Quality Technician Resume Examples: Stand Out with These 6 Tips
---
### Sample Resume 1
**Position number:** 1
**Person:** 1
**Position title:** Quality Control Inspector
**Position slug:** quality-control-inspector
**Name:** Jessica
**Surname:** Thompson
**Birthdate:** March 15, 1990
**List of 5 companies:**
- Ford Motor Company
- General Motors
- Mercedes-Benz
- Toyota
- Honda
**Key competencies:**
- Visual Inspection
- Defect Identification
- Quality Standards Compliance
- Data Analysis
- Effective Communication
---
### Sample Resume 2
**Position number:** 2
**Person:** 2
**Position title:** Quality Assurance Technician
**Position slug:** quality-assurance-technician
**Name:** Mark
**Surname:** Johnson
**Birthdate:** July 22, 1985
**List of 5 companies:**
- Nestle
- Kraft Heinz
- PepsiCo
- Unilever
- Mondelez International
**Key competencies:**
- Process Improvement
- Quality Testing Techniques
- Root Cause Analysis
- Documentation Skills
- Team Collaboration
---
### Sample Resume 3
**Position number:** 3
**Person:** 3
**Position title:** Manufacturing Quality Technician
**Position slug:** manufacturing-quality-technician
**Name:** Emily
**Surname:** Nguyen
**Birthdate:** September 10, 1992
**List of 5 companies:**
- General Electric
- Honeywell
- Siemens
- Caterpillar
- Rockwell Automation
**Key competencies:**
- ISO Standards Knowledge
- Equipment Calibration
- Process Monitoring
- Troubleshooting Skills
- Statistical Quality Control
---
### Sample Resume 4
**Position number:** 4
**Person:** 4
**Position title:** Quality Assurance Analyst
**Position slug:** quality-assurance-analyst
**Name:** David
**Surname:** Rodriguez
**Birthdate:** February 5, 1988
**List of 5 companies:**
- IBM
- Microsoft
- Oracle
- SAP
- Salesforce
**Key competencies:**
- Software Testing
- Quality Audits
- Test Planning & Execution
- Agile Methodology
- Data Reporting
---
### Sample Resume 5
**Position number:** 5
**Person:** 5
**Position title:** Quality Improvement Specialist
**Position slug:** quality-improvement-specialist
**Name:** Sarah
**Surname:** Patel
**Birthdate:** November 3, 1995
**List of 5 companies:**
- Medtronic
- Johnson & Johnson
- Boston Scientific
- Abbott Laboratories
- Zimmer Biomet
**Key competencies:**
- Quality Management Systems
- Six Sigma Methodologies
- Quality Training & Development
- Risk Management
- Continuous Improvement
---
### Sample Resume 6
**Position number:** 6
**Person:** 6
**Position title:** Supplier Quality Technician
**Position slug:** supplier-quality-technician
**Name:** Brian
**Surname:** Lee
**Birthdate:** December 27, 1980
**List of 5 companies:**
- Boeing
- Lockheed Martin
- Raytheon
- Northrop Grumman
- General Dynamics
**Key competencies:**
- Supplier Audits
- Contract Compliance
- Quality Metrics Management
- Root Cause Corrective Action (RCCA)
- Supplier Relationship Management
---
Feel free to modify any details as needed!
---
### Sample 1
**Position number:** 1
**Position title:** Quality Assurance Technician
**Position slug:** quality-assurance-technician
**Name:** John
**Surname:** Smith
**Birthdate:** March 5, 1990
**List of 5 companies:** Apple, Microsoft, Intel, Samsung, IBM
**Key competencies:**
- Quality Control and Assurance
- Root Cause Analysis
- Statistical Process Control
- ISO 9001 Standards
- Problem Solving
---
### Sample 2
**Position number:** 2
**Position title:** Quality Control Technician
**Position slug:** quality-control-technician
**Name:** Sarah
**Surname:** Johnson
**Birthdate:** July 12, 1985
**List of 5 companies:** Tesla, Ford, GE, Dupont, Siemens
**Key competencies:**
- Inspection and Testing
- Data Analysis
- Compliance Audits
- Quality Improvement Strategies
- Team Collaboration
---
### Sample 3
**Position number:** 3
**Position title:** Manufacturing Quality Technician
**Position slug:** manufacturing-quality-technician
**Name:** Michael
**Surname:** Evans
**Birthdate:** September 14, 1992
**List of 5 companies:** Boeing, Lockheed Martin, Honeywell, Johnson Controls, 3M
**Key competencies:**
- Process Control
- Lean Manufacturing Principles
- Equipment Calibration
- Documentation and Reporting
- Training and Mentorship
---
### Sample 4
**Position number:** 4
**Position title:** Quality Assurance Analyst
**Position slug:** quality-assurance-analyst
**Name:** Emily
**Surname:** Davis
**Birthdate:** November 22, 1987
**List of 5 companies:** Google, Facebook, Amazon, Netflix, Adobe
**Key competencies:**
- Software Testing
- Test Case Development
- Defect Tracking
- Agile Methodologies
- User Acceptance Testing
---
### Sample 5
**Position number:** 5
**Position title:** Quality Improvement Technician
**Position slug:** quality-improvement-technician
**Name:** Robert
**Surname:** Brown
**Birthdate:** February 18, 1983
**List of 5 companies:** Pfizer, Merck, Novartis, GSK, AstraZeneca
**Key competencies:**
- Six Sigma
- Process Mapping
- Quality Metrics
- Training and Development
- Change Management
---
### Sample 6
**Position number:** 6
**Position title:** Field Quality Technician
**Position slug:** field-quality-technician
**Name:** Jessica
**Surname:** Wilson
**Birthdate:** May 30, 1995
**List of 5 companies:** Verizon, AT&T, Sprint, T-Mobile, Cisco
**Key competencies:**
- Customer Support and Service
- Field Inspections
- Technical Troubleshooting
- Data Collection and Reporting
- Compliance with Regulatory Standards
---
Feel free to modify any of the samples to better meet your needs!
Quality Technician Resume Examples: Top 6 Samples for Success in 2024
We are seeking a Quality Technician with a proven track record of leadership in quality assurance and process improvement. This role requires a detail-oriented professional who has successfully led cross-functional teams to enhance product integrity, resulting in a 15% reduction in defects over the past year. The ideal candidate will demonstrate strong collaborative skills, fostering a culture of continuous improvement among peers. With deep technical expertise in quality control methodologies and experience in conducting hands-on training sessions, the Quality Technician will empower teams to uphold high standards, ultimately elevating operational excellence and driving customer satisfaction.
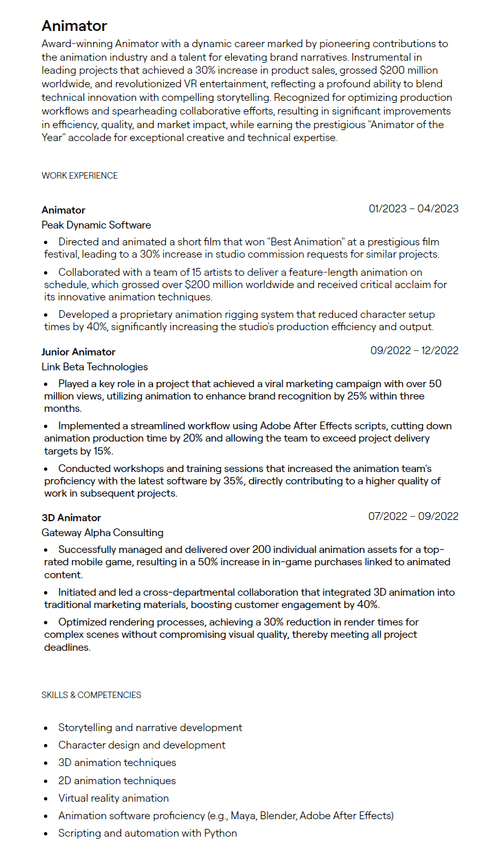
A quality technician plays a vital role in ensuring products meet rigorous standards and specifications, directly impacting customer satisfaction and brand reputation. This position demands attention to detail, strong analytical skills, and a deep understanding of quality control processes. To secure a job as a quality technician, candidates should pursue relevant certifications, such as Six Sigma or ISO standards, and gain experience in quality assurance through internships or entry-level roles in manufacturing or laboratory settings. Effective communication skills and the ability to work collaboratively in a team are equally important to ensure compliance and enhance production efficiency.
Common Responsibilities Listed on Quality Technician Resumes:
Here are ten common responsibilities typically listed on quality technician resumes:
Conduct Inspections: Perform regular inspections of products and processes to ensure compliance with quality standards and specifications.
Data Collection & Analysis: Collect and analyze data related to product quality, using statistical tools to identify trends and areas for improvement.
Documentation: Maintain accurate records of inspections, tests, and quality assessments, ensuring documentation is compliant with regulatory standards.
Quality Control Testing: Execute routine quality control tests on raw materials, in-process items, and finished products to verify their conformity.
Problem Resolution: Identify defects or quality issues and collaborate with production teams to implement corrective actions and prevent recurrence.
Training & Support: Provide training and support to production staff on quality control processes and best practices to enhance overall product quality.
Process Improvement: Participate in continuous improvement initiatives, such as Lean and Six Sigma, to optimize manufacturing processes and enhance quality.
Equipment Calibration: Ensure that measuring and testing equipment is calibrated and maintained to meet quality standards and regulatory requirements.
Supplier Quality Management: Assist in evaluating and monitoring supplier performance to ensure quality compliance of incoming materials.
Regulatory Compliance: Stay updated with industry regulations and standards to ensure that quality practices align with legal requirements and industry benchmarks.
When crafting a resume for the quality assurance technician position, it is crucial to highlight relevant experience with quality control methodologies, including statistical process control and root cause analysis. Emphasize familiarity with ISO 9001 standards and any previous roles that involved problem-solving in quality assurance settings. Showcase contributions to improving processes and ensuring compliance within high-tech environments. Additionally, including specific achievements or certifications that demonstrate expertise in quality control will strengthen the resume. Lastly, ensure that the key competencies align closely with the job description to capture the attention of potential employers effectively.
