Quality Control Specialist Resume Examples for 2024 Success
---
### Sample 1
- **Position number:** 1
- **Person:** 1
- **Position title:** Quality Assurance Technician
- **Position slug:** quality-assurance-technician
- **Name:** Sarah
- **Surname:** Johnson
- **Birthdate:** 1988-05-12
- **List of 5 companies:** Pfizer, Johnson & Johnson, Merck, Novartis, AstraZeneca
- **Key competencies:** Inspection techniques, Regulatory compliance, Quality documentation, Root cause analysis, Statistical process control
---
### Sample 2
- **Position number:** 2
- **Person:** 2
- **Position title:** Quality Control Analyst
- **Position slug:** quality-control-analyst
- **Name:** Jason
- **Surname:** Lee
- **Birthdate:** 1990-08-25
- **List of 5 companies:** Coca-Cola, PepsiCo, Unilever, Nestlé, Kraft Heinz
- **Key competencies:** Data analysis, Risk assessment, Quality auditing, FDA regulations, Performance metrics
---
### Sample 3
- **Position number:** 3
- **Person:** 3
- **Position title:** Quality Assurance Inspector
- **Position slug:** quality-assurance-inspector
- **Name:** Emily
- **Surname:** Sanchez
- **Birthdate:** 1995-01-30
- **List of 5 companies:** Boeing, Lockheed Martin, Raytheon, Northrop Grumman, General Dynamics
- **Key competencies:** Technical inspection, ISO standards, Attention to detail, Testing methodologies, Regulatory standards
---
### Sample 4
- **Position number:** 4
- **Person:** 4
- **Position title:** Quality Compliance Coordinator
- **Position slug:** quality-compliance-coordinator
- **Name:** David
- **Surname:** Patel
- **Birthdate:** 1984-11-14
- **List of 5 companies:** GE Healthcare, Siemens, Philips Healthcare, Canon Medical, Medtronic
- **Key competencies:** Compliance audits, Quality management systems, Documentation control, Problem solving, Training and development
---
### Sample 5
- **Position number:** 5
- **Person:** 5
- **Position title:** Quality Improvement Specialist
- **Position slug:** quality-improvement-specialist
- **Name:** Amanda
- **Surname:** Robinson
- **Birthdate:** 1992-04-21
- **List of 5 companies:** Mayo Clinic, Cleveland Clinic, Johns Hopkins Hospital, Texas Medical Center, Massachusetts General Hospital
- **Key competencies:** Process optimization, Performance improvement, Data interpretation, Change management, Patient safety standards
---
### Sample 6
- **Position number:** 6
- **Person:** 6
- **Position title:** Quality Systems Analyst
- **Position slug:** quality-systems-analyst
- **Name:** Mark
- **Surname:** Thompson
- **Birthdate:** 1987-09-18
- **List of 5 companies:** Intel, AMD, NVIDIA, Texas Instruments, Qualcomm
- **Key competencies:** System analysis, Quality assurance methodologies, Risk management, Statistical analysis tools, Software validation
---
Feel free to make any modifications or specify further details for each position!
---
### Sample 1
**Position number:** 1
**Position title:** Quality Control Inspector
**Position slug:** quality-control-inspector
**Name:** Jane
**Surname:** Smith
**Birthdate:** 1985-05-12
**List of 5 companies:** Apple, Intel, Samsung, LG, Sony
**Key competencies:** Attention to detail, analytical skills, proficiency in quality control software, understanding of quality assurance standards, problem-solving abilities
---
### Sample 2
**Position number:** 2
**Position title:** Quality Assurance Technician
**Position slug:** quality-assurance-technician
**Name:** Alex
**Surname:** Johnson
**Birthdate:** 1990-03-22
**List of 5 companies:** Dell, Microsoft, HP, IBM, Cisco
**Key competencies:** Technical proficiency in testing methodologies, strong communication skills, experience with automation testing tools, knowledge of ISO standards, teamwork and collaboration
---
### Sample 3
**Position number:** 3
**Position title:** Quality Control Analyst
**Position slug:** quality-control-analyst
**Name:** Maria
**Surname:** Garcia
**Birthdate:** 1988-11-09
**List of 5 companies:** Google, Amazon, Facebook, Oracle, Tesla
**Key competencies:** Data analysis, statistical process control, report generation, critical thinking, project management
---
### Sample 4
**Position number:** 4
**Position title:** Quality Improvement Specialist
**Position slug:** quality-improvement-specialist
**Name:** David
**Surname:** Thompson
**Birthdate:** 1986-07-14
**List of 5 companies:** Pfizer, Johnson & Johnson, Roche, Merck, Novartis
**Key competencies:** Lean Six Sigma methodologies, training and coaching skills, process mapping, root cause analysis, customer service orientation
---
### Sample 5
**Position number:** 5
**Position title:** Regulatory Quality Control Specialist
**Position slug:** regulatory-quality-control-specialist
**Name:** Sarah
**Surname:** Lee
**Birthdate:** 1992-02-25
**List of 5 companies:** Bayer, AstraZeneca, GlaxoSmithKline, Amgen, Biogen
**Key competencies:** Regulatory compliance understanding, strong documentation skills, experience with GxP regulations, risk assessment capabilities, cross-functional teamwork
---
### Sample 6
**Position number:** 6
**Position title:** Quality Control Supervisor
**Position slug:** quality-control-supervisor
**Name:** Michael
**Surname:** Brown
**Birthdate:** 1980-10-30
**List of 5 companies:** Coca-Cola, Nestlé, Procter & Gamble, Kraft Heinz, Unilever
**Key competencies:** Leadership and mentoring skills, quality audits, SOP writing, performance metrics tracking, conflict resolution
---
Feel free to tailor these samples further to fit specific needs or additional details!
Quality Control Specialist Resume Examples: 6 Top Formats to Use
We are seeking a dynamic Quality Control Specialist with a proven track record of leading quality initiatives to enhance product integrity and compliance. With expertise in data analysis and process optimization, you have successfully reduced defect rates by 30% through implementing robust quality management systems. Your collaborative approach fosters strong cross-functional relationships, driving team alignment on quality standards and best practices. As a mentor, you conduct engaging training sessions that empower team members to uphold excellence in quality assurance, creating a culture of continuous improvement that has significantly elevated production outcomes and customer satisfaction.
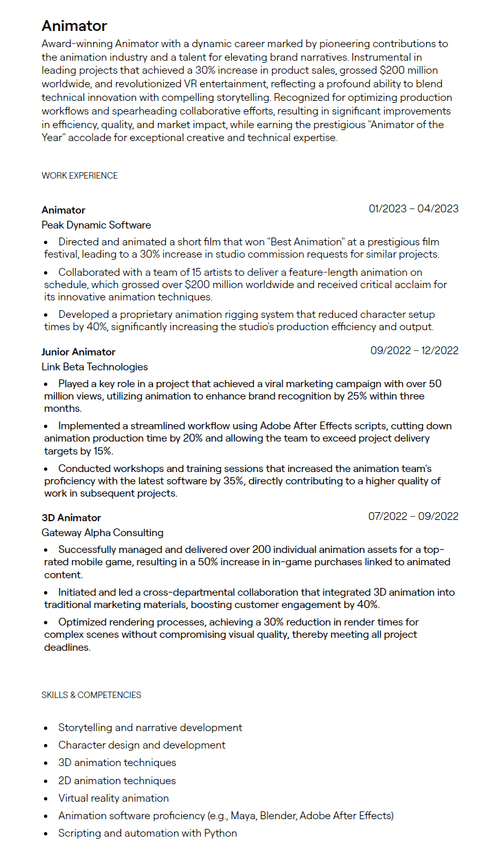
A quality control specialist plays a pivotal role in ensuring products meet rigorous standards of quality and safety, safeguarding both consumer satisfaction and company reputation. This position demands a keen eye for detail, analytical skills, and an understanding of manufacturing processes, alongside strong communication abilities for collaborating with cross-functional teams. To secure a job as a quality control specialist, candidates should pursue relevant education in engineering or quality management, obtain certifications such as Six Sigma or ASQ, and gain hands-on experience through internships or entry-level positions in quality assurance to demonstrate their commitment and expertise in the field.
Common Responsibilities Listed on Quality Control Specialist Resumes:
Here are 10 common responsibilities typically listed on resumes for quality control specialists:
Conducting Inspections: Performing regular inspections of materials, products, and processes to ensure compliance with quality standards.
Data Analysis: Analyzing quality data to identify trends, defects, and areas for improvement.
Developing Quality Standards: Establishing and maintaining quality control processes and protocols to meet industry regulations and company policies.
Documenting Findings: Preparing detailed reports on inspection results and quality control activities for management review.
Training Staff: Educating team members on quality standards, procedures, and best practices to promote a quality-centric culture.
Implementing Corrective Actions: Identifying non-conformances and developing and executing corrective and preventive action plans.
Collaborating with Departments: Working closely with production, engineering, and supply chain teams to resolve quality issues and enhance overall product quality.
Conducting Audits: Performing internal quality audits to assess compliance with established quality standards and identify areas for improvement.
Reviewing Product Specifications: Ensuring that product specifications and quality criteria align with customer requirements and industry standards.
Utilizing Quality Control Tools: Employing statistical process control (SPC) and other quality control methodologies to monitor and improve production processes.
When crafting a resume for the Quality Control Inspector position, it's crucial to emphasize attention to detail and analytical skills, as these are vital for accurately assessing product quality. Highlight proficiency in quality control software and a strong understanding of quality assurance standards, showcasing any relevant certifications. Problem-solving abilities should also be underscored, demonstrating the capability to identify and rectify quality issues efficiently. Additionally, mention experience with well-respected companies in the industry to enhance credibility and convey familiarity with high-quality standards. Finally, consider including specific achievements or metrics that illustrate past successes in quality control roles.
[email protected] • +1234567890 • https://www.linkedin.com/in/janesmith • https://twitter.com/janesmith
Detail-oriented Quality Control Inspector with extensive experience in leading tech companies such as Apple and Intel. Proficient in utilizing advanced quality control software and established quality assurance standards to enhance product reliability. Demonstrates exceptional analytical and problem-solving skills to identify issues and implement effective solutions. Proven track record of performing thorough inspections, ensuring adherence to specifications, and enhancing overall operational efficiency. Committed to upholding high-quality standards in fast-paced environments while fostering a culture of continuous improvement. Seeking to leverage expertise in quality control to contribute to a dynamic team focused on excellence.
WORK EXPERIENCE
- Conducted thorough inspections of products to ensure compliance with quality standards, reducing defects by 20%.
- Utilized advanced quality control software for tracking and reporting issues, enhancing team efficiency.
- Collaborated with cross-functional teams to implement corrective actions that led to a 15% increase in production yield.
- Trained new employees on quality assurance processes, contributing to a smoother onboarding experience.
- Developed detailed inspection reports that were utilized in quarterly management reviews.
- Led the quality assurance team in identifying and mitigating risks, improving overall product reliability.
- Played a key role in the transition to new quality assurance standards that aligned with industry best practices.
- Achieved a 30% reduction in inspection times through process optimization and efficient resource allocation.
- Participated in audits and inspections by regulatory bodies, maintaining a 100% compliance rating.
- Fostered a culture of quality among peers through effective communication and leadership skills.
- Oversaw a team of quality inspectors, implementing training programs that improved team performance by 25%.
- Streamlined the quality inspection process, reducing average inspection duration by 15% without compromising quality.
- Developed and maintained Standard Operating Procedures (SOPs) to ensure adherence to internal and external quality standards.
- Worked with suppliers to enhance product quality at the source, leading to a reduction in incoming defects.
- Championed the initiative to utilize data analysis for identifying recurring quality issues, resulting in proactive improvements.
SKILLS & COMPETENCIES
Sure! Here are 10 skills for Jane Smith, the Quality Control Inspector:
- Attention to detail
- Analytical skills
- Proficiency in quality control software
- Understanding of quality assurance standards
- Problem-solving abilities
- Knowledge of inspection techniques
- Ability to conduct audits and assessments
- Strong communication skills
- Time management and organization
- Team collaboration and support
COURSES / CERTIFICATIONS
Here is a list of 5 certifications and complete courses for Jane Smith, the Quality Control Inspector from Sample 1:
Certified Quality Inspector (CQI)
Issued by: American Society for Quality (ASQ)
Date: June 2019ISO 9001:2015 Lead Auditor Training
Provider: PECB
Date: September 2020Statistical Quality Control (SQC) Course
Provider: Coursera
Date: March 2021Six Sigma Green Belt Certification
Issued by: International Association for Six Sigma Certification (IASSC)
Date: November 2022Quality Control Fundamentals
Provider: Udemy
Date: January 2023
EDUCATION
Education for Jane Smith (Quality Control Inspector)
Bachelor of Science in Quality Assurance
University of California, Berkeley
Graduated: May 2007Certified Quality Inspector (CQI)
American Society for Quality (ASQ)
Obtained: June 2010
When crafting a resume for the Quality Assurance Technician position, it's crucial to highlight technical proficiency in various testing methodologies and experience with automation testing tools. Strong communication skills should be emphasized, indicating an ability to collaborate effectively with team members. Knowledge of ISO standards is essential, showcasing familiarity with industry regulations and practices. Additionally, emphasize any relevant teamwork and collaboration experiences that demonstrate the ability to work in a dynamic environment. Tailoring achievements and skills to directly reflect the responsibilities of the role will enhance the resume's effectiveness in capturing attention.
[email protected] • +1-234-567-8901 • https://www.linkedin.com/in/alexjohnson • https://twitter.com/alexjohnson
**Summary for Alex Johnson, Quality Assurance Technician:**
Detail-oriented and technically proficient Quality Assurance Technician with extensive experience across leading tech companies, including Dell and Microsoft. Adept in testing methodologies and a strong communicator, Alex excels in collaborating with cross-functional teams to ensure high-quality deliverables. Proficient in automation testing tools and knowledgeable about ISO standards, he effectively optimizes processes to enhance product quality. With a demonstrated ability to adapt to dynamic environments and a commitment to excellence, Alex is poised to drive continuous improvement in quality assurance practices.
WORK EXPERIENCE
- Led the implementation of automated testing protocols, resulting in a 30% decrease in testing time while maintaining product quality.
- Collaborated with software development teams to enhance product functionality, leading to a 20% increase in customer satisfaction scores.
- Conducted training sessions for new hires on quality assurance processes, improving team proficiency by 15%.
- Assessed and refined existing testing methodologies, resulting in a 10% reduction in product defects through improved detection processes.
- Played a vital role in achieving ISO 9001 certification for the quality department, aligning company processes with international standards.
- Implemented a regression testing strategy that reduced the number of post-release defects by 25%.
- Collaborated with cross-functional teams to launch a new product line, contributing to record-breaking sales in the first quarter.
- Utilized advanced quality metrics to track performance, resulting in data-driven decisions that improved product reliability.
- Facilitated a comprehensive review of quality standards, leading to an upgrade in practices that enhanced team efficiency by 18%.
- Recognized as 'Employee of the Month' three times for outstanding contributions to product quality and team collaboration.
- Developed and standardized quality assurance procedures that were adopted company-wide, increasing overall efficiency by 22%.
- Spearheaded a customer feedback initiative that directly influenced product design, improving user engagement by over 30%.
- Coordinated with product management to define quality metrics and drive continuous improvement initiatives across projects.
- Documented and communicated quality issues to stakeholders, successfully reducing product recalls by 15% year-over-year.
- Contributed to quarterly strategy meetings, influencing decision-making with detailed analysis of quality trends and potential improvements.
- Executed robust testing strategies that improved product performance metrics significantly across multiple projects.
- Championed the integration of machine learning techniques in quality assurance processes, enhancing defect detection rates by 40%.
- Mentored junior technicians, fostering a culture of continuous learning that led to higher team morale and productivity.
- Participated in ISO audits, resulting in commendations for maintaining high-quality standards.
- Initiated a monthly quality review program, facilitating collaborative discussions that drove innovation and improvement.
SKILLS & COMPETENCIES
Skills for Alex Johnson (Quality Assurance Technician)
- Proficient in automation testing tools (e.g., Selenium, QTP)
- Strong understanding of testing methodologies (e.g., unit, integration, and system testing)
- Excellent written and verbal communication skills
- Knowledge of ISO standards and compliance
- Ability to execute and manage test plans and test cases
- Strong problem-solving skills and critical thinking
- Experience with defect tracking and reporting tools (e.g., JIRA, Bugzilla)
- Effective collaborator in cross-functional teams
- Familiarity with programming languages (e.g., Java, Python, C#)
- Detail-oriented with strong analytical skills
COURSES / CERTIFICATIONS
Here’s a list of five certifications and completed courses for Alex Johnson, the Quality Assurance Technician from Sample 2:
Certified Software Quality Analyst (CSQA)
Date: January 2021ISTQB Certified Tester Foundation Level
Date: June 2020Automation Testing with Selenium
Date: March 2022ISO 9001:2015 Quality Management System Training
Date: August 2019Agile Testing Certification
Date: April 2023
EDUCATION
Education for Alex Johnson (Quality Assurance Technician)
Bachelor of Science in Computer Science
University of California, Berkeley
Graduated: May 2012Certification in Quality Assurance
American Society for Quality (ASQ)
Completed: August 2015
When crafting a resume for the Quality Control Analyst position, it is crucial to highlight strong data analysis skills and proficiency in statistical process control, as these competencies are central to effective quality assessment. Emphasizing experience in report generation showcases the ability to communicate findings clearly. Including critical thinking abilities demonstrates problem-solving skills essential for identifying and addressing quality issues. Project management experience should also be showcased, as it indicates capability in overseeing quality initiatives. Mentioning familiarity with industry-leading companies can further enhance credibility and attract potential employers' attention.
[email protected] • +1-555-123-4567 • https://www.linkedin.com/in/mariagarcia • https://twitter.com/mariagarcia
Maria Garcia is a detail-oriented Quality Control Analyst with expertise in data analysis and statistical process control. With experience at industry leaders like Google and Amazon, she excels in report generation and critical thinking, driving improvements in quality assurance processes. Maria’s strong project management skills ensure timely completion of initiatives, while her ability to analyze complex datasets empowers data-driven decision-making. Passionate about maintaining high standards and enhancing operational efficiency, she is well-equipped to contribute significantly to quality control efforts in any organization.
WORK EXPERIENCE
- Led a cross-functional team to implement statistical process control techniques, resulting in a 15% reduction in product defects.
- Developed and executed testing protocols that increased compliance with ISO standards by 30%.
- Created detailed reports to present findings to senior management, supporting strategic decision-making.
- Collaborated with software development teams to refine quality assurance practices, enhancing overall product reliability.
- Trained junior analysts on data analysis tools, fostering a culture of continuous improvement.
- Implemented automated testing protocols, which decreased testing time by 40% and improved efficiency.
- Facilitated communication between development teams and quality assurance to ensure streamlined project timelines.
- Conducted root cause analysis for quality issues, leading to proactive measures that improved product quality.
- Initiated bi-weekly quality review meetings, resulting in enhanced collaboration and problem-solving among team members.
- Recognition for excellence in performance with 'Employee of the Quarter' award.
- Led Lean Six Sigma initiatives that improved process efficiency by 25%, directly impacting production timelines.
- Designed and implemented training programs for over 100 employees to increase awareness of quality standards.
- Conducted comprehensive audits that resulted in a 20% increase in adherence to quality compliance for internal processes.
- Utilized customer feedback to identify key quality improvement areas, enhancing overall customer satisfaction.
- Awarded 'Quality Champion' for outstanding contributions to maintaining high standards.
- Ensured regulatory compliance for all quality processes, achieving zero compliance violations during internal audits.
- Developed a risk assessment framework that identified potential quality issues early in the product development cycle.
- Collaborated with cross-functional teams to align product development with GxP regulations, ensuring market readiness.
- Enhanced documentation processes, improving traceability and accountability for all quality reports.
- Contributed to the successful launch of three major products by overseeing quality assurance protocols.
SKILLS & COMPETENCIES
Skills for Maria Garcia (Quality Control Analyst)
- Data analysis
- Statistical process control
- Report generation
- Critical thinking
- Project management
- Proficiency in quality control software
- Quality assurance methodology
- Problem-solving abilities
- Attention to detail
- Effective communication skills
COURSES / CERTIFICATIONS
Here is a list of 5 certifications or completed courses for Maria Garcia, the Quality Control Analyst from Sample 3:
Certified Quality Auditor (CQA)
Issuing Organization: American Society for Quality (ASQ)
Date Completed: June 2021Lean Six Sigma Green Belt Certification
Issuing Organization: International Association for Six Sigma Certification (IASSC)
Date Completed: November 2020Data Analysis and Visualization with Python
Issuing Organization: Coursera (offered by IBM)
Date Completed: March 2022Statistical Process Control (SPC) Fundamentals
Issuing Organization: ASQ
Date Completed: January 2020Project Management Professional (PMP)
Issuing Organization: Project Management Institute (PMI)
Date Completed: September 2023
EDUCATION
Education for Maria Garcia (Position 3: Quality Control Analyst)
Bachelor of Science in Quality Assurance
University of California, Berkeley
Graduation Date: May 2010Certificate in Six Sigma Green Belt
American Society for Quality (ASQ)
Completion Date: August 2012
When crafting a resume for the Quality Improvement Specialist position, it’s crucial to highlight expertise in Lean Six Sigma methodologies, as well as training and coaching abilities for effective team development. Emphasize experience in process mapping and root cause analysis to demonstrate problem-solving capabilities. Additionally, showcasing strong customer service orientation and the ability to improve operational efficiency can set the candidate apart. Relevant experience from reputable companies in the pharmaceutical industry should also be included to validate expertise. Finally, ensure to convey effective communication skills that facilitate collaboration with cross-functional teams.
[email protected] • 555-123-4567 • https://www.linkedin.com/in/david-thompson • https://twitter.com/david_thompson
David Thompson is a skilled Quality Improvement Specialist with extensive experience in the pharmaceutical industry, having worked with leading companies such as Pfizer and Johnson & Johnson. He possesses a strong command of Lean Six Sigma methodologies and excels in training and coaching teams. With expertise in process mapping and root cause analysis, David is dedicated to enhancing operational efficiency and ensuring high-quality standards. His exceptional customer service orientation, combined with his ability to drive continuous improvement initiatives, makes him a valuable asset in any organization striving for excellence in quality assurance.
WORK EXPERIENCE
- Led a cross-functional team to implement Lean Six Sigma methodologies, resulting in a 30% reduction in production waste.
- Developed and executed training programs that enhanced team skills in process mapping and root cause analysis, which improved operational efficiency by 25%.
- Collaborated with senior management to identify key performance indicators, driving a focus on customer service orientation and satisfaction metrics.
- Facilitated workshops that fostered a culture of continuous improvement, positively impacting employee engagement scores by 15%.
- Recognized as 'Employee of the Year' for outstanding contributions to quality initiatives that significantly enhanced product offerings.
- Initiated and led a quality reporting system that streamlined data collection, improving response time for quality issues by 20%.
- Assisted in the development of new product quality specifications that met regulatory standards, contributing to successful product launches.
- Conducted comprehensive audits and inspections of production processes to ensure compliance with ISO standards, improving internal compliance rates by 40%.
- Developed actionable reports on quality data that supported strategic decision-making for product development.
- Mentored junior staff in statistical process control techniques, enhancing team capacity and readiness.
- Coordinated quality improvement initiatives that led to a 15% increase in efficiency in project workflows.
- Managed communication between departments to ensure project milestones were met on time, facilitating successful project delivery.
- Implemented a feedback loop for evaluating project outcomes, yielding insights that informed future quality improvement strategies.
- Conducted risk assessments for ongoing projects, identifying potential issues and implementing proactive solutions.
- Presented project updates to stakeholders, utilizing storytelling techniques to convey complex information clearly.
- Supported research and development teams by conducting rigorous quality assessments on experimental data.
- Assisted in the preparation of documentation and reports that adhered to GxP regulations, strengthening compliance measures.
- Collaborated with scientists to ensure quality control practices were integrated into experimental protocols.
- Participated in quality management meetings, contributing insights that shaped laboratory best practices.
- Received commendation for attention to detail, reducing discrepancies in data reporting.
SKILLS & COMPETENCIES
Here is a list of 10 skills for David Thompson, the Quality Improvement Specialist:
- Lean Six Sigma methodologies
- Training and coaching skills
- Process mapping techniques
- Root cause analysis
- Customer service orientation
- Data analysis and interpretation
- Project management
- Effective communication and presentation skills
- Change management
- Statistical analysis and continuous improvement strategies
COURSES / CERTIFICATIONS
Here are five certifications or completed courses for David Thompson, the Quality Improvement Specialist from Sample 4:
Lean Six Sigma Green Belt Certification
Issuing Organization: American Society for Quality (ASQ)
Completion Date: June 2018Root Cause Analysis Training
Issuing Organization: Institute of Quality Assurance
Completion Date: March 2019Project Management Professional (PMP) Certification
Issuing Organization: Project Management Institute (PMI)
Completion Date: January 2020ISO 9001:2015 Internal Auditor Course
Issuing Organization: International Register of Certificated Auditors (IRCA)
Completion Date: September 2021Customer Service Excellence Training
Issuing Organization: Dale Carnegie Training
Completion Date: February 2022
EDUCATION
Education for David Thompson (Quality Improvement Specialist)
Bachelor of Science in Industrial Engineering
University of Michigan, Ann Arbor, MI
Graduated: May 2008Master of Business Administration (MBA)
Massachusetts Institute of Technology (MIT), Cambridge, MA
Graduated: June 2010
When crafting a resume for a Regulatory Quality Control Specialist, it's crucial to emphasize regulatory compliance knowledge and experience with GxP regulations, as these are key to the role. Strong documentation skills should be highlighted, showcasing attention to detail and the ability to maintain accurate records. Including risk assessment capabilities demonstrates proficiency in evaluating potential compliance issues. Additionally, mentioning skills in cross-functional teamwork illustrates the ability to collaborate across departments, essential for regulatory alignment. Tailoring the resume to reflect relevant industry experience and certifications can set the applicant apart in a competitive job market.
[email protected] • (555) 123-4567 • https://www.linkedin.com/in/sarah-lee • https://twitter.com/sarahlee92
**Summary for Sarah Lee - Regulatory Quality Control Specialist**
Dedicated Regulatory Quality Control Specialist with a strong background in the pharmaceutical industry, having worked with leading companies such as Bayer and AstraZeneca. Proficient in regulatory compliance and documentation, with extensive knowledge of GxP regulations. Possesses exceptional risk assessment capabilities and excels in cross-functional teamwork, ensuring adherence to quality standards. Adept at navigating complex regulatory environments, passionate about maintaining product integrity and safety. Committed to continuous improvement and contributing to organizational success through meticulous attention to detail and effective communication skills. Seeking to leverage expertise to enhance quality operations in a dynamic environment.
WORK EXPERIENCE
- Led the implementation of a new quality management system that reduced product defects by 30%.
- Coordinated cross-functional teams to ensure adherence to GxP regulations, leading to a successful regulatory audit with zero non-conformities.
- Developed and maintained comprehensive documentation for quality processes, enhancing compliance and operational efficiency.
- Conducted training sessions for employees on regulatory compliance and quality assurance best practices, improving team competency by 25%.
- Collaborated with R&D to integrate quality measures into new product development, effectively leveraging risk assessment capabilities.
- Implemented Lean Six Sigma methodologies, resulting in a 40% improvement in process efficiency across the department.
- Spearheaded the transition to an automated quality control system that increased throughput by 20% while reducing errors.
- Established quality KPIs that led to enhanced performance tracking and increased accountability among team members.
- Cultivated strong relationships with cross-functional teams, providing strategic insights that drove product development improvements.
- Recognized for excellence in quality assurance with the company's Internal Excellence Award in 2017.
- Executed comprehensive risk assessments that identified potential compliance issues, leading to the implementation of proactive corrective actions.
- Maintained up-to-date knowledge of industry regulations, ensuring all products met stringent GxP requirements.
- Prepared regulatory submission documents, obtaining approval for multiple product launches ahead of schedule.
- Conducted internal audits to ensure compliance with quality standards, fostering a culture of continuous improvement within the organization.
- Presented compliance audit results to upper management, successfully advocating for necessary resource allocations to support quality initiatives.
- Performed routine quality inspections, achieving a 98% accuracy rate in identifying defective products.
- Collaborated with manufacturing teams to resolve quality issues, contributing to a 15% reduction in customer complaints.
- Assisted in the development of quality training materials, enhancing employee awareness of quality standards and procedures.
- Utilized statistical process control techniques to monitor production processes, leading to informed decision-making.
- Participated in cross-departmental quality improvement projects that achieved significant cost savings for the company.
SKILLS & COMPETENCIES
Here is a list of 10 skills for Sarah Lee, the Regulatory Quality Control Specialist:
- Regulatory compliance knowledge
- Strong documentation and reporting skills
- Understanding of GxP regulations (Good Practice regulations)
- Risk assessment and management abilities
- Cross-functional teamwork and collaboration
- Attention to detail and accuracy
- Problem-solving skills
- Knowledge of audit processes and quality standards
- Proficient in quality management systems (QMS)
- Ability to conduct training sessions on regulatory practices
COURSES / CERTIFICATIONS
Here is a list of 5 certifications and completed courses for Sarah Lee, the Regulatory Quality Control Specialist:
Certified Quality Improvement Associate (CQIA)
Issued by the American Society for Quality (ASQ)
Date: April 2020Regulatory Affairs Certification (RAC)
Issued by the Regulatory Affairs Professionals Society (RAPS)
Date: August 2021Good Manufacturing Practices (GMP) Training
Completed at the Food and Drug Administration (FDA)
Date: November 2019Risk Management Principles and Practices
Online Course by Coursera (Offered by University of California, Irvine)
Date: March 2022Six Sigma Green Belt Certification
Issued by the International Association for Six Sigma Certification (IASSC)
Date: January 2023
EDUCATION
Education for Sarah Lee (Regulatory Quality Control Specialist)
Bachelor of Science in Biochemistry
University of California, Los Angeles (UCLA)
Graduated: June 2013Master of Science in Regulatory Affairs
Northeastern University
Graduated: May 2016
When crafting a resume for a Quality Control Supervisor position, it's essential to highlight leadership and mentoring skills, as they indicate the ability to guide and develop a team effectively. Emphasizing experience in conducting quality audits and writing standard operating procedures (SOPs) showcases attention to detail and regulatory compliance. Additionally, showcasing skills in tracking performance metrics demonstrates the capacity for data-driven decision-making. Conflict resolution capabilities should also be accentuated, illustrating the ability to manage team dynamics and ensure a harmonious work environment. Tailoring the resume to reflect relevant industry experience with prominent companies can further strengthen the application.
[email protected] • +1-234-567-8901 • https://www.linkedin.com/in/michaelbrown • https://twitter.com/michaelbrown
**Summary:**
Dedicated and experienced Quality Control Supervisor with over 15 years in the food and beverage industry, adept at leading teams to ensure compliance with stringent quality standards. Proven leadership and mentoring skills have resulted in improved team performance and successful quality audits at leading companies like Coca-Cola and Nestlé. Expertise in writing Standard Operating Procedures (SOPs), tracking performance metrics, and resolving conflicts effectively. Committed to fostering a culture of continuous improvement and maintaining the highest quality standards to drive operational excellence and enhance product integrity.
WORK EXPERIENCE
- Led a quality improvement initiative that decreased product defects by 30%, contributing to a significant increase in customer satisfaction.
- Established and implemented SOPs that streamlined quality audits, resulting in a 25% reduction in audit time.
- Trained and mentored a team of 10 quality inspectors, fostering a culture of continuous improvement and efficient workflow.
- Collaborated with cross-functional teams to identify and resolve production discrepancies, enhancing overall product reliability.
- Introduced a performance metrics system that improved accountability and tracking of quality control processes.
- Conducted comprehensive data analyses that identified critical quality issues, leading to the successful launch of a more stable product line.
- Developed statistical process control charts that improved process monitoring and reduced variability in production.
- Generated detailed reports for upper management that informed strategic decisions regarding quality enhancements.
- Participated in root cause analyses that effectively reduced product recalls by 15%.
- Collaborated with product development teams to ensure compliance with quality regulations in new product designs.
- Implemented Lean Six Sigma methodologies to streamline processes, yielding a 20% reduction in operational costs.
- Designed and delivered training programs on quality improvement practices for over 50 employees.
- Championed a quality initiative that enhanced product features, leading to a 40% sales increase in the subsequent quarter.
- Engaged in mentorship and coaching of junior staff to promote quality awareness throughout the organization.
- Conducted regular quality audits, ensuring continuous compliance with industry standards and internal policies.
- Oversaw compliance audits and ensured strict adherence to GxP regulations across various operational levels.
- Executed risk assessments that identified potential regulatory issues, averting significant fines and operational disruptions.
- Developed and maintained comprehensive documentation for all quality processes and regulatory submissions.
- Facilitated cross-functional teamwork to address quality concerns, enhancing collaboration between departments.
- Coordinated training sessions on regulatory compliance for teams, improving overall awareness and accountability.
SKILLS & COMPETENCIES
Here is a list of 10 skills for Michael Brown, the Quality Control Supervisor:
- Leadership and mentoring skills
- Quality audits
- Standard Operating Procedure (SOP) writing
- Performance metrics tracking
- Conflict resolution
- Effective communication skills
- Team management and coordination
- Knowledge of quality assurance methodologies
- Risk management and assessment
- Continuous improvement practices
COURSES / CERTIFICATIONS
Here are five certifications or completed courses for Michael Brown, the Quality Control Supervisor:
Certified Quality Auditor (CQA)
Issued by: American Society for Quality (ASQ)
Date: April 2019Lean Six Sigma Green Belt Certification
Issued by: International Association for Six Sigma Certification (IASSC)
Date: September 2020ISO 9001:2015 Lead Auditor Training
Provider: BSI Group
Date: January 2021Advanced Quality Management Techniques
Provider: Coursera (University of Michigan)
Date: March 2022Conflict Resolution and Mediation Skills
Provider: LinkedIn Learning
Date: July 2023
EDUCATION
Bachelor of Science in Food Science and Technology, 2002
University of California, DavisMaster of Quality Management, 2005
University of Texas at Austin
Crafting a standout resume for a quality control specialist position demands a focus on both technical proficiency and the effective communication of soft skills. Quality control specialists are essential in ensuring products meet industry standards, so highlighting experience with industry-standard tools such as Six Sigma, Lean methodologies, and statistical process control can significantly enhance your appeal to potential employers. When detailing your professional history, quantifying achievements—like reducing defect rates or streamlining inspection processes—provides concrete evidence of your impact. Aligning your experience with the specific requirements of the job listing is critical; if a job description emphasizes proficiency in certain software or knowledge of regulatory standards, be sure to address these points within your resume.
In addition to technical skills, a quality control specialist must possess a blend of hard and soft skills that demonstrate a comprehensive expertise in the field. Highlighting your analytical abilities, attention to detail, and problem-solving skills can set your resume apart from others. Additionally, interpersonal skills are crucial, as quality control often requires collaboration across various departments. Providing examples of previous teamwork or leadership can showcase your ability to communicate effectively and contribute to a positive work environment. Tailoring your resume to reflect the specific language used in a job description and emphasizing relevant skills will signal to hiring managers that you not only possess the necessary qualifications but also understand the demands of the role. In today's competitive job market, a well-crafted resume that articulates both your technical capabilities and your soft skill set is vital for capturing the attention of top companies seeking quality control professionals.
Essential Sections for a Quality Control Specialist Resume
Contact Information
- Full name
- Phone number
- Email address
- LinkedIn profile or personal website (if applicable)
Professional Summary
- A brief overview of your experience and expertise in quality control
- Highlight specific skills or accomplishments that set you apart
Skills
- List of relevant technical and soft skills (e.g., statistical analysis, problem-solving, attention to detail)
- Certifications related to quality control (e.g., Six Sigma, ISO certification)
Work Experience
- Job titles and company names
- Dates of employment
- Key responsibilities and achievements in each role
Education
- Degrees obtained (e.g., Bachelor's in Quality Assurance, Engineering)
- Relevant coursework or projects highlighted
Certifications
- Professional certifications that demonstrate your knowledge and competency
- Relevant training programs completed
Additional Sections to Enhance Your Quality Control Specialist Resume
Achievements
- Specific metrics that demonstrate your impact (e.g., reduced defects by X%)
- Awards or recognition received for outstanding work
Professional Memberships
- Memberships in quality control or industry-related organizations (e.g., ASQ)
Technical Proficiencies
- Familiarity with quality management software or tools (e.g., Minitab, ISO 9001)
Additional Training
- Workshops, seminars, or continuing education that enhance your skill set
Languages
- Foreign languages spoken, especially if relevant to the industry or role
Volunteer Work or Extracurricular Activities
- Relevant experience that showcases leadership, teamwork, or community involvement in quality-related initiatives
Generate Your Resume Summary with AI
Accelerate your resume crafting with the AI Resume Builder. Create personalized resume summaries in seconds.
Crafting an impactful resume headline is essential for quality control specialists looking to make a strong first impression on potential employers. The headline serves as a brief yet powerful snapshot of your skills, expertise, and unique qualifications, laying the foundation for the rest of your application.
To resonate with hiring managers, your headline should succinctly convey your specialization in quality control. Start by including relevant keywords that reflect your expertise, such as “Quality Control Specialist,” “Quality Assurance Expert,” or “Regulatory Compliance Professional.” These terms are often used in job descriptions and help your resume appear in applicant tracking systems, increasing your chances of being noticed.
Additionally, your headline should highlight your distinctive qualities and accomplishments. For example, you might include quantifiable achievements, like “Certified Quality Control Specialist with 5+ Years of Experience Improving Product Quality by 30%.” This blends your role with specific outcomes, making your value proposition clear.
Personalizing your headline is crucial; consider what sets you apart in a competitive field. Focus on your industry experience, specific skill sets—such as Six Sigma certification or familiarity with ISO standards—and any notable projects or initiatives you've led.
Ultimately, an effective headline grabs the hiring manager's attention and encourages them to delve deeper into your resume. Aim for clarity and impact, ensuring your headline encapsulates not just your professional title but also the unique contributions you bring to the table. A well-crafted headline not only sets the tone for your resume but positions you as a strong candidate who can deliver results.
Quality Control Specialist Resume Headline Examples:
Strong Resume Headline Examples
Strong Resume Headline Examples for a Quality Control Specialist
- Detail-Oriented Quality Control Specialist with 5+ Years in Manufacturing and Process Improvement
- Certified Quality Auditor with Expertise in ISO Standards and Lean Six Sigma Methodologies
- Results-Driven Quality Control Specialist Skilled in Statistical Process Control and Root Cause Analysis
Why These are Strong Headlines
Specificity and Experience: Each headline specifies the individual’s role (Quality Control Specialist) and adds quantifiable experience (e.g., "5+ Years"). This immediately informs potential employers about the candidate's level of expertise and depth of experience.
Certification and Methodologies: The mention of professional certifications (e.g., Certified Quality Auditor) and methodologies (e.g., ISO Standards, Lean Six Sigma) highlights the candidate’s qualifications. This shows commitment to the profession and a proactive approach to personal and professional development, setting candidates apart in job applications.
Action-Oriented Language: Words like "Detail-Oriented," "Results-Driven," and "Skilled" convey a strong sense of professionalism and capability. This kind of language captures attention and implies a proactive and effective approach to quality management, which is essential in the quality control field.
Weak Resume Headline Examples
Weak Resume Headline Examples for Quality Control Specialist:
- "Experienced Quality Control Specialist Seeking New Opportunities"
- "Quality Control Professional with a Background in Manufacturing"
- "Dedicated Quality Control Specialist Looking for a Job"
Why These Are Weak Headlines:
Lack of Specificity:
- Phrases like "seeking new opportunities" or "looking for a job" are vague and do not convey what makes the candidate unique. Instead of generic terms, the headline should highlight specific skills or achievements that differentiate the applicant from others in the same field.
No Emphasis on Skills or Achievements:
- These headlines do not mention key skills, certifications, or accomplishments that are relevant to the role of a quality control specialist. A strong resume headline should showcase qualifications, such as expertise in Six Sigma methodologies or experience with specific quality control software.
Passive Tone:
- The use of phrases like "seeking" or "looking for" creates a passive impression. A more effective headline would be proactive and assertive, focusing on what the candidate brings to the table rather than what they are seeking. A strong headline should communicate confidence and a readiness to contribute to a potential employer.
Crafting an exceptional resume summary for a Quality Control Specialist is crucial, as it serves as a snapshot of your professional experience and capabilities. This summary should immediately captivate potential employers by highlighting your skills, accomplishments, and unique qualities. A well-written summary not only showcases your technical proficiency but also demonstrates your ability to collaborate with teams and attention to detail. Tailoring your resume summary to align with the specific role you're targeting can make a significant difference in gaining the attention of hiring managers. Here are key points to include in your summary:
Years of Experience: Clearly state the number of years you've spent in quality control or related fields, emphasizing any relevant achievements that showcase your expertise.
Specialized Industries: Highlight your experience in specific industries such as manufacturing, pharmaceuticals, or food production, as this demonstrates your adaptability and depth of knowledge.
Technical Proficiency: Include your experience with specific quality control software (e.g., Six Sigma, ISO standards) and methodologies, showcasing your technical skills that are crucial for the role.
Collaboration and Communication: Emphasize your ability to work collaboratively with cross-functional teams, ensuring that quality assurance processes are integrated across different departments. Mention any communication skills that enhance your ability to present findings to diverse audiences.
Attention to Detail: Illustrate your meticulous nature and how it contributes to ensuring high-quality outcomes, thereby reducing errors and improving processes.
By focusing on these key elements, your resume summary can become a compelling introduction that effectively highlights your qualifications, making you a standout candidate for the role of a Quality Control Specialist.
Quality Control Specialist Resume Summary Examples:
Strong Resume Summary Examples
Resume Summary Examples for a Quality Control Specialist
Detail-Oriented Quality Control Specialist:
Results-driven Quality Control Specialist with over 5 years of experience in implementing rigorous quality assurance processes in manufacturing environments. Expertise in identifying defects and streamlining procedures, resulting in a 30% reduction in product return rates. Demonstrated ability to lead QA teams to achieve compliance with industry standards and improve overall product quality.Proactive Quality Assurance Advocate:
Dedicated quality control professional with a proven track record of successfully managing quality assessments and inspections in fast-paced production settings. Skilled in data analysis, documentation, and corrective action planning that has contributed to enhancing operational efficiencies. Recognized for building strong cross-functional relationships to promote a culture of quality throughout the organization.Innovative Quality Control Analyst:
Accomplished Quality Control Specialist with a comprehensive background in statistical process control and quality audits. Passionate about using analytics to drive continuous improvement initiatives, having reduced waste by 25% and improved throughput in various projects. Strong communicator adept at training teams on quality standards and best practices.
Why These Are Strong Summaries
Specificity and Results: Each summary provides concrete examples of achievements and specific metrics (like percentages of reduction in return rates or waste), which demonstrate effectiveness and quantifiable success—qualities that hiring managers find persuasive.
Focused on Relevant Expertise: The summaries highlight relevant skills and experiences directly tied to quality control, such as quality assurance processes, data analysis, and compliance with industry standards. This shows that the candidate understands what is critical in the role.
Strong Action Verbs and Professional Tone: The use of active language and professional terminology conveys confidence and expertise. Phrases like "results-driven," "dedicated," and "accomplished" set a positive tone and project the candidate as a proactive contributor.
Teamwork and Leadership Emphasis: The summaries acknowledge the importance of collaboration and the ability to lead teams, which is crucial in roles that require cross-functional engagement to ensure quality.
By incorporating these elements, the summaries effectively communicate the candidate's qualifications and readiness for the role of a Quality Control Specialist.
Lead/Super Experienced level
Here are five examples of strong resume summaries for a Lead/Super Experienced Quality Control Specialist:
Proven Leadership in Quality Assurance: Over 10 years of experience in quality control and assurance within manufacturing environments, leading cross-functional teams to implement effective quality management systems that enhance product reliability and compliance with ISO standards.
Strategic Process Improvement Advocate: Expert in analyzing and optimizing quality processes, driving reductions in defects by 30% through the deployment of Six Sigma methodologies and the implementation of a continuous improvement culture across multiple teams.
Regulatory Compliance Expertise: Comprehensive understanding of industry regulations and standards including FDA, ISO 9001, and GMP, with a track record of ensuring successful audits and certifications that bolster organizational reputation and customer trust.
Data-Driven Decision Maker: Utilizes advanced statistical analysis to identify trends and drive corrective actions, resulting in improved operational efficiency and a 25% increase in customer satisfaction ratings over the past five years.
Mentorship and Training Champion: Committed to developing talent within the quality department by designing and implementing training programs for junior staff, fostering a highly skilled team that consistently meets and exceeds quality expectations.
Senior level
Detail-Oriented Quality Control Expert: Over 10 years of experience implementing and managing quality assurance protocols in high-stake production environments, ensuring compliance with industry standards and boosting product reliability by 30%.
Results-Driven Quality Control Specialist: Proven track record in leading cross-functional teams to identify and resolve quality issues, resulting in a 25% reduction in defect rates and significant cost savings for the organization.
Analytical Problem Solver: Expertise in utilizing statistical process control (SPC) and Six Sigma methodologies to analyze quality trends and drive continuous improvement initiatives, leading to enhanced operational efficiency.
Regulatory Compliance Advocate: Extensive knowledge of ISO, FDA, and industry-specific regulations, successfully leading audits and maintaining certifications that assure product quality and compliance, thus safeguarding company reputation.
Team Leader and Mentor: Strong leadership skills with a focus on training and developing quality control personnel, fostering a culture of high standards and accountability that enhances team performance and product quality across all levels.
Mid-Level level
Here are five examples of strong resume summaries for a mid-level quality control specialist:
Detail-Oriented Professional: Detail-oriented Quality Control Specialist with over 5 years of experience in manufacturing and production. Proven track record of implementing effective quality assurance processes that reduce product defects by 20%.
Process Improvement Advocate: Results-driven quality control expert skilled in conducting thorough inspections and audits. Adept at process improvement initiatives that enhance efficiency and minimize waste across operations.
Regulatory Compliance Expertise: Experienced in ensuring compliance with industry regulations and standards, including ISO 9001 and FDA guidelines. Strong analytical skills paired with a dedication to fostering a culture of quality within the workplace.
Cross-Functional Collaborator: Collaborative quality control specialist with a keen ability to communicate across departments. Successfully led cross-functional teams in identifying root causes of defects and implementing corrective actions, resulting in a 15% increase in overall product quality.
Tech-Savvy Quality Assurance: Tech-savvy professional experienced in utilizing data analysis tools and software for quality assessment. Proficient in statistical process control (SPC) and capable of leveraging technology to streamline quality assurance processes.
Junior level
Here are five bullet points for a strong resume summary tailored for a junior-quality-control specialist:
Detail-oriented quality control specialist with a foundational understanding of industry standards and practices, eager to apply skills in monitoring production processes and ensuring compliance with specifications.
Recent graduate with hands-on experience in quality assurance methodologies, demonstrating a commitment to maintaining high standards in product quality and safety.
Proficient in using basic QC tools and techniques, including statistical process control and root cause analysis, to identify discrepancies and drive continuous improvement in manufacturing processes.
Strong analytical thinker with excellent problem-solving abilities, ready to support team efforts in inspecting and testing products to enhance quality outcomes.
Collaborative team player dedicated to fostering a quality-centric culture by actively participating in inspections and contributing to the development of best practices in quality assurance.
Entry-Level level
Entry-Level Quality Control Specialist Resume Summary
- Detail-oriented and motivated recent graduate with a degree in Industrial Engineering, eager to apply theoretical knowledge to ensure quality standards in production processes.
- Proficient in basic quality control techniques and methodologies, including Six Sigma and statistical process control, with hands-on experience from academic projects and internships.
- Strong analytical skills and a commitment to continuous learning, seeking to support quality assurance teams in delivering high-quality products while adhering to safety and compliance standards.
- Excellent communication and teamwork abilities, demonstrated through collaborative projects, aiming to contribute to a positive work environment and effective quality management.
- Familiar with quality management systems (QMS) and documentation, eager to assist in enhancing operational efficiency and minimizing defects in a dynamic manufacturing setting.
Experienced Quality Control Specialist Resume Summary
- Accomplished Quality Control Specialist with over 5 years of relevant experience in fast-paced manufacturing environments, dedicated to optimizing processes and ensuring product quality.
- Proven track record in implementing quality assurance protocols and statistical analysis tools, leading to a 20% reduction in defects and significant cost savings for previous employers.
- Strong expertise in conducting regular inspections, audits, and training programs, ensuring compliance with industry standards and fostering a culture of quality throughout the organization.
- Excellent problem-solving abilities with a proactive approach to quality issues, utilizing root cause analysis and corrective action plans to enhance product performance and customer satisfaction.
- Certified ISO 9001 internal auditor with a deep understanding of regulatory requirements, committed to driving continuous improvement initiatives that align with business goals and customer expectations.
Weak Resume Summary Examples
Weak Resume Summary Examples
“I have experience in quality control and am looking for a job in this field.”
“A quality control specialist with some knowledge about inspections and testing.”
“I'm a dedicated worker seeking a position in quality control.”
Why These Are Weak Headlines
Lack of Specificity: Each summary lacks concrete details that define the individual's experience, skills, and accomplishments. Phrases like "experience in quality control" and "some knowledge" are vague and fail to communicate the applicant’s actual proficiency or expertise.
Absence of Quantifiable Achievements: These summaries do not highlight any measurable accomplishments or contributions that would demonstrate value. For example, mentioning a percentage improvement in quality metrics or the specific industries worked in would provide a clearer picture of the candidate's qualifications.
Generic Language: The summaries use generic phrases that could apply to any candidate and do not reflect the unique strengths, experiences, or goals of the individual. The lack of passion or clear intention (“dedicated worker seeking a position”) makes the candidate seem unmotivated or unsure about their career path.
Resume Objective Examples for Quality Control Specialist:
Strong Resume Objective Examples
Detail-oriented Quality Control Specialist with over 5 years of experience in manufacturing environments, seeking to leverage expertise in process improvement and compliance to enhance product quality and operational efficiency at XYZ Corporation.
Dedicated Quality Control Specialist skilled in statistical quality control methods and ISO standards, aiming to contribute strong analytical abilities and a commitment to excellence to the quality assurance team at ABC Industries.
Results-driven Quality Control Specialist with a proven track record in implementing effective quality assurance protocols, looking to bring my expertise in defect analysis and team collaboration to support the mission of DEF Manufacturing.
Why these are strong objectives:
These objectives are effective because they clearly outline the candidate's relevant experience and skills, aligning them with potential employer needs. Each objective specifies the number of years of experience and particular competencies, making it easy for hiring managers to see the candidate's value at a glance. Furthermore, they are tailored to the respective companies, indicating a genuine interest in the specific roles, which can set the candidate apart in a competitive job market.
Lead/Super Experienced level
Here are five strong resume objective examples for a Lead/Super Experienced Quality Control Specialist:
Driven Quality Control Specialist with over 10 years of experience in managing quality assurance teams and implementing robust quality control systems to optimize production processes and reduce defects by 30%. Seeking to leverage expertise in regulatory compliance and team leadership to enhance product quality at [Company Name].
Detail-oriented Quality Control Leader with extensive expertise in statistical process control and continuous improvement methodologies. Aiming to contribute my proven track record of reducing quality costs by 25% to the dynamic team at [Company Name], fostering a culture of excellence and precision.
Accomplished Quality Control Specialist with a strong background in leading cross-functional teams to drive quality improvement initiatives and ensure compliance with industry standards. Passionate about utilizing data-driven decision-making to elevate product quality at [Company Name] while mentoring the next generation of quality professionals.
Expert Quality Control Manager with a decade of experience in developing and implementing quality management systems that increase efficiency and product reliability. Eager to apply my leadership skills and analytical expertise to propel [Company Name] toward achieving its quality objectives and maintaining industry leadership.
Strategic Quality Assurance Professional known for enhancing product quality through rigorous testing protocols and effective training programs. Dedicated to leading a high-performing quality control team at [Company Name] to exceed customer expectations and drive operational excellence.
Senior level
Here are five strong resume objective examples for a Senior Quality Control Specialist:
Results-Driven Quality Specialist: Detail-oriented professional with over 7 years of experience in quality control and assurance, seeking to leverage expertise in developing and implementing quality standards to enhance operational efficiency and product excellence.
Strategic Quality Assurance Leader: Accomplished quality control specialist with extensive background in regulatory compliance and process improvement, aiming to contribute to an organization's success by driving continuous improvement initiatives and fostering a culture of quality.
Experienced Quality Control Expert: Senior quality control specialist with a proven track record of reducing defects by 30% through rigorous testing and inspection methodologies, looking to utilize analytical skills and industry knowledge to ensure top-notch product quality in a dynamic environment.
Innovative Quality Management Professional: Dynamic quality control leader with over a decade of experience in guiding cross-functional teams to enhance product reliability and safety, committed to applying best practices in a senior role to elevate the quality standards of an esteemed organization.
Proactive Quality Assurance Engineer: Senior specialist with deep expertise in statistical process control and root cause analysis, aspiring to drive quality initiatives that align with business objectives and improve customer satisfaction in a forward-thinking company.
Mid-Level level
Certainly! Here are five strong resume objective examples tailored for a mid-level quality control specialist:
Detail-Oriented Professional: Results-driven quality control specialist with over 5 years of experience in implementing and monitoring quality assurance processes to enhance product reliability and compliance. Seeking to leverage expertise in statistical analysis and industry standards to contribute to [Company Name]'s commitment to quality and excellence.
Process Improvement Advocate: Quality control specialist with a robust background in developing and executing quality management systems in manufacturing environments. Aim to apply my skills in root cause analysis and continuous improvement initiatives at [Company Name] to elevate operational efficiency and product quality.
Regulatory Compliance Expert: Mid-level quality control professional skilled in ensuring adherence to ISO and FDA regulations. Eager to bring my strong analytical skills and attention to detail to [Company Name] to safeguard product integrity and maintain the highest quality standards.
Cross-Functional Collaborator: Dynamic quality control specialist with comprehensive experience in collaborating with cross-functional teams to drive quality initiatives and solve complex quality issues. Looking to join [Company Name] to enhance team performance and elevate product quality through a proactive quality assurance approach.
Data-Driven Decision Maker: Accomplished quality control specialist with expertise in using data analytics to drive quality improvements and reduce defects. Seeking to join [Company Name] to utilize my skills in data analysis and process optimization to enhance product quality and customer satisfaction.
Junior level
Here are five strong resume objective examples for a junior-level Quality Control Specialist:
Detail-oriented Quality Control Specialist eager to apply strong analytical skills and a foundational understanding of quality assurance processes to enhance product quality and compliance in a fast-paced manufacturing environment.
Recent graduate in Quality Assurance with hands-on experience in quality inspection techniques and a solid understanding of industry standards, seeking to contribute a fresh perspective and dedication to excellence in a junior Quality Control Specialist role.
Motivated Junior Quality Control Specialist with experience in conducting tests and inspections, looking to leverage exceptional problem-solving skills and a commitment to improving production efficiency at [Company Name].
Dedicated and results-driven professional with a background in quality control and a passion for ensuring product reliability, seeking to join [Company Name] to support quality improvement initiatives and deliver exceptional results.
Ambitious Quality Control enthusiast with foundational skills in data analysis and quality inspection processes, aiming to further develop expertise while contributing to quality assurance efforts in a dynamic team environment at [Company Name].
Entry-Level level
Sure! Here are five strong resume objective examples for an entry-level Quality Control Specialist:
Detail-Oriented and Aspiring Quality Control Specialist: Seeking to leverage my analytical skills and attention to detail in an entry-level quality control position, where I can contribute to ensuring product excellence and compliance with industry standards.
Recent Graduate with a Passion for Quality Assurance: Motivated entry-level professional with a Bachelor's degree in [Your Degree] and a foundational understanding of quality control processes, eager to apply my training in a dynamic team environment to enhance product quality and efficiency.
Analytical Thinker Seeking Quality Control Role: Enthusiastic about beginning my career as a quality control specialist; dedicated to applying my problem-solving skills and commitment to accuracy in a reputable organization that values product integrity.
Entry-Level Quality Control Professional: Recent graduate with hands-on experience in laboratory practices and a keen eye for detail, looking to join a team where I can learn and grow while ensuring the highest quality standards are met in all products.
Motivated and Detail-Driven Candidate: Seeking an entry-level position as a Quality Control Specialist, where I can utilize my strong organizational skills and commitment to quality assurance to contribute to a company’s success and maintain product standards.
Weak Resume Objective Examples
Weak Resume Objective Examples for a Quality Control Specialist
"Looking for a quality control position where I can use my skills and gain experience."
"To obtain a job in quality control that offers a good salary and benefits."
"Aspiring quality control specialist eager to support the team and learn more."
Reasons Why These Objectives Are Weak
Lack of Specificity: The objectives are vague and do not specify what particular skills or experiences the candidate possesses that would be beneficial for the quality control role. Employers are looking for candidates who can demonstrate how they can add value to the company, rather than simply expressing a desire for a job.
Focus on Personal Gain: The objectives tend to center around what the applicant hopes to gain from the position (experience, salary, benefits) rather than what they can contribute to the company. This self-centered approach can come across as unprofessional and may not resonate with hiring managers.
Ambiguity and Lack of Action: Phrases like “looking for” and “eager to support” do not convey confidence or initiative. A strong resume objective should be assertive and clearly state what the candidate intends to achieve in the quality control field, showing a proactive attitude and clear career goals.
When crafting an effective work experience section for a quality control specialist resume, it's crucial to emphasize relevant skills and accomplishments that demonstrate your expertise in ensuring product quality and compliance with standards. Here’s a structured approach to help you create a compelling section:
Job Titles and Company Names: Clearly list your job titles, company names, and dates of employment. Ensure that your most recent experience appears first, following a reverse-chronological order.
Tailored Job Descriptions: For each role, provide a brief overview of your responsibilities. Focus on quality control tasks such as inspecting products, running tests, and analyzing data. Use industry-relevant terminology to resonate with hiring managers.
Quantifiable Achievements: Whenever possible, quantify your accomplishments with specific metrics. For example, mention “Reduced defect rate by 30% through implementation of new testing protocols” or “Improved production efficiency by 20% by revising quality standards”. Numbers make your contributions more tangible.
Key Skills and Tools: Highlight the specific skills and tools you used in your roles. Mention proficiency in quality management systems (e.g., ISO 9001), statistical process control (SPC), and software tools (e.g., Minitab, Six Sigma methodologies).
Emphasize Collaboration: Quality control often involves working closely with other departments. Note your collaboration with production teams, suppliers, and management to foster a quality-oriented culture.
Continuous Improvement: Describe your involvement in continuous improvement initiatives, such as developing training programs or participating in audits. Showcase your commitment to enhancing quality processes.
Format Clearly: Use bullet points for readability, and keep descriptions concise—ideally 1-2 lines each. This allows hiring managers to quickly identify your qualifications.
By structuring your work experience section thoughtfully, you'll effectively communicate your skills as a quality control specialist, making a strong impression on potential employers.
Best Practices for Your Work Experience Section:
Certainly! Here are 12 best practices for the Work Experience section, specifically tailored for a Quality Control Specialist:
Use Clear Job Titles: Ensure your job titles are clear and accurately reflect your role, such as “Quality Control Specialist” or “Quality Assurance Technician.”
Quantify Achievements: Include measurable achievements, such as “Reduced defect rates by 15% through rigorous testing protocols.”
Highlight Relevant Skills: Focus on skills pertinent to quality control, such as data analysis, statistical process control, and inspection techniques.
Describe Key Responsibilities: Clearly outline your core responsibilities, emphasizing aspects like quality inspections, compliance audits, and testing procedures.
Tailor Content to the Industry: Customize your experience descriptions to align with the specific industry you’re applying to, such as manufacturing, pharmaceuticals, or food production.
Include Tools and Software: Mention any relevant tools or software you have experience with, such as Six Sigma, ISO standards, or quality management systems (QMS).
Show Continuous Improvement: Highlight your involvement in continuous improvement initiatives, demonstrating a commitment to enhancing processes and systems.
Focus on Problem-Solving: Share examples where you identified quality issues and implemented effective solutions, showcasing your analytical and troubleshooting skills.
Demonstrate Team Collaboration: Emphasize your ability to work in cross-functional teams, collaborating with production staff, engineers, and management to uphold quality standards.
Utilize Action Verbs: Begin bullet points with strong action verbs like "analyzed," "developed," "implemented," and "monitored" to convey impact energetically.
Keep It Relevant: Limit your descriptions to relevant experiences that directly relate to quality control—avoid unrelated roles unless transferable skills can be drawn upon.
Use Consistent Formatting: Maintain a uniform format with bullet points, clear headings, and consistent font styles, making it easy for hiring managers to skim quickly.
By following these best practices, you can create a compelling Work Experience section that effectively highlights your qualifications as a Quality Control Specialist.
Strong Resume Work Experiences Examples
Strong Resume Work Experience Examples for a Quality Control Specialist
Quality Control Analyst at ABC Manufacturing
Implemented a new quality control process that reduced product defects by 30%, leading to a significant increase in customer satisfaction and a 15% reduction in return rates over one year.Quality Assurance Technician at XYZ Electronics
Conducted thorough inspections and testing on assembly lines, identifying and resolving issues in real-time, which improved production efficiency by 20% and decreased downtime by 25%.Quality Improvement Specialist at LMN Foods
Designed and executed a training program for production staff aimed at adherence to quality standards, resulting in a 40% decrease in non-compliance incidents and fostering a culture of continuous improvement within the team.
Why These Work Experiences are Strong
Quantifiable Achievements: Each example highlights measurable outcomes (e.g., percentage reductions in defects, returns, and non-compliance incidents) that demonstrate the candidate’s impact on the organization. This showcases career accomplishments rather than just duties performed.
Relevant Skills and Impact: The roles described focus on critical skills needed in quality control, such as process implementation, hands-on inspection, and training development. This alignment with key responsibilities shows the candidate’s preparedness for similar future roles.
Continuous Improvement Mindset: By emphasizing initiatives that not only corrected current issues but also created systemic changes (like training programs), these experiences illustrate the candidate’s forward-thinking approach and commitment to enhancing quality standards in a proactive manner.
Lead/Super Experienced level
Senior Quality Control Specialist, XYZ Manufacturing Co. | June 2018 - Present
Led a team of 10 quality control inspectors in implementing ISO 9001 standards, resulting in a 25% decrease in product defects and a 15% increase in customer satisfaction ratings within the first year.Quality Assurance Manager, ABC Industries | January 2015 - May 2018
Developed and executed comprehensive quality assurance strategies that improved process efficiency by 30% and reduced compliance issues by 40%, while overseeing audits and training programs for staff.Lead Quality Control Engineer, DEF Electronics | March 2012 - December 2014
Spearheaded a cross-departmental initiative to integrate advanced statistical process control methodologies, enhancing production accuracy by 20% and significantly minimizing waste through continuous improvement practices.Quality Systems Manager, GHI Pharmaceuticals | July 2008 - February 2012
Managed the implementation of quality management systems across multiple facilities, resulting in a successful regulatory compliance record during inspections and a 50% reduction in product recall incidents.Senior Compliance Auditor, JKL Chemical Corporation | August 2005 - June 2008
Conducted in-depth compliance audits and risk assessments, identifying critical areas for improvement that led to an annual savings of $1.5 million and ensured adherence to industry regulations, enhancing overall product safety and quality.
Senior level
Sure! Below are five bullet points representing strong resume work experience examples for a Senior Quality Control Specialist:
Leadership in Quality Systems: Spearheaded the implementation of a robust quality management system that reduced product non-conformances by 30%, ensuring compliance with ISO 9001 standards and enhancing overall operational efficiency.
Advanced Data Analysis: Utilized advanced statistical methods to analyze quality control data, which led to targeted improvements in manufacturing processes, resulting in a 25% decrease in defect rates over a six-month period.
Cross-Departmental Collaboration: Collaborated with engineering and production teams to develop and refine quality control protocols, effectively bridging communication gaps and improving product quality while reducing inspection times by 40%.
Training and Development: Designed and conducted comprehensive training programs for junior quality staff and production personnel, elevating team competency in quality assurance practices and achieving a 95% satisfaction rating in post-training evaluations.
Regulatory Compliance Expertise: Successfully navigated complex regulatory environments, conducting audits and inspections that resulted in zero non-compliance issues during third-party inspections, thereby solidifying the company’s reputation for quality excellence.
Mid-Level level
Sure! Here are five bullet points suitable for a mid-level Quality Control Specialist's resume:
Quality Assurance Processes: Developed and implemented comprehensive quality control processes that improved product consistency and reduced defects by 20% over a 12-month period, ensuring adherence to industry standards.
Data Analysis & Reporting: Conducted detailed data analysis of production metrics, creating monthly performance reports that identified key areas for improvement and supported management in strategic decision-making.
Cross-Functional Collaboration: Worked closely with cross-functional teams, including production, engineering, and supply chain, to initiate corrective actions and preventive measures, enhancing overall product quality and customer satisfaction.
Training & Development: Led training sessions for new hires and existing staff on quality control protocols and best practices, fostering a culture of quality awareness that resulted in a significant decrease in inspection failures.
Regulatory Compliance: Ensured compliance with ISO 9001 and other relevant industry standards by conducting regular audits and inspections, maintaining documentation, and facilitating external audit preparations, which resulted in zero non-conformance reports during audits.
Junior level
Sure! Here are five bullet point examples suitable for a junior-level Quality Control Specialist:
Conducted routine inspections of raw materials and finished products to ensure compliance with quality standards, resulting in a 15% reduction in defects over a six-month period.
Assisted in developing and implementing quality control procedures through collaboration with senior specialists, leading to enhanced operational efficiency and reduced waste.
Performed data analysis on quality reports and identified trends, providing actionable insights to the team that improved production processes by minimizing errors.
Facilitated training sessions for new employees on quality assurance protocols and best practices, fostering a culture of quality awareness and accountability within the team.
Collaborated with cross-functional teams to address quality issues and implement corrective actions, successfully achieving a 20% improvement in overall product quality metrics.
Entry-Level level
Here are five strong bullet point examples for an entry-level Quality Control Specialist resume:
Conducted thorough inspections of raw materials and finished products, utilizing standard operating procedures to ensure compliance with quality standards and regulations, resulting in a 15% reduction in defects.
Assisted in the development and implementation of quality control plans, collaborating with cross-functional teams to identify areas for improvement, thereby enhancing product consistency and overall customer satisfaction.
Participated in routine audits and evaluations of production processes, documenting findings and recommending corrective actions that contributed to increased operational efficiency.
Utilized statistical process control (SPC) techniques to monitor production metrics, aiding in real-time decision-making and contributing to a 10% increase in production yield.
Supported training initiatives for new employees on quality assurance protocols, fostering a culture of quality and ensuring a thorough understanding of best practices among team members.
Weak Resume Work Experiences Examples
Weak Resume Work Experience Examples for Quality Control Specialist
Quality Control Intern at ABC Manufacturing, June 2022 - August 2022
- Assisted in basic inspection of products and recorded results in a spreadsheet.
- Shadowed senior quality control professionals and attended training sessions.
Warehouse Associate at XYZ Distribution, January 2021 - May 2022
- Sorted and organized products for shipping, ensuring proper labeling and handling.
- Performed simple checks on incoming products against packing lists.
Sales Associate at Retail Store, June 2020 - December 2020
- Engaged with customers and managed transactions at the cash register.
- Maintained cleanliness and organization of the sales floor and stockroom.
Why These Are Weak Work Experiences
Limited Responsibilities and Impact: These roles do not show substantial involvement in quality control processes or decision-making. For example, simply assisting in inspections or shadowing lacks proactive engagement or contributions that demonstrate quality control knowledge or skills.
Lack of Relevant Skills Application: The experiences detailed do not highlight specific quality control methodologies, tools, or technologies that are crucial in the field (like Six Sigma, statistical process control, etc.). The work performed is either too entry-level or completely unrelated to quality assurance and control.
Absence of Measurable Achievements: None of the examples present measurable outcomes or improvements attributable to the individual’s contributions. Quality control specialists are expected to improve processes or reduce defects, and without such achievements showcased, the impact of the experiences remains minimal.
Overall, these examples fail to demonstrate relevant expertise, responsibilities, or accomplishments that would make a candidate stand out for a quality control specialist position.
Top Skills & Keywords for Quality Control Specialist Resumes:
To enhance your quality control specialist resume, focus on highlighting key skills and relevant keywords. Emphasize your proficiency in quality assurance processes, statistical analysis, and Six Sigma methodologies. Include technical skills such as familiarity with quality control tools (e.g., Six Sigma, ISO 9001), inspection techniques, and data analysis software. Showcase your attention to detail, problem-solving abilities, and effective communication skills. Keywords like “root cause analysis,” “compliance,” “process improvement,” “data-driven,” and “audit” can attract attention from hiring managers. Tailor your resume to each job description to match specific requirements, ensuring your skills align with the employer's needs.
Top Hard & Soft Skills for Quality Control Specialist:
Hard Skills
Sure! Here’s a table with 10 hard skills for a quality control specialist, along with their descriptions. Each hard skill is formatted as a link as per your request.
Hard Skills | Description |
---|---|
Quality Assurance | Knowledge of quality assurance processes to ensure products meet specified standards. |
Statistical Analysis | Ability to analyze data statistically to identify trends and assess quality levels. |
Inspection Techniques | Proficiency in various inspection methods to evaluate product quality effectively. |
Root Cause Analysis | Skill in identifying the underlying causes of defects or issues in processes or products. |
Six Sigma | Knowledge of Six Sigma methodologies to improve process efficiency and reduce defects. |
Audit Techniques | Ability to conduct internal audits to verify compliance with quality standards. |
Quality Management Systems | Familiarity with implementing and managing quality management systems like ISO 9001. |
Documentation | Proficient in creating and maintaining quality control documentation and reports. |
Technical Reporting | Ability to compile and present technical quality-related documentation clearly and accurately. |
Lean Manufacturing | Knowledge of lean principles to streamline processes and eliminate waste in production. |
Feel free to adjust or expand upon the descriptions as needed!
Soft Skills
Sure! Here’s a table with 10 soft skills relevant to a quality control specialist, including links in the specified format.
Soft Skills | Description |
---|---|
Communication | The ability to convey information clearly and effectively, both verbally and in writing. |
Attention to Detail | The capacity to notice small details that can impact the quality of work and product integrity. |
Problem Solving | The skill to identify problems, analyze them, and develop effective solutions. |
Critical Thinking | The ability to evaluate issues objectively and make informed decisions based on analysis. |
Adaptability | The willingness to adjust to new conditions and changes in processes or technologies. |
Teamwork | The capability to work effectively as part of a team, collaborating with others to achieve goals. |
Time Management | The ability to prioritize tasks and manage one’s time efficiently to meet deadlines. |
Organization | The skill to arrange and manage resources systematically to improve efficiency and processes. |
Flexibility | The readiness to adapt to changing conditions or unexpected challenges in the workplace. |
Conflict Resolution | The ability to handle disputes and disagreements constructively and find amicable solutions. |
Feel free to adjust any part of the descriptions or skills as needed!
Elevate Your Application: Crafting an Exceptional Quality Control Specialist Cover Letter
Quality Control Specialist Cover Letter Example: Based on Resume
Dear [Company Name] Hiring Manager,
I am excited to submit my application for the Quality Control Specialist position at [Company Name], as advertised. With over five years of experience in quality assurance and a passion for precision, I am eager to contribute my expertise to uphold and enhance your esteemed reputation.
Throughout my career, I have developed a strong foundation in quality control methodologies, including Six Sigma and ISO standards, which have enabled me to identify process inefficiencies and drive improvement initiatives. My proficiency in industry-standard software such as Minitab, SAP Quality Management, and QDB has been instrumental in analyzing data trends and streamlining operations, leading to a 20% reduction in defects at my previous employer.
In my most recent role at [Previous Company Name], I led a team in executing a comprehensive quality audit that uncovered critical areas for improvement across multiple departments. This initiative not only decreased non-conformance reports by 30% but also fostered a culture of quality awareness amongst team members. My collaborative work ethic has allowed me to build strong relationships with cross-functional teams, ensuring quality standards are met while maintaining alignment with production goals.
I am particularly impressed by [Company Name]'s commitment to innovation and excellence in [specific product/service]. I am enthusiastic about the possibility of bringing my skills in quality analysis and my proactive approach to your team, contributing to continuous improvement and operational success.
Thank you for considering my application. I am looking forward to the opportunity to discuss how my background and passion for quality control can help [Company Name] achieve its objectives.
Best regards,
[Your Name]
[Your Phone Number]
[Your Email Address]
When crafting a cover letter for a Quality Control Specialist position, it's important to tailor your content to highlight your skills, experiences, and understanding of the role. Here’s a guide to what you need to include:
Header and Greeting: Start with your name, address, and contact information at the top. Follow this with the date and the employer's details. Use a professional greeting, addressing the hiring manager by name if possible (e.g., “Dear [Name]”).
Introduction: Open with a strong introduction that grabs attention. Mention the position you’re applying for and how you found out about the job. Briefly state your background in quality control and your enthusiasm for the role.
Relevant Experience: In the next paragraph, highlight your relevant experience. Discuss previous positions where you ensured product quality, conducted audits, or collaborated with other departments. Use specific examples, such as “Successfully implemented a quality management system that reduced defects by 20% within six months.”
Skills and Qualifications: Detail the skills that make you a strong candidate. This could include knowledge of quality control methods, proficiency in statistical analysis, ISO standards, or familiarity with tools like Six Sigma. You might say, “My expertise in root cause analysis and corrective actions has consistently improved product integrity.”
Alignment with Company Values: Research the company and mention how your values align with theirs. This shows that you’ve done your homework and are genuinely interested in being a part of their team. For instance, if the company values continuous improvement, discuss your commitment to professional development.
Conclusion and Call to Action: Conclude by expressing your eagerness for an interview to discuss how your qualifications align with the company’s needs. Encourage a follow-up and thank them for considering your application.
Professional Closing: Use a professional closing, such as “Sincerely,” followed by your name.
Overall, keep your cover letter concise, ideally one page, and ensure it aligns with the job description while reflecting your personality and professionalism.
Resume FAQs for Quality Control Specialist:
How long should I make my Quality Control Specialist resume?
When crafting a resume for a quality control specialist position, aim for a length of one page, especially if you have less than 10 years of experience. A concise, focused resume allows hiring managers to quickly assess your qualifications without overwhelming them with information. Highlight your skills, relevant experience, and achievements that directly relate to quality control.
If you have extensive experience—over a decade—consider extending your resume to two pages. However, ensure every detail remains relevant to the job application, avoiding unnecessary filler. Use bullet points for clarity, and prioritize information that demonstrates your expertise in quality assurance processes, regulatory compliance, and proficiency in quality control tools and methodologies.
Employ industry-specific keywords to optimize your resume for applicant tracking systems (ATS). Alongside technical skills, emphasize soft skills like attention to detail, analytical thinking, and problem-solving abilities, as these are crucial in quality control roles.
Ultimately, aim for clarity and impact rather than simply filling space. Tailor your content for each application, showcasing your most pertinent qualifications while keeping the format clean and professional.
What is the best way to format a Quality Control Specialist resume?
Formatting a resume for a Quality Control Specialist position requires clarity, organization, and attention to detail, reflecting the skills necessary for the job. Here are key elements to consider:
Header: Start with your name, contact information, and LinkedIn profile, if applicable. Use a professional email address.
Professional Summary: Include a brief, compelling summary (2-3 sentences) that highlights your experience, skills, and career objectives. Tailor this to the Quality Control field.
Skills Section: List relevant skills prominently, such as knowledge of quality standards (ISO, Six Sigma), testing methodologies, data analysis, and proficiency in quality control software. Use bullet points for easy readability.
Work Experience: Clearly outline your work history in reverse chronological order, focusing on positions related to quality control. Include job titles, company names, and dates of employment, along with bullet points describing your accomplishments and responsibilities.
Education: Detail your educational background, including degrees and certifications relevant to quality control.
Certifications: Mention any relevant certifications, such as Certified Quality Auditor (CQA) or Certified Quality Improvement Associate (CQIA).
Formatting: Use a clean, professional font and consistent spacing. Ensure headings are bolded for distinction, and keep the resume to one page, if possible, or two at most for extensive experience.
By presenting your qualifications in a structured manner, you enhance your chances of making a strong impression.
Which Quality Control Specialist skills are most important to highlight in a resume?
When crafting a resume for a Quality Control Specialist position, it’s crucial to highlight specific skills that demonstrate your expertise and suitability for the role. Here are some of the most important skills to emphasize:
Attention to Detail: Quality Control Specialists must meticulously examine products and processes to identify defects and ensure compliance with standards.
Analytical Skills: Proficiency in data analysis allows you to interpret testing results and make informed decisions about product quality.
Knowledge of Quality Standards: Familiarity with industry standards such as ISO, Six Sigma, or GMP is essential. Highlight any certifications that validate your knowledge.
Technical Proficiency: Experience with quality control software and tools, such as statistical process control (SPC) systems, can set you apart from other candidates.
Problem-Solving Skills: The ability to quickly identify issues and implement effective solutions is key to maintaining product quality.
Communication Skills: Ability to clearly document findings and collaborate effectively with team members and other departments.
Organizational Skills: Efficiently managing time and resources to conduct tests and audits while maintaining comprehensive records is vital.
By highlighting these skills, you will represent your qualifications effectively, making your resume stand out to potential employers.
How should you write a resume if you have no experience as a Quality Control Specialist?
Writing a resume for a quality control specialist position without direct experience can be challenging, but there are strategies to effectively showcase your potential. Start with a strong objective statement that highlights your enthusiasm for quality control and your willingness to learn.
Next, focus on relevant skills. Emphasize transferable skills such as attention to detail, problem-solving, analytical thinking, and effective communication. If you have experience in any manufacturing or laboratory settings, highlight that to demonstrate familiarity with industry practices.
In the education section, include any relevant coursework, certifications, or training related to quality assurance, laboratory techniques, or production processes. If you have participated in projects or internships that involved quality assessment or teamwork, describe those experiences.
Consider including a volunteer experience section where you can showcase involvement in activities that required organizational skills, attention to detail, or adherence to standards.
Lastly, tailor your resume to the job description by using keywords that match the requirements, indicating your understanding of the role. By framing your background in a positive light and demonstrating a proactive attitude, you can make a compelling case for your candidacy, even without formal experience.
Professional Development Resources Tips for Quality Control Specialist:
null
TOP 20 Quality Control Specialist relevant keywords for ATS (Applicant Tracking System) systems:
Here's a table with 20 relevant keywords for a Quality Control Specialist that can help enhance your resume for ATS (Applicant Tracking Systems) optimization. Each keyword is accompanied by a brief description to provide context.
Keyword | Description |
---|---|
Quality Assurance | Processes and methodologies used to ensure product quality meets specified standards. |
ISO Standards | International standards for ensuring quality in processes and products. |
Root Cause Analysis | Identifying the underlying reasons for defects or issues to prevent recurrence. |
Statistical Process Control | Techniques for monitoring and controlling processes using statistics. |
Auditing | Systematic examination of processes to ensure compliance with company and regulatory standards. |
Compliance | Ensuring adherence to laws, regulations, and internal policies. |
Quality Improvement | Initiatives aimed at enhancing product quality and performance. |
Inspection | Examination of products and processes to ensure they meet quality standards. |
Non-conformance Reporting | Documenting and tracking deviations from quality standards or specifications. |
Training and Development | Programs aimed at enhancing employee skills and knowledge in quality control processes. |
Corrective Action | Processes designed to rectify identified quality issues to prevent recurrence. |
Continuous Improvement | Ongoing efforts to enhance products, services, or processes. |
Documentation | Creating and maintaining records related to quality processes and inspections. |
Quality Control Plans | Strategic frameworks outlining quality control measures for specific projects or operations. |
Risk Management | Identifying, assessing, and mitigating risks that could impact product quality. |
Analytical Skills | Ability to analyze data and trends to inform quality control decisions. |
Lean Manufacturing | Streamlining production processes to eliminate waste while maintaining quality. |
Six Sigma | Data-driven approach to improving quality and reducing defects through defined methodologies. |
Test Plans | Detailed descriptions of testing methods and procedures to evaluate product quality. |
Team Collaboration | Working effectively with cross-functional teams to achieve quality goals. |
Including these keywords in your resume, particularly in context (i.e., where you demonstrate your experience and skills associated with each), will improve your chances of passing through ATS filters and getting noticed by hiring managers.
Sample Interview Preparation Questions:
Can you describe your experience with quality control processes and methodologies you have implemented in previous roles?
How do you ensure compliance with industry standards and regulations during the quality control process?
Describe a time when you identified a defect in a product. How did you handle the situation?
What tools or software have you used for quality control, and how do they enhance your ability to perform your duties?
How do you prioritize quality control tasks when working under tight deadlines or in a high-pressure environment?
Related Resumes for Quality Control Specialist:
Generate Your NEXT Resume with AI
Accelerate your resume crafting with the AI Resume Builder. Create personalized resume summaries in seconds.