Six Sigma Resume Examples to Boost Your Job Search in 2024
---
**Sample Resume 1**
- **Position number:** 1
- **Person:** 1
- **Position title:** Six Sigma Black Belt
- **Position slug:** six-sigma-black-belt
- **Name:** John
- **Surname:** Smith
- **Birthdate:** February 15, 1985
- **List of 5 companies:** Boeing, General Electric, Honeywell, Ford, Motorola
- **Key competencies:** Process improvement, Lean methodologies, Project management, Statistical analysis, Team leadership
---
**Sample Resume 2**
- **Position number:** 2
- **Person:** 2
- **Position title:** Six Sigma Green Belt
- **Position slug:** six-sigma-green-belt
- **Name:** Maria
- **Surname:** Garcia
- **Birthdate:** April 22, 1990
- **List of 5 companies:** Amazon, 3M, Intel, IBM, Pfizer
- **Key competencies:** Quality control, Data-driven decision making, Problem-solving, Collaboration, Process mapping
---
**Sample Resume 3**
- **Position number:** 3
- **Person:** 3
- **Position title:** Six Sigma Analyst
- **Position slug:** six-sigma-analyst
- **Name:** Kevin
- **Surname:** Johnson
- **Birthdate:** August 10, 1987
- **List of 5 companies:** Nestle, PepsiCo, Toyota, Siemens, Deloitte
- **Key competencies:** Data analysis, KPI tracking, Statistical software (Minitab, R), Continuous improvement, Reporting
---
**Sample Resume 4**
- **Position number:** 4
- **Person:** 4
- **Position title:** Six Sigma Project Manager
- **Position slug:** six-sigma-project-manager
- **Name:** Lisa
- **Surname:** Brown
- **Birthdate:** November 5, 1982
- **List of 5 companies:** Coca-Cola, FedEx, Procter & Gamble, Johnson & Johnson, Lockheed Martin
- **Key competencies:** Project lifecycle management, Stakeholder engagement, Risk management, Resource allocation, Team building
---
**Sample Resume 5**
- **Position number:** 5
- **Person:** 5
- **Position title:** Six Sigma Quality Engineer
- **Position slug:** six-sigma-quality-engineer
- **Name:** David
- **Surname:** Wilson
- **Birthdate:** January 30, 1995
- **List of 5 companies:** Tesla, General Motors, Bosch, ABB, Raytheon
- **Key competencies:** Quality assurance processes, Root cause analysis, Process validation, Failure mode and effects analysis (FMEA), Vendor quality management
---
**Sample Resume 6**
- **Position number:** 6
- **Person:** 6
- **Position title:** Six Sigma Process Improvement Specialist
- **Position slug:** six-sigma-process-improvement-specialist
- **Name:** Sarah
- **Surname:** Miller
- **Birthdate:** June 12, 1989
- **List of 5 companies:** Microsoft, Facebook, HP, Unilever, Oracle
- **Key competencies:** Workflow optimization, Change management, Training and development, Cost reduction strategies, Benchmarking
---
Feel free to adjust any of the details as needed!
### Sample 1
- **Position number:** 1
- **Position title:** Six Sigma Analyst
- **Position slug:** six-sigma-analyst
- **Name:** Emily
- **Surname:** Turner
- **Birthdate:** 1988-07-15
- **List of 5 companies:**
1. Ford Motor Company
2. GE Appliances
3. Siemens
4. Honeywell
5. 3M
- **Key competencies:** Data analysis, Process improvement, Statistical tools, Lean methodologies, Project management
---
### Sample 2
- **Position number:** 2
- **Position title:** Six Sigma Black Belt
- **Position slug:** six-sigma-black-belt
- **Name:** Michael
- **Surname:** Johnson
- **Birthdate:** 1985-03-22
- **List of 5 companies:**
1. Motorola
2. Raytheon
3. Intel
4. Pfizer
5. Boeing
- **Key competencies:** Leadership, Advanced analytics, Root cause analysis, Cross-functional collaboration, Training & mentoring
---
### Sample 3
- **Position number:** 3
- **Position title:** Six Sigma Project Manager
- **Position slug:** six-sigma-project-manager
- **Name:** Sarah
- **Surname:** Thompson
- **Birthdate:** 1990-11-02
- **List of 5 companies:**
1. Accenture
2. Bank of America
3. IBM
4. Amazon
5. Procter & Gamble
- **Key competencies:** Project life cycle management, Budget management, Risk assessment, Team leadership, Stakeholder communication
---
### Sample 4
- **Position number:** 4
- **Position title:** Six Sigma Process Improvement Specialist
- **Position slug:** six-sigma-process-improvement-specialist
- **Name:** David
- **Surname:** Martinez
- **Birthdate:** 1984-05-30
- **List of 5 companies:**
1. Coca-Cola
2. Nestlé
3. Johnson & Johnson
4. FedEx
5. The Hershey Company
- **Key competencies:** Process mapping, Value stream analysis, Performance metrics, Change management, Quality control
---
### Sample 5
- **Position number:** 5
- **Position title:** Six Sigma Quality Engineer
- **Position slug:** six-sigma-quality-engineer
- **Name:** Jessica
- **Surname:** Lee
- **Birthdate:** 1992-09-14
- **List of 5 companies:**
1. Tesla
2. Phillips
3. DuPont
4. Boston Scientific
5. United Technologies
- **Key competencies:** Statistical process control, Quality assurance, Failure modes and effects analysis (FMEA), Root cause analysis, Calibration techniques
---
### Sample 6
- **Position number:** 6
- **Position title:** Six Sigma Consultant
- **Position slug:** six-sigma-consultant
- **Name:** Christopher
- **Surname:** White
- **Birthdate:** 1980-01-26
- **List of 5 companies:**
1. Deloitte
2. PwC
3. KPMG
4. EY
5. Capgemini
- **Key competencies:** Client management, Strategic planning, Problem-solving, Workshop facilitation, Change management
---
Feel free to modify any details to better suit your needs!
Six Sigma Resume Examples: Stand Out with These 6 Winning Templates
We are seeking a dynamic Six Sigma Leader with a proven track record of driving process improvements and delivering measurable results. The ideal candidate will possess exceptional technical expertise in Lean methodologies and statistical analysis, successfully leading cross-functional teams to reduce waste and enhance efficiency. With a history of overseeing impactful projects that yield cost savings and quality enhancements, this individual will also excel in conducting targeted training sessions to elevate team competencies. Through effective collaboration and communication, you will foster a culture of continuous improvement, ensuring sustained operational excellence across the organization.
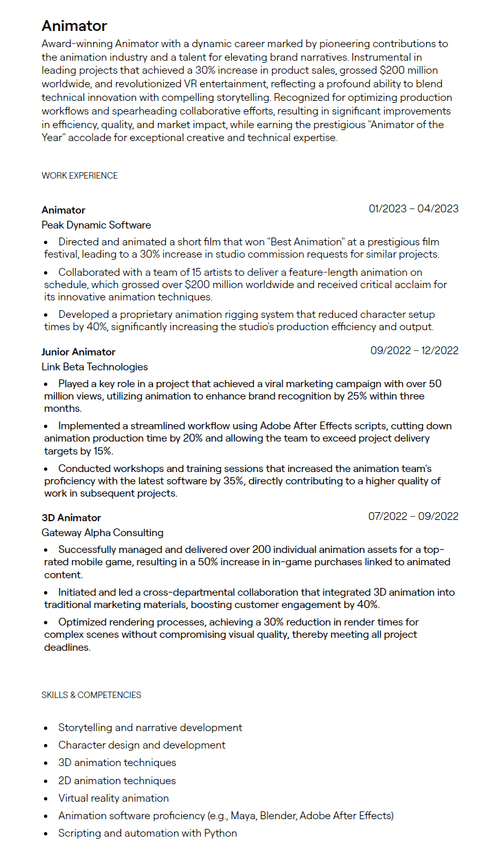
A Six Sigma professional plays a crucial role in optimizing processes, reducing defects, and enhancing quality in organizations. This role demands talents in analytical thinking, problem-solving, and data-driven decision-making, along with strong leadership and communication skills to effectively guide teams through improvement initiatives. To secure a job in this field, candidates should pursue Six Sigma certifications (such as Green Belt or Black Belt), gain practical experience through internships or project work, and develop proficiency in statistical analysis tools. Building a strong professional network and showcasing successful process improvement projects can further enhance job prospects in this competitive landscape.
Common Responsibilities Listed on Six Sigma Resumes:
Certainly! Here are 10 common responsibilities that are often listed on Six Sigma resumes:
Process Improvement: Identified and analyzed process inefficiencies to implement Six Sigma methodologies, resulting in significant performance enhancements.
Data Analysis: Utilized statistical tools and software (e.g., Minitab, Excel) to analyze data and measure process performance, ensuring data-driven decision-making.
Project Management: Led cross-functional teams in Six Sigma projects, effectively managing timelines, resources, and project milestones to achieve targeted outcomes.
Training and Mentorship: Developed and delivered training sessions on Six Sigma principles and tools to team members, fostering a culture of continuous improvement.
Root Cause Analysis: Conducted root cause analysis (RCA) using techniques such as Fishbone Diagrams and 5 Whys to identify the underlying issues in processes.
Control Plans: Created and implemented control plans to sustain improvements and ensure process stability post-project completion.
Stakeholder Engagement: Collaborated with stakeholders at various levels to gather requirements and ensure alignment with organizational goals and objectives.
Risk Management: Assessed potential risks in processes and projects, developing mitigation strategies to minimize negative impacts.
Documentation and Reporting: Maintained comprehensive documentation of project phases, findings, and outcomes, providing regular updates to senior management.
Continuous Improvement Initiatives: Participated in or led initiatives aimed at fostering a culture of continuous improvement and operational excellence within the organization.
These points highlight the core responsibilities associated with Six Sigma practices and demonstrate the value a candidate can bring to a potential employer.
When crafting a resume for a Six Sigma Analyst, it is crucial to highlight relevant experience in data analysis and process improvement. Emphasize proficiency with statistical tools and lean methodologies, as these are vital for success in the role. Include any experience with project management to demonstrate the ability to lead improvements effectively. Showcase contributions to process enhancements at notable companies within the industry, as this builds credibility. Lastly, consider highlighting any certifications, notable projects, or specific metrics achieved to further enhance the resume's appeal to potential employers.
[email protected] • +1-555-0123 • https://www.linkedin.com/in/emilyturner • https://twitter.com/emilyturner
Results-driven Six Sigma Analyst with over 5 years of experience in the automotive and manufacturing sectors, including tenures at Ford Motor Company and GE Appliances. Proficient in data analysis and process improvement, leveraging statistical tools and lean methodologies to drive operational efficiency. Adept in project management, demonstrating a consistent ability to deliver high-quality results on time and under budget. Recognized for exceptional analytical skills and a commitment to continuous improvement, Emily Turner is dedicated to enhancing organizational performance through data-driven insights and innovative solutions.