[email protected] • (555) 123-4567 • https://www.linkedin.com/in/johnsmith • https://twitter.com/johnsmith
Results-driven Quality Assurance Technician with extensive experience at leading technology companies such as Apple and Microsoft. Proficient in Quality Control and Assurance, Root Cause Analysis, and Statistical Process Control, with a solid understanding of ISO 9001 Standards. Demonstrates exceptional problem-solving abilities and a commitment to maintaining high standards in product quality. Adept at employing analytical skills to improve processes and enhance product performance. A collaborative team player with a track record of driving quality initiatives and fostering a culture of continuous improvement in fast-paced environments. Committed to achieving excellence in quality assurance practices.
WORK EXPERIENCE
- Led a team of 10 in implementing ISO 9001 standards, resulting in a 25% reduction in product defects.
- Conducted root cause analysis for recurring quality issues, successfully driving corrective actions that improved product reliability.
- Developed and executed Statistical Process Control (SPC) techniques, enhancing process efficiency and data accuracy.
- Collaborated with cross-functional teams to devise quality improvement initiatives, contributing to a 15% increase in overall production output.
- Championed internal audits to ensure compliance with quality benchmarks, fostering a culture of continuous improvement.
- Implemented and managed quality control processes across product lines, leading to an increase in customer satisfaction scores by 30%.
- Utilized advanced problem-solving techniques to address complex quality assurance challenges, reducing investigation time by 40%.
- Trained and mentored new team members in quality standards and protocols, enhancing team productivity and cohesion.
- Analyzed quality data to inform strategy development, driving initiatives that aligned with corporate objectives.
- Received the 'Excellence in Quality Award' for outstanding contributions to product quality improvement.
- Developed testing protocols for new products, ensuring stringent quality checks were adhered to before market release.
- Facilitated cross-departmental collaborations to align quality requirements with production capabilities, optimizing resource allocation.
- Drove process optimization projects through data analysis, improving operational efficiency by 20%.
- Conducted training sessions on quality standards and improvement techniques, elevating team competence in quality assurance practices.
- Regularly presented quality performance reports to senior management, influencing strategic decisions.
- Executed compliance audits that reinforced adherence to industry regulations, mitigating risks and enhancing overall quality.
- Participated in the development of quality training materials, ensuring a uniform understanding of quality processes across the team.
- Monitored product quality metrics, initiating troubleshooting processes for non-conforming products.
- Engaged in regular communication with stakeholders to report on quality initiatives and progress.
- Participated in continuous improvement programs that led to a sustainable quality management system.
SKILLS & COMPETENCIES
Here is a list of 10 skills for John Smith, the Quality Assurance Technician from Sample 1:
- Quality Control and Assurance
- Root Cause Analysis
- Statistical Process Control (SPC)
- ISO 9001 Standards
- Problem Solving Techniques
- Quality Auditing
- Data Analysis and Interpretation
- Risk Management
- Documentation and Reporting
- Cross-Functional Team Collaboration
COURSES / CERTIFICATIONS
Here’s a list of 5 certifications and completed courses for John Smith, the Quality Assurance Technician:
Certified Quality Technician (CQT)
Date Obtained: August 2018Six Sigma Green Belt Certification
Date Obtained: March 2019ISO 9001:2015 Internal Auditor Training
Date Completed: January 2020Statistical Process Control (SPC) Course
Date Completed: June 2021Root Cause Analysis Workshop
Date Completed: October 2022
EDUCATION
Education for John Smith
Bachelor of Science in Quality Assurance
University of California, Berkeley
Graduated: May 2012Certified Quality Technician (CQT)
American Society for Quality (ASQ)
Certified: August 2015
When crafting a resume for a Quality Control Technician, it is crucial to highlight relevant experience in inspection and testing processes, ensuring compatibility with industry standards. Emphasize skills in data analysis and compliance audits, showcasing the ability to identify and rectify quality issues. Demonstrating successful quality improvement strategies alongside team collaboration will strengthen the candidate's profile. Additionally, including previous experience with notable companies in manufacturing or engineering fields will enhance credibility. Quantifying achievements, such as improved efficiency rates or reduced defect levels, can further illustrate the candidate's impact in previous roles.
[email protected] • (555) 123-4567 • https://www.linkedin.com/in/sarahjohnson • https://twitter.com/sarahjohnson
Proactive and detail-oriented Quality Control Technician with over 10 years of experience in diverse industries including automotive and manufacturing. Proven expertise in inspection and testing methodologies, data analysis, and compliance audits, ensuring adherence to quality standards and regulations. Adept at developing and implementing quality improvement strategies, fostering team collaboration, and driving efficient processes. Recognized for strong problem-solving abilities and commitment to maintaining high-quality outcomes. Experienced in working with renowned companies like Tesla, Ford, and GE, bringing a keen eye for detail and a steadfast dedication to quality excellence.
WORK EXPERIENCE
- Conducted comprehensive inspections and testing on production line outputs which reduced product defects by 15%.
- Developed and implemented data analysis tools for tracking quality metrics, resulting in a 20% improvement in compliance rates.
- Led compliance audits and effectively collaborated with cross-functional teams to drive quality improvement initiatives.
- Trained and mentored junior team members on quality control processes and standards, enhancing team capability and morale.
- Streamlined reporting processes which decreased turnaround time for quality reports by 30%.
- Executed quality improvement strategies that increased efficiency by 25% while maintaining compliance with industry standards.
- Managed inspection processes of incoming materials, reducing errors by 10% through proactive vendor collaboration.
- Identified areas for improvement within the manufacturing workflow and implemented corrective actions, leading to a substantial decrease in cycle times.
- Coordinated with engineering teams to resolve quality issues, enhancing product reliability and customer satisfaction ratings.
- Played a key role in launching a new product line, ensuring all quality metrics were met during the initial production phase.
- Performed routine inspections and developed adherence protocols for quality compliance, improving audit scores by 40%.
- Analyzed quality data to identify trends and worked with production teams to implement corrective actions promptly.
- Facilitated workshops and training sessions for operational teams emphasizing the importance of quality control and best practices.
- Created detailed documentation for quality processes, enhancing knowledge transfer and team alignment.
- Collaborated with supply chain partners to ensure quality standards are met from source to production, reducing material quality issues by 50%.
- Lead quality monitoring initiatives across multiple production lines, achieving consistent product quality for high-stakes clients.
- Utilized Lean Six Sigma principles to enhance quality assurance processes, resulting in cost savings and reduced waste.
- Spearheaded a project that integrated new quality management software, increasing tracking efficiency and reporting capabilities.
- Mentored teams on statistical process control and quality standards, enhancing the overall quality culture within the organization.
- Recognized with the 'Excellence in Quality' award for exemplary commitment to quality standards and continuous improvement.
SKILLS & COMPETENCIES
Sure! Here is a list of 10 skills for Sarah Johnson, the Quality Control Technician from Sample 2:
- Inspection and Testing
- Data Analysis
- Compliance Audits
- Quality Improvement Strategies
- Team Collaboration
- Risk Assessment
- Documentation and Reporting
- Continuous Improvement Techniques
- Process Optimization
- Communication and Interpersonal Skills
COURSES / CERTIFICATIONS
Certifications and Courses for Sarah Johnson (Quality Control Technician)
Certified Quality Technician (CQT)
- Issuing Organization: American Society for Quality (ASQ)
- Date Obtained: March 2020
Six Sigma Green Belt Certification
- Issuing Organization: International Association for Six Sigma Certification (IASSC)
- Date Obtained: July 2019
ISO 9001:2015 Lead Auditor Training
- Issuing Organization: SGS
- Date Completed: February 2021
Quality Control Fundamentals Course
- Institution: Coursera (Offered by University of California, Irvine)
- Date Completed: November 2018
Advanced Data Analysis for Quality Control
- Institution: edX (Offered by MIT)
- Date Completed: April 2022
EDUCATION
Education for Sarah Johnson (Quality Control Technician)
Bachelor of Science in Industrial Engineering
University of Michigan, Ann Arbor
Graduated: May 2007Certified Quality Auditor (CQA)
American Society for Quality (ASQ)
Certification Date: June 2010
When crafting a resume for the Manufacturing Quality Technician position, it is crucial to emphasize key competencies such as process control and lean manufacturing principles, as they are vital in ensuring efficiency and quality in production. Highlight relevant experience with equipment calibration and documentation skills, demonstrating attention to detail. Training and mentorship abilities should also be noted, showcasing a commitment to team development. Additionally, mentioning experience with reputable companies in the aerospace or manufacturing sectors can enhance credibility. Tailoring the resume to reflect specific achievements and contributions in past roles will further strengthen the application.
[email protected] • +1-555-0123 • https://www.linkedin.com/in/michael-evans • https://twitter.com/michael_evans
Dedicated Manufacturing Quality Technician with a proven track record in ensuring optimal product quality within leading aerospace and technology companies such as Boeing and Lockheed Martin. Proficient in process control and lean manufacturing principles, I excel in equipment calibration and meticulous documentation. My expertise in training and mentorship fosters a culture of continuous improvement among team members. Committed to upholding the highest standards of quality, I leverage analytical skills to drive efficiency and minimize defects in production processes. Strong collaborative abilities enable me to thrive in fast-paced environments, delivering results that meet and exceed organizational objectives.
WORK EXPERIENCE
- Led a project on process control that improved production efficiency by 20%, significantly reducing waste.
- Implemented lean manufacturing principles that resulted in a 15% increase in product quality ratings.
- Trained new staff in quality assurance protocols, enhancing the team's capabilities and consistency.
- Collaborated with cross-functional teams to develop comprehensive documentation for process improvements.
- Conducted routine equipment calibration which decreased downtime by 30%.
- Developed and executed test cases that identified defects early in the development lifecycle, improving software quality by 25%.
- Established a standardized defect tracking system that streamlined the resolution process and improved team accountability.
- Participated in Agile ceremonies, providing insights that led to improved project timelines and team productivity.
- Worked closely with user experience teams to conduct user acceptance testing, ensuring high levels of customer satisfaction.
- Authored detailed compliance reports that facilitated successful audits by regulatory bodies.
- Executed quality improvement strategies that contributed to a 10% increase in overall operational efficiency.
- Led compliance audits, ensuring adherence to ISO 9001 standards and enhancing quality metrics.
- Utilized statistical process control techniques to analyze data and drive decision-making processes.
- Mentored junior technicians, fostering a culture of continuous improvement and professional development.
- Enhanced communication channels across production teams, resulting in reduced error rates in quality checks.
- Spearheaded quality assurance initiatives that led to a 30% improvement in customer feedback scores.
- Utilized Six Sigma methodologies to streamline processes and reduce costs, achieving significant savings for the organization.
- Collaborated with R&D departments to ensure that new product lines met stringent quality standards prior to launch.
- Generated detailed analysis reports that guided executive decisions, positively impacting strategic directions.
- Recognized for exemplary performance, receiving the 'Innovative Quality Leader Award' in 2023.
SKILLS & COMPETENCIES
Skills for Michael Evans (Manufacturing Quality Technician)
- Process Control
- Lean Manufacturing Principles
- Equipment Calibration
- Documentation and Reporting
- Training and Mentorship
- Quality Auditing
- Failure Mode and Effects Analysis (FMEA)
- Root Cause Analysis
- Continuous Improvement Strategies
- Team Leadership and Communication
COURSES / CERTIFICATIONS
Here is a list of 5 certifications and courses relevant for Michael Evans, the Manufacturing Quality Technician (Sample 3):
Certified Quality Engineer (CQE)
Issued by the American Society for Quality (ASQ)
Date: March 2021Lean Six Sigma Green Belt
Offered by the International Association for Six Sigma Certification
Date: June 2020ISO 9001:2015 Internal Auditor Training
Completed through the International Register of Certificated Auditors (IRCA)
Date: September 2019Root Cause Analysis Training
Conducted by the Quality Improvement Institute
Date: January 2022Statistical Process Control (SPC) Techniques
Completed with the Lean Manufacturing Certification Program
Date: July 2020
EDUCATION
Education for Michael Evans (Sample 3)
Bachelor of Science in Industrial Engineering
University of Michigan, Ann Arbor, MI
Graduation Year: 2014Certified Quality Engineer (CQE)
American Society for Quality (ASQ)
Certification Date: 2016
When crafting a resume for a Quality Assurance Analyst, it’s crucial to highlight expertise in software testing and agile methodologies. Emphasize proficiency in test case development and defect tracking, showcasing familiarity with various testing tools. Additionally, demonstrating strong analytical skills and attention to detail is essential, as is the ability to collaborate within an Agile team environment. Relevant certifications and experience with user acceptance testing can further strengthen the application. Highlighting contributions to past projects that improved software quality or enhanced team efficiency will also be beneficial in capturing the attention of potential employers.
[email protected] • +1-555-0134 • https://www.linkedin.com/in/emilydavisqa • https://twitter.com/emilydavisqa
Results-driven Quality Assurance Analyst with extensive experience in software testing and quality control across leading tech companies such as Google and Amazon. Proficient in test case development, defect tracking, and implementing Agile methodologies to enhance software quality and user satisfaction. Demonstrates strong analytical skills with a keen ability to identify issues, streamline processes, and collaborate effectively with cross-functional teams. Committed to continuous improvement, ensuring compliance with industry standards while delivering optimal solutions in fast-paced environments. Adept at user acceptance testing, seeking to leverage expertise to drive quality initiatives within innovative organizations.
WORK EXPERIENCE
- Led a team of testers in developing and executing test cases for multiple software applications, enhancing product quality by 30%.
- Implemented an automated testing framework that reduced testing time by 40%, allowing for quicker release cycles.
- Collaborated closely with product management and development teams to identify and fix defects, resulting in lower defect rates post-release.
- Conducted user acceptance testing (UAT) with clients, improving customer satisfaction scores by 25%.
- Standardized documentation processes for test cases and defect tracking, contributing to improved team efficiency.
- Spearheaded quality improvement initiatives that led to a 20% decrease in software bugs and significantly enhanced user experience.
- Developed training materials for new hires on quality assurance processes, resulting in a 50% reduction in onboarding time.
- Analyzed data from various projects to identify trends, leading to actionable insights that improved product functionalities.
- Played a key role in Agile ceremonies, contributing to continuous improvement and ensuring adherence to quality standards.
- Recognized for excellence in stakeholder communication, facilitating various client workshops for product feedback.
- Managed defect-tracking systems, prioritizing and coordinating defect resolution to meet project deadlines.
- Initiated quality audits that ensured compliance with regulatory standards, resulting in zero compliance issues during assessments.
- Utilized defect analytics to present regular reports to senior management, providing insights that influenced strategic decisions.
- Collaborated with cross-functional teams to enhance product usability based on insights gained from user testing.
- Received 'Employee of the Month' recognition twice for outstanding contributions to team success and product quality.
- Currently leading a project to integrate new testing methodologies that align with DevOps practices, aiming for faster deployment cycles.
- Mentored junior analysts in test case development and defect management, fostering a culture of continuous learning within the team.
- Collaborating with customer support teams to gather insights on user complaints and refining quality standards accordingly.
- Developing comprehensive test strategies that not only meet project requirements but also enhance overall product performance.
- Conducting regular training sessions on Agile methodologies and quality assurance best practices to ensure team alignment.
SKILLS & COMPETENCIES
Here are 10 skills for Emily Davis, the Quality Assurance Analyst from Sample 4:
- Software Testing
- Test Case Development
- Defect Tracking
- Agile Methodologies
- User Acceptance Testing
- Automated Testing Tools
- Performance Testing
- Quality Assurance Documentation
- Risk Assessment
- Cross-Functional Collaboration
COURSES / CERTIFICATIONS
Certainly! Here’s a list of 5 certifications and completed courses for Emily Davis, the Quality Assurance Analyst from Sample 4:
Certified Software Tester (CSTE)
Issued by: Quality Assurance Institute (QAI)
Date Completed: March 2018Agile Certified Practitioner (PMI-ACP)
Issued by: Project Management Institute (PMI)
Date Completed: July 2019ISTQB Certified Tester Foundation Level (CTFL)
Issued by: International Software Testing Qualifications Board (ISTQB)
Date Completed: November 2016Advanced Test Automation with Selenium
Provider: Udacity
Date Completed: February 2021User Acceptance Testing (UAT) Essentials
Provider: LinkedIn Learning
Date Completed: January 2022
EDUCATION
Education for Emily Davis (Quality Assurance Analyst)
Bachelor of Science in Computer Science
University of California, Berkeley
Graduated: May 2010Master of Science in Quality Assurance
Georgia Institute of Technology
Graduated: December 2013
When crafting a resume for a Quality Improvement Technician, it's crucial to highlight expertise in Six Sigma and process mapping, showcasing a strong foundation in quality metrics and continuous improvement methodologies. Include relevant experience in the pharmaceutical industry, emphasizing roles that involved training and development, as well as change management. Tailor the resume to demonstrate problem-solving skills and a track record of implementing successful quality initiatives. Utilize quantifiable achievements to illustrate the impact of previous work on organizational performance. Lastly, emphasize effective communication capabilities and teamwork, as collaboration is key in driving quality improvements across departments.
[email protected] • +1-234-567-8901 • https://www.linkedin.com/in/robertbrown • https://twitter.com/robertbrown
Dedicated Quality Improvement Technician with a robust background in the pharmaceutical industry, leveraging expertise gained at top companies like Pfizer and Merck. Proficient in Six Sigma methodologies and process mapping, Robert Brown excels in driving quality metrics and fostering training and development initiatives. A results-oriented professional, he is adept at change management, ensuring continuous improvement within processes. With a keen ability to analyze and implement quality improvement strategies, he is committed to enhancing operational efficiency while ensuring compliance with industry standards. Robert brings a strong foundation in quality assurance and is ready to contribute to organizational success.
WORK EXPERIENCE
- Led a Six Sigma project that improved production efficiency by 20%, resulting in an annual cost saving of $500,000.
- Developed and implemented quality metrics dashboards that improved stakeholders' decision-making speed by 35%.
- Facilitated training workshops for over 100 employees on quality assurance techniques and Six Sigma methodology.
- Spearheaded a cross-departmental initiative that improved product compliance with regulatory standards, which contributed to a 15% reduction in customer complaints.
- Collaborated with R&D teams to enhance product design processes, leading to a significant decrease in defects during the product launch phase.
- Conducted comprehensive audits across multiple departments, ensuring adherence to ISO 9001 standards.
- Implemented a new quality control process that reduced product processing time by 30%.
- Analyzed quality data and developed strategies that decreased return rates by 25%.
- Trained team members on new quality assurance protocols and digital tools, enhancing overall team productivity.
- Authored detailed reports on process vulnerabilities, which informed executive reviews and led to targeted improvement initiatives.
- Managed quality assurance testing for new drug applications, significantly contributing to successful FDA approvals.
- Developed intelligent defect tracking systems that significantly improved the identification and resolution of issues.
- Created and executed comprehensive test plans that ensured the quality and compliance of over 15 products.
- Worked closely with cross-functional teams to implement feedback from customers, resulting in a 40% increase in satisfaction scores.
- Recognized with the 'Excellence in Quality Award' for outstanding contributions to the company's product development lifecycle.
- Reduced production errors by 50% through process mapping and implementation of continuous improvement practices.
- Integrated lean manufacturing principles that improved workflow, resulting in a 20% increase in output capacity.
- Performed root cause analysis on production issues, leading to long-term solutions that improved product durability.
- Successfully led quality improvement initiatives that won internal recognition and boosted team morale.
- Developed training materials and conducted sessions for new hires on quality standards and company policies.
SKILLS & COMPETENCIES
Sure! Here are 10 skills for Robert Brown, the Quality Improvement Technician:
- Six Sigma Methodologies
- Process Mapping and Analysis
- Statistical Quality Control
- Quality Metrics Development
- Root Cause Analysis
- Change Management Strategies
- Project Management
- Training and Development Facilitation
- Continuous Improvement Techniques
- Regulatory Compliance Expertise
COURSES / CERTIFICATIONS
Here’s a list of 5 certifications or completed courses for Robert Brown, the Quality Improvement Technician:
Six Sigma Green Belt Certification
Date: March 2020Certified Quality Improvement Associate (CQIA)
Date: July 2019Lean Manufacturing Certification
Date: November 2018Quality Management System (QMS) Internal Auditor Training
Date: February 2017Process Mapping and Improvement Course
Date: April 2016
EDUCATION
Education for Robert Brown (Quality Improvement Technician)
Bachelor of Science in Engineering Management
University of Michigan, Ann Arbor, MI
Graduated: May 2005Six Sigma Green Belt Certification
American Society for Quality (ASQ)
Completed: March 2010
When crafting a resume for a Field Quality Technician, it's essential to highlight relevant experience in customer support and technical troubleshooting, as these roles require strong problem-solving skills and the ability to communicate effectively with clients. Emphasizing field inspection skills shows proficiency in real-world applications of quality assurance. Additionally, showcasing data collection and reporting capabilities is crucial, as it demonstrates analytical skills and attention to detail. Lastly, mentioning familiarity with regulatory standards illustrates adherence to compliance, which is vital in maintaining quality assurance in the field. Tailoring these aspects effectively can enhance the resume's impact.
[email protected] • (555) 123-4567 • https://www.linkedin.com/in/jessicawilson • https://twitter.com/jessicawilson
Dynamic and detail-oriented Field Quality Technician with a solid background in telecommunications. Adept at conducting field inspections and performing technical troubleshooting to ensure optimal service delivery. Proven experience in customer support and service, coupled with strong skills in data collection and reporting. Committed to compliance with regulatory standards, ensuring that all procedures meet established quality benchmarks. Possesses a collaborative mindset, effectively working alongside cross-functional teams to drive improvements and enhance customer satisfaction. Eager to leverage expertise to contribute to innovative solutions in a fast-paced environment within the telecommunications industry.
WORK EXPERIENCE
- Conducted thorough field inspections that improved compliance with regulatory standards by 30%.
- Implemented a new data collection process that enhanced reporting accuracy, leading to a 25% reduction in customer complaints.
- Collaborated with engineering and customer support teams to troubleshoot technical issues and provide swift resolutions, resulting in a 15% increase in customer satisfaction scores.
- Trained and mentored junior technicians, promoting best practices in compliance and inspection techniques.
- Developed and documented operational procedures that streamlined workflows and improved overall efficiency by 20%.
- Led a cross-functional team to execute quality audits, identifying areas for improvement which decreased operational defects by 40%.
- Used statistical analysis tools to track performance metrics and presented findings to senior management, aiding in strategic planning.
- Coordinated with field teams to implement real-time corrective actions, improving service delivery times by 18%.
- Spearheaded a quality improvement initiative that increased product reliability, contributing to a 10% boost in repeat business.
- Awarded 'Employee of the Year' for outstanding contributions to product quality and customer service in 2022.
- Resolved technical issues and provided solutions to clients, achieving a 95% first-call resolution rate.
- Delivered product knowledge training sessions, enhancing team capabilities and resulting in improved troubleshooting skills.
- Utilized customer feedback to drive improvements in service processes, culminating in a 20% increase in Net Promoter Score.
- Collaborated with product development teams to relay issues and contribute to product enhancements, ensuring better field performance.
- Maintained an organized log of service incidents and outcomes which improved future response strategies.
- Assisted in developing test cases for software products that increased testing efficiency by 15%.
- Participated in quality assurance reviews to evaluate compliance with established testing standards.
- Gathered and analyzed data on product performance, which was presented to the engineering team for product refinement.
- Facilitated communication between different departments to ensure alignment on quality goals and objectives.
- Helped create a knowledge base for common issues encountered in field inspections which served as a resource for new hires.
SKILLS & COMPETENCIES
Certainly! Here’s a list of 10 skills for Jessica Wilson, the Field Quality Technician:
- Customer Support and Service
- Field Inspections
- Technical Troubleshooting
- Data Collection and Reporting
- Compliance with Regulatory Standards
- Attention to Detail
- Strong Communication Skills
- Problem Solving
- Quality Assurance Testing
- Team Collaboration
COURSES / CERTIFICATIONS
Here’s a list of 5 certifications or completed courses for Jessica Wilson, the Field Quality Technician:
Certified Quality Improvement Associate (CQIA)
Issued by: ASQ (American Society for Quality)
Date: July 2021ISO 9001:2015 Internal Auditor Training
Provider: SGS Academy
Date: March 2022Lean Six Sigma Yellow Belt Certification
Provider: IASSC (International Association for Six Sigma Certification)
Date: November 2022Technical Troubleshooting and Root Cause Analysis Course
Provider: Coursera - University of California, Irvine
Date: January 2023Customer Support Essentials Certification
Provider: LinkedIn Learning
Date: April 2023
EDUCATION
Education for Jessica Wilson (Field Quality Technician)
Bachelor of Science in Quality Assurance
University of California, Berkeley
Graduated: May 2017Associate Degree in Applied Science - Quality Control Technology
City College of San Francisco
Graduated: May 2015
Crafting a compelling resume as a quality technician requires a strategic approach that highlights both technical proficiency and relevant experience. Start by tailoring your resume to the specific job description; thoroughly read the listing and incorporate keywords that reflect the qualities the employer seeks. Showcase your technical skills prominently, emphasizing familiarity with industry-standard tools such as Six Sigma methodologies, quality management software, and various measurement instruments. Consider creating a dedicated "Skills" section that not only details your technical capabilities but also includes soft skills like attention to detail, analytical thinking, and effective communication. These attributes are crucial in ensuring that quality standards are maintained and that issues are promptly identified and resolved.
In addition to presenting your skills effectively, your resume should include quantifiable achievements that demonstrate your impact in previous roles. Use metrics and concrete examples to illustrate how your quality control measures led to reduced error rates, improved compliance, or enhanced customer satisfaction. This will help potential employers visualize your contributions. Also, don’t forget the importance of layout and clarity; use bullet points for readability and maintain a professional yet approachable tone. Finally, consider adding a summary statement at the top of your resume to concisely convey your professional identity and key strengths. Remember, competition for quality technician positions can be fierce, so a well-structured and tailored resume is essential in setting yourself apart and aligning your expertise with the expectations of top companies. By strategically showcasing both your hard and soft skills and keeping your document aligned with industry standards, you substantially increase your chances of landing interviews and, ultimately, the job.
Essential Sections for a Quality Technician Resume
Contact Information
- Full name
- Phone number
- Email address
- LinkedIn profile (if applicable)
- Location (City, State)
Professional Summary
- Brief summary of qualifications
- Highlight key skills and experience
- Mention specific industry experience
Skills
- Technical skills related to quality assurance
- Familiarity with quality management systems (e.g., ISO, Six Sigma)
- Proficiency in quality inspection tools and software
Work Experience
- Job titles and company names
- Dates of employment (month/year)
- Key responsibilities and achievements
- Relevant metrics or results
Education
- Degree(s) obtained
- Major or field of study
- Name of institution
- Graduation date
Certifications
- Relevant certifications (e.g., CQI, CQT)
- Dates achieved and issuing organizations
Professional Affiliations
- Membership in relevant industry organizations
- Participation in professional events or committees
Additional Sections to Consider for a Competitive Edge
Projects
- Specific projects related to quality improvement
- Tools and methodologies used
- Outcomes and impact on the organization
Technical Proficiencies
- Software and tools used (e.g., statistical analysis software, ERP systems)
- Familiarity with programming languages (if applicable)
- Knowledge of data analysis techniques
Awards and Recognitions
- Any awards received related to quality assurance or work performance
- Acknowledgment from peers or management
Publications and Presentations
- Articles or papers published in industry journals
- Presentations given at conferences or industry events
Language Skills
- Proficiency in multiple languages (if relevant to the job)
- Certifications for language proficiency
Volunteer Experience
- Roles in volunteer organizations
- Relevant skills or knowledge gained through volunteer work
Generate Your Resume Summary with AI
Accelerate your resume crafting with the AI Resume Builder. Create personalized resume summaries in seconds.
Crafting an impactful resume headline is essential for quality technicians seeking to make a strong first impression with hiring managers. Your headline serves as a snapshot of your skills and specializations, effectively communicating what you bring to the table in a competitive field.
To create a compelling headline, start by clearly identifying your primary area of expertise within quality assurance or quality control. For example, instead of a generic statement like “Quality Technician,” consider something more descriptive, such as “Experienced Quality Technician Specializing in FDA Compliance and Six Sigma Methodologies.” This specificity not only highlights your skills but also makes it easier for hiring managers to see your fit for the role.
Additionally, infuse your headline with distinctive qualities or notable career achievements that differentiate you from other candidates. If you’ve led successful audits, reduced defect rates, or implemented innovative quality control processes, consider incorporating these elements into your headline. Phrasing like “Proven Record in Elevating Quality Standards and Enhancing Operational Efficiency” can showcase your impact effectively.
Remember that your headline sets the tone for the rest of your application and serves as an invitation for hiring managers to explore your qualifications further. Aim for clarity and brevity—ideally, your headline should be a single sentence or phrase that encapsulates your professional essence.
Lastly, tailor your headline to align with the specific job description you are applying for. Highlighting key skills and experiences mentioned in the job posting can further resonate with the hiring manager, demonstrating not only your qualifications but also your genuine interest in the position. By strategically crafting your resume headline, you will capture attention, generate interest, and increase your chances of advancing in the hiring process.
Quality Assurance Technician Resume Headline Examples:
Strong Resume Headline Examples
Strong Resume Headline Examples for Quality Technician
"Detail-Oriented Quality Technician with 5+ Years of Experience in ISO 9001 Compliance and Quality Assurance Processes"
"Results-Driven Quality Technician Specializing in Root Cause Analysis and Continuous Improvement Methodologies"
"Certified Quality Technician with Proven Track Record in Reducing Defect Rates by 30% Through Effective Quality Control Measures"
Why These are Strong Headlines
Clarity and Specificity: Each headline clearly states the job title and key qualifications, making it immediately obvious to hiring managers what role the candidate is targeting and what skills they bring. By specifying areas of expertise, like ISO 9001 Compliance or Root Cause Analysis, the candidate positions themselves as knowledgeable in vital industry standards and practices.
Quantifiable Achievements: Including specific metrics (e.g., “5+ years of experience” or “Reducing Defect Rates by 30%”) provides tangible evidence of the candidate's capabilities and impact in their previous roles. This helps in grabbing the attention of employers who value proven results and effectiveness.
Industry-Relevant Keywords: Each headline incorporates relevant industry terms and certifications, which not only resonates with hiring managers but also aids in passing Applicant Tracking Systems (ATS). Modern recruitment practices often use these systems to filter resumes, so including keywords related to quality control and technician expertise enhances the likelihood of being noticed.
Weak Resume Headline Examples
Weak Resume Headline Examples for Quality Technician
- "Quality Technician Seeking Job"
- "Experienced in Quality Control"
- "Hardworking Individual Looking for Opportunities"
Why These are Weak Headlines
"Quality Technician Seeking Job": This headline is vague and lacks specificity. It does not highlight any particular skills, achievements, or areas of expertise that would make the candidate stand out from others who are also seeking jobs. A stronger headline would articulate specialized skills or unique qualities.
"Experienced in Quality Control": While this headline notes experience, it is overly simplistic and does not define the level of expertise, the types of quality control processes the candidate is familiar with, or any relevant certifications or tools used. It misses an opportunity to showcase key qualifications that would attract potential employers.
"Hardworking Individual Looking for Opportunities": This headline is generic and unremarkable. Phrases like "hardworking" are commonly used and do not provide specific insights into the candidate’s skills or successes in the quality sector. Moreover, it lacks any mention of the technician's role, expertise, or unique contributions they could bring to a prospective employer.
Overall, weak headlines fail to convey a strong personal brand, lack specificity, and do not effectively market the candidate’s qualifications to potential employers, making it challenging to capture attention in a competitive job market.
An exceptional resume summary for a Quality Technician serves as your professional snapshot, effectively conveying your qualifications and setting you apart in a competitive job market. This brief description is crucial, as it encapsulates your experience, technical skills, and collaborative abilities, enabling potential employers to quickly grasp your value. An engaging summary highlights not just facts but also captures your story, demonstrating your passion for quality assurance. Tailoring your resume summary to align with the specific role you’re targeting enhances its impact, ensuring it resonates with hiring managers and reflects your unique fit for the position.
Key Points to Include in Your Quality Technician Resume Summary:
- Years of Experience: Clearly state your years of relevant experience in quality assurance, underscoring your seasoned perspective on industry best practices.
- Specialized Industries: Mention any specific industries in which you have expertise (e.g., manufacturing, pharmaceuticals, food safety) to highlight your adaptability and sector knowledge.
- Technical Proficiency: Highlight your proficiency with quality management software and tools (like Six Sigma, ISO standards, or statistical analysis software) to show your technical capability and commitment to compliance.
- Collaboration and Communication Skills: Emphasize your ability to work in cross-functional teams and communicate effectively with stakeholders, as teamwork is integral to quality assurance.
- Attention to Detail: Illustrate your meticulous approach to quality control, showcasing how your keen eye for detail has led to successful project outcomes or process improvements.
By integrating these elements into your summary, you create a robust introduction that captures your expertise and aligns with the needs of potential employers.
Quality Assurance Technician Resume Summary Examples:
Strong Resume Summary Examples
Resume Summary Examples for Quality Technician
Detail-oriented Quality Technician with over 5 years of experience in implementing quality control processes and conducting rigorous testing protocol. Proven track record of enhancing product quality and safety through meticulous inspections and collaboration with production teams. Adept at using analytical software and quality management systems to drive continuous improvement.
Proficient Quality Technician with extensive knowledge of ISO 9001 standards and hands-on experience in monitoring production processes. Skilled in identifying quality issues, performing root cause analysis, and executing corrective actions to maintain product integrity. Strong communication and teamwork skills, leading to improved operational efficiency.
Certified Quality Technician with a strong background in statistical process control and quality assurance methodologies. Over 4 years of experience working in fast-paced manufacturing environments, ensuring compliance with industry regulations and standards. Passionate about fostering a culture of quality and continuous improvement among team members.
Why These Are Strong Summaries
Clarity and Relevance: Each summary clearly states the candidate's role (Quality Technician) and provides specifics about their experience, skills, and achievements. This relevance makes it easy for hiring managers to quickly assess the candidate's fit for the role.
Quantifiable Achievements: By including specific years of experience and references to standards like ISO 9001, the summaries demonstrate the candidate's expertise and reliability, which adds credibility and showcases measurable adherence to industry standards.
Focus on Skills and Impact: The summaries highlight not only technical skills (like knowledge of statistical process control) but also soft skills (such as teamwork and communication). This balance showcases the candidate's well-rounded capabilities and their potential impact on the organization, which is crucial for a Quality Technician role.
Commitment to Improvement: Phrases like "continuous improvement" and "fostering a culture of quality" signal the candidate's proactive attitude and dedication to excellence. This is attractive to employers looking for team members who can contribute to long-term success in quality management.
Lead/Super Experienced level
Sure! Here are five strong resume summary examples for a Lead/Super Experienced Quality Technician:
Quality Leadership Expertise: Over 10 years of experience in quality control and assurance within manufacturing environments, adept at leading cross-functional teams to implement quality systems that enhance product reliability and comply with industry standards.
Process Improvement Advocate: Proven track record of utilizing Six Sigma and Lean methodologies to streamline quality processes, resulting in a 30% reduction in defect rates and significant cost savings for previous employers.
Advanced Problem-Solving Skills: Skilled in conducting root cause analysis and implementing corrective actions, effectively resolving complex quality issues that improve customer satisfaction and drive operational excellence.
Regulatory Compliance Champion: Extensive knowledge of ISO, FDA, and other regulatory standards, with a strong ability to audit and ensure compliance, contributing to successful certifications and maintaining high-quality benchmarks in production.
Training and Development Focus: Committed to fostering a culture of quality, with experience in developing and delivering training programs for personnel at all levels to enhance understanding of quality principles and promote best practices across the organization.
Senior level
Sure! Here are five strong resume summary examples for a Senior Quality Technician:
Detail-Oriented Quality Expert: Seasoned Quality Technician with over 10 years of experience in ensuring compliance with industry standards and regulations, leading successful quality improvement initiatives that resulted in a 20% reduction in defects.
Process Improvement Specialist: Proficient in utilizing Six Sigma methodologies to identify process inefficiencies and implement corrective actions, enhancing overall product quality and customer satisfaction in a fast-paced manufacturing environment.
Cross-Functional Team Leader: Recognized for fostering collaboration across engineering, production, and quality departments, leading to streamlined operations and improved product quality metrics by 30% over two years.
Strategic Quality Assurance Professional: Committed to maintaining high-quality standards through rigorous testing and inspection processes; successfully managed multiple projects with diverse teams to achieve ISO 9001 certification in record time.
Innovative Problem Solver: Experienced in employing advanced statistical analysis and quality control tools; effectively reduced product non-conformance rates through proactive inspection and continuous training programs for technical staff.
Mid-Level level
Sure! Here are five bullet point examples of strong resume summaries for a mid-level Quality Technician:
Detail-oriented Quality Technician with over 5 years of experience in implementing quality control processes and conducting thorough inspections, ensuring compliance with industry standards and regulations.
Skilled in using various measurement tools and techniques to analyze product specifications, contributing to a 15% reduction in defects through proactive quality improvement initiatives.
Proven track record of collaborating with cross-functional teams to develop and execute corrective action plans, enhancing product reliability and increasing customer satisfaction ratings.
Advanced knowledge of quality management systems and methodologies, including Six Sigma and ISO 9001, with a successful history of leading audits and training staff on quality assurance practices.
Strong problem-solving skills with the ability to quickly identify issues and implement effective solutions, resulting in streamlined operations and improved efficiency across production lines.
Junior level
Here are five strong resume summary examples for a junior experienced quality technician:
Detail-oriented quality technician with over 2 years of hands-on experience in conducting inspections and testing processes in manufacturing environments. Proven ability to identify defects and implement corrective actions to improve product quality.
Motivated quality technician equipped with foundational knowledge in quality assurance principles and methodologies. Successfully supported senior staff in performing audits and compiling quality reports, demonstrating a commitment to continuous improvement.
Enthusiastic quality technician with a solid background in ISO 9001 standards and quality control procedures. Adept at utilizing measuring instruments and software tools to analyze data and enhance production quality.
Results-driven quality technician with experience in collaborating with cross-functional teams to ensure compliance with quality standards. Strong analytical skills with the ability to troubleshoot issues and recommend effective solutions.
Dedicated to achieving high levels of customer satisfaction, while maintaining quality standards. Familiar with inspection techniques and quality documentation, eager to contribute to a dynamic quality assurance team.
Entry-Level level
Entry-Level Quality Technician Resume Summary Examples:
Detail-oriented recent graduate with a degree in Industrial Engineering, eager to apply knowledge of quality control methods and processes to ensure product excellence in a fast-paced manufacturing environment.
Highly motivated individual with hands-on experience in laboratory quality testing; skilled in using various measuring instruments and adhering to safety protocols to achieve accurate results in compliance with industry standards.
Recent technical school graduate with foundational training in quality assurance techniques and a demonstrated commitment to maintaining high standards of product integrity and process efficiency.
dedicated team player seeking a Quality Technician position, equipped with strong analytical skills and a passion for problem-solving, ready to contribute to quality improvements and enhance operational workflows.
Self-starter with a solid background in customer service and teamwork, keen to leverage attention to detail and a commitment to quality in an entry-level role to support compliance and continuous improvement initiatives.
Experienced Quality Technician Resume Summary Examples:
Accomplished Quality Technician with over 5 years of experience in the manufacturing sector, specializing in quality assurance and control, and a proven track record of reducing defects by implementing effective inspection protocols.
Results-driven professional with extensive knowledge of ISO 9001 standards and statistical quality control (SQC) methodologies, dedicated to ensuring product compliance and enhancing operational efficiency through data-driven decision-making.
Seasoned Quality Technician adept at utilizing advanced quality inspection tools and techniques; successfully led cross-functional teams to implement corrective actions and improve product quality in alignment with customer specifications.
Exceptional problem solver with expertise in performing root cause analysis and driving continuous improvement initiatives; recognized for developing innovative quality training programs that enhance employee skills and promote a culture of quality.
Versatile Quality Technician with comprehensive experience in both incoming and in-process quality inspections; strong communicator and collaborator, committed to fostering teamwork and achieving organizational quality objectives.
Weak Resume Summary Examples
Weak Resume Summary Examples for Quality Technician
"I am a quality technician looking for a job in a manufacturing company. I have done quality control in the past."
"Experienced technician seeking opportunities in quality assurance. I am adaptable and have a variety of experience."
"As a quality technician with some experience, I want to work at your company and help improve your products."
Why These are Weak Headlines:
Lack of Specificity: Each summary is vague and does not provide concrete examples of skills or achievements. For instance, stating "I have done quality control in the past" does not indicate what specific tasks were performed or what the outcomes were.
Absence of Value Proposition: The summaries fail to showcase what unique value the candidate brings to the employer. Phrases like "I want to work at your company" sound passive and do not highlight any qualities that would make the candidate an asset.
Generic Language: The use of generic terms like "variety of experience" and "some experience" does not give a clear picture of the applicant's expertise or the depth of their knowledge in quality assurance processes, tools, or methodologies. It creates an impression of a lack of confidence or commitment.
Resume Objective Examples for Quality Assurance Technician:
Strong Resume Objective Examples
Detail-oriented quality technician with over 4 years of experience in the manufacturing sector, seeking to leverage expertise in quality assurance processes to enhance product reliability and drive continuous improvement within a results-oriented team.
Committed quality technician with a proven track record in conducting rigorous testing and inspections, aiming to apply analytical skills and knowledge of industry standards at [Company Name] to achieve excellence in product quality and compliance.
Results-driven quality technician with comprehensive knowledge of quality control methodologies, looking to contribute to [Company Name]'s mission by ensuring high levels of product integrity and supporting efforts in achieving optimal production performance.
Why this is a strong objective:
These objectives are effective because they are specific, providing details about the candidate's experience and skills relevant to the role. Each statement highlights the candidate's commitment to quality, the ability to enhance processes, and a clear intent to contribute to the prospective employer's goals. Additionally, they focus on results and continuous improvement, which are key qualities in a quality technician, making them compelling and targeted to attract the attention of hiring managers.
Lead/Super Experienced level
Here are five strong resume objective examples for a Lead/Super Experienced Quality Technician:
Detail-Oriented Quality Leader: Accomplished Quality Technician with over 10 years of experience in quality assurance and process improvement. Seeking to leverage extensive knowledge of compliance standards and team leadership skills to enhance product quality and operational efficiency at [Company Name].
Results-Driven Quality Assurance Expert: Seasoned Quality Technician with a proven track record in reducing defects by 30% through innovative quality control systems. Aiming to contribute leadership expertise and strategic insight to drive excellence in quality manufacturing processes at [Company Name].
Dynamic Quality Control Supervisor: Experienced professional with 15 years in quality inspection, leading high-performing teams to exceed quality benchmarks. Passionate about applying strong analytical and problem-solving skills to optimize quality processes and foster a culture of continuous improvement at [Company Name].
Innovative Quality Assurance Specialist: Senior Quality Technician with extensive experience in implementing lean methodologies and Six Sigma principles. Looking to utilize advanced knowledge in quality systems and leadership to mentor teams and elevate product standards within [Company Name].
Strategic Quality Improvement Leader: Quality Technician with an exceptional ability to analyze quality data and implement process enhancements. Seeking to join [Company Name] to lead quality initiatives, improve customer satisfaction, and ensure regulatory compliance through effective team collaboration.
Senior level
Here are five strong resume objective examples for a senior-level quality technician:
Results-Driven Quality Assurance Expert: Seeking to leverage over 10 years of extensive experience in quality management and process improvement to enhance the product quality and operational efficiency at [Company Name]. Committed to utilizing data-driven approaches and team collaboration to exceed industry standards.
Dedicated Quality Technician with Leadership Skills: Aiming to apply my proven track record of implementing quality control measures and training junior staff to uphold and elevate quality standards at [Company Name]. Passionate about fostering a culture of continuous improvement and innovation.
Detail-Oriented Quality Assurance Specialist: Looking to contribute my expertise in ISO standards and advanced statistical analysis to [Company Name]. Equipped with a strong background in root cause analysis, I'm dedicated to identifying and addressing quality issues proactively.
Proactive Quality Technician with Advanced Troubleshooting Skills: Eager to join [Company Name] to utilize my 12+ years of experience in troubleshooting and quality inspection. Focused on developing effective quality systems that drive customer satisfaction and reduce operational costs.
Strategic Quality Management Professional: Desire to bring my extensive experience in quality control processes and regulatory compliance to [Company Name]. A keen ability to lead cross-functional teams and implement strategic quality initiatives to enhance overall product reliability and safety.
Mid-Level level
Here are five strong resume objective examples for a mid-level quality technician:
Detail-Oriented QA Specialist: Results-driven quality technician with over 5 years of experience in implementing and improving quality control processes. Seeking to leverage expertise in data analysis and problem-solving to enhance product quality at XYZ Company.
Process Improvement Advocate: Mid-level quality technician skilled in conducting thorough audits and inspections to ensure compliance with industry standards. Aiming to contribute to continuous improvement initiatives and quality assurance strategies at ABC Manufacturing.
Analytical Quality Technician: Dedicated quality technician with extensive experience in root cause analysis and corrective action processes. Eager to apply analytical skills and quality management expertise to support XYZ Corp's commitment to exceptional product standards.
Team-Oriented Quality Assurance Professional: Collaborative quality technician with 4 years of hands-on experience in cross-functional teams. Looking to utilize strong communication and technical skills to foster a quality-driven culture at ABC Inc.
Compliance-Focused Quality Technician: Quality assurance professional with a proven track record in maintaining industry compliance while optimizing operations. Seeking to bring a proactive approach to quality assurance practices to enhance the efficiency and effectiveness of quality control at DEF Industries.
Junior level
Sure! Here are five bullet points of strong resume objective examples for a Junior Quality Technician:
Detail-oriented recent graduate with a background in quality assurance and a keen eye for identifying discrepancies, seeking to leverage analytical skills to contribute to quality control efforts at [Company Name].
Motivated Junior Quality Technician with hands-on experience in inspection and testing, eager to apply knowledge of ISO standards and quality protocols to enhance product quality and operational efficiency.
Enthusiastic quality assurance professional with practical internship experience in manufacturing environments, aiming to support the quality control team at [Company Name] by ensuring compliance with industry standards and regulations.
Dedicated team player with foundational skills in quality analysis and problem-solving, seeking to bring a strong commitment to maintaining high standards of quality and consistency in production processes.
Results-driven individual with a passion for quality improvement, looking to utilize skills in data analysis and reporting to help [Company Name] achieve its quality targets and foster a culture of excellence.
Entry-Level level
Sure! Here are five strong resume objective examples for an entry-level quality technician position:
Detail-Oriented and Analytical: Recent graduate with a degree in Industrial Engineering, seeking to leverage strong analytical skills and attention to detail in an entry-level quality technician role. Committed to ensuring product integrity and compliance with industry standards.
Hands-On Experience with Quality Control: Eager to apply hands-on experience in laboratory settings and knowledge of quality control processes as an entry-level quality technician. Aiming to contribute to a team dedicated to maintaining high-quality standards in manufacturing.
Team Player with a Passion for Quality: Motivated individual with a background in life sciences looking to break into the quality assurance field. Seeking to bring strong problem-solving abilities and a passion for quality to a dynamic quality technician position.
Strong Technical Skills: Entry-level quality technician with a solid foundation in statistical process control and quality measurement tools. Driven to support a positive work environment while ensuring that products meet rigorous quality standards.
Dedicated and Eager to Learn: Aspiring quality technician and recent graduate with a proven track record of academic excellence in quality management principles. Excited to utilize fresh perspectives and learn from experienced professionals while contributing to the quality assurance team.
Weak Resume Objective Examples
Weak Resume Objective Examples for a Quality Technician:
"Looking for a quality technician position where I can use my skills to help the company."
"To obtain a job as a quality technician and gain experience in the field."
"Seeking a quality technician role to contribute to the team while hoping to learn more about quality control."
Why These Objectives Are Weak:
Lack of Specificity: The objectives do not specify what skills or qualifications the candidate possesses that relate to the role. Vague statements such as "use my skills" or "gain experience" don't clearly communicate the candidate's value to the employer or how they can contribute to the organization.
Focus on Personal Gain: Phrases like "hoping to learn more" or "gain experience" highlight the candidate's personal aspirations rather than the needs of the employer. Objective statements should focus on how the candidate's skills and experiences can benefit the organization, rather than on what the candidate hopes to achieve.
No Unique Value Proposition: These objectives lack a unique angle or value proposition that sets the candidate apart from others. Exceptional objectives convey a sense of enthusiasm and tailored skills relevant to the specific job, whereas these examples appear generic and unremarkable, making it difficult for employers to see why they should choose this candidate over others.
Crafting an effective work experience section for a Quality Technician resume requires precision, clarity, and relevance. Here’s a guide to ensure that your experience stands out:
Structure: Start with your job title, followed by the company name, location, and dates of employment. Use a clear and consistent format throughout. For example:
- Quality Technician, ABC Manufacturing, Chicago, IL | June 2020 – Present
Bullet Points Over Paragraphs: Use bullet points to enhance readability. Each point should focus on achievements and responsibilities rather than general tasks.
Quantifiable Achievements: Highlight your accomplishments with numbers or percentages to illustrate impact. For example:
- Reduced defect rates by 15% through the implementation of a new quality control protocol.
Action Verbs: Begin each bullet with powerful action verbs (e.g., Developed, Implemented, Analyzed) to convey initiative and impact.
Relevant Skills: Focus on skills related to quality assurance, such as inspection methodologies, data analysis, or proficiency in quality management software. For instance:
- Conducted detailed inspections and tests on incoming materials, ensuring compliance with industry standards.
Collaboration and Communication: Describe your role in cross-functional teams. This shows your ability to work collaboratively and communicate effectively. For example:
- Collaborated with engineering and production teams to identify and rectify quality issues swiftly.
Continuous Improvement: Emphasize your commitment to improving processes. Mention participation in initiatives like Six Sigma or Lean methodologies:
- Participated in Six Sigma projects that enhanced process efficiency by 20%.
Customization: Tailor this section for each application by mirroring the language and requirements of the job description. Highlight experiences that align closely with the prospective employer’s needs.
Incorporating these elements will create a compelling work experience section that effectively showcases your qualifications as a Quality Technician, increasing your chances of landing an interview.
Best Practices for Your Work Experience Section:
Here are 12 best practices for crafting an effective Work Experience section for a Quality Technician resume:
Use Clear Job Titles: Clearly label your job titles to reflect your role as a quality technician, ensuring relevance and clarity.
Prioritize Relevant Experience: List your most relevant work experience first, focusing on positions that align closely with quality assurance and control.
Quantify Achievements: Use numbers to illustrate your impact, such as "Reduced defects by 20%," which adds credibility and showcases your contributions.
Highlight Technical Skills: Emphasize specific skills related to quality assurance, such as experience with inspections, testing methods, and quality management systems (e.g., ISO 9001).
Use Action Verbs: Begin bullet points with strong action verbs like "Conducted," "Developed," "Implemented," and "Analyzed" to convey proactivity and initiative.
Include Certifications: Mention any relevant certifications, such as Six Sigma or Quality Auditor, to demonstrate your commitment to quality standards.
Detail Responsibilities: Describe your day-to-day responsibilities clearly, focusing on tasks you performed that relate directly to quality processes.
Emphasize Problem-Solving: Highlight instances where you identified and resolved quality issues, showcasing your analytical thinking and ability to improve processes.
Show Collaboration: Illustrate your ability to work with cross-functional teams, indicating your skills in communication and teamwork within quality assurance contexts.
Focus on Compliance: Mention any compliance or regulatory standards you worked with, indicating your understanding of industry requirements.
Tailor Content to the Job Description: Adjust your work experience section to align with the keywords and requirements listed in the job description you are applying for.
Maintain a Professional Format: Use a clean, easy-to-read format with consistent font sizes, bullet points, and spacing to present your experience clearly and professionally.
By following these best practices, you can create a compelling Work Experience section that effectively showcases your qualifications as a Quality Technician.
Strong Resume Work Experiences Examples
Resume Work Experiences Examples for Quality Technician
Performed Rigorous Quality Inspections: Executed detailed inspections and tests on incoming materials, in-process components, and finished products, achieving a 98% compliance rate with industry standards, which significantly reduced defects and rework costs.
Implemented Quality Improvement Initiatives: Spearheaded a quality improvement project that utilized statistical process control (SPC) techniques, resulting in a 25% increase in process efficiency and a notable decrease in scrap rates over a six-month period.
Led Cross-Functional Training Sessions: Developed and conducted training workshops for production team members on quality assurance best practices, enhancing team understanding of quality metrics and processes, which improved overall team performance and accountability.
Why These are Strong Work Experiences
Quantifiable Achievements: Each bullet point includes specific metrics (e.g., 98% compliance rate, 25% increase in efficiency) which provide clear evidence of past successes and the impact of the candidate's contributions, making accomplishments tangible.
Proactive Role: Demonstrating initiative—such as leading projects and training sessions—highlights the candidate’s leadership skills and commitment to continuous improvement, traits that are highly valued in quality assurance roles.
Relevance to Industry Standards: The mention of techniques like statistical process control illustrates both technical proficiency and an understanding of industry practices, showcasing the candidate's ability to apply specialized knowledge effectively within their role.
Lead/Super Experienced level
Certainly! Here are five bullet points for a strong resume that highlight work experience for a Lead/Super Experienced Quality Technician:
Led a team of 10 quality technicians to implement a robust quality assurance program, resulting in a 30% reduction in product defects and significant improvements in overall production efficiency.
Developed and executed comprehensive training programs for new hires and existing staff, enhancing quality control processes and ensuring adherence to industry standards, which increased compliance ratings by 25%.
Spearheaded cross-functional quality improvement initiatives, collaborating with engineering and production departments to identify root causes of quality issues and implementing corrective actions that improved customer satisfaction scores by 15%.
Utilized advanced statistical process control (SPC) techniques to analyze production data and identify trends, enabling proactive decision-making and a 40% improvement in process reliability over a 12-month period.
Established and maintained effective quality documentation systems and audits, facilitating ISO certification renewal and achieving zero non-conformities during the latest compliance inspection.
Senior level
Sure! Here are five strong bullet point examples of work experience for a Senior Quality Technician:
Led cross-functional teams in implementing quality management systems, resulting in a 30% reduction in product defects and increased compliance with industry standards and customer specifications.
Developed and executed comprehensive testing protocols and inspection schedules, which improved workflow efficiency and reduced time-to-market for new products by 15%.
Trained and mentored junior quality technicians on best practices in quality assurance, fostering a culture of continuous improvement and elevating the team's overall performance.
Utilized statistical process control (SPC) and Six Sigma methodologies to analyze production data, driving initiatives that decreased variability and enhanced overall product reliability.
Collaborated with suppliers and internal stakeholders to resolve quality issues, successfully negotiating corrective actions and implementing preventive measures that resulted in a 25% decrease in return rates.
Mid-Level level
Certainly! Here are five strong resume work experience examples tailored for a mid-level Quality Technician:
Quality Assurance Compliance: Developed and implemented quality control procedures that improved product defect identification by 25%, ensuring 100% compliance with industry standards and regulatory requirements.
Process Improvement: Led a cross-functional team to analyze and refine manufacturing processes, resulting in a 15% reduction in production downtime and a significant cost saving of $50,000 annually.
Training & Development: Conducted training sessions for new hires and ongoing staff on quality management systems and inspection techniques, enhancing team competency and decreasing error rates by 30%.
Data Analysis: Utilized statistical quality control (SQC) methods to analyze production data and identify trends, which informed corrective actions and contributed to a 20% increase in overall product quality.
Customer Complaint Resolution: Collaborated with customer service and engineering teams to investigate product defects and resolve customer complaints efficiently, leading to a 40% improvement in customer satisfaction scores.
Junior level
Sure! Here are five bullet point examples for a junior-level quality technician resume:
Conducted routine quality inspections on production lines, ensuring compliance with industry standards and company specifications, which resulted in a 15% decrease in defects over six months.
Assisted in developing and implementing standard operating procedures (SOPs) for quality control processes, leading to improved efficiency and accuracy in inspections and reporting.
Collaborated with cross-functional teams to troubleshoot quality issues, contributing to the identification and resolution of root causes that enhanced overall product quality.
Utilized measuring and testing equipment to perform product evaluations, documenting findings and providing actionable insights that supported continuous improvement initiatives.
Participated in quality audits and assessments, providing detailed reports and suggestions for corrective actions that facilitated compliance with regulatory requirements and improved operational practices.
Entry-Level level
Certainly! Here are five bullet point examples of strong resume work experiences for an entry-level quality technician:
Conducted routine inspections of production processes to ensure adherence to quality standards, precision measuring equipment, and tools, leading to a 15% reduction in defects.
Assisted in the development and implementation of quality control procedures, utilizing statistical analysis tools to identify areas for improvement and enhance overall product quality.
Collaborated with cross-functional teams to troubleshoot and resolve quality issues, effectively communicating findings to the production team, which resulted in a 10% increase in operational efficiency.
Participated in training sessions focused on quality assurance methodologies and best practices, gaining hands-on experience in ISO 9001 standards and lean manufacturing techniques.
Maintained comprehensive documentation of quality control inspections and test results, ensuring compliance with regulatory requirements and facilitating seamless audits.
Weak Resume Work Experiences Examples
Weak Resume Work Experience Examples for a Quality Technician
Quality Assurance Intern, ABC Manufacturing | Summer 2022
- Assisted permanent staff with routine inspections and documented findings.
- Observed production processes and noted any deviations without implementing corrective actions.
Quality Control Assistant, XYZ Electronics | January 2021 - June 2021
- Helped organize quality data and participated in team meetings.
- Conducted basic testing under supervision but rarely took the initiative to suggest improvements.
Warehouse Associate, DEF Logistics | January 2020 - December 2020
- Followed standard operating procedures to package and ship products.
- Ensured products were in compliance with shipping requirements but did not engage in quality assessments or process improvements.
Why These Work Experiences are Weak
Lack of Responsibility and Initiative: The examples showcase a pattern of limited responsibility, where the individual mainly assisted others or observed rather than actively managed quality processes. Quality technicians need to demonstrate hands-on experience and proactive problem-solving skills.
Limited Impact and Contributions: In these roles, there are no evidence or examples of the candidate contributing to significant projects or implementing changes that improved quality or efficiency. Quality technicians should highlight achievements that had a measurable impact on the quality systems and processes.
Minimaluse of Technical Skills: Strong quality technicians utilize various tools and techniques, such as statistical process control or root cause analysis. These examples show a lack of technical engagement, focusing instead on administrative tasks, which does not align with the core functions of a quality technician role.
Top Skills & Keywords for Quality Assurance Technician Resumes:
Crafting a standout quality technician resume involves showcasing essential skills and relevant keywords. Focus on technical abilities such as quality control, inspection techniques, and knowledge of ISO standards. Highlight analytical skills, problem-solving, and attention to detail. Include experience with tools like calipers, micrometers, and statistical process control (SPC). Keywords like "root cause analysis," "data analysis," "quality assurance," and "compliance" are crucial. Additionally, emphasize soft skills such as teamwork and communication. Certifications like Six Sigma or Lean Manufacturing can enhance your profile. Tailor your resume to specific job descriptions, integrating relevant keywords to improve visibility in applicant tracking systems (ATS).
Top Hard & Soft Skills for Quality Assurance Technician:
Hard Skills
Here's a table with 10 hard skills for a quality technician along with their descriptions:
Hard Skills | Description |
---|---|
Quality Control | The process of ensuring products meet specified standards through inspections and testing. |
Quality Assurance | A systematic approach to ensuring quality in production processes and services across various industries. |
Statistical Process Control | The use of statistical methods to monitor and control a process, ensuring it operates at its maximum potential. |
Failure Mode and Effect Analysis | A structured approach to identifying and addressing potential failures in a product or process before they occur. |
Root Cause Analysis | A method for identifying the underlying reasons for a problem and finding effective solutions to prevent recurrence. |
Six Sigma | A data-driven methodology aimed at reducing defects and improving quality in processes and products. |
Lean Manufacturing | A production practice that considers the expenditure of resources in any aspect other than the direct creation of value for the end customer to be wasteful and thus a target for elimination. |
Auditing | The process of reviewing and assessing quality systems for compliance with standards and procedures. |
Measurement Systems Analysis | A methodology to ensure that the measurement processes yield accurate and precise results. |
ISO Standards | International standards outlining quality management principles and guidelines for maintaining quality across various industries. |
Feel free to adjust or expand the descriptions as needed!
Soft Skills
Here’s a table of 10 soft skills for a quality technician along with their descriptions:
Soft Skills | Description |
---|---|
Communication | The ability to clearly convey information and ideas to others, ensuring understanding and effective collaboration. |
Attention to Detail | The skill to notice and assess small details that can significantly impact product quality and compliance. |
Problem Solving | The capacity to identify issues, analyze information, and implement effective solutions to prevent the recurrence of problems. |
Teamwork | The ability to work collaboratively with others to achieve common goals, contributing to a positive work environment. |
Adaptability | Being flexible and able to adjust to new conditions, challenges, or changes in processes and technology. |
Time Management | The ability to prioritize tasks and manage time effectively to meet deadlines and maintain efficiency. |
Critical Thinking | The skill to analyze facts and develop a reasoned judgment, enabling effective decision-making in quality assurance processes. |
Creativity | The ability to think outside the box and bring new ideas or approaches to improve quality processes and outcomes. |
Flexibility | The willingness to take on various roles and responsibilities or to change plans and approaches as needed. |
Leadership | The ability to guide and motivate team members, fostering a culture of quality and continuous improvement. |
Feel free to ask if you need additional information or modifications!
Elevate Your Application: Crafting an Exceptional Quality Assurance Technician Cover Letter
Quality Assurance Technician Cover Letter Example: Based on Resume
Dear [Company Name] Hiring Manager,
I am writing to express my enthusiasm for the Quality Technician position at [Company Name], as advertised. With a robust background in quality assurance and a passion for enhancing product integrity, I am excited about the opportunity to contribute to your team.
I have over five years of experience in quality control within the manufacturing sector, where I honed my technical skills and attention to detail. My previous role at [Previous Company Name] involved conducting rigorous inspections and testing procedures that ensured compliance with industry standards. I successfully identified areas for quality improvement, which led to a 15% reduction in defects and an increase in customer satisfaction ratings.
Proficient in industry-standard software, including Minitab and Quality Assurance Management Systems (QAMS), I have utilized data analysis to inform decision-making and drive process enhancements. My technical expertise combined with my problem-solving skills has empowered me to lead quality training sessions for new team members, fostering a culture of continuous improvement and collaboration.
I thrive in team environments where open communication and shared goals are paramount. At [Previous Company Name], I collaborated closely with cross-functional teams to streamline processes, resulting in a 20% increase in operational efficiency. My commitment to maintaining high-quality standards, along with my ability to mentor others, has been a core component of my professional journey.
I am eager to bring my expertise and collaborative work ethic to [Company Name] and contribute to your mission of delivering exceptional products. Thank you for considering my application. I look forward to the possibility of discussing how my skills and experiences align with your needs.
Best regards,
[Your Name]
Crafting a cover letter for a quality technician position requires a careful blend of professionalism, clarity, and relevance to the specific job you’re targeting. Here’s a detailed guide on what to include and how to structure your letter.
Key Components to Include:
Header: Start with your contact information, followed by the date and the employer's details. This sets a formal tone.
Salutation: Address the letter to a specific person if possible. If you cannot find a name, "Dear Hiring Manager" is acceptable.
Introduction: Begin with a strong opening statement. Mention the position you’re applying for and where you found the listing. This conveys enthusiasm and directs focus to your objective.
Relevant Experience: Highlight your professional experience related to quality assurance. Use specific examples that showcase your skills in inspections, testing, compliance with industry standards, or quality management systems (like ISO 9001). Tie your experiences back to the job description.
Technical Skills: Discuss essential skills such as proficiency in Quality Management software, data analysis, problem-solving, and knowledge of statistical process control (SPC). Your ability to perform audits or inspections is also pertinent.
Achievements: Quantify your accomplishments when possible. For instance, if you contributed to a project that reduced defect rates by a certain percentage, mention this to underline your effectiveness.
Soft Skills: Quality technicians require strong communication skills, attention to detail, and teamwork abilities. Illustrate these traits through relevant examples from previous employment.
Closing Paragraph: Reiterate your interest and express enthusiasm about the opportunity to contribute to the company's success. Mention your desire for an interview and how to best reach you.
Signature: End with a professional closing like "Sincerely," followed by your name.
Crafting Tips:
- Tailor Each Letter: Customize your letter for each application to reflect the specific requirements and culture of the company.
- Keep It Concise: Aim for a one-page format without compromising essential information.
- Proofread: Ensure there are no grammatical errors or typos, as these could undermine your professionalism.
By following this structured approach, you can effectively communicate your qualifications for the quality technician position.
Resume FAQs for Quality Assurance Technician:
How long should I make my Quality Assurance Technician resume?
When crafting a resume for a quality technician position, aim for one page, especially if you have less than 10 years of experience. Hiring managers generally prefer concise resumes that highlight relevant skills and experiences without overwhelming detail. A one-page format allows you to showcase your qualifications effectively while keeping the reader's attention.
If you have extensive experience or advanced qualifications, a two-page resume can be appropriate, but ensure that every detail adds value. Focus on relevant experience, certifications, and skills specifically related to quality control and assurance, such as knowledge of industry standards (like ISO, Six Sigma) and proficiency in quality management software.
Utilize bullet points for clarity and include key accomplishments that demonstrate your impact in previous roles. Tailor your resume for each application, emphasizing the skills and experiences that align with the specific job description. Additional sections such as professional development, certifications, or technical skills can enhance your profile, but maintain a clean layout with adequate white space for easy reading.
Ultimately, the goal is to present a compelling snapshot of your qualifications that encourages hiring managers to consider you for an interview while adhering to a clear and professional format.
What is the best way to format a Quality Assurance Technician resume?
Creating a strong resume for a quality technician position involves a clear, structured format that highlights your skills and experience effectively. Here’s a recommended format:
Header: Start with your name, contact information, and LinkedIn profile (if applicable) at the top.
Objective Statement: Write a brief, compelling summary that outlines your career goals and what you bring to the role. Tailor this to each job application.
Skills Section: List relevant technical skills such as knowledge of quality control processes, inspection methodologies, use of measuring tools, and familiarity with quality standards (ISO, Six Sigma).
Professional Experience: Detail your work history in reverse chronological order. For each position, include the job title, company name, location, and dates of employment. Use bullet points to describe your responsibilities and achievements, focusing on specific accomplishments and metrics.
Education: Include your highest degree first, along with any relevant certifications (e.g., Certified Quality Inspector).
Additional Sections: If relevant, add sections for additional certifications, professional affiliations, or training related to quality management.
Ensure the layout is clean, with consistent fonts and spacing, making it easy to read. Tailoring your resume for each application improves your chances of standing out to employers.
Which Quality Assurance Technician skills are most important to highlight in a resume?
When crafting a resume for a quality technician position, it’s crucial to highlight specific skills that demonstrate your expertise in quality assurance and control. First and foremost, attention to detail is paramount; showcasing your ability to meticulously evaluate products or processes ensures that you can maintain high standards.
Analytical skills are also essential, as quality technicians must interpret data and identify trends. Including experience with statistical process control (SPC) can set you apart. Proficiency in using quality management software and tools, such as Six Sigma, Lean methodologies, and Failure Mode and Effects Analysis (FMEA), is vital and should be featured prominently.
Moreover, problem-solving skills are important; providing examples of how you've successfully addressed quality issues will illustrate your practical experience. Excellent communication skills, both written and verbal, are crucial for documenting findings and collaborating with engineering and production teams.
Additionally, familiarity with industry-specific regulations and standards, such as ISO 9001 or FDA guidelines (for specific sectors), will demonstrate your capability to ensure compliance. Lastly, teamwork and collaboration abilities highlight your readiness to work within a cross-functional environment, making you a strong candidate for the role. Prioritizing these skills will strengthen your resume and attract potential employers.
How should you write a resume if you have no experience as a Quality Assurance Technician?
Writing a resume for a quality technician position without direct experience may seem challenging, but you can effectively highlight your skills and potential. Start with a strong objective statement that conveys your enthusiasm for the position and your willingness to learn.
Next, focus on transferable skills. Include relevant abilities such as attention to detail, problem-solving, and analytical thinking. If you've worked in related fields, emphasize any responsibilities or tasks that demonstrate quality control or assurance.
In the education section, list any relevant coursework or certifications, such as quality management, lean manufacturing, or Six Sigma principles. If you have completed any hands-on projects, internships, or volunteer work that put you in a quality-focused role, outline those experiences.
Consider adding a skills section where you can mention proficiency with tools and technologies pertinent to quality control, like statistical analysis software or inspection tools.
Lastly, personalize your resume for each job application by researching the company's values and emphasizing how your background aligns with their goals. Even without direct experience, your proactive approach and relevant skills can make a compelling case for your candidacy as a quality technician.
Professional Development Resources Tips for Quality Assurance Technician:
null
TOP 20 Quality Assurance Technician relevant keywords for ATS (Applicant Tracking System) systems:
Certainly! Below is a table listing 20 relevant words that you can use in your resume as a quality technician, along with their descriptions. These words will help you effectively pass through an Applicant Tracking System (ATS) used in recruitment.
Keyword | Description |
---|---|
Quality Assurance | Processes and activities that ensure the required quality of products or services. |
Quality Control | Procedures used to maintain the desired level of quality in a product/service by testing and inspection. |
Compliance | Adherence to industry standards, regulations, and company policies. |
Inspection | Examination of materials/products to ensure they meet specified criteria. |
Root Cause Analysis | A method of problem-solving that identifies the underlying causes of faults or problems. |
Continuous Improvement | Ongoing efforts to enhance products, services, or processes for increased efficiency and quality. |
Statistical Process Control | Methodology that uses statistical methods to monitor and control processes. |
Auditing | Systematic examination of records or activities to ensure compliance and effectiveness. |
Non-Conformance | Instances where products or processes do not meet specified standards. |
Corrective Action | Steps taken to eliminate the causes of detected non-conformities or other undesirable situations. |
Preventive Action | Steps taken to eliminate the causes of potential non-conformities. |
Documentation | Maintaining accurate records and reports related to quality assurance and testing procedures. |
Testing | Evaluation of products through various methods to verify their quality and performance. |
Calibration | Ensuring that measuring instruments and equipment are accurate and conform to standards. |
ISO Standards | International standards that ensure the quality, safety, and efficiency of products and services. |
Data Analysis | Reviewing and interpreting data to inform decision-making and improve processes. |
Training | Providing education and skills to team members on quality standards and procedures. |
Team Collaboration | Working effectively with colleagues across departments to achieve common quality goals. |
Problem-Solving | Ability to analyze issues and develop solutions to improve quality and efficiency. |
Lean Manufacturing | Systematic approach to identifying and eliminating waste to improve efficiency in manufacturing. |
Using these keywords appropriately in your resume can help you highlight your skills and experiences relevant to the quality technician role, maximizing your chances of passing the ATS filters.
Sample Interview Preparation Questions:
Can you describe your experience with quality assurance processes and how they relate to the role of a quality technician?
How do you prioritize tasks when faced with multiple quality control issues that need immediate attention?
What quality control tools and software are you familiar with, and how have you utilized them in your previous work?
Can you provide an example of a time when you identified a quality issue and the steps you took to resolve it?
How do you stay current with industry standards and regulations related to quality assurance and control?
Related Resumes for Quality Assurance Technician:
Generate Your NEXT Resume with AI
Accelerate your resume crafting with the AI Resume Builder. Create personalized resume summaries in seconds.