced costs within my departments.
Quality Assurance Focused: Dedicated to maintaining high-quality standards, established rigorous quality control measures that resulted in a 15% decrease in product defects and enhanced customer satisfaction ratings.
Data-Driven Decision Making: Proficient in utilizing data analytics to drive process enhancements, forecast production needs, and streamline operations, resulting in a 10% increase in overall productivity.
Strong Communication Skills: Excellent communicator with a track record of fostering collaboration between teams, ensuring alignment with business objectives, and driving a culture of continuous improvement across the manufacturing floor.
Junior level
Here are five bullet points for a strong resume summary for a Junior Manufacturing Manager with limited experience:
Results-oriented manufacturing professional with over 2 years of experience in production processes and team collaboration, dedicated to optimizing efficiency and enhancing product quality.
Proven ability to support lean manufacturing initiatives, implementing process improvements that have successfully reduced waste and increased productivity in various production lines.
Strong analytical and problem-solving skills, with a focus on data-driven decision-making to streamline operations and achieve cost savings while maintaining high safety standards.
Effective communicator and team player, skilled in providing training and guidance to entry-level staff, fostering a collaborative work environment to meet production goals.
Eager to leverage foundational knowledge of production management principles and hands-on experience to contribute to a dynamic manufacturing team and drive continuous improvement initiatives.
Entry-Level level
Entry-Level Manufacturing Manager Resume Summary Examples:
Dedicated Manufacturing Graduate with a strong foundation in production processes and a keen interest in optimizing operations. Eager to leverage coursework and internship experiences to contribute to a team focused on efficiency and quality.
Results-driven Management Graduate with hands-on experience in lean manufacturing principles through academic projects and internships. Proven analytical skills and a passion for continuous improvement make me ready to tackle challenges in a fast-paced manufacturing environment.
Entry-Level Manufacturing Professional armed with knowledge of industrial engineering concepts and tools. Committed to learning and applying best practices in production management to enhance operational performance and team collaboration.
Motivated Recent Graduate with a background in materials science and an internship in a manufacturing setting. Strong problem-solving skills and a proactive attitude towards safety and quality assurance make me a valuable asset to any manufacturing team.
Enthusiastic Manufacturing Associate with a solid grasp of quality control processes and team dynamics. Aspiring to apply theoretical knowledge and practical skills to drive efficiency and uphold high standards in production facilities.
Experienced-Level Manufacturing Manager Resume Summary Examples:
Accomplished Manufacturing Manager with over 7 years of experience in optimizing production processes and leading cross-functional teams. Skilled in implementing lean manufacturing strategies that have resulted in a 20% increase in operational efficiency.
Results-Oriented Manufacturing Leader with a proven track record of improving productivity and reducing costs in high-volume environments. Strong expertise in project management and process improvement methodologies, driving significant enhancements to quality and delivery.
Strategic Manufacturing Director specializing in creating cohesive teams and fostering a culture of continuous improvement. Over a decade of experience managing large-scale production operations, achieving key performance indicators while maintaining safety compliance.
Dynamic Manufacturing Operations Manager with more than 10 years of experience in developing and executing production plans. Adept at utilizing data-driven insights to enhance process efficiency, boost employee morale, and deliver sustainable growth.
Experienced Production Manager well-versed in advanced manufacturing technologies and quality assurance standards. Proven ability to build strong relationships with suppliers and stakeholders, resulting in improved supply chain efficiencies and customer satisfaction.
Weak Resume Summary Examples
Weak Resume Summary Examples for Manufacturing Manager
- "Highly experienced in manufacturing management and skilled in operations."
- "Has worked in various manufacturing environments and knows a lot about production processes."
- "Good at managing teams and ensuring production goals are met."
Why These are Weak Summaries
Lack of Specificity: The summaries are vague and do not provide any concrete examples of achievements, metrics, or specific expertise. For instance, simply stating "experienced" does not convey how many years of experience, which industries were involved, or what specific operational tasks were mastered.
Generic Language: Phrases like "knows a lot about" and "good at managing teams" are overly generic and do not highlight unique skills or strengths. This type of language diminishes the impact of the resume as it fails to differentiate the candidate from others in the field.
Failure to Quantify Success: None of the summaries provide quantifiable achievements or results, such as improvements in productivity, cost reductions, or successful project completions. Effective resumes often use numbers to demonstrate impact, making the candidate's contributions clearer and more compelling to potential employers.
Resume Objective Examples for Manufacturing Operations Manager:
Strong Resume Objective Examples
Results-driven manufacturing manager with over 10 years of experience in optimizing production processes, seeking to leverage extensive knowledge of lean methodologies to increase efficiency in a leading manufacturing firm.
Dynamic professional with expertise in managing cross-functional teams and improving quality control measures, aiming to contribute to a manufacturing organization committed to excellence and innovation.