WORK EXPERIENCE
- Led a cross-functional team to reduce product defects by 25%, enhancing customer satisfaction and product reliability.
- Designed and implemented a new data analysis framework that improved reporting efficiency by 40%.
- Streamlined manufacturing processes using Lean methodologies, resulting in a savings of $500,000 annually.
- Facilitated workshops that educated over 100 employees in Six Sigma principles, boosting organizational capabilities.
- Collaborated with engineering teams to drive process improvements that increased production efficiency by 15%.
- Spearheaded a project that integrated data analysis tools, reducing project delivery time by 30%.
- Utilized advanced statistical tools to identify trends and implemented corrective actions, leading to a 20% reduction in operational costs.
- Developed key performance metrics to monitor process improvements, resulting in a 10% increase in productivity.
- Engaged with stakeholders to align Six Sigma initiatives with business goals, driving a more strategic approach to process improvements.
- Recognized with a company award for exemplary contributions to quality improvement in manufacturing processes.
- Improved quality control processes, reducing non-conformance incidents by 35%, significantly impacting product quality.
- Analyzed customer feedback data to identify root causes of issues and implemented solutions that improved customer retention by 15%.
- Conducted Six Sigma training sessions and coaching for 50+ employees, fostering a culture of continuous improvement.
- Collaborated with IT and operations teams to enhance data integrity and accessibility, improving decision-making capabilities.
- Participated in a cross-company initiative that identified cost-saving opportunities totaling $1 million.
- Driving cross-departmental projects to enhance supply chain efficiencies, resulting in a 20% reduction in lead times.
- Leveraging advanced analytics to support strategic decisions that increased market competitiveness and customer satisfaction.
- Facilitating Six Sigma events that led to process optimizations, directly impacting revenue growth by 15%.
- Implemented a new project management framework that increased accountability and transparency in reporting.
- Recognized for exceptional performance with a quarterly excellence award due to significant contributions to team success.
SKILLS & COMPETENCIES
Here are 10 skills for Emily Turner, the Six Sigma Analyst:
- Data analysis
- Process improvement
- Statistical tools
- Lean methodologies
- Project management
- Quality control techniques
- Data visualization
- Root cause analysis
- Process mapping
- Risk assessment
COURSES / CERTIFICATIONS
Here is a list of 5 certifications or completed courses for Emily Turner, the Six Sigma Analyst:
Certified Six Sigma Green Belt (CSSGB)
- Issuing Organization: American Society for Quality (ASQ)
- Date Completed: March 2019
Lean Six Sigma Yellow Belt Certification
- Issuing Organization: International Association for Six Sigma Certification (IASSC)
- Date Completed: July 2018
Data Analysis and Visualization with Excel
- Issuing Organization: Coursera
- Date Completed: November 2020
Introduction to Statistical Process Control
- Issuing Organization: Purdue University Online
- Date Completed: February 2021
Project Management Professional (PMP)
- Issuing Organization: Project Management Institute (PMI)
- Date Completed: August 2021
EDUCATION
- Bachelor of Science in Industrial Engineering, University of Michigan, 2006-2010
- Lean Six Sigma Green Belt Certification, ASQ (American Society for Quality), 2012
When crafting a resume for a Six Sigma Black Belt position, it's crucial to highlight leadership experience and advanced analytical skills. Emphasize expertise in root cause analysis and cross-functional collaboration, showcasing successful project outcomes. Include training and mentoring capabilities to demonstrate a commitment to developing others in Six Sigma methodologies. The resume should reflect specific accomplishments at notable companies, emphasizing measurable impacts on process improvement and efficiency. Tailor the language to align with industry standards, focusing on results-driven metrics and strategic initiatives that exemplify effective problem-solving and project management.
[email protected] • (555) 123-4567 • https://www.linkedin.com/in/michaeljohnson • https://twitter.com/michaeljohnson
Results-driven Six Sigma Black Belt professional with over 10 years of experience in implementing advanced analytics and process improvement strategies for leading organizations, including Motorola and Pfizer. Adept at root cause analysis, fostering cross-functional collaboration, and training teams to achieve operational excellence. Known for leveraging leadership capabilities to mentor junior staff and drive successful project outcomes. Proven track record in streamlining processes and enhancing quality, significantly contributing to organizational efficiency and effectiveness. Committed to continuous improvement and delivering measurable results in fast-paced environments.
WORK EXPERIENCE
- Led a cross-functional team to implement a Six Sigma project that reduced product defect rates by 30%, resulting in a $2 million annual cost saving.
- Developed and facilitated training programs for over 100 employees on Six Sigma methodologies, enhancing team capability and project delivery.
- Conducted root cause analysis and process mapping sessions that identified bottlenecks in the production line, leading to a 25% improvement in operational efficiency.
- Collaborated with marketing teams to align product enhancements with customer feedback, significantly increasing customer satisfaction ratings.
- Recognized with the 'Excellence in Leadership' award for outstanding contributions to process improvements and team development.
- Spearheaded a project that optimized supply chain processes, reducing lead times by 20% and increasing overall efficiency.
- Utilized advanced analytics to design and implement key performance indicators (KPIs) for several departments, fostering a data-driven culture.
- Facilitated workshops with executive leadership to strategize and solve complex business challenges, improving decision-making processes.
- Mentored junior Black Belt candidates through their certification journeys, enhancing the overall Six Sigma competency within the organization.
- Achieved recognition as 'Employee of the Year' for delivering exceptional project results and demonstrating innovative thinking.
- Oversee a portfolio of Six Sigma projects with a focus on strategic execution, cross-functional collaboration, and stakeholder management.
- Establish a continuous improvement framework across multiple business units that resulted in a 15% reduction in operational costs.
- Drive initiatives that leverage Lean methodologies to streamline processes, resulting in enhanced productivity and quicker turnaround times.
- Engage with clients to identify improvement areas and tailor solutions that align with their organizational goals, ensuring sustainable growth.
- Implemented an internal recognition program that celebrates Six Sigma project milestones, cultivating a culture of excellence.
SKILLS & COMPETENCIES
Skills for Michael Johnson (Six Sigma Black Belt)
- Leadership and team management
- Advanced data analytics
- Root cause analysis techniques
- Effective cross-functional collaboration
- Training and mentoring of team members
- Strategic problem-solving
- Process optimization methodologies
- Change management strategies
- Risk assessment and mitigation
- Continuous improvement initiatives
COURSES / CERTIFICATIONS
Here is a list of 5 certifications or complete courses for Michael Johnson, the Six Sigma Black Belt:
Six Sigma Black Belt Certification
Institution: American Society for Quality (ASQ)
Date Completed: March 2020Lean Six Sigma Green Belt Certification
Institution: International Association for Six Sigma Certification (IASSC)
Date Completed: July 2018Data Analytics for Business: An Introduction to Data Analysis
Institution: Coursera (offered by University of Pennsylvania)
Date Completed: January 2021Project Management Professional (PMP)
Institution: Project Management Institute (PMI)
Date Completed: November 2019Root Cause Analysis and Problem Solving
Institution: Udemy
Date Completed: February 2022
EDUCATION
Education for Michael Johnson (Six Sigma Black Belt)
Master of Science in Engineering Management
Institution: Northwestern University
Graduation Date: June 2010Bachelor of Science in Industrial Engineering
Institution: Michigan State University
Graduation Date: May 2007
When crafting a resume for a Six Sigma Project Manager, it's crucial to highlight expertise in project life cycle management and budget management, underscoring proficiency in leading teams effectively. Emphasize experience in stakeholder communication and risk assessment, showcasing the ability to navigate complex project dynamics. Include examples of past projects to quantify successes and improvements achieved through Six Sigma methodologies. Additionally, highlight cross-functional teamwork and any certifications in Six Sigma to demonstrate credibility and commitment to continuous improvement, thereby appealing to potential employers looking for a results-oriented professional.
[email protected] • (555) 123-4567 • https://www.linkedin.com/in/sarahthompson • https://twitter.com/sarahthompson
Dynamic Six Sigma Project Manager with extensive experience in leading cross-functional teams to drive process improvements across various industries, including finance and technology. Proven expertise in managing project life cycles, overseeing budget allocations, and performing comprehensive risk assessments to ensure project success. Skilled in stakeholder communication and fostering collaboration among team members, delivering impactful solutions that enhance operational efficiency. With a solid foundation in Six Sigma methodologies and a passion for continuous improvement, I am committed to achieving high-performance results and exceeding organizational goals.
WORK EXPERIENCE
- Led a cross-functional team to implement process improvements that increased product sales by 30% within one year.
- Managed a budget of $1M for a critical project that successfully launched a new product line, resulting in a 25% increase in global revenue.
- Developed and maintained stakeholder communication plans that enhanced project visibility and engagement, leading to a 10% increase in project success rates.
- Utilized Lean methodologies to streamline operations, reducing lead time by 15% and improving overall efficiency.
- Mentored and trained junior team members in Six Sigma best practices, fostering a culture of continuous improvement.
- Coordinated the deployment of Six Sigma initiatives across multiple departments, driving consistency and quality improvements.
- Analyzed performance metrics to identify areas for improvement, which resulted in a 20% decrease in operational costs.
- Facilitated workshops and training sessions to enhance team understanding of Six Sigma principles, improving team competency by 40%.
- Collaborated with senior management to develop strategic improvement plans, leading to a 15% boost in customer satisfaction ratings.
- Created comprehensive documentation of project methodologies and results, recognized by leadership as best practices.
- Conducted data analysis for process improvement projects, identifying root causes of inefficiency and recommending sustainable solutions.
- Supported the project management team in the execution of Six Sigma projects, contributing to a 10% increase in project throughput.
- Participated in value stream mapping activities, collaborating with teams to streamline processes and eliminate waste.
- Assisted in the development of training materials on Six Sigma tools and methodologies, fostering a culture of quality.
- Instrumental in achieving ISO 9001 certification for the organization by ensuring compliance with quality standards.
- Assisted project teams in the deployment of Six Sigma methodologies, providing analytical support and reports.
- Supported the documentation of project processes and results, contributing to knowledge sharing within the organization.
- Collaborated with team members to monitor project progress and implement corrective actions as necessary.
- Participated in client meetings to gather requirements and provide updates on project status.
- Developed strong relationships with stakeholders, enhancing team collaboration and project support.
SKILLS & COMPETENCIES
Here are 10 skills for Sarah Thompson, the Six Sigma Project Manager:
- Project life cycle management
- Budget management
- Risk assessment
- Team leadership
- Stakeholder communication
- Process mapping
- Change management
- Performance measurement and analysis
- Conflict resolution
- Agile project management
COURSES / CERTIFICATIONS
Here are 5 certifications and completed courses for Sarah Thompson, the Six Sigma Project Manager:
Six Sigma Green Belt Certification
Issued by: American Society for Quality (ASQ)
Date: April 2021Project Management Professional (PMP)
Issued by: Project Management Institute (PMI)
Date: September 2020Lean Six Sigma Project Management Course
Provider: Coursera (offered by University of Georgia)
Date: January 2022Agile Project Management Certification
Issued by: Scrum Alliance
Date: June 2019Risk Management Professional (PMI-RMP)
Issued by: Project Management Institute (PMI)
Date: March 2020
EDUCATION
Education for Sarah Thompson (Six Sigma Project Manager)
Master of Business Administration (MBA), Project Management
University of Michigan, Ann Arbor
Graduated: May 2015Bachelor of Science in Industrial Engineering
Georgia Institute of Technology
Graduated: May 2012
When crafting a resume for a Six Sigma Process Improvement Specialist, it's crucial to highlight expertise in process mapping and value stream analysis, showcasing an ability to identify inefficiencies and recommend enhancements. Emphasizing experience with performance metrics will demonstrate a strong analytical skill set. Additionally, detailing familiarity with change management and quality control practices can illustrate capability in implementing new processes effectively. Listing notable companies worked with adds credibility, while showcasing collaborative and leadership skills is essential to convey the ability to work cross-functionally and drive team initiatives in a results-oriented environment.
[email protected] • +1-555-0123 • https://www.linkedin.com/in/davidmartinez • https://twitter.com/davidmartinez
David Martinez is a dedicated Six Sigma Process Improvement Specialist with extensive experience in enhancing operational efficiency across diverse industries. With a robust background at leading companies like Coca-Cola and Johnson & Johnson, he excels in process mapping, value stream analysis, and performance metrics. David’s expertise in change management and quality control empowers teams to drive continuous improvement initiatives effectively. His analytical mindset, combined with strong communication skills, allows him to collaborate seamlessly with stakeholders, ensuring successful project outcomes and fostering a culture of quality excellence within organizations.
WORK EXPERIENCE
- Led process mapping initiatives that streamlined operations, reducing turnaround times by 30%.
- Implemented value stream analysis resulting in a 25% increase in efficiency across multiple departments.
- Developed and executed performance metrics to benchmark process outcomes, enhancing quality control measures.
- Facilitated change management programs that improved employee engagement and adoption of new technologies.
- Recognized for outstanding contributions with the 'Excellence in Process Improvement' award.
- Spearheaded cross-functional teams in conducting root cause analysis to identify inefficiencies, resulting in a 20% reduction in waste.
- Designed and implemented quality control protocols leading to a 15% decrease in product defects.
- Cultivated strong relationships with stakeholders to foster collaboration on process improvement initiatives.
- Produced comprehensive reports detailing process performance enhancements, facilitating informed executive decision-making.
- Facilitated workshops that equipped staff with Lean Six Sigma principles, enhancing overall operational knowledge.
- Drove quality assurance initiatives that elevated product satisfaction ratings by over 40%.
- Collaborated with IT to implement data analytics tools for real-time performance monitoring.
- Championed a culture of continuous improvement, mentoring junior staff on Lean methodologies and project management.
- Successfully led a project that reduced processing costs by 18% while maintaining product integrity.
- Received recognition for valuable contributions to global strategy through process improvements and innovation.
- Conducted assessments of existing manufacturing processes and proposed optimization strategies.
- Participated in a team tasked with enhancing customer feedback loops, leading to improved service response times.
- Implemented preventative measures based on previous failure analysis, resulting in minimal downtime.
- Provided training sessions for employees on Six Sigma practices, strengthening team competencies.
- Contributed to cross-departmental projects focusing on quality assurance and enhanced operational effectiveness.
- Executed process improvement projects that delivered high-impact results in production efficiency.
- Utilized statistical analysis tools to identify trends and forecast areas for improvement.
- Collaborated with quality assurance teams to integrate Lean strategies into daily operations.
- Facilitated brainstorming sessions that yielded innovative solutions to complex process-related challenges.
- Prepared and presented findings and recommendations to executive teams, influencing strategic direction.
SKILLS & COMPETENCIES
Here’s a list of 10 skills for David Martinez, the Six Sigma Process Improvement Specialist:
- Process mapping
- Value stream analysis
- Performance metrics development
- Change management
- Quality control techniques
- Root cause analysis
- Continuous improvement strategies
- Lean methodologies
- Data analysis
- Team collaboration and communication
COURSES / CERTIFICATIONS
Here’s a list of 5 certifications or completed courses for David Martinez, the Six Sigma Process Improvement Specialist:
Certified Six Sigma Green Belt (CSSGB)
- Institution: ASQ (American Society for Quality)
- Date Completed: June 2020
Lean Six Sigma Black Belt Certification
- Institution: IASSC (International Association for Six Sigma Certification)
- Date Completed: March 2021
Process Improvement Certification
- Institution: Purdue University
- Date Completed: September 2019
Change Management Certification
- Institution: Prosci
- Date Completed: February 2022
Enterprise Process Management Certification
- Institution: Georgetown University
- Date Completed: November 2023
Feel free to adjust any of the details as necessary!
EDUCATION
Education of David Martinez (Sample 4)
Master of Science in Industrial Engineering
University of Michigan
September 2006 - May 2008Bachelor of Science in Mechanical Engineering
University of California, Berkeley
September 2000 - May 2004
When crafting a resume for a Six Sigma Quality Engineer, it is crucial to emphasize technical expertise in statistical process control and quality assurance methodologies. Highlight experience with failure modes and effects analysis (FMEA), showcasing the ability to identify and mitigate risks. Include proficiency in calibration techniques, ensuring compliance with industry standards. Additionally, underscore problem-solving skills and a successful track record in implementing quality improvement projects within reputable organizations. It's important to detail collaborative work in cross-functional teams, demonstrating effective communication skills that enhance project outcomes and foster a culture of continuous improvement.
[email protected] • (555) 123-4567 • https://www.linkedin.com/in/jessicaleeco • https://twitter.com/jessicaleetech
Jessica Lee is a dedicated Six Sigma Quality Engineer with extensive experience in the industry, having worked with prestigious companies such as Tesla and DuPont. Born on September 14, 1992, Jessica excels in statistical process control, quality assurance, and root cause analysis, utilizing her expertise in failure modes and effects analysis (FMEA) and calibration techniques to enhance product quality and efficiency. With a strong focus on continuous improvement, she effectively collaborates with cross-functional teams to drive initiatives that significantly reduce defects and optimize processes, making her a valuable asset in any organization striving for excellence.
WORK EXPERIENCE
- Led an initiative that improved product quality by 30% through the implementation of Statistical Process Control (SPC) techniques.
- Collaborated cross-functionally to develop and enforce quality assurance protocols, resulting in a 25% reduction in product defects.
- Conducted Failure Modes and Effects Analysis (FMEA) to anticipate potential failures, achieving an overall risk reduction of 40% in production processes.
- Spearheaded a calibration technique optimization project that reduced equipment downtime by 20%.
- Trained and mentored junior engineers in quality assurance practices and Lean Six Sigma methodologies.
- Implemented quality improvements using Lean methodologies, resulting in a 15% increase in operational efficiency.
- Developed and executed quality plans for new products, leading to a successful launch with zero post-release defects.
- Utilized Root Cause Analysis (RCA) to investigate and resolve customer complaints, enhancing customer satisfaction ratings by 20%.
- Participated in cross-departmental teams to enhance supply chain processes, resulting in a 10% decrease in costs.
- Facilitated quality workshops that promoted best practices across teams, contributing to a culture of continuous improvement.
- Executed process improvements that led to a cost savings of $250,000 in manufacturing through the use of FMEA and root cause analysis.
- Developed comprehensive documentation for quality standards, enhancing compliance rates by 30%.
- Participated in cross-functional audits and assessments, achieving a 95% success rate in compliance reviews.
- Utilized statistical data analysis to identify and mitigate production risk areas, contributing to an increase in production yield by 12%.
- Coordinated training sessions on quality tools and methodologies for staff, bolstering team’s engagement and performance.
- Developed and implemented a rigorous quality reporting system that led to improved transparency in product performance metrics.
- Led a project team in reducing cycle times by 20% through Lean Six Sigma principles, positively affecting product delivery timelines.
- Facilitated continuous improvement projects that enhanced product consistency and quality across the board.
- Merged quality metrics with business performance indicators to create actionable insights for senior management.
- Received team recognition awards for outstanding contributions to process improvement initiatives.
SKILLS & COMPETENCIES
Sure! Here’s a list of 10 skills for Jessica Lee, the Six Sigma Quality Engineer:
- Statistical process control
- Quality assurance techniques
- Failure modes and effects analysis (FMEA)
- Root cause analysis
- Calibration techniques
- Process improvement methodologies
- Data interpretation and analysis
- Risk management practices
- Lean manufacturing principles
- Documentation and reporting skills
COURSES / CERTIFICATIONS
Sure! Here’s a list of 5 certifications or courses for Jessica Lee, the Six Sigma Quality Engineer:
Certified Six Sigma Green Belt (CSSGB)
- Date: March 2020
Certified Quality Engineer (CQE)
- Date: July 2021
Lean Six Sigma Black Belt Training
- Date: January 2022
Statistical Process Control (SPC) Essentials
- Date: September 2021
Failure Modes and Effects Analysis (FMEA) Workshop
- Date: June 2022
Feel free to modify any of the details as needed!
EDUCATION
Education for Jessica Lee (Six Sigma Quality Engineer)
Bachelor of Science in Industrial Engineering
University of Michigan, Ann Arbor
Graduated: May 2014Master of Science in Quality Assurance
Purdue University
Graduated: May 2016
When crafting a resume for a Six Sigma Consultant, it's crucial to emphasize strong client management skills, showcasing the ability to build and maintain relationships with clients effectively. Highlight strategic planning capabilities, demonstrating expertise in developing and implementing improvement plans. Problem-solving skills should be underscored through examples of successfully addressing complex issues. Additionally, include experience in workshop facilitation to illustrate collaborative skills and the ability to engage teams. Lastly, showcase change management proficiency, reflecting a solid understanding of guiding organizations through transitions while ensuring continuous improvement practices are integrated seamlessly into existing systems.
[email protected] • +1-555-123-4567 • https://www.linkedin.com/in/christopherwhite • https://twitter.com/chriswhite
Dedicated Six Sigma Consultant with over a decade of experience in driving process improvements and operational excellence across diverse industries. Proven expertise in client management, strategic planning, and problem-solving, enhancing organizational efficiencies and effectiveness. Highly skilled in workshop facilitation and change management, enabling teams to adapt and thrive in dynamic environments. Adept at delivering insights and recommendations that align with client goals, fostering long-term relationships with top firms such as Deloitte, PwC, and KPMG. Committed to empowering organizations with innovative solutions that yield measurable results and sustainable growth.
WORK EXPERIENCE
- Led a cross-functional team to implement Six Sigma methodologies that improved production efficiency by 30%, resulting in a $1.5M increase in annual revenue.
- Facilitated workshops to enhance problem-solving skills among client teams, resulting in a 25% reduction in project timelines.
- Developed and executed a strategic improvement plan that addressed client-specific challenges, leading to a 20% increase in customer satisfaction ratings.
- Implemented performance metrics that tracked key processes, allowing clients to make data-driven decisions that improved operational efficiency.
- Recognized as the 'Innovator of the Year' for developing a new approach to project management that integrated Agile and Six Sigma principles.
- Consulted on Six Sigma projects for Fortune 500 companies, facilitating continuous improvement initiatives that saved clients over $3M annually.
- Partnered with client leadership teams to design training programs that upskilled over 300 employees in Lean and Six Sigma techniques.
- Managed a portfolio of projects that streamlined operations in manufacturing and healthcare sectors, resulting in improved quality and reduced waste.
- Conducted in-depth data analysis to identify root causes of quality issues, implementing corrective actions that decreased defect rates by 40%.
- Served as a mentor to junior consultants, fostering a culture of excellence and continuous learning within the firm.
- Directed a Six Sigma initiative that improved supply chain efficiency, which led to a 15% reduction in operational costs for a large retail client.
- Collaborated with cross-functional teams to develop and deploy a comprehensive quality management system, enhancing compliance with international standards.
- Implemented root cause analysis and corrective action processes that resolved quality issues and improved product reliability by 35%.
- Led performance reviews and gap analysis for ongoing projects, establishing best practices that were adopted company-wide.
- Achieved certification as a Six Sigma Black Belt, further honing advanced analytical and leadership capabilities.
- Worked with a team to analyze processes in the healthcare sector, resulting in a 20% improvement in patient turnaround times.
- Designed and conducted training sessions focused on Lean methodologies for over 200 healthcare professionals across multiple facilities.
- Evaluated process workflows, identifying bottlenecks and recommending innovative solutions that improved patient care quality.
- Developed and presented KPIs to senior management, demonstrating the impact of Six Sigma projects on operational performance.
- Awarded the 'Excellence in Consulting' award for outstanding performance and significant contributions to client project success.
SKILLS & COMPETENCIES
Here are 10 skills for Christopher White, the Six Sigma Consultant:
- Client relationship management
- Strategic planning and execution
- Advanced problem-solving techniques
- Workshop and training facilitation
- Data-driven decision making
- Change management strategies
- Process optimization methodologies
- Quality improvement initiatives
- Risk assessment and mitigation
- Effective communication and presentation skills
COURSES / CERTIFICATIONS
Here is a list of 5 certifications or completed courses for Christopher White, the Six Sigma Consultant:
Certified Six Sigma Black Belt (CSSBB)
- Institution: ASQ (American Society for Quality)
- Completion Date: June 2019
Lean Six Sigma Green Belt Certification
- Institution: International Association for Six Sigma Certification (IASSC)
- Completion Date: September 2018
Project Management Professional (PMP)
- Institution: Project Management Institute (PMI)
- Completion Date: March 2020
Change Management Certification
- Institution: Prosci
- Completion Date: January 2021
Data-Driven Decision Making Course
- Institution: Coursera (offered by the University of Illinois)
- Completion Date: April 2022
Feel free to modify or adjust any entries to better fit your needs!
EDUCATION
Education for Christopher White (Sample 6)
Master of Business Administration (MBA)
University of Chicago, Booth School of Business
Graduation Date: June 2005Bachelor of Science in Industrial Engineering
Pennsylvania State University
Graduation Date: May 2002
Crafting a compelling resume for a Six Sigma role requires a strategic approach that highlights not only technical proficiency but also essential soft skills. Six Sigma methodologies, such as DMAIC (Define, Measure, Analyze, Improve, Control), necessitate a solid understanding of industry-standard tools, like Minitab, SigmaXL, and R, which should be prominently featured on your resume. Employers are keen on candidates who can effectively analyze data, manage projects, and drive process improvements. Being explicit about your proficiency with these tools, and providing examples of how you have successfully applied them in previous roles, can set you apart. Moreover, emphasize your achievements by quantifying results—mention specific percentages of cost savings, reductions in process cycle time, or improvements in customer satisfaction that you have driven.
While technical skills are critical, soft skills are equally vital in a Six Sigma context where team collaboration and communication play significant roles in project success. Include skills such as leadership, problem-solving, and change management, showcasing instances where you effectively led teams or facilitated cross-departmental cooperation. Tailoring your resume to the job role is paramount; carefully read job descriptions and incorporate relevant keywords and phrases to demonstrate alignment with what top companies seek. This approach not only ensures that your resume passes through Applicant Tracking Systems (ATS) but also resonates with hiring managers. Ultimately, a standout resume reflects a well-rounded professional capable of driving process excellence. By strategically showcasing both technical and soft skills, you position yourself as an attractive candidate in the competitive landscape of Six Sigma roles.
Essential Sections for a Six Sigma Resume
Contact Information
- Full name
- Phone number
- Email address
- LinkedIn profile or personal website (if applicable)
Professional Summary
- A brief overview of your experience and skills in Six Sigma and continuous improvement.
Certifications
- Six Sigma certification level (e.g., Green Belt, Black Belt, Master Black Belt)
- Any other relevant certifications (e.g., Lean, Project Management Professional)
Work Experience
- Job titles and responsibilities related to Six Sigma and process improvement.
- Specific achievements and results related to Six Sigma initiatives.
Education
- Degrees obtained and relevant coursework related to Six Sigma and operational excellence.
Skills
- Key competencies in Six Sigma tools and methodologies (e.g., DMAIC, root cause analysis, statistical analysis)
- Technical skills (e.g., software proficiency in Minitab, Excel, etc.)
Additional Sections to Stand Out
Projects
- Highlight key Six Sigma projects you led or contributed to, including objectives, methods, and outcomes.
Technical Proficiencies
- List software and tools you are proficient with that are relevant to Six Sigma (e.g., statistical analysis software, process mapping tools).
Awards and Recognition
- Any awards or formal recognition you received for Six Sigma projects or contributions to process improvements.
Professional Affiliations
- Membership in professional organizations related to quality and process improvement (e.g., ASQ, ISQ).
Volunteer Experience
- Any volunteer roles that demonstrate leadership, teamwork, or Six Sigma application.
Publications or Presentations
- Articles, papers, or presentations you've authored or contributed to related to Six Sigma or quality improvement.
Generate Your Resume Summary with AI
Accelerate your resume crafting with the AI Resume Builder. Create personalized resume summaries in seconds.
Crafting an impactful resume headline is crucial for professionals in the Six Sigma domain, as it serves as a snapshot of your skills and sets the tone for your application. A well-formulated headline can pique the interest of hiring managers, compelling them to delve deeper into your resume.
When creating your headline, begin by summarizing your specialization. Use precise, powerful language to encapsulate your expertise—consider terms like “Certified Six Sigma Black Belt” or “Lean Six Sigma Expert.” Highlighting specific certifications or methodologies demonstrates your qualifications at a glance and shows relevance to the position you’re targeting.
Next, reflect on your distinctive qualities, skills, and career achievements. Identify what makes you stand out—perhaps it’s your track record in process improvement, your ability to lead cross-functional teams, or your expertise in utilizing data analytics for problem-solving. For instance, a compelling headline could be: “Results-Driven Six Sigma Black Belt with Proven Success in Reducing Operational Costs by 30%.” This not only conveys your Six Sigma credentials but also offers a glimpse into your impact on previous employers.
Your headline should also be tailored to resonate with hiring managers by incorporating keywords from the job description. This strategy enhances your visibility and relevance in applicant tracking systems (ATS) often used in the hiring process.
Remember, your resume headline is your first impression; make it count. A clear, concise, and targeted headline will not only capture attention but also entice hiring managers to explore your qualifications further. In a competitive field, an impactful resume headline can be the difference between landing an interview and getting overlooked.
Six Sigma Quality Manager Resume Headline Examples:
Strong Resume Headline Examples
Strong Resume Headline Examples for Six Sigma
- Certified Six Sigma Black Belt with 8+ Years of Experience in Process Improvement
- Results-Driven Six Sigma Specialist Focused on Reducing Waste and Enhancing Efficiency
- Six Sigma Expert with Proven Track Record in Leading Cross-Functional Teams to Achieve Operational Excellence
Why These are Strong Headlines
Clarity and Specificity: Each headline clearly indicates the candidate's level of Six Sigma certification (e.g., Black Belt) and their years of experience. This specificity helps recruiters quickly understand the candidate's qualifications.
Focus on Results: Phrases like "Results-Driven" and "Proven Track Record" suggest a results-oriented mindset, which is critical in Six Sigma roles. This emphasis on outcomes resonates well with employers looking for candidates who can demonstrate tangible improvements.
Relevance to Role: By including keywords such as "Process Improvement," "Waste Reduction," and "Operational Excellence," these headlines align closely with the core competencies and goals of Six Sigma initiatives, making them relevant for positions in quality management and operational roles.
Weak Resume Headline Examples
Weak Resume Headline Examples for Six Sigma
- "Experienced with Quality Control"
- "Seeking Opportunities in Process Improvement"
- "Knowledgeable About Six Sigma Concepts"
Why These Are Weak Headlines
Lack of Specificity: The phrase "Experienced with Quality Control" fails to specify what level of experience the candidate possesses or the context in which this experience was gained. This generic statement does not highlight any particular achievements or skills that could differentiate the candidate from others in the field.
Uncertainty in Intent: "Seeking Opportunities in Process Improvement" is vague and implies that the candidate is still exploring their options. It does not convey a sense of confidence or readiness for the role. Effective headlines should assert the candidate's qualifications rather than simply express a desire for a position.
Minimal Value Proposition: "Knowledgeable About Six Sigma Concepts" merely states familiarity with the subject without demonstrating application. It lacks any mention of skills, certifications, or successful project outcomes, which would help to establish proof of expertise and show potential employers how the candidate can add value to their organization.
An exceptional resume summary is crucial for any professional, especially in Six Sigma, as it succinctly highlights your qualifications and experiences. This snapshot serves as an effective introduction, capturing the attention of hiring managers and setting the tone for the rest of the resume. A well-crafted summary not only outlines your professional background and technical skills but also reflects your ability to collaborate, lead, and pay meticulous attention to detail—qualities that are vital in Six Sigma roles. Customizing your summary to align with the specific job you’re targeting is essential, as it ensures that your expertise and value are immediately evident.
Here are key points to include in your Six Sigma resume summary:
Years of Experience: Specify your years of experience in Six Sigma methodologies, including your certifications (e.g., Green Belt, Black Belt), to establish your credibility.
Specialized Styles or Industries: Highlight any particular industries you've worked in, such as manufacturing, healthcare, or finance, showcasing your relevant expertise in those sectors.
Expertise with Software: Mention any Six Sigma-related software or tools you’re proficient in, such as Minitab or JMP, to demonstrate your technical proficiency.
Collaboration and Communication Abilities: Emphasize your ability to work collaboratively with cross-functional teams, and mention any experience in leading team initiatives or training sessions.
Attention to Detail: Illustrate your meticulous approach to problem-solving and quality improvement, showcasing examples of how your attention to detail has contributed to successful projects or process enhancements.
Crafting a thoughtful summary by integrating these elements will help position you as a top candidate in the competitive field of Six Sigma.
Six Sigma Quality Manager Resume Summary Examples:
Strong Resume Summary Examples
Resume Summary Examples for Six Sigma Professionals:
Example 1:
Results-driven Six Sigma Black Belt with over 8 years of experience leading process improvement initiatives across manufacturing and service sectors. Proven track record of reducing operational costs by up to 30% while enhancing product quality and customer satisfaction through the application of Lean methodologies.Example 2:
Accomplished Quality Assurance Specialist with a Six Sigma Green Belt certification and extensive experience in data analysis and process optimization. Adept at identifying inefficiencies and implementing sustainable solutions that drive business excellence, resulting in a 25% reduction in defect rates within a year.Example 3:
Innovative Six Sigma Master Black Belt with a strong background in project management and team leadership. Skilled at fostering a culture of continuous improvement, leading cross-functional teams to deliver process enhancements that boost efficiency by over 40% and drive revenue growth.
Why These Summaries Are Strong:
Clear Credentials: Each summary begins by identifying the individual's Six Sigma certification level (Black Belt, Green Belt, Master Black Belt), establishing authority and expertise in the field right from the start.
Quantifiable Achievements: These summaries include specific metrics that reflect the candidate's impact on previous organizations, such as percentages in cost reduction or defect rate improvement. These quantifications provide concrete evidence of their capabilities and contribute to a compelling narrative of success.
Focused Skills and Outcomes: The summaries succinctly highlight relevant skills (e.g., data analysis, project management, Lean methodologies) while linking them directly to positive business outcomes. This clarity not only showcases the candidate’s abilities but also aligns their experience with the needs and goals of potential employers.
Lead/Super Experienced level
Here are five bullet points for a strong resume summary for a Lead or Super Experienced level professional with Six Sigma expertise:
Results-Driven Leader: Accomplished Lead Six Sigma Black Belt with over 10 years of experience in driving process improvements and optimizing operational efficiency in high-pressure environments, achieving a measurable reduction in operational costs by up to 30%.
Cross-Functional Collaboration: Expert in leading cross-functional teams to implement Six Sigma methodologies, facilitating training sessions, and fostering a culture of continuous improvement, resulting in enhanced team performance and project delivery timelines.
Data-Driven Decision Maker: Proficient in utilizing advanced statistical analysis and Six Sigma tools to identify process bottlenecks and develop strategic solutions, leading to a 25% improvement in cycle time and increased customer satisfaction ratings.
Strategic Visionary: Proven track record of aligning Six Sigma initiatives with organizational goals, driving transformational change across multiple departments, and delivering significant ROI through targeted project execution and stakeholder engagement.
Mentorship and Development: Passionate about mentoring junior professionals in Six Sigma principles, successfully developing high-performance teams and cultivating a new generation of Lean Six Sigma practitioners who contribute to sustained organizational success.
Senior level
Sure! Here are five bullet points for a strong resume summary tailored for a Senior-level Six Sigma professional:
Proven Leader in Process Improvement: Senior Six Sigma Black Belt with over 10 years of experience driving process excellence through methodical data analysis and strategic implementation of Lean Six Sigma methodologies across diverse industries.
Expert in Change Management: Demonstrated ability to lead cross-functional teams in high-pressure environments, successfully reducing operational costs by 20% while enhancing productivity and customer satisfaction through innovative problem-solving techniques.
Data-Driven Decision Maker: Proficient in utilizing statistical tools and software (e.g., Minitab, JMP) to identify inefficiencies and develop actionable recommendations, leading to significant improvements in quality control and performance metrics.
Mentorship and Training: Committed to fostering a culture of continuous improvement by mentoring junior team members and leading training initiatives, resulting in a 30% increase in Six Sigma project completions within the organization.
Strategic Visionary: Adept at aligning Six Sigma projects with organizational goals, utilizing strategic thinking to ensure successful project management from conception to execution, ultimately driving long-term business growth and sustainability.
Mid-Level level
Certainly! Here are five bullet points for a strong resume summary focused on Six Sigma, suitable for a mid-level experienced professional:
Proven Lean Six Sigma Practitioner: Demonstrated ability to lead process improvement initiatives resulting in a 20% reduction in waste and a 15% increase in operational efficiency across diverse manufacturing teams.
Data-Driven Decision Maker: Utilizes advanced statistical tools and methodologies to analyze data, identify root causes of process inefficiencies, and implement sustainable solutions, achieving notable cost savings.
Cross-Functional Leadership: Experienced in collaborating with multidisciplinary teams to drive Six Sigma projects, fostering a culture of continuous improvement and enhancing overall team performance.
Certified Six Sigma Green Belt: Successfully completed Six Sigma certification with hands-on experience in DMAIC and DMADV methodologies, delivering projects on time and within budget in fast-paced environments.
Training and Mentorship: Passionate about coaching professionals on Six Sigma principles and best practices, contributing to workforce development and establishing an organization-wide commitment to quality improvement.
Junior level
Certainly! Here are five bullet points for a strong resume summary tailored for a junior-level candidate with Six Sigma experience:
Results-Oriented Problem Solver: Recently completed Six Sigma Yellow Belt certification, applying data-driven methodologies to improve operational efficiency in project-based assignments during internships.
Analytical Thinker: Demonstrated ability to analyze processes and identify areas for improvement, contributing to a 15% increase in team productivity through hands-on experience in process mapping and root cause analysis.
Collaborative Team Player: Assisted cross-functional teams in implementing Six Sigma principles, fostering collaboration and communication that led to enhanced project outcomes and stakeholder satisfaction.
Keen Learner Committed to Excellence: Eager to leverage strong foundational knowledge of Six Sigma tools and techniques to support continuous improvement initiatives and drive quality assurance in a dynamic work environment.
Detail-Oriented and Organized: Proven track record of meticulous documentation and reporting on project progress, ensuring compliance with Six Sigma standards and promoting a culture of accountability within project teams.
Entry-Level level
Entry-Level Six Sigma Resume Summary
Detail-Oriented Problem Solver: Recent graduate with a Six Sigma Green Belt certification and hands-on experience in process improvement projects during internships, adept at identifying inefficiencies and implementing sustainable solutions.
Analytical Thinker: Strong background in data analysis and statistical techniques gained through academic coursework, complemented by project experience using Six Sigma methodologies to enhance operational performance.
Team Collaboration Skills: Proven ability to work effectively within cross-functional teams to facilitate process mapping and root cause analysis, contributing to successful project outcomes as part of a university-led Six Sigma initiative.
Adaptable Learner: Quick to adapt and learn new concepts, demonstrated through successful completion of Six Sigma training, and continuous pursuit of knowledge in lean methodologies and operational excellence.
Communication Proficiency: Excellent written and verbal communication skills, able to present analytical findings and process improvement recommendations clearly to diverse stakeholders, fostering alignment and driving project success.
Experienced-Level Six Sigma Resume Summary
Results-Driven Six Sigma Specialist: Accomplished Six Sigma Black Belt with over 5 years of experience leading cross-functional teams to drive process improvements and achieve tangible cost savings in manufacturing environments.
Expert in Lean Methodologies: Proven track record in implementing lean principles alongside Six Sigma techniques, resulting in enhanced operational efficiency and reduced waste by up to 30% in previous projects.
Project Management Expertise: Skilled in managing complex projects from inception to completion, utilizing strong analytical abilities and Six Sigma tools to deliver projects on time and within budget while meeting quality standards.
Data-Driven Decision Maker: Adept at using statistical software to analyze process data and make informed decisions, leading to process optimization and increased profitability for various organizations.
Effective Leadership & Training: Experienced in training and mentoring teams on Six Sigma practices, fostering a culture of continuous improvement and ensuring successful knowledge transfer across the organization.
Weak Resume Summary Examples
Weak Resume Summary Examples for Six Sigma
"I have some experience in Six Sigma and took a few courses."
"I know about Six Sigma principles and tools, and I believe I could help a company."
"Six Sigma is interesting to me, and I want to learn more in a professional setting."
Why These Are Weak Headlines
Lack of Quantifiable Achievements: The summaries do not provide any specific examples or measurable outcomes from previous roles. Employers want to see evidence of how an applicant's Six Sigma knowledge has led to tangible improvements, such as percentage reductions in waste, cost savings, or increases in efficiency.
Vagueness and Lack of Confidence: Phrases like "I have some experience" and "I believe" convey uncertainty and do not instill confidence in the employer regarding the candidate's abilities. Instead, a strong resume should assert the applicant's qualifications with certainty and clarity.
No Demonstrated Commitment or Expertise: The summaries suggest a lack of dedication or deeper understanding of Six Sigma methodologies. Expressions of interest alone do not convey an actionable skill set that can contribute to a company’s goals, which is essential when applying for roles that require specific technical expertise or project management skills.
Resume Objective Examples for Six Sigma Quality Manager:
Strong Resume Objective Examples
Results-driven Six Sigma professional seeking to leverage expertise in process improvement and quality management at [Company Name] to enhance operational efficiency and reduce costs, contributing to a culture of continuous improvement.
Detail-oriented Six Sigma Green Belt aiming to apply analytical skills and a data-driven approach to problem-solving at [Company Name], ensuring optimal performance and quality standards are consistently achieved.
Motivated Six Sigma Black Belt with extensive experience in leading cross-functional teams and managing large-scale projects seeking to join [Company Name] to drive innovative process solutions and foster a high-performance work environment.
Why these are strong objectives:
These resume objectives are effective because they are specific and focused on the candidate's skills and expertise in Six Sigma. Each objective clearly states the desired position and aligns the candidate’s qualifications with the potential employer's needs. Furthermore, they highlight measurable outcomes, such as operational efficiency and cost reduction, which demonstrate the candidate's commitment to contributing positively to the organization. By including the company name, the objectives also reflect personal interest and dedication, making them more compelling to hiring managers.
Lead/Super Experienced level
Here are five strong resume objective examples for a Lead/Super Experienced level candidate in Six Sigma:
Objective 1: Dynamic Six Sigma Leader with over 10 years of experience in driving process improvements and quality control initiatives. Seeking to leverage expertise in Lean methodologies and team leadership to enhance operational efficiency at [Company Name].
Objective 2: Results-driven Six Sigma Black Belt professional with a proven track record of delivering substantial cost savings and reducing waste in complex manufacturing environments. Eager to lead transformative projects that enhance product quality and operational excellence at [Company Name].
Objective 3: Accomplished Six Sigma Master Black Belt with extensive experience in training and mentoring cross-functional teams. Passionate about cultivating a culture of continuous improvement to optimize business processes and exceed strategic goals at [Company Name].
Objective 4: Strategic Six Sigma expert with a history of implementing data-driven solutions that yield significant performance enhancements. Committed to advancing quality management and fostering innovation as part of the leadership team at [Company Name].
Objective 5: Visionary Six Sigma professional with 15+ years in organizational improvement and change management across diverse industries. Aiming to apply advanced statistical analysis and lean principles to drive sustainable growth and enhance customer satisfaction at [Company Name].
Senior level
Here are five strong resume objective examples tailored for a senior-level position in Six Sigma:
Strategic Quality Improvement Leader: Results-driven Six Sigma Black Belt with over 10 years of experience in process optimization and quality control, adept at leveraging data analysis to drive operational excellence and enhance customer satisfaction.
Operational Efficiency Expert: Senior Six Sigma Professional with a proven track record of leading cross-functional teams to achieve substantial cost reductions and process improvements, committed to implementing sustainable methodologies that align with organizational goals.
Transformational Change Agent: With extensive expertise in Six Sigma methodologies, I aim to utilize my strong leadership skills and analytical mindset to lead high-impact quality initiatives that enhance overall business performance and innovation.
Performance Enhancement Specialist: Senior Six Sigma practitioner with a history of executing large-scale projects that yield measurable results, seeking to contribute strategic insight and advanced problem-solving capabilities to foster a culture of continuous improvement.
Data-Driven Decision Maker: Seasoned Six Sigma expert with a focus on quantitative analysis and project management, dedicated to driving stakeholder engagement and deploying best practices that enhance efficiency, reduce waste, and improve bottom-line results.
Mid-Level level
Sure! Here are five strong resume objective examples for a mid-level Six Sigma professional:
Results-Driven Process Improvement Specialist: "Detail-oriented Six Sigma professional with over 5 years of experience in utilizing DMAIC methodologies to streamline operations and enhance quality. Seeking to leverage analytical skills and process optimization expertise to drive continuous improvement at [Company Name]."
Experienced Quality Assurance Analyst: "Mid-level Six Sigma Green Belt with a proven track record in reducing operational costs by 20% through effective data analysis and project management. Eager to contribute strong problem-solving abilities and collaborative spirit to the quality improvement team at [Company Name]."
Data-Driven Project Manager: "Accomplished Six Sigma practitioner with 6 years of experience leading cross-functional teams in process reengineering initiatives. Looking to apply my passion for quality management and strong communication skills to facilitate successful project outcomes at [Company Name]."
Skilled Operational Excellence Advocate: "Dedicated Six Sigma professional with a solid foundation in lean principles and a commitment to fostering a culture of quality. Aiming to support [Company Name] in achieving operational efficiency and improving customer satisfaction through strategic data-driven decisions."
Quality Improvement Enthusiast: "Proactive Six Sigma Green Belt with a comprehensive background in identifying process inefficiencies and implementing sustainable solutions in fast-paced environments. Seeking to bring my expertise in performance metrics and team leadership to [Company Name] to help drive transformative initiatives."
Junior level
Here are five strong resume objective examples for a junior-level position focused on Six Sigma:
Detail-oriented engineering graduate seeking a Junior Six Sigma Analyst role to leverage a foundational knowledge of process improvement methodologies and data analysis skills to enhance operational efficiency in a dynamic manufacturing environment.
Recent graduate in Industrial Engineering with a passion for quality management and process optimization, aiming to contribute my analytical skills and Six Sigma training to support continuous improvement initiatives within a forward-thinking organization.
Driven quality assurance professional with hands-on experience in process mapping and data-driven decision-making, looking for a Junior Six Sigma position to apply my knowledge of Six Sigma principles while contributing to cost reduction and quality enhancement projects.
Motivated analytics enthusiast with an understanding of Six Sigma principles and a strong background in statistical analysis, eager to join a collaborative team to assist in problem-solving and process improvement efforts that drive organizational success.
Recent Six Sigma Green Belt certified professional, aiming to utilize my skills in process improvement and quantitative analysis as a Junior Six Sigma Associate to support the implementation of Lean methodologies and foster a culture of continuous improvement within the company.
Entry-Level level
Sure! Here are five strong resume objective examples tailored for entry-level candidates in the Six Sigma field:
Analytical and Detail-Oriented Graduate: Highly motivated recent graduate with a degree in Industrial Engineering seeking to leverage Six Sigma methodologies and problem-solving skills to drive quality improvements and operational efficiency in an entry-level role.
Aspiring Quality Analyst: Results-driven individual with a passion for process optimization, aiming to apply foundational Six Sigma knowledge and a commitment to continuous improvement within a fast-paced manufacturing environment.
Entry-Level Process Improvement Enthusiast: Energetic and detail-oriented candidate eager to contribute to a dynamic team by utilizing basic Six Sigma principles to identify workflow inefficiencies and enhance product quality.
Recent Graduate with Six Sigma Certification: Dedicated and eager professional with a Six Sigma Yellow Belt certification looking to kickstart a career in quality management, aiming to assist organizations in streamlining processes and ensuring high standards of quality.
Motivated Team Player with a Focus on Quality: Entry-level candidate with strong analytical skills and a foundational understanding of Six Sigma practices, seeking to support process improvement initiatives in a collaborative environment and contribute to overall business success.
Weak Resume Objective Examples
Weak Resume Objective Examples for Six Sigma
- "Looking for a position in a company where I can use my Six Sigma knowledge to help improve processes."
- "To obtain a role that utilizes my Six Sigma training and certification."
- "Seeking any opportunity to apply my skills in Six Sigma."
Why These Objectives are Weak
Lack of Specificity: The statements are too vague and do not specify the type of role or industry. This leaves employers unclear about the candidate's preferences and goals, making it difficult for them to see how the applicant aligns with their needs.
Limited Value Proposition: Each objective fails to communicate what the candidate brings to the table—specific skills, experiences, or achievements related to Six Sigma. Effective objectives should outline how the candidate can add value to the organization.
Generic Language: The use of phrases like "any opportunity" or "help improve processes" does not convey a strong sense of ambition or interest in taking on specific challenges. An effective objective should reflect a clear understanding of the role and an eagerness to contribute to the company's success.
When crafting an effective work experience section for a Six Sigma-focused resume, it’s essential to highlight your skills, accomplishments, and the impact of your contributions clearly and quantifiably. Here’s how to do it:
Tailor to Six Sigma Principles: Use terminology and concepts from Six Sigma, such as DMAIC (Define, Measure, Analyze, Improve, Control) and statistical analysis. This showcases your familiarity with Six Sigma methodologies.
Quantify Achievements: Whenever possible, use specific metrics to demonstrate your impact. For instance, instead of stating “improved process efficiency,” specify “increased process efficiency by 25%, resulting in annual savings of $50,000.”
Highlight Relevant Roles: Focus on positions where you've applied Six Sigma principles. You can include job titles like Quality Analyst, Process Improvement Specialist, or Lean Six Sigma Consultant. Ensure that each role includes relevant duties.
Use Action Verbs: Start bullet points with strong action verbs such as “Led,” “Facilitated,” “Analyzed,” "Reduced," or “Implemented.” This approach creates a dynamic description of your experience.
Showcase Projects: Detail notable Six Sigma projects you were involved in. Describe your role, the tools used (like Minitab), and the outcomes. For example, “Led a project to streamline customer service processes, reducing response time from 48 hours to 24 hours.”
Incorporate Soft Skills: Mention collaboration, leadership, and communication skills. Emphasize your ability to work cross-functionally and mentor team members in Six Sigma principles.
Layout and Clarity: Use a clear, professional format. Outline your work experience in reverse chronological order, ensuring each listing includes the job title, company name, dates of employment, and bullet points describing your responsibilities and achievements.
By following these guidelines, you can present a compelling work experience section that effectively communicates your Six Sigma expertise and contributions.
Best Practices for Your Work Experience Section:
Here are 12 best practices for showcasing your work experience section specifically related to Six Sigma methodologies:
Use Clear Six Sigma Terminology: Incorporate key terms such as DMAIC (Define, Measure, Analyze, Improve, Control), SIPOC (Suppliers, Inputs, Process, Outputs, Customers), and DPMO (Defects Per Million Opportunities) to demonstrate familiarity with Six Sigma concepts.
Focus on Measurable Outcomes: Quantify your achievements by providing metrics, such as percentage reductions in defects, cost savings, or increased efficiency, to illustrate the impact of your Six Sigma projects.
Highlight Certifications: Include any relevant Six Sigma certifications (e.g., Yellow Belt, Green Belt, Black Belt) to validate your expertise and commitment to the methodology.
Detail Specific Roles: Clearly define your role in Six Sigma projects (e.g., team leader, data analyst) to help potential employers understand your contributions and responsibilities.
Describe the Projects: Summarize the Six Sigma projects you’ve worked on, emphasizing your problem-solving approach and the specific tools or techniques used.
Showcase Team Collaboration: Emphasize your ability to work within cross-functional teams, demonstrating collaboration and communication skills essential for Six Sigma initiatives.
Incorporate Soft Skills: Highlight relevant soft skills such as leadership, training, and facilitation to show your ability to guide teams in Six Sigma processes.
Illustrate Continuous Improvement: Discuss your involvement in ongoing improvement processes, demonstrating a commitment to not only managing existing issues but also fostering a culture of continuous improvement.
Include Relevant Industries: Mention industries or sectors where you have applied Six Sigma principles, showcasing versatility and adaptability across different environments.
Utilize Action Verbs: Start bullet points with strong action verbs (e.g., led, optimized, analyzed) to convey a sense of initiative and results-oriented achievement.
Tailor to Job Descriptions: Customize your work experience section to align with specific job descriptions, ensuring that relevant Six Sigma experience is front and center.
Showcase Training and Mentoring: If applicable, highlight experiences where you trained or mentored others in Six Sigma methodologies, demonstrating your leadership and knowledge transfer capabilities.
Using these best practices can help strengthen your work experience section and better showcase your abilities in Six Sigma-focused roles.
Strong Resume Work Experiences Examples
Strong Resume Work Experience Examples for Six Sigma
Process Improvement Specialist, ABC Manufacturing Inc. (June 2020 - Present)
- Led a cross-functional team in a Six Sigma Green Belt project that reduced the production cycle time by 25%, resulting in a cost savings of $150,000 annually.
Quality Assurance Analyst, XYZ Technologies (January 2018 - May 2020)
- Implemented Six Sigma methodologies to identify process inefficiencies, achieving a reduction in product defects by 30% over six months, significantly enhancing customer satisfaction ratings.
Operations Manager, DEF Logistics Solutions (March 2016 - December 2017)
- Spearheaded Lean Six Sigma initiatives that streamlined warehouse operations, resulting in a 40% increase in throughput and a 20% decrease in operational costs within the first year.
Why This is Strong Work Experience
Quantifiable Results: Each experience highlights specific, measurable outcomes (e.g., percentage improvements, cost savings), which demonstrate the candidate's ability to drive real change and deliver value.
Relevant Skills and Methodologies: The roles explicitly reference the use of Six Sigma and Lean methodologies, showcasing the candidate's proficiency in these frameworks, which are critical in many industries for process improvement and quality management.
Leadership and Collaboration: The experiences reflect the candidate's capability to lead teams and collaborate across functions, essential traits for successful project management, especially in complex, cross-departmental initiatives associated with Six Sigma projects.
These attributes make the work experiences compelling to potential employers looking for candidates with a strong track record in process improvement and operational excellence.
Lead/Super Experienced level
Here are five bullet points for a strong resume highlighting work experience related to Six Sigma for a lead or super experienced level professional:
Led Cross-Functional Six Sigma Projects: Spearheaded multiple DMAIC (Define, Measure, Analyze, Improve, Control) initiatives across departments, successfully reducing process variations by an average of 30%, resulting in cost savings of over $1 million annually.
Mentorship and Training of Teams: Developed and conducted Six Sigma training programs for over 100 employees, fostering a culture of continuous improvement and enabling teams to effectively utilize Lean methodologies to enhance operational efficiency.
Strategic Process Improvement Initiatives: Directed high-impact process improvement initiatives that leveraged statistical analysis and Six Sigma tools, achieving a 25% reduction in cycle time for key production processes while simultaneously improving product quality by 20%.
Performance Tracking and Reporting: Implemented robust performance metrics and monitoring systems to provide real-time insights into project progress, facilitating timely decision-making and ensuring project milestones were consistently met or exceeded.
Stakeholder Engagement and Communication: Collaborated closely with executive leadership and cross-departmental teams to align Six Sigma efforts with organizational goals, effectively communicating project outcomes and insights, which drove strategic business improvements and enhanced stakeholder buy-in.
Senior level
Sure! Here are five bullet points showcasing strong resume work experience examples for a Senior Six Sigma professional:
Led a cross-functional team in the implementation of Six Sigma methodologies that resulted in a 30% reduction in manufacturing defects, directly contributing to a $1.5 million increase in annual revenue.
Developed and executed a comprehensive training program for over 100 employees on DMAIC processes, fostering a culture of continuous improvement and achieving a 25% increase in process efficiency within the first year.
Spearheaded a Lean Six Sigma project to optimize supply chain operations, achieving a 40% decrease in cycle time and a 20% reduction in inventory costs through the successful application of Value Stream Mapping techniques.
Conducted root cause analysis for recurring quality issues using advanced statistical tools, leading to the redesign of key process components and a 50% decrease in customer complaints over an 18-month period.
Collaborated with executive leadership to establish strategic KPI metrics and dashboards, enhancing decision-making processes and driving accountability across teams, which improved overall operational performance by 35%.
Mid-Level level
Here are five bullet points showcasing strong work experiences for a mid-level Six Sigma professional:
Process Improvement: Led cross-functional teams in a Six Sigma project that reduced process cycle time by 30%, resulting in a savings of $150,000 annually and significantly enhancing service delivery times.
Data Analysis: Utilized statistical tools and Six Sigma methodologies to analyze defects in manufacturing processes, achieving a 20% reduction in defect rates and contributing to a 15% increase in customer satisfaction scores.
Lean Six Sigma Training: Developed and facilitated Lean Six Sigma training sessions for 50+ employees, fostering a culture of continuous improvement and equipping staff with techniques to identify and eliminate waste within their work processes.
Quality Control Initiatives: Spearheaded quality control initiatives that implemented Six Sigma techniques to monitor process performance, leading to a decrease in variation and maintaining compliance with industry regulations.
Project Management: Successfully managed multiple Six Sigma projects from initiation to completion, consistently meeting project timelines and goals while enhancing team collaboration and stakeholder engagement in process improvement efforts.
Junior level
Certainly! Here are five bullet points showcasing strong work experience examples for a Junior level position focused on Six Sigma methodologies:
Assisted in Process Improvement Projects: Collaborated with senior team members to analyze and map existing processes using Six Sigma tools, contributing to a 10% increase in overall efficiency within the manufacturing line.
Data Collection and Analysis: Conducted data collection and statistical analysis as part of a DMAIC project, identifying key performance indicators and providing insights that informed process adjustments, leading to a reduction in defects by 15%.
Participated in Kaizen Events: Engaged in multiple Kaizen events that fostered team brainstorming and problem-solving, resulting in actionable plans to streamline workflow and improve team productivity by 20%.
Developed Training Materials: Created and delivered training materials focused on Six Sigma fundamentals to new hires, enhancing their understanding and application of quality improvement techniques.
Supported Quality Assurance Efforts: Worked closely with QA teams to monitor compliance with Six Sigma standards, actively participating in audits that yielded a 5% decrease in non-compliance issues over six months.
Entry-Level level
Here are five bullet point examples of strong work experiences for an entry-level position involving Six Sigma methodologies:
Quality Improvement Project: Collaborated with a cross-functional team to apply Six Sigma principles in a process improvement project, leading to a 15% reduction in production defects over three months.
Data Analysis: Assisted in analyzing process data using statistical tools such as DMAIC to identify inefficiencies, resulting in recommendations that improved overall workflow by 20%.
Training and Support: Supported Six Sigma Green Belts by creating training materials and conducting workshops, enhancing team members' understanding of process improvement techniques.
Process Mapping: Participated in value stream mapping exercises to visualize and streamline production workflows, contributing to an increase in operational efficiency by identifying key bottlenecks.
Documentation and Reporting: Maintained comprehensive documentation of project progress and outcomes, providing regular reports to management that highlighted key performance indicators and supported strategic decision-making.
Weak Resume Work Experiences Examples
Weak Resume Work Experience Examples for Six Sigma
Quality Control Intern at XYZ Manufacturing
- Assisted with monitoring product quality on the assembly line.
- Performed basic data entry tasks related to quality checks.
- Shadowed team members during routine quality inspections.
Administrative Assistant at ABC Corp
- Supported the team by filing documents and organizing meetings.
- Helped create simple Excel spreadsheets to track project progress.
- Attended team meetings without contributing to discussions on process improvements.
Sales Associate at Retail Store
- Engaged with customers to sell products and handled transactions.
- Occasionally discussed customer feedback with the management.
- Participated in a workshop about sales techniques but did not apply any processes for quality improvement.
Why These are Weak Work Experiences
Lack of Direct Contribution:
In the examples above, the roles do not showcase substantial contributions to Six Sigma principles or methodologies. For instance, simply assisting in quality control or performing basic data entry fails to demonstrate active involvement in process improvement, which is core to Six Sigma.Insufficient Impact on Process Improvements:
The experiences listed do not indicate any involvement in the analysis or application of Six Sigma techniques to enhance processes. Participation in routine tasks without measurable impact on efficiency, waste reduction, or quality enhancement does not reflect Six Sigma capabilities.Limited Engagement with Six Sigma Tools and Concepts:
The candidates do not appear to have engaged with key Six Sigma tools such as DMAIC (Define, Measure, Analyze, Improve, Control) or any data-driven decision-making processes. Attending meetings or shadowing does not equate to active participation in Six Sigma projects or initiatives, limiting the value of these experiences in the context of a Six Sigma-focused resume.
Top Skills & Keywords for Six Sigma Quality Manager Resumes:
When crafting a Six Sigma resume, emphasize the following top skills and keywords:
- DMAIC (Define, Measure, Analyze, Improve, Control) methodology.
- Statistical Analysis tools (like Minitab).
- Process Improvement and optimization.
- Root Cause Analysis techniques.
- Lean Principles to eliminate waste.
- Data-Driven Decision Making.
- Project Management abilities.
- Quality Assurance and control.
- Training and Mentoring skills.
- Problem-Solving capabilities.
Incorporate relevant certifications (e.g., Green Belt or Black Belt) and quantify achievements (e.g., percentage improvements or cost savings) to enhance your resume's impact.
Top Hard & Soft Skills for Six Sigma Quality Manager:
Hard Skills
Sure! Below is a table with 10 hard skills relevant to Six Sigma, including descriptions and formatted links as requested.
Hard Skills | Description |
---|---|
Data Analysis | The process of inspecting, cleansing, transforming, and modeling data to uncover useful information. |
Statistical Process Control | A method of quality control that uses statistical methods to monitor and control a process. |
Root Cause Analysis | A technique used to identify the underlying reasons for faults or problems in a process. |
Fishbone Diagram | A visual tool for categorizing potential causes of problems to identify root causes. |
Lean Principles | Principles focused on minimizing waste within manufacturing systems without sacrificing productivity. |
Process Mapping | The act of defining the steps involved in a process to improve clarity and identify areas for improvement. |
DMAIC | A data-driven quality strategy used to improve processes that includes Define, Measure, Analyze, Improve, and Control phases. |
Quality Management Systems | Framework for managing an organization’s processes to ensure consistent quality in products or services. |
Advanced Statistics | The application of complex statistical methods to analyze data and draw conclusions. |
Project Management | The application of knowledge, skills, tools, and techniques to project activities to meet project requirements. |
Feel free to adjust the descriptions as needed!
Soft Skills
Sure! Here’s a table with 10 soft skills relevant to Six Sigma, along with their descriptions:
Soft Skills | Description |
---|---|
Communication | The ability to convey information clearly and effectively to team members and stakeholders. |
Problem Solving | Skills that help identify issues, analyze situations, and implement effective solutions. |
Leadership | The ability to guide, motivate, and manage teams towards achieving project goals. |
Teamwork | Collaborating effectively with others to achieve common objectives and improve processes. |
Adaptability | Being flexible and open to change, allowing for adjustments in strategies when necessary. |
Time Management | Skills to prioritize tasks and manage time efficiently to meet project deadlines. |
Critical Thinking | The ability to analyze situations, recognize patterns, and make reasoned judgments. |
Conflict Resolution | Skills to address and resolve disagreements in a constructive manner. |
Creativity | The capacity to think outside the box and develop innovative solutions to improve processes. |
Negotiation | Skills to reach mutually beneficial agreements with stakeholders and team members. |
Feel free to use or modify this table as needed!
Elevate Your Application: Crafting an Exceptional Six Sigma Quality Manager Cover Letter
Six Sigma Quality Manager Cover Letter Example: Based on Resume
Dear [Company Name] Hiring Manager,
I am excited to apply for the Six Sigma position at [Company Name], as advertised on your careers page. With a robust foundation in quality management, a Green Belt certification, and a passion for process improvement, I am eager to contribute to your team and drive operational excellence.
Throughout my five years of experience in manufacturing and service industries, I have successfully led various Six Sigma projects that resulted in substantial cost savings and enhanced process efficiencies. At my previous role with [Previous Company Name], I spearheaded a project that reduced production defects by 30% within six months, which saved the company over $150,000 annually. My proficiency in DMAIC methodologies has enabled me to identify root causes effectively and implement sustainable solutions.
I am also skilled in industry-standard software such as Minitab, Microsoft Excel, and Tableau, which I have utilized to analyze data and visualize results for team presentations and stakeholder discussions. I believe that utilizing technology effectively is essential for driving informed decision-making and fostering a culture of continuous improvement.
Collaboration is at the heart of what I do; I thrive in team environments where I can share insights and learn from others. During my tenure at [Another Previous Company Name], I facilitated cross-functional workshops that brought together different departments to align on project goals. This collaboration not only improved project outcomes but also strengthened inter-departmental relationships.
I am drawn to [Company Name] because of your commitment to innovation and quality. I am excited about the opportunity to contribute to a forward-thinking company that values process excellence. Thank you for considering my application. I look forward to discussing how my skills and experiences align with the goals of your team.
Best regards,
[Your Name]
When crafting a cover letter for a Six Sigma position, it’s essential to convey both your qualifications and your understanding of Six Sigma methodologies. Here’s a guide on what to include:
Structure of the Cover Letter:
Header: Include your name, address, email, and phone number at the top, followed by the date and the employer's contact information.
Salutation: Address the hiring manager by name if possible. If not, "Dear Hiring Manager" is acceptable.
Content to Include:
Introduction: Start with a strong opening that captures attention. Mention the position you are applying for and how you learned about the opportunity. Highlight any personal connections or enthusiasm for the company.
Relevant Experience: Briefly outline your experience with Six Sigma practices. Mention certifications such as Green Belt or Black Belt, and highlight specific projects where you implemented Six Sigma methodologies, detailing measurable results.
Key Skills: Elaborate on skills that make you a strong candidate, such as process improvement, data analysis, and problem-solving. Use examples that demonstrate how you've used these skills to achieve tangible results in previous roles.
Understanding of Six Sigma Principles: Convey your understanding of Six Sigma tools and techniques, such as DMAIC (Define, Measure, Analyze, Improve, Control), and how they can benefit the potential employer.
Cultural Fit and Motivation: Share why you are interested in this particular company and role. Mention any shared values or goals that align with their mission, demonstrating that you’ve researched the organization.
Conclusion: Reinforce your enthusiasm for the role and express your eagerness to contribute to their team. Invite them to reach out for a follow-up discussion and thank them for considering your application.
Final Tips:
- Tailor Your Letter: Customize your cover letter for each application to reflect the specific job and company.
- Be Concise: Aim for one page, focusing on the most relevant information.
- Proofread: Ensure there are no grammatical or spelling errors. A polished letter shows professionalism.
By following this structure and including these elements, you'll create a compelling cover letter tailored for a Six Sigma position.
Resume FAQs for Six Sigma Quality Manager:
How long should I make my Six Sigma Quality Manager resume?
When crafting a Six Sigma resume, it's essential to strike a balance between providing enough detail and keeping it concise. Typically, a one-page resume is ideal for most job seekers, especially those with less than 10 years of experience. This length allows you to highlight relevant skills, certifications, and accomplishments without overwhelming the reader.
For professionals with extensive experience or those pursuing senior-level positions, a two-page resume may be appropriate. In this case, focus on showcasing your Six Sigma achievements, including projects you've led, process improvements implemented, and quantifiable results. Use bullet points to make your accomplishments clear and impactful.
Regardless of the length, clarity is key. Tailor your resume to the specific role you’re applying for, using keywords from the job description to make it more compelling. Highlight your Six Sigma certifications (such as Green Belt or Black Belt) and any relevant training you’ve received.
Remember, recruiters often skim resumes, so ensure yours is easy to navigate. Use clear headings and a professional layout, focusing on the most relevant experiences and skills to stand out in a competitive job market.
What is the best way to format a Six Sigma Quality Manager resume?
Creating a Six Sigma resume requires a strategic format that showcases your expertise in process improvement and quality management. Here’s an effective approach:
Header: Start with your name, professional title (e.g., Six Sigma Green Belt), and contact information.
Professional Summary: Include a brief 2-3 sentence summary that highlights your Six Sigma certification, years of experience, and key skills. This section should capture the attention of hiring managers quickly.
Certifications: List your Six Sigma certifications prominently (e.g., Green Belt, Black Belt), along with any relevant credentials like Lean certifications or project management certifications.
Core Competencies: Create a bullet-point list of your key skills relevant to Six Sigma, such as process mapping, statistical analysis, and root cause analysis. Tailor this section to the job description.
Professional Experience: Structure this section in reverse chronological order. For each role, include your job title, company name, dates of employment, and bullet points that quantify your achievements (e.g., reducing defects by X% or improving process efficiency).
Education: List your degrees, starting with the most recent, along with any relevant coursework or projects related to quality management.
Projects: Optionally, include a section on significant Six Sigma projects, detailing methodologies used and results achieved.
Ensure your resume is clear, concise, and free from jargon, making it easy for recruiters to recognize your Six Sigma expertise.
Which Six Sigma Quality Manager skills are most important to highlight in a resume?
When crafting a resume to highlight Six Sigma skills, it's essential to focus on competencies that demonstrate proficiency in process improvement and quality control. Here are the six most important skills to emphasize:
Data Analysis: Ability to collect, analyze, and interpret data using statistical tools to identify trends and improve processes.
Problem-Solving: Expertise in identifying root causes of defects and inefficiencies, employing methodologies like DMAIC (Define, Measure, Analyze, Improve, Control).
Process Mapping: Proficiency in visualizing processes through flowcharts and value stream mapping to understand workflows and identify bottlenecks.
Project Management: Experience in leading projects, ensuring that Six Sigma initiatives are executed on time, within scope, and aligned with business goals.
Team Leadership: Capability to lead cross-functional teams, fostering collaboration and driving engagement among team members toward common objectives.
Continuous Improvement Mindset: Commitment to fostering a culture of continuous improvement through ongoing training, evaluation, and adaptation of processes.
Including certifications like Green Belt or Black Belt can further enhance your profile, showcasing your commitment and expertise in Six Sigma methodologies. Tailor your resume to highlight these skills in context, using specific examples to demonstrate their impact.
How should you write a resume if you have no experience as a Six Sigma Quality Manager?
Writing a resume for a Six Sigma position without direct experience can be challenging, but it’s an opportunity to highlight your relevant skills, education, and any transferable experiences. Start by creating a strong objective statement that indicates your interest in Six Sigma methodologies and your willingness to learn and contribute to process improvement.
Next, emphasize your educational background. If you've completed any coursework or certifications related to Six Sigma, such as a Green Belt or Yellow Belt training, make sure to showcase that prominently. Include any relevant projects or case studies from your coursework that demonstrate your understanding of Six Sigma principles.
In the skills section, highlight analytical skills, problem-solving abilities, and proficiency in using tools often associated with Six Sigma, such as statistical software or data analysis tools. If you’ve worked on projects or in roles where you’ve applied process improvement, even in a different context, be sure to detail those experiences.
Finally, consider including volunteer work or internships that involve teamwork, leadership, or project management, as these demonstrate qualities valuable to a Six Sigma role. Tailor your resume to the job description, ensuring that your passion for continuous improvement shines through. This approach can help you stand out, even without direct experience.
Professional Development Resources Tips for Six Sigma Quality Manager:
null
TOP 20 Six Sigma Quality Manager relevant keywords for ATS (Applicant Tracking System) systems:
Sure! Here’s a table of 20 keywords relevant to Six Sigma that can help you pass Applicant Tracking Systems (ATS) used in recruitment. Each term is accompanied by a brief description:
Keyword | Description |
---|---|
Six Sigma | A set of techniques and tools for process improvement that aims to reduce defects and improve quality. |
Lean | A methodology that focuses on minimizing waste within manufacturing systems while simultaneously maximizing productivity. |
DMAIC | A data-driven quality strategy used to improve processes and stands for Define, Measure, Analyze, Improve, Control. |
Process Improvement | The practice of analyzing and enhancing existing processes to boost efficiency and effectiveness. |
Quality Assurance | A way of preventing errors or defects in manufacturing and service delivery, ensuring a level of quality. |
Statistical Analysis | The use of statistical methods to analyze data and inform decisions in quality management. |
Root Cause Analysis | A method of problem-solving that identifies the primary cause of a defect or problem to prevent re-occurrence. |
Total Quality Management | A comprehensive approach to improving competitiveness, effectiveness, and flexibility through planning, organizing, and understanding each activity. |
Value Stream Mapping | A lean-management technique that analyzes the flow of materials and information currently required to bring a product or service to a consumer. |
Continuous Improvement | Ongoing effort to improve products, services, or processes over time, aiming for incremental changes. |
Kaizen | A Japanese term meaning "change for better," representing a philosophy of continuous improvement. |
Control Charts | A statistical tool used to determine if a manufacturing or business process is in a state of control. |
Standard Operating Procedure (SOP) | Detailed, written instructions to achieve uniformity of the performance of a specific function. |
Quality Management System (QMS) | A formal system documenting processes, procedures, and responsibilities for achieving quality policies and objectives. |
Project Management | The discipline of planning, organizing, and managing resources to achieve specific goals and objectives. |
Training & Development | Processes for enhancing the skills and knowledge of employees to improve overall quality and efficiency. |
Change Management | A systematic approach to dealing with change, both from the perspective of an organization and the individual. |
Performance Metrics | Measurements used to gauge organizational performance, often associated with quality standards. |
Audit | A systematic examination of a quality system carried out by an internal or external quality auditor. |
Stakeholder Engagement | The process of involving individuals or groups who may affect or be affected by a project or decision, ensuring their needs and concerns are considered. |
Using these keywords in your resume, particularly in the context of your experience and accomplishments, can help it align with ATS requirements and improve your chances of being noticed by recruiters.
Sample Interview Preparation Questions:
Can you explain the DMAIC process and its significance in Six Sigma projects?
How do you identify and prioritize potential process improvements in a Six Sigma project?
What statistical tools and techniques do you find most useful in analyzing data for Six Sigma projects?
Can you provide an example of a successful Six Sigma project you led or were a part of, and what was your role?
How do you ensure that the improvements made through Six Sigma are sustainable over time?
Related Resumes for Six Sigma Quality Manager:
Generate Your NEXT Resume with AI
Accelerate your resume crafting with the AI Resume Builder. Create personalized resume summaries in seconds.