Strategic thinker with a track record of reducing operational costs and enhancing product quality, looking to utilize data-driven decision-making skills to drive sustainable growth in a forward-thinking manufacturing environment.
Why these are strong objectives:
These objectives are impactful because they clearly articulate the candidate's experience, specialized skills, and goals for the future role. They highlight specific achievements, such as optimizing production processes and reducing costs, which demonstrate the candidate's value to potential employers. Additionally, they align the candidate's aspirations with the needs of the manufacturing organization, indicating a mutual benefit. This clarity and focus make the objectives compelling and indicative of the candidate's readiness to contribute effectively.
Lead/Super Experienced level
Sure! Here are five strong resume objective examples tailored for a lead or super experienced manufacturing manager:
Results-Driven Leader: Accomplished manufacturing manager with over 15 years of experience in optimizing production processes, reducing costs, and increasing efficiency. Seeking to leverage my expertise in Lean Six Sigma methodologies to drive continuous improvement and operational excellence in a forward-thinking organization.
Strategic Operations Expert: Highly experienced manufacturing professional with a proven track record of leading cross-functional teams and managing high-volume production environments. Aiming to apply my strategic leadership skills and data-driven decision-making to elevate productivity and support company growth.
Transformational Change Agent: Dynamic manufacturing manager with a focus on transforming operational capabilities through innovative technology implementation and employee engagement. Eager to utilize my skills in change management and process optimization to enhance overall performance in a challenging industry setting.
Safety and Quality Champion: Dedicated manufacturing manager with over 20 years of experience in fostering safety and quality excellence within production teams. Seeking to contribute my expertise in compliance management and quality assurance to ensure exceptional standards in a reputable manufacturing company.
Visionary Leader in Manufacturing Technologies: Forward-thinking manufacturing manager with extensive experience in implementing advanced manufacturing technologies and automation solutions. Looking to leverage my knowledge of Industry 4.0 to lead initiatives that enhance production efficiency and drive competitive advantage.
Senior level
Here are five strong resume objective examples suitable for a senior-level manufacturing manager:
Results-Driven Leader: Highly accomplished manufacturing manager with over 15 years of experience in optimizing production processes and improving efficiency. Seeking to leverage extensive operational expertise to drive high-performance manufacturing initiatives at [Company Name].
Strategic Innovator: Senior manufacturing professional with a proven track record of implementing lean manufacturing principles and reducing operational costs by up to 25%. Aiming to contribute to [Company Name] by fostering a culture of continuous improvement and operational excellence.
Cross-Functional Collaborator: Dynamic manufacturing manager skilled in leading cross-functional teams to achieve strategic manufacturing goals. Eager to bring a strong background in quality control and supply chain management to enhance productivity and ensure superior product delivery at [Company Name].
Quality-Focused Visionary: Experienced in spearheading quality assurance programs and driving compliance with industry standards, I am passionate about delivering innovative solutions that enhance product reliability. Seeking an opportunity at [Company Name] to elevate quality standards and operational performance.
Change Agent in Manufacturing: Dedicated manufacturing manager with a robust background in driving transformation initiatives across diverse production environments. Looking to apply expertise in workforce development and technology integration to optimize manufacturing operations at [Company Name].
Mid-Level level
Here are five strong resume objective examples for a mid-level manufacturing manager:
Results-Driven Leader: Accomplished manufacturing manager with over 5 years of experience in optimizing production processes. Seeking to leverage expertise in lean manufacturing to enhance operational efficiency and drive cost reduction in a dynamic manufacturing environment.
Quality Assurance Advocate: Detail-oriented manufacturing manager skilled in implementing quality control processes and procedures. Aiming to utilize my background in Six Sigma methodologies to ensure product excellence and increase customer satisfaction in a growing manufacturing firm.
Team Development Focus: Dynamic manufacturing manager with a proven ability to lead and develop cross-functional teams. Looking to apply my skills in employee training and staff management to foster a culture of continuous improvement and innovation in a reputable manufacturing organization.
Strategic Operations Specialist: Mid-level manufacturing manager with a strong track record in supply chain optimization and inventory management. Eager to contribute to operational strategy development and execution to drive higher efficiency and productivity levels for a forward-thinking company.
Technology Integration Expert: Forward-thinking manufacturing manager with extensive experience in integrating advanced manufacturing technologies and automation. Seeking to enhance operational capabilities and streamline production processes in a progressive manufacturing environment.
Junior level
Here are five strong resume objective examples for a Junior Manufacturing Manager position:
Aspiring Manufacturing Manager: Results-driven professional with over two years of experience in production supervision and process optimization, seeking to leverage strong leadership skills and a passion for quality control to drive efficiency and enhance productivity in a dynamic manufacturing environment.
Dedicated Production Coordinator: Motivated individual with hands-on experience in assembly line operations and team collaboration, aiming to contribute to a progressive manufacturing company by applying effective problem-solving skills and a commitment to continuous improvement.
Manufacturing Process Enthusiast: Entry-level manufacturing professional with a strong foundation in Lean manufacturing principles and safety practices, looking to advance to a Junior Manufacturing Manager role to implement innovative processes and support team growth while exceeding production targets.
Detail-oriented Manufacturing Graduate: Recent graduate with internship experience in manufacturing operations and project management, seeking to utilize analytical skills and a proactive approach to enhance production workflows and uphold quality standards in a supportive management position.
Emerging Production Leader: Passionate about manufacturing and committed to team success, with a background in managing small teams and conducting performance analysis, looking to further develop managerial skills while contributing to high-quality production output in an established manufacturing facility.
Entry-Level level
Sure! Here are five strong resume objective examples for an entry-level manufacturing manager position:
Entry-Level Manufacturing Manager Resume Objectives:
Driven Recent Graduate
Energetic and detail-oriented recent graduate with a degree in Industrial Engineering, seeking to leverage strong analytical skills and passion for manufacturing to contribute to process improvement and efficiency as an entry-level Manufacturing Manager.Proactive Team Player
Motivated and organized individual with hands-on experience in lean manufacturing techniques, aiming to join a dynamic manufacturing team to help optimize workflows and enhance production schedules while fostering a collaborative team environment.Aspiring Manufacturing Leader
Ambitious individual with a solid foundation in production management principles, eager to apply academic knowledge and internship experience to drive operational excellence and contribute to team success in an entry-level Manufacturing Manager role.Detail-Oriented Problem Solver
Focused entry-level professional with a keen eye for detail and strong problem-solving skills, seeking to enhance manufacturing processes and improve productivity through innovative leadership and effective resource management.Passionate About Process Improvement
Enthusiastic and tech-savvy recent graduate dedicated to utilizing advanced data analysis skills and a passion for efficiency to implement best practices and drive continuous improvement initiatives as an entry-level Manufacturing Manager.
Weak Resume Objective Examples
Weak Resume Objective Examples for a Manufacturing Manager:
"Seeking a management position in a manufacturing company to utilize my skills and experience."
"Aiming for a manufacturing manager role to improve production processes and make the company better."
"To obtain a manufacturing manager position where I can apply my knowledge and help the business grow."
Reasons Why These Objectives Are Weak:
Lack of Specificity: All three objectives are vague and do not specify what particular skills, experiences, or achievements the candidate brings to the table. Instead of highlighting unique qualifications, they offer generic aspirations that could apply to any candidate.
Passive Language: The use of phrases like "seeking" and "aiming for" suggests a passive approach rather than an assertive commitment to drive results for the company. Strong objectives should convey confidence and emphasize direct contributions the candidate can make.
Focus on Self Rather Than Employer: These objectives focus primarily on what the candidate seeks instead of demonstrating what they can offer to the employer. A more effective objective would identify specific ways the candidate's expertise aligns with the company’s goals and needs, such as improving efficiency, reducing costs, or enhancing product quality.
In summary, an effective resume objective for a manufacturing manager should be specific, assertive, and focused on the value they bring to the organization.
Creating an effective work experience section for a manufacturing manager's resume demands a focus on relevant skills, achievements, and responsibilities that showcase your qualifications. Here’s a guideline to help you craft this section:
Use a Clear Format: Begin with the job title, company name, location, and dates of employment. Use bullet points for easy readability, focusing on your accomplishments rather than just responsibilities.
Highlight Relevant Experience: Tailor your entries to highlight roles in manufacturing, production management, operations, or similar fields. The experiences should directly relate to the skills needed for a manufacturing manager.
Emphasize Achievements: Quantify your achievements wherever possible. Use metrics such as percentage improvements in productivity, cost reductions, or safety incident reductions. For example, "Reduced production costs by 15% through process optimization" or "Increased production efficiency by 20% by implementing lean manufacturing techniques."
Showcase Leadership Skills: As a manufacturing manager, you’ll lead teams, so highlight your leadership experience. Discuss how you managed teams, resolved conflicts, or mentored staff. For instance, "Led a cross-functional team of 30 in a successful plant restructuring project that improved workflow efficiency."
Focus on Relevant Skills and Technologies: Mention any specific manufacturing methodologies (such as Lean, Six Sigma), tools, or technologies (like ERP systems) you’ve implemented or worked with. For example, "Implemented a new ERP system that streamlined inventory management, reducing stock discrepancies by 30%."
Professional Development: If applicable, include any relevant certifications or training you've received, such as Lean Certification or Project Management Professional (PMP).
Remember to keep the descriptions concise and impactful, highlighting how your experience aligns with the expectations of a manufacturing manager role. Tailoring each entry to the job description will significantly enhance your appeal to potential employers.
Best Practices for Your Work Experience Section:
Certainly! Here are 12 best practices for crafting an effective Work Experience section on a resume for a manufacturing manager:
Tailor Your Bullet Points: Customize your experience to match the job description, emphasizing relevant skills and accomplishments that align with the specific manufacturing manager role you’re applying for.
Use Action Verbs: Start each bullet point with strong action verbs such as "Implemented," "Led," "Optimized," or "Streamlined" to convey your contributions effectively.
Quantify Achievements: Wherever possible, include specific metrics, percentages, or dollar amounts to illustrate the impact of your work (e.g., “Increased production efficiency by 15%”).
Focus on Leadership: Highlight your leadership capabilities by detailing your experience managing teams, conducting training, and developing staff to foster a productive work environment.
Emphasize Cost Savings: Showcase initiatives you’ve led that resulted in significant cost reductions or improved profitability within the manufacturing process.
Highlight Process Improvements: Describe your role in optimizing manufacturing processes, implementing Lean methodologies, or achieving Six Sigma certification, if applicable.
Showcase Safety Records: Include your experience in promoting workplace safety and compliance with regulations, emphasizing any improvements in safety metrics or certifications obtained.
Mention Technology and Automation: Detail your experience with automation, new technologies, or production management software relevant to the manufacturing sector.
Demonstrate Problem-Solving Skills: Provide examples of complex problems you’ve successfully addressed in manufacturing settings, showcasing your analytical and troubleshooting abilities.
Include Cross-Functional Collaboration: Illustrate your experience working with other departments (e.g., quality assurance, supply chain, R&D) to achieve manufacturing goals.
Outline Project Management Experience: Highlight any significant projects you have managed, detailing your roles, outcomes, and any improvements to timelines or quality.
Keep it Concise and Relevant: Limit your bullet points to the most relevant roles and achievements, focusing on the last 10-15 years of your career to maintain a concise and impactful section.
These best practices can help ensure your Work Experience section stands out and effectively communicates your qualifications as a manufacturing manager.
Strong Resume Work Experiences Examples
Resume Work Experience Examples for a Manufacturing Manager
Optimized Production Processes:
Led a cross-functional team in redesigning the production workflow, resulting in a 20% increase in efficiency and a 15% reduction in waste over a 12-month period.Team Leadership and Training:
Managed a team of 50+ employees, implementing a comprehensive training program that improved employee performance metrics by 30% and significantly reduced turnover rates.Budget Management and Cost Reduction:
Successfully managed a $5 million annual budget, negotiating with suppliers to achieve a 10% cost reduction while maintaining the quality of materials, contributing to improved profit margins.
Why These are Strong Work Experiences
Quantifiable Results:
Each bullet point includes specific, quantifiable achievements that demonstrate the candidate's ability to deliver measurable improvements. This shows potential employers the direct impact of the candidate's actions.Leadership and Collaboration:
The experiences highlight leadership capabilities and the ability to work effectively with diverse teams. Leadership is a vital quality for a manufacturing manager, as they often need to drive team performance and efficiency.Financial Acumen:
Mentioning budget management and cost reduction shows the candidate's financial awareness and ability to contribute to the company's bottom line. Employers highly value this capability, as it aligns with their goals to maximize profits while minimizing costs.
Lead/Super Experienced level
Sure! Here are five strong resume work experience examples tailored for a Lead/Super Experienced Manufacturing Manager position:
Oversaw Operational Efficiency: Led a team of 50+ employees in a high-volume automotive manufacturing facility, implementing lean manufacturing principles that increased production efficiency by 30% while reducing waste by 25% over two years.
Strategic Project Management: Managed the successful launch of three new product lines, coordinating cross-functional teams and ensuring adherence to timelines and budgets, resulting in a 15% increase in annual revenue.
Quality Assurance Leadership: Developed and enforced stringent quality control protocols that reduced defects by 40%, ultimately enhancing customer satisfaction and increasing repeat business.
Cost Reduction Initiatives: Spearheaded an initiative to optimize the supply chain process, negotiating contracts that decreased material costs by 20% annually while maintaining product quality and delivery times.
Continuous Improvement Champion: Fostered a culture of continuous improvement through training and mentorship programs, empowering employees to identify and implement process improvements that contributed to operational savings of $500,000 per year.
Senior level
Here are five bullet point examples of strong work experiences for a Senior Manufacturing Manager:
Led the optimization of production processes in a high-volume manufacturing facility, resulting in a 20% increase in operational efficiency and a 15% reduction in production costs over two years.
Implemented Lean Manufacturing principles that streamlined workflows and reduced waste by 25%, directly contributing to enhanced product quality and improved delivery timelines.
Managed cross-functional teams of over 100 employees, fostering a culture of collaboration and continuous improvement, which improved employee retention rates by 30% and enhanced overall team performance.
Spearheaded the introduction of advanced manufacturing technologies, including automation and robotics, which accelerated production capabilities and reduced cycle times by 40% while maintaining rigorous safety and quality standards.
Developed and executed strategic production plans aligned with organizational goals, successfully navigating through supply chain disruptions while maintaining a 98% on-time delivery rate and exceeding customer satisfaction targets.
Mid-Level level
Sure! Here are five bullet points that showcase strong work experience examples for a Mid-Level Manufacturing Manager:
Process Optimization: Led a cross-functional team in the implementation of Lean manufacturing techniques, resulting in a 15% reduction in production cycle time and a 10% decrease in material waste over one year.
Team Leadership: Supervised a team of 25 production staff, fostering a culture of safety and continuous improvement that achieved a 20% reduction in workplace incidents while enhancing overall team productivity through targeted training programs.
Budget Management: Managed an annual budget of $1.5 million for manufacturing operations, successfully identifying cost-saving opportunities that led to a 12% reduction in expenses without compromising product quality.
Quality Assurance: Developed and enforced stringent quality control measures that improved product reliability by 30%, achieving a customer satisfaction rating of over 95% for three consecutive quarters.
Project Management: Led a major facility upgrade project that involved the installation of new machinery and technology, which enhanced production capacity by 25% and improved operational efficiency within a six-month timeline.
Junior level
Certainly! Here are five bullet points that highlight strong work experiences for a junior-level manufacturing manager:
Process Improvement Initiatives: Spearheaded initiatives that streamlined production workflows, reducing processing time by 15% and increasing overall efficiency in the manufacturing line.
Team Collaboration: Worked closely with cross-functional teams to implement new manufacturing strategies, leading to a 10% decrease in material waste and an improvement in product quality.
Safety Compliance and Training: Assisted in developing and conducting safety training programs for production staff, achieving a 20% reduction in workplace accidents over one year.
Production Scheduling: Supported the planning and scheduling of production runs, ensuring optimal utilization of resources and meeting production targets consistently.
Inventory Management: Helped maintain accurate inventory levels through regular audits and reporting, contributing to a 25% reduction in holding costs while ensuring the timely availability of materials.
Entry-Level level
Here are five bullet points exemplifying strong resume work experiences for an entry-level manufacturing manager:
Quality Control Initiatives: Assisted in the implementation of quality control processes, resulting in a 15% reduction in defect rates during production, demonstrating a commitment to maintaining high standards in manufacturing operations.
Lean Manufacturing Projects: Collaborated with senior management on lean manufacturing projects, successfully identifying waste reduction opportunities that improved operational efficiency by 10%, and fostered a culture of continuous improvement.
Team Leadership: Led a cross-functional team of 5 on a time-sensitive project, coordinating tasks effectively to meet production deadlines and enhancing team collaboration, ultimately achieving a 20% increase in output.
Production Scheduling: Supported the creation of efficient production schedules using resource allocation and demand forecasting, optimizing workflow and reducing downtime by 12% over three months.
Safety Compliance: Assisted in enforcing safety protocols and training new staff on best practices, contributing to a 30% decrease in workplace accidents and reinforcing a culture of safety within the manufacturing environment.
Weak Resume Work Experiences Examples
Weak Resume Work Experience Examples for Manufacturing Manager
Assembly Line Supervisor at XYZ Corp. (June 2019 - March 2020)
- Oversaw daily operations of the assembly line and ensured that tasks were completed.
- Trained new employees on standard operating procedures and basic manufacturing processes.
- Maintained inventory of supplies and reported shortages to management.
Production Assistant at ABC Manufacturing (January 2018 - May 2019)
- Assisted in the assembly of products and operated machinery under supervision.
- Kept the work area clean and organized to promote safety and efficiency.
- Helped with basic troubleshooting of equipment under guidance.
Quality Control Trainee at DEF Industries (August 2017 - December 2017)
- Observed and documented quality control processes while learning from senior staff.
- Conducted basic inspections of finished products and reported findings.
- Participated in team meetings and provided input on process improvements.
Why These Work Experiences Are Weak
Limited Responsibilities: Each example reflects roles with minimal decision-making authority or leadership responsibilities. A manufacturing manager role typically requires strong leadership skills, strategic planning, and the ability to drive improvements in production processes. These experiences do not demonstrate such capabilities.
Lack of Demonstrated Impact: The examples provided do not showcase any quantifiable achievements or contributions to the organization. For a manufacturing manager position, it's important to illustrate how one's actions led to improvements in efficiency, cost reductions, or enhanced team performance.
Focus on Basic Tasks: The highlighted experiences center on entry-level tasks (e.g., assisting, observing, and basic training) rather than on advanced manufacturing principles or methodologies (like Lean, Six Sigma, or process optimization). A manufacturing manager should have a background that includes strategic oversight, process design, and team management rather than merely performing operational tasks.
Top Skills & Keywords for Manufacturing Operations Manager Resumes:
When crafting a manufacturing manager resume, emphasize key skills and relevant keywords to stand out. Highlight leadership abilities like "team management" and "cross-functional collaboration." Include technical skills such as "Lean Manufacturing," "Six Sigma," and "Quality Control" to showcase process improvement expertise. Mention "Supply Chain Management," "Production Planning," and "Inventory Management" to demonstrate operational knowledge. Emphasize "Problem-Solving" and "Data Analysis" to illustrate your analytical skills. Incorporate keywords related to "Safety Compliance," "Cost Reduction," and "Continuous Improvement" to align with industry standards. Tailor your resume to reflect specific achievements and metrics that quantify your impact in previous roles.
Top Hard & Soft Skills for Manufacturing Operations Manager:
Hard Skills
Here’s a table with 10 hard skills for a manufacturing manager along with their descriptions:
Hard Skills | Description |
---|---|
Lean Manufacturing | A methodology focused on minimizing waste and maximizing productivity in manufacturing processes. |
Project Management | The practice of planning, executing, and closing projects effectively and efficiently. |
Six Sigma | A set of techniques and tools for process improvement aimed at reducing defects and variance. |
Quality Management Systems | Frameworks that help organizations ensure consistent quality in their products and services. |
Supply Chain Management | The management of the flow of goods and services, including all processes that transform raw materials into final products. |
Manufacturing Technology | Understanding the latest technologies and processes used in manufacturing to improve efficiency and quality. |
Production Planning | The process of organizing and scheduling manufacturing activities to meet customer demand effectively. |
Industrial Engineering | Applying engineering principles to optimize complex processes, systems, and organizations. |
Automation Systems | Knowledge of automated processes and systems used to enhance production efficiency and reliability. |
Health and Safety Regulations | Understanding industry-specific health and safety standards to ensure a safe working environment. |
This table offers a comprehensive overview of essential hard skills for a manufacturing manager along with their links and descriptions.
Soft Skills
Here’s a table with 10 soft skills relevant for a manufacturing manager along with their descriptions:
Soft Skills | Description |
---|---|
Leadership | The ability to guide and motivate a team towards achieving production goals and maintaining high morale. |
Communication | Effective verbal and written communication skills essential for conveying information clearly and concisely. |
Problem Solving | The capability to identify issues quickly and develop effective solutions to enhance operational efficiency. |
Teamwork | The skill to collaborate with various departments and foster a cooperative workplace environment. |
Adaptability | Flexibility to adjust strategies and approaches in response to changing production demands or challenges. |
Time Management | The ability to prioritize tasks effectively to ensure that production schedules are met. |
Critical Thinking | The skill to analyze situations logically and make informed decisions that benefit the organization. |
Conflict Resolution | The ability to address and resolve disputes among team members to maintain a harmonious work environment. |
Empowerment | Encouraging and enabling employees to take initiative and contribute effectively to the manufacturing process. |
Mentorship | The ability to guide and develop less experienced employees, fostering their growth and skills. |
Feel free to modify the table or descriptions as per your specific needs!
Elevate Your Application: Crafting an Exceptional Manufacturing Operations Manager Cover Letter
Manufacturing Operations Manager Cover Letter Example: Based on Resume
Dear [Company Name] Hiring Manager,
I am writing to express my interest in the Manufacturing Manager position at [Company Name]. With over eight years of experience in the manufacturing sector and a fervent passion for optimizing production processes, I am excited about the opportunity to contribute to your team.
Throughout my career, I have honed my technical skills, becoming proficient in industry-standard software such as AutoCAD, SolidWorks, and SAP. I successfully led a team of 20 at my previous employer, where I implemented lean manufacturing techniques that resulted in a 25% reduction in waste and a 30% increase in productivity. My technical expertise, combined with my strong analytical abilities, allows me to troubleshoot complex issues efficiently while maintaining a focus on quality and safety.
I am particularly proud of a project where I spearheaded the integration of a new manufacturing line that resulted in a 40% improvement in output without compromising product quality. This achievement was made possible through close collaboration with cross-functional teams, including engineering, quality assurance, and supply chain management. My collaborative work ethic has always fostered a positive environment, resulting in enhanced team cohesion and innovation.
At [Company Name], I am excited about the prospect of leveraging my experience to drive operational excellence and lead your team toward achieving strategic goals. I am committed to continuous improvement and believe that my proactive approach can facilitate the adoption of best practices in manufacturing processes.
I would welcome the opportunity to discuss in further detail how my unique blend of skills and experience can add value to your organization. Thank you for considering my application.
Best regards,
[Your Name]
[Your Email]
[Your Phone Number]
[Your LinkedIn Profile]
A compelling cover letter for a manufacturing manager position should effectively highlight your expertise, experience, and enthusiasm for the role. Here’s a guide to crafting a successful cover letter.
Essential Elements:
Header:
Include your name, contact information, and the date. Then, add the employer's name and address.Greeting:
Address the hiring manager by name, if possible. Use "Dear [Hiring Manager's Name]" or "Dear Hiring Committee".Introduction:
Start with a strong opening sentence stating the position you’re applying for and where you found the job listing. Express your enthusiasm for the role and the company.Relevant Experience:
Highlight your relevant experience in manufacturing management. Discuss your key responsibilities in previous roles, such as overseeing production processes, implementing quality control measures, or managing teams. Use specific examples to demonstrate your achievements, like improving production efficiency or reducing costs.Skills and Qualifications:
Mention key skills that align with the job description, such as knowledge of lean manufacturing principles, project management capabilities, or expertise in safety regulations. Tailor this section to reflect what is sought by the employer.Cultural Fit:
Research the company culture and values. Align your personal values and describe why you are a good fit. Highlight any experience you have with team collaboration or leadership that mirrors the company's culture.Closing:
Reiterate your enthusiasm for the position and state your eagerness to discuss your candidacy further. Invite them to contact you for an interview. Thank them for considering your application.Signature:
End with a professional closing such as "Sincerely" or "Best regards," followed by your name.
Crafting Your Cover Letter:
- Be Concise: Aim for one page, focusing on the most relevant information.
- Use Professional Language: Maintain a professional tone while letting your personality shine through.
- Proofread: Check for errors in spelling, grammar, or punctuation.
By following these guidelines, you’ll create a well-structured, engaging cover letter that showcases your qualifications for the manufacturing manager position.
Resume FAQs for Manufacturing Operations Manager:
How long should I make my Manufacturing Operations Manager resume?
When crafting a resume for a manufacturing manager position, a one to two-page length is ideal. The length depends on your experience and the relevance of the information to the job you're applying for. If you have extensive experience (10+ years), a two-page resume may be justified to encompass your accomplishments, leadership roles, and the technical skills that are pertinent to manufacturing.
Focus on quality over quantity. Highlight your most relevant achievements, skills, and experiences tailored to the job description. Start with a strong summary statement, followed by key skills, professional experience, and education. Use bullet points for clarity, emphasizing quantifiable results, such as cost reductions, efficiency improvements, and successfully completed projects.
Employers in the manufacturing sector value clarity and brevity, so make sure every line serves a purpose. Remove outdated or less relevant experiences, and avoid excessive details that could dilute your key qualifications. Lastly, ensure a clean layout with adequate white space for easy reading, which can enhance the presentation of your resume at a glance. In summary, aim for a concise, impactful resume that effectively showcases your capabilities as a manufacturing manager.
What is the best way to format a Manufacturing Operations Manager resume?
When formatting a resume for a manufacturing manager position, clarity and professionalism are key. Start with a concise header that includes your name, phone number, email address, and LinkedIn profile. Following this, a strong summary or objective statement should highlight your years of experience, key skills, and what you aim to achieve in your next role.
Organize the main sections clearly:
Core Competencies: List relevant skills (e.g., Lean manufacturing, Six Sigma, project management) in bullet points for easy skimming.
Professional Experience: Detail your past roles in reverse chronological order, emphasizing achievements and responsibilities. Use bullet points to describe specific contributions, focusing on quantifiable results (e.g., “Increased production efficiency by 20%”).
Education: Include your degrees, relevant certifications (e.g., PMP, Six Sigma Green Belt), and any specialized training in manufacturing.
Additional Sections: You may add sections for professional affiliations, awards, or relevant projects to showcase your commitment and expertise further.
Use a clean and professional font, maintaining consistent formatting for headings and bullet points. Limit your resume to one or two pages, ensuring that it is easy to read and visually appealing.
Which Manufacturing Operations Manager skills are most important to highlight in a resume?
When crafting a resume for a manufacturing manager position, it is essential to highlight key skills that demonstrate your capability to lead and optimize production processes effectively.
Firstly, leadership is paramount; showcasing your ability to manage teams, delegate tasks, and inspire a collaborative environment can set you apart. Next, emphasize process optimization skills, such as lean manufacturing or Six Sigma methodologies, to illustrate your expertise in enhancing efficiency and reducing waste.
Project management skills are also crucial, as they enable you to oversee multiple projects simultaneously, ensuring that timelines and budgets are met. Highlighting technical proficiencies, such as knowledge of manufacturing software (e.g., ERP systems) and equipment, can add value to your profile.
Moreover, problem-solving abilities reflect your capacity to troubleshoot and resolve issues swiftly, maintaining production flow. Include strong communication skills to convey complex information clearly, facilitating collaboration across departments.
Finally, showcase your understanding of safety and compliance regulations, signaling your commitment to maintaining a safe workplace. By presenting a well-rounded skill set that includes leadership, optimization, project management, technical knowledge, problem-solving, communication, and compliance, you will create a compelling resume that aligns with industry demands.
How should you write a resume if you have no experience as a Manufacturing Operations Manager?
Writing a resume for a manufacturing manager position without direct experience can be challenging, but it’s certainly possible to highlight your relevant skills and background effectively. Start with a strong objective statement that conveys your enthusiasm and highlights transferable skills. Focus on soft skills such as leadership, problem-solving, and communication, which are critical in manufacturing environments.
Next, emphasize your education, particularly any degrees, certifications, or courses related to manufacturing, engineering, or management. If you have project experience from coursework or internships, outline these in a section titled "Relevant Projects" or "Academic Projects." Describe your role, the skills utilized, and the outcomes.
Additionally, consider including any supervisory or team-oriented roles, even in non-manufacturing settings. This demonstrates your ability to manage people and processes.
A section for relevant skills can showcase technical skills, such as familiarity with manufacturing processes, quality control, or software tools like ERP systems.
Finally, if applicable, include volunteer experiences, emphasizing leadership or management aspects to further demonstrate your capability. Tailor your resume to emphasize how these experiences prepare you for a manufacturing manager role, presenting yourself as a capable candidate eager to learn and grow in the field.
Professional Development Resources Tips for Manufacturing Operations Manager:
null
TOP 20 Manufacturing Operations Manager relevant keywords for ATS (Applicant Tracking System) systems:
Sure! Below is a table with 20 relevant keywords for a manufacturing manager's resume, along with descriptions to help explain their significance in the context of manufacturing management.
Keyword | Description |
---|---|
Lean Manufacturing | A methodology that focuses on minimizing waste within manufacturing systems without sacrificing productivity. |
Six Sigma | A data-driven approach to improve quality by identifying and removing causes of defects. |
Process Optimization | Techniques used to improve the efficiency of manufacturing processes and workflows. |
Quality Control | Practices designed to ensure that manufacturing processes and outputs meet certain standards. |
Supply Chain Management | The management of the flow of goods and services from procurement to delivery. |
Continuous Improvement | Ongoing efforts to enhance products, services, or processes through incremental improvements. |
Production Planning | The management process of establishing production targets and schedules to meet demands. |
Equipment Maintenance | Strategies to maintain machinery and equipment to ensure high performance and minimize downtime. |
Safety Compliance | Adhering to safety regulations and standards to ensure a safe working environment for employees. |
Cost Reduction | Strategies aimed at lowering production costs while maintaining quality and output levels. |
Inventory Management | The supervision of non-capitalized assets (inventory) and stock items to reduce waste and optimize capital. |
Workforce Training | Developing staff skills and knowledge to enhance productivity and efficiency on the production floor. |
Project Management | The application of skills, tools, and techniques to meet project requirements within a manufacturing context. |
Resource Allocation | Efficiently distributing and managing physical, human, and financial resources within manufacturing operations. |
Kaizen | A Japanese term meaning "change for better," representing continuous improvement in manufacturing processes. |
Just-In-Time (JIT) | Inventory strategy aimed at reducing holding costs and increasing efficiency by receiving goods only as they are needed. |
Collaboration | Working effectively with cross-functional teams and stakeholders to achieve common goals in manufacturing. |
Regulatory Compliance | Abiding by laws, regulations, and standards that govern manufacturing processes and practices. |
Data Analysis | The process of inspecting and interpreting data to make informed decisions on manufacturing efficiency and quality improvement. |
Performance Metrics | Tools used to evaluate the success and efficiency of manufacturing operations against key performance indicators (KPIs). |
Incorporating these keywords into your resume will help align your skills and experiences with what hiring managers in the manufacturing sector are looking for, and it will improve your chances of passing the Applicant Tracking System (ATS).
Sample Interview Preparation Questions:
Can you describe your experience with lean manufacturing techniques and how you have implemented them in previous roles?
How do you prioritize production schedules in a high-demand environment while ensuring quality standards are met?
What strategies do you use to manage and motivate a diverse team on the manufacturing floor?
How do you approach problem-solving when faced with unexpected production delays or equipment failures?
Can you provide an example of a successful process improvement initiative you led and the measurable outcomes it produced?
Related Resumes for Manufacturing Operations Manager:
Generate Your NEXT Resume with AI
Accelerate your resume crafting with the AI Resume Builder. Create personalized resume summaries in seconds